Aerospace & Defense Process Control Applications
Application Overview
Precision instrumentation, control systems, and analyzers play a critical role in aerospace and defense manufacturing, testing, and operational environments. From fuel and hydraulic system monitoring to structural integrity testing and environmental control, advanced process control solutions ensure safety, performance, and regulatory compliance. Aerospace systems demand high-accuracy sensors, real-time data acquisition, and automation to optimize operations in flight systems, ground support equipment, propulsion testing, and component manufacturing.
In defense applications, reliability and precision are paramount for weapons systems, radar technology, military aircraft, and naval operations. Flow meters, pressure transmitters, vibration sensors, and gas analyzers enable real-time monitoring of fuel efficiency, atmospheric conditions, and structural stresses in extreme environments. Advanced SCADA and PLC-based control systems integrate with high-performance sensors to provide predictive maintenance, automated safety responses, and real-time diagnostics to support mission-critical operations and meet stringent FAA, NASA, and military standards.
How Our Products Support Your Industry
Clipper Controls provides high-precision instrumentation, automation, and process control solutions tailored for aerospace and defense applications. Our flow meters, pressure sensors, vibration analyzers, and environmental monitoring systems ensure accurate data acquisition, real-time diagnostics, and operational efficiency in mission-critical environments.
Key Applications and Solutions
Flow Measurement & Control
Precise flow measurement and control are critical in aerospace and defense applications, where fluid dynamics impact fuel efficiency, propulsion performance, cooling systems, and hydraulic operations. Accurate flow monitoring ensures mission-critical reliability, safety, and regulatory compliance in environments that demand high precision, durability, and resilience under extreme temperatures, pressures, and gravitational forces. Advanced flow meters, controllers, and automated monitoring systems provide real-time data acquisition, predictive maintenance, and optimized system performance, reducing operational risks and improving efficiency in aircraft, spacecraft, defense vehicles, and military facilities.
Flow Measurement & Control Applications in Aerospace & Defense
Flow measurement plays an essential role in propulsion, cooling, fuel distribution, and environmental control systems. Reliable flow monitoring helps optimize performance, ensure compliance with military and aerospace standards, and prevent system failures in mission-critical operations.
Aircraft & Spacecraft Fuel Flow Monitoring:
Coriolis and ultrasonic flow meters provide highly accurate mass and volumetric fuel flow measurement in aircraft engines, rocket propulsion systems, and UAV fuel delivery.
Turbine flow meters with extreme-temperature tolerance monitor liquid oxygen (LOX) and liquid hydrogen (LH₂) flow in cryogenic rocket engines, ensuring precise fuel mixture control.
Flow controllers in jet propulsion systems regulate fuel injection for thrust optimization, efficiency improvements, and emissions control.
Cryogenic & High-Pressure Flow Systems:
Thermal mass flow meters accurately measure compressed gas flow in space propulsion systems, satellite cooling loops, and life support systems.
Differential pressure flow meters monitor supercooled cryogenic fluids in space launch systems, missile guidance systems, and deep-space exploration vehicles.
Ultrasonic flow meters provide non-invasive measurement in cryogenic and high-pressure fuel handling applications, reducing contamination risks.
Hydraulic & Pneumatic Flow Control in Aerospace Systems:
Magnetic and Coriolis flow meters regulate hydraulic fluid circulation in landing gear, flight control actuators, and weapons deployment mechanisms.
Vortex flow meters measure cooling fluid and compressed air flow in avionics, radar cooling systems, and high-altitude reconnaissance aircraft.
Digital flow controllers ensure precise delivery of lubricants, hydraulic fluids, and coolants in fighter jets, military drones, and defense ground vehicles.
Environmental & Life Support Systems in Aircraft & Spacecraft:
Thermal mass flow meters regulate oxygen, nitrogen, and carbon dioxide levels in pressurized aircraft cabins, space station life support systems, and military submarines.
Flow sensors in water recycling systems ensure proper distribution of potable water, wastewater, and humidity control fluids in long-duration space missions.
Gas flow meters monitor inert gas suppression systems in fuel tanks, ammunition storage, and fire suppression systems in military and aerospace facilities.
Defense Infrastructure & Military Facility Flow Control:
Flow monitoring in cooling towers and HVAC systems ensures operational stability in mission-critical radar stations, missile defense installations, and aircraft hangars.
Fuel distribution flow meters in naval vessels, ground combat vehicles, and remote airbases ensure proper allocation and efficiency in battlefield conditions.
Smart flow control systems optimize energy and fuel consumption, reducing operational costs in military bases, aerospace manufacturing plants, and unmanned defense outposts.
Key Purchasing Considerations
Choosing the right flow measurement and control instrumentation for aerospace and defense applications requires evaluating fluid properties, operational conditions, integration requirements, and regulatory standards. The following factors should guide decision-making:
Accuracy & Response Time:
Coriolis and ultrasonic flow meters provide high-precision mass flow measurement for rocket propellants, aircraft fuel, and cryogenic fluids.
Turbine and vortex flow meters offer fast response times for high-pressure hydraulic and pneumatic applications in flight control systems and missile guidance systems.
Environmental Durability & System Compatibility:
High-temperature and cryogenic-rated flow meters withstand extreme conditions in liquid oxygen, liquid hydrogen, and high-altitude fuel applications.
Radiation-hardened and shock-resistant flow meters ensure functionality in space missions, military avionics, and defense ground vehicles.
Material Compatibility & Corrosion Resistance:
316L stainless steel and Inconel flow meters resist corrosion in jet fuel, hydraulic fluids, and supercooled cryogenic applications.
Teflon and ceramic-lined flow sensors prevent contamination in oxygen-rich and ultra-pure fluid handling applications.
Integration with Advanced Control Systems:
SCADA, PLC, and telemetry-compatible flow sensors enable real-time monitoring and automated control in missile launch systems, unmanned aerial vehicles (UAVs), and defense infrastructure.
Digital communication protocols (HART, Modbus, Profibus, CAN bus) ensure seamless data integration with flight control systems and propulsion monitoring networks.
Regulatory Compliance & Military Standards:
Ensure compliance with FAA, NASA, AS9100, MIL-STD, and ITAR regulations for aerospace and defense applications.
Flow meters used in military aircraft and space propulsion systems must meet DO-160 environmental conditions and test procedures for airborne equipment.
Maintenance & Lifecycle Costs:
Non-intrusive and self-diagnostic flow meters reduce maintenance needs in remote and unmanned aerospace applications.
Redundant flow measurement systems enhance reliability in defense-critical fuel and hydraulic networks, ensuring operational continuity.
Pressure Monitoring & Regulation
Accurate pressure monitoring and regulation are essential for aerospace and defense applications, where even minor deviations can impact safety, performance, and regulatory compliance. From hydraulic flight control systems and rocket propulsion to cabin pressurization and fuel distribution, maintaining precise pressure levels is critical to ensuring reliability, optimizing efficiency, and preventing system failures. Advanced pressure sensors, transmitters, and regulators provide real-time data acquisition, predictive maintenance insights, and automated safety controls, helping aerospace and defense systems operate safely in high-altitude, deep-space, and extreme-environment conditions.
Pressure Monitoring & Regulation Applications in Mission-Critical Systems
Precise pressure control is required in propulsion, hydraulic, pneumatic, environmental, and life-support systems across aerospace and defense sectors. Reliable pressure measurement helps optimize performance, ensure compliance, and prevent catastrophic failures in mission-critical operations.
Aircraft & Spacecraft Hydraulic and Pneumatic Systems:
High-precision pressure transmitters monitor hydraulic systems in aircraft landing gear, aileron actuators, and thrust reversers, ensuring smooth operation.
Differential pressure sensors regulate pneumatic systems for braking, de-icing, and flight control surfaces, improving responsiveness and safety.
Digital pressure regulators optimize hydraulic performance in military drones, fighter jets, and unmanned aerial vehicles (UAVs), preventing mechanical failures.
Rocket Propulsion & Space Launch Systems:
Cryogenic pressure sensors regulate liquid oxygen (LOX) and liquid hydrogen (LH₂) flow in rocket propulsion and space station life support systems.
High-pressure transducers monitor fuel tank pressurization and combustion chamber conditions, ensuring precise fuel-to-oxidizer ratios.
Burst pressure relief sensors prevent structural damage in booster stages and satellite propulsion systems during extreme launch conditions.
Cabin Pressurization & Environmental Control Systems:
Barometric pressure sensors regulate aircraft cabin pressurization, maintaining safe oxygen levels for crew and passengers.
Differential pressure monitors ensure sealed compartments and life-support systems in spacecraft and military submarines maintain structural integrity.
Air quality pressure sensors regulate oxygen, nitrogen, and carbon dioxide levels in space habitats, military aircraft, and command centers.
Fuel, Coolant, & Lubrication Pressure Control:
Flow-integrated pressure transmitters measure jet fuel, cryogenic propellant, and hydraulic fluid pressures, preventing leaks and optimizing flow rates.
Coolant system pressure sensors maintain proper thermal regulation in radar systems, avionics, and high-performance jet engines.
Oil pressure sensors protect turbine engines, auxiliary power units (APUs), and military vehicle drivetrains from overheating and wear.
Missile, Defense, & Radar Systems:
Vacuum and high-pressure sensors monitor guided missile launch systems, ensuring proper pressure stabilization during ignition sequences.
Radar cooling system pressure monitors regulate fluid flow in phased array radar and military communication infrastructure, ensuring optimal system performance.
Blast overpressure sensors provide real-time measurement of shock waves and explosion impact for military testing and defense applications.
Key Purchasing Considerations
Choosing the right pressure monitoring and regulation instrumentation for aerospace and defense applications requires evaluating fluid properties, environmental conditions, regulatory requirements, and system compatibility. The following factors should guide decision-making:
Accuracy & Sensitivity:
High-precision pressure transducers (0.1% or better accuracy) are required for flight control hydraulics, cabin pressurization, and propulsion systems.
Low-drift, high-repeatability sensors ensure long-term stability in space missions, unmanned vehicles, and remote military operations.
Extreme Environment Durability:
Cryogenic-rated pressure sensors withstand temperatures as low as -320°F (-196°C) for LOX and LH₂ storage.
High-temperature sensors operate in combustion chambers, exhaust systems, and hypersonic vehicles.
Radiation-hardened and shock-resistant sensors ensure performance in space exploration and defense combat environments.
Material Compatibility & Corrosion Resistance:
Titanium, Hastelloy, and stainless steel sensor housings are necessary for fuel systems, cryogenic applications, and aerospace coolants.
Hermetically sealed and explosion-proof designs protect against extreme altitude, vacuum, and high-G acceleration forces.
Integration with Control & Monitoring Systems:
SCADA, PLC, and real-time telemetry-compatible sensors enable seamless integration into flight control systems, satellite telemetry, and defense monitoring platforms.
CAN bus, Modbus, and HART-enabled sensors provide digital diagnostics and data logging for aerospace safety compliance.
Compliance with Aerospace & Defense Standards:
Ensure sensors meet FAA, NASA, AS9100, MIL-STD, and ITAR regulations for aerospace and defense applications.
Pressure sensors in military aircraft and space propulsion systems must meet DO-160 and MIL-STD-810 environmental testing requirements.
Reliability & Maintenance Needs:
Self-calibrating, drift-resistant pressure sensors reduce the need for frequent recalibration in long-duration space and defense missions.
Fail-safe pressure monitoring systems with redundancy enhance reliability in propulsion, fuel, and hydraulic networks.
Temperature Sensing & Control
Precise temperature sensing and control are critical in aerospace and defense applications, where extreme operating conditions demand high-accuracy thermal monitoring for fuel systems, propulsion, avionics, and structural integrity. Components in aircraft, spacecraft, missiles, and military vehicles are exposed to high-speed airflow, combustion heat, cryogenic cooling, and extreme environmental fluctuations. Maintaining stable temperatures ensures optimal performance, reliability, and compliance with FAA, NASA, and military standards. Advanced RTDs, thermocouples, infrared sensors, and thermal imaging systems enable real-time data collection, predictive maintenance, and automated thermal regulation in mission-critical aerospace and defense systems.
Temperature Sensing & Control Applications for Aerospace & Defense
Temperature monitoring and thermal control are essential for mission success, safety, and efficiency in aerospace and defense operations. Key applications include:
Aircraft & Spacecraft Thermal Management:
RTDs (Resistance Temperature Detectors) and high-temperature thermocouples monitor engine combustion temperatures, exhaust gas temperatures (EGT), and turbine blade conditions in jet engines.
Infrared thermal sensors provide non-contact temperature measurement in reentry vehicles, heat shields, and space station modules exposed to extreme external conditions.
Cryogenic temperature probes regulate liquid hydrogen (LH₂) and liquid oxygen (LOX) cooling systems in rocket propulsion and deep-space exploration vehicles.
Missile & Defense System Temperature Control:
High-temperature thermocouples monitor warhead and missile propulsion system heat buildup, preventing overheating in hypersonic and guided missile systems.
Thermal imaging and heat flux sensors track temperature variations in defense radar systems, missile launch platforms, and battlefield electronics.
Infrared thermography systems enhance stealth technology in military aircraft, ensuring heat signature reduction in combat applications.
Avionics & Electronics Cooling Systems:
Micro-thermocouples and surface-mounted temperature sensors regulate onboard avionics, cockpit displays, and flight control systems to prevent overheating in military aircraft.
Liquid cooling system temperature monitors manage heat dissipation in high-power radar arrays, communication systems, and satellite electronics.
Thermal runaway sensors in lithium-ion battery systems detect overheating risks in UAVs, satellites, and military-grade power storage.
Fuel System & Hydraulic Fluid Temperature Control:
Immersion temperature sensors ensure proper viscosity and flow of aviation fuel, cryogenic rocket propellants, and hydraulic fluids.
Heat exchangers with integrated temperature sensors regulate cooling loops in fuel tanks and engine lubrication systems.
Self-regulating heating elements prevent fuel freezing at high altitudes, improving efficiency and safety in long-duration flights.
Military Vehicle & Naval Vessel Temperature Regulation:
Infrared thermal sensors track heat dissipation in armored vehicles, naval ship propulsion systems, and active cooling systems.
Heat-resistant temperature probes monitor jet afterburner temperatures and exhaust heat signatures, improving stealth and operational efficiency.
Fire detection thermal sensors provide early warning of excessive heat buildup in engine compartments and weapons systems.
Key Purchasing Considerations
Selecting temperature sensing and control instrumentation for aerospace and defense applications requires evaluating thermal range, environmental durability, regulatory compliance, and integration with monitoring systems. The following considerations should guide decision-making:
Accuracy & Response Time:
High-precision RTDs (±0.1°C accuracy) and fast-response thermocouples ensure real-time monitoring of rapid temperature fluctuations in jet engines and space vehicles.
Infrared temperature sensors with millisecond response times enable non-contact heat monitoring in hypersonic and high-speed aircraft applications.
Extreme Environment Durability:
Cryogenic-rated temperature sensors (-320°F/-196°C) withstand liquid hydrogen and liquid oxygen cooling conditions in rocket propulsion.
High-temperature thermocouples (up to 2,200°F/1,200°C) are required for afterburners, missile propulsion, and hypersonic flight.
Radiation-hardened and high-altitude-rated sensors ensure performance in deep-space missions and military satellite applications.
Material Compatibility & Corrosion Resistance:
Inconel, platinum, and ceramic-coated sensors provide thermal resistance in extreme aerospace environments.
Hermetically sealed temperature probes protect against moisture, corrosive fuels, and pressurized cabin conditions.
System Integration & Smart Monitoring:
SCADA, PLC, and telemetry-compatible temperature sensors enable real-time data collection in military vehicles, UAVs, and satellite networks.
Digital temperature controllers (Modbus, HART, CAN bus compatible) ensure automated thermal regulation in avionics and propulsion systems.
Compliance with Aerospace & Military Standards:
Ensure compliance with FAA, NASA, AS9100, MIL-STD, and ITAR regulations for aerospace and defense applications.
Sensors used in military aircraft and space missions must meet DO-160 and MIL-STD-810 testing requirements for environmental conditions.
Reliability & Maintenance Efficiency:
Self-diagnostic and drift-resistant temperature sensors reduce calibration requirements in long-duration aerospace applications.
Dual-redundancy thermal sensors improve reliability in mission-critical propulsion and fuel monitoring systems.
Level Detection & Management
Accurate level detection and management are critical for fuel systems, hydraulic reservoirs, cryogenic propellant storage, and coolant tanks in aerospace and defense applications. Maintaining precise fluid levels ensures system reliability, operational efficiency, and compliance with FAA, NASA, and military regulations. Radar, ultrasonic, capacitive, and guided wave level sensors provide real-time monitoring and automated control for liquid oxygen (LOX), liquid hydrogen (LH₂), jet fuel, hydraulic fluids, and coolant levels in extreme conditions such as high altitudes, deep-space environments, and combat operations.
Level Detection & Management Applications in Aerospace & Military Applications
Level detection plays a vital role in fuel, hydraulic, and environmental systems in aircraft, spacecraft, and military infrastructure. Advanced level sensors help prevent system failures, optimize resource utilization, and ensure mission-critical readiness.
Aerospace Fuel & Cryogenic Propellant Monitoring:
Radar and guided wave level sensors provide continuous fuel level monitoring in aircraft, rockets, and UAVs, ensuring optimal propulsion system performance.
Cryogenic-compatible level transmitters regulate liquid hydrogen (LH₂) and liquid oxygen (LOX) storage in rocket propulsion systems and space station life support systems.
Dielectric-based capacitive level sensors ensure precise measurement of aviation fuel levels in extreme temperature and pressure conditions.
Hydraulic Fluid & Lubrication System Level Monitoring:
Ultrasonic level sensors measure hydraulic fluid levels in landing gear actuators, control surfaces, and braking systems, preventing mechanical failures.
Load cell-based level monitoring ensures proper lubricant levels in jet engines, turbines, and military ground vehicles, reducing friction and overheating risks.
Differential pressure level sensors track coolant and hydraulic fluid levels in fighter jets, helicopters, and spacecraft, ensuring continuous performance.
Missile & Defense Infrastructure Level Control:
Radar and optical level sensors monitor fuel and oxidizer levels in guided missile launch systems, ensuring precise fuel mixture and reliable ignition.
Acoustic wave and float-based level detectors provide high-accuracy monitoring for liquid propellant tanks in ballistic and hypersonic missile systems.
TDR (Time-Domain Reflectometry) sensors measure fuel levels in autonomous military vehicles and unmanned defense drones for optimal mission endurance.
Spacecraft Environmental & Life Support Systems:
Non-contact radar level sensors regulate water supply and wastewater storage in long-duration space missions, ensuring closed-loop resource management.
Capacitive level detectors monitor oxygen and nitrogen reserves in spacecraft life support systems, maintaining habitable conditions in space stations.
Cryogenic level probes track thermal control fluid levels in satellite cooling systems and interplanetary exploration vehicles.
Military Ship & Submarine Level Detection:
Submersible hydrostatic level sensors track ballast water, fuel, and coolant levels in naval vessels and submarines, optimizing buoyancy and stability.
Ultrasonic and guided wave radar sensors provide real-time monitoring of diesel and nuclear reactor coolant levels, ensuring reactor safety in combat conditions.
Automated level control systems integrate with shipboard SCADA systems, improving efficiency in fuel distribution and onboard fluid management.
Key Purchasing Considerations
Selecting the right level detection and management instrumentation for aerospace and military applications requires evaluating fluid properties, environmental conditions, regulatory requirements, and system integration capabilities. The following factors should guide decision-making:
Accuracy & Sensor Sensitivity:
Radar and guided wave level sensors offer high accuracy for cryogenic propellant and aviation fuel monitoring.
Differential pressure and hydrostatic level transmitters provide stable readings in high-altitude and high-pressure aerospace systems.
Extreme Environmental Durability:
Cryogenic-rated level sensors (-320°F/-196°C) withstand extreme cold conditions in space missions and liquid hydrogen storage tanks.
High-temperature level detectors operate in missile propulsion and afterburner fuel tanks, where heat resistance is crucial.
Radiation-hardened sensors ensure functionality in deep-space exploration, satellite systems, and nuclear-powered defense applications.
Material Compatibility & Corrosion Resistance:
Stainless steel, titanium, and Hastelloy level sensors are necessary for jet fuel, cryogenic propellants, and hydraulic fluid applications.
Hermetically sealed, explosion-proof designs protect against moisture, corrosion, and extreme atmospheric pressures.
Integration with Military & Aerospace Control Systems:
SCADA, PLC, and telemetry-compatible level sensors enable remote monitoring of aircraft, spacecraft, and defense infrastructure.
HART, Modbus, and CAN bus communication protocols ensure seamless data integration with flight control, satellite telemetry, and defense logistics.
Compliance with Aerospace & Military Standards:
Ensure compliance with FAA, NASA, AS9100, MIL-STD, and ITAR regulations for level detection in aerospace and military applications.
Sensors used in military aircraft and space missions must meet DO-160 and MIL-STD-810 environmental test requirements.
Reliability & Maintenance Considerations:
Self-diagnostic level sensors with automated calibration minimize maintenance needs in long-duration space missions and autonomous defense systems.
Fail-safe level detection with redundancy enhances reliability in critical fuel and hydraulic networks, ensuring mission continuity.
Vibration & Structural Health
Vibration & Structural Health Monitoring Applications for Aerospace Equipment
Vibration and structural monitoring systems provide critical diagnostics and early failure detection, ensuring reliability, safety, and extended operational life of aerospace and military equipment. Key applications include:
Aircraft & Spacecraft Structural Health Monitoring:
Tri-axial accelerometers and MEMS vibration sensors detect structural fatigue, high-frequency oscillations, and excessive mechanical loads in aircraft fuselages, wings, and rotorcraft blades.
Strain gauges and fiber optic sensors track real-time stress distribution in composite and metallic airframe structures, helping prevent catastrophic failures.
Smart material-embedded SHM systems monitor fatigue life in spacecraft hulls and thermal expansion in satellite components under extreme temperature variations.
Propulsion System Vibration & Engine Health Monitoring:
Piezoelectric vibration sensors analyze turbofan, turboprop, and rocket engine oscillations, providing early warnings of bearing wear, unbalanced rotors, or combustion instabilities.
High-temperature accelerometers monitor vibration-induced thermal stress in jet turbines, missile propulsion systems, and scramjet engines.
Shock and impact sensors detect abnormal pressure waves and engine resonance in high-thrust aerospace applications.
Military Vehicle & Defense Infrastructure Monitoring:
Seismic and structural motion sensors provide blast wave detection and structural integrity monitoring for military bunkers, defense installations, and naval ship hulls.
Vibration and shock sensors in ground vehicles track suspension system performance, chassis fatigue, and impact damage in armored personnel carriers and tactical trucks.
Real-time vibration monitoring of rail gun and artillery systems ensures safe operation and recoil impact assessment.
Missile & Hypersonic Flight Vibration Analysis:
High-G shock sensors and strain gauges measure vibrational loads in ballistic and cruise missile flight paths, ensuring payload stability.
Aeroelastic monitoring systems detect structural oscillations and aerodynamic flutter in hypersonic vehicles and reentry capsules.
Pressure and vibration correlation sensors track shock wave interactions in supersonic and hypersonic propulsion systems, optimizing performance and reliability.
Rotating Equipment & UAV Structural Monitoring:
Wireless vibration monitoring systems provide continuous tracking of UAV rotor performance, structural load balancing, and fuselage stress in autonomous defense aircraft.
Gyroscopic and inertial sensors help detect vibration-induced drift in navigation and targeting systems for military drones and reconnaissance aircraft.
Aerospace-grade MEMS accelerometers monitor flight control actuators, engine mounts, and wing load distribution, preventing in-flight mechanical failures.
Key Purchasing Considerations
Selecting the right vibration and structural health monitoring instrumentation for aerospace and military applications requires evaluating system compatibility, environmental durability, and compliance factors. The following considerations should guide decision-making:
Accuracy & Sensor Sensitivity:
Tri-axial accelerometers and MEMS sensors ensure high-resolution monitoring of low-amplitude vibrations and high-frequency oscillations.
Piezoelectric vibration sensors provide real-time alerts for bearing failures, rotor imbalances, and excessive stress loads.
High-temperature accelerometers enable vibration monitoring in jet engines, missile propulsion, and afterburner systems.
Durability in Extreme Aerospace Environments:
Shock-resistant, high-G vibration sensors are required for missile launches, hypersonic vehicles, and ballistic reentry vehicles.
Radiation-hardened and cryogenic-capable strain gauges ensure reliability in satellite structures and deep-space exploration.
Hermetically sealed sensors protect against moisture, fuel exposure, and extreme pressure differentials.
Integration with Aerospace Control & Safety Systems:
SCADA, PLC, and telemetry-compatible vibration sensors provide real-time diagnostics in military aircraft, spacecraft, and naval defense systems.
Digital output accelerometers with CAN bus, Modbus, or HART communication allow seamless integration into automated safety and maintenance systems.
Wireless vibration monitoring networks enable remote diagnostics in unmanned aerial systems (UAS) and defense infrastructure.
Compliance with Aerospace & Military Standards:
Ensure compliance with FAA, NASA, AS9100, MIL-STD, and ITAR regulations for aerospace and defense applications.
Sensors used in military aircraft and space missions must meet DO-160, MIL-STD-810, and ASME structural integrity standards.
Reliability & Predictive Maintenance Capabilities:
Self-diagnostic vibration sensors with automated calibration improve reliability in long-duration space missions and military deployments.
Embedded AI-powered SHM systems analyze vibration patterns and detect structural weaknesses before critical failures occur.
Multi-sensor redundancy enhances structural monitoring reliability in mission-critical aircraft, naval vessels, and missile systems.
Gas Detection & Environmental Monitoring
Ensuring air quality and environmental safety is critical in aerospace and defense applications, where enclosed environments, high-altitude operations, and hazardous materials pose risks to personnel and equipment. Real-time gas detection and environmental monitoring systems protect pilots, astronauts, ground crews, and defense personnel from exposure to oxygen depletion, toxic gases, combustion byproducts, and volatile organic compounds (VOCs). Advanced infrared (IR), electrochemical, photoionization, and catalytic bead sensors provide early leak detection, air quality analysis, and compliance with FAA, NASA, and military safety standards.
Gas Detection & Environmental Monitoring Applications in Aerospace & Defense
Gas detection plays a crucial role in life support systems, fuel storage, propulsion monitoring, and hazardous material handling in military and aerospace settings. Key applications include:
Aircraft & Spacecraft Life Support Systems:
Oxygen (O₂) and carbon dioxide (CO₂) sensors ensure safe breathing conditions in pressurized aircraft cabins, space station modules, and long-duration space missions.
Trace gas analyzers detect nitrogen (N₂) imbalances, preventing hypoxia and decompression sickness in high-altitude flight operations.
Ammonia (NH₃) and hydrogen sulfide (H₂S) sensors monitor air quality in spacecraft wastewater recycling and closed-loop environmental control systems.
Rocket Propulsion & Fuel System Leak Detection:
Infrared gas analyzers detect methane (CH₄), hydrogen (H₂), and oxygen (O₂) leaks in cryogenic fuel storage, booster stages, and launch pad systems.
Electrochemical hydrogen sensors prevent H₂ buildup in fuel cells and high-energy propulsion systems, reducing explosion risks.
VOC sensors and flame ionization detectors (FIDs) ensure safe handling of hypergolic propellants in missile and spacecraft fueling operations.
Military Vehicle & Submarine Air Quality Monitoring:
CO and NO₂ sensors track diesel exhaust buildup in military ground vehicles, armored personnel carriers (APCs), and naval vessels.
Multi-gas analyzers monitor confined air quality in submarine oxygen regeneration systems, ensuring long-duration operational safety.
Particulate matter (PM) sensors measure airborne contaminants in aircraft carrier hangars, military aircraft repair bays, and confined vehicle maintenance areas.
Defense Facility & Ammunition Storage Safety:
Explosive gas detectors prevent combustion risks in weapons manufacturing, missile silos, and defense storage bunkers.
Chlorine (Cl₂) and fluorine (F₂) gas monitors detect hazardous chemical leaks in military-grade rocket fuel and missile propellants.
Radiation and gas hybrid sensors provide early detection of nuclear material leaks in strategic defense locations.
Airborne & Space-Based Environmental Monitoring:
High-altitude atmospheric sensors track ozone (O₃), carbon monoxide (CO), and greenhouse gases for military reconnaissance and climate analysis.
Laser absorption spectrometers provide real-time air composition analysis in satellite-based environmental monitoring missions.
Hypersonic vehicle gas detectors measure plasma composition and aerodynamic heating effects in reentry vehicles and missile defense systems.
Key Purchasing Considerations
Selecting the right gas detection and environmental monitoring instrumentation for aerospace and defense applications requires evaluating sensor accuracy, environmental durability, and integration capabilities. The following factors should guide decision-making:
Accuracy & Sensitivity:
Electrochemical gas sensors provide high-precision detection for oxygen, CO₂, CO, and toxic gas exposure limits in aircraft and spacecraft environments.
Infrared (IR) and catalytic bead sensors ensure rapid response to combustible gas leaks in fuel storage and missile propulsion systems.
Photoionization detectors (PIDs) monitor VOCs and airborne contaminants in chemical weapons handling and hazardous material transport.
Environmental Durability & Extreme Condition Performance:
Radiation-hardened and cryogenic-compatible gas sensors ensure functionality in space exploration and nuclear-powered defense systems.
Shock-resistant and explosion-proof sensors withstand high-G acceleration, launch vibrations, and military-grade fuel storage conditions.
Hermetically sealed detectors prevent contamination in hyperbaric and vacuum environments such as space stations and defense submarines.
Integration with Military & Aerospace Safety Systems:
SCADA, PLC, and real-time telemetry-compatible gas sensors enable seamless monitoring of aircraft cabins, defense facilities, and UAV platforms.
Wireless and IoT-enabled detectors allow remote air quality tracking in unmanned spacecraft, high-altitude UAVs, and forward operating bases.
Multi-gas detection networks with centralized alert systems improve safety in military bunkers, missile silos, and aircraft fuel farms.
Compliance with Aerospace & Defense Regulations:
Ensure compliance with FAA, NASA, AS9100, MIL-STD, and ITAR regulations for gas detection in aerospace and defense applications.
Sensors used in military aircraft and space missions must meet DO-160, MIL-STD-810, and NIOSH exposure limits for hazardous gases.
Reliability & Maintenance Considerations:
Self-calibrating gas sensors with built-in diagnostics reduce maintenance requirements in remote and space-based defense systems.
Multi-redundant gas detection arrays improve fail-safe reliability in missile fuel handling, submarine oxygen regulation, and combat vehicle environments.
Analytical Instrumentation for Compliance
High-precision analytical instrumentation is essential for aerospace and defense applications, ensuring regulatory compliance, system integrity, and mission reliability. From fuel quality testing and material composition analysis to contaminant detection and environmental monitoring, advanced spectrometers, chromatography systems, particle analyzers, and gas sensors provide real-time data for predictive maintenance, safety assurance, and process optimization. NASA, FAA, and military standards require strict traceability, accuracy, and repeatability, making analytical instrumentation a critical component in manufacturing, propulsion testing, and operational safety.
Analytical Instrumentation Applications for Aerospace & Defense Compliance
Analytical instruments are used across aerospace production, in-flight monitoring, propulsion system diagnostics, and military defense operations to ensure compliance with stringent safety, environmental, and material standards. Key applications include:
Fuel Quality & Contaminant Analysis:
Gas chromatography (GC) and mass spectrometry (MS) analyze aviation fuel purity, hydrocarbon content, and trace contaminants, ensuring compliance with ASTM D1655 and MIL-DTL-5624 fuel standards.
Fourier-transform infrared (FTIR) spectrometers detect chemical degradation in jet fuels, lubricants, and hydraulic fluids, preventing in-flight system failures.
Total organic carbon (TOC) analyzers monitor hydrazine and RP-1 rocket propellant purity, reducing risks of fuel instability and combustion irregularities.
Material Integrity & Coating Verification:
X-ray fluorescence (XRF) and laser-induced breakdown spectroscopy (LIBS) verify alloy composition and surface treatments in aircraft fuselages, spacecraft components, and missile structures.
Optical emission spectroscopy (OES) ensures metal purity in high-strength aerospace materials, preventing failures in extreme environmental conditions.
Thickness and adhesion analyzers test thermal protection coatings in hypersonic vehicles and reentry capsules, ensuring durability and heat resistance.
Environmental & Atmospheric Monitoring in Aerospace Systems:
Gas analyzers and infrared spectrometers detect oxygen, carbon dioxide, and trace gases in pressurized aircraft cabins and spacecraft life support systems.
Airborne particle counters monitor dust, ice, and combustion particles in jet engines and high-altitude flight conditions, ensuring operational safety.
Radioactive isotope detectors provide real-time radiation monitoring in space missions, nuclear-powered aircraft carriers, and military installations.
Hydraulic & Coolant System Contaminant Detection:
Particle analyzers and viscosity meters assess hydraulic fluid quality in aircraft landing gear, flight control actuators, and cooling systems.
Water content analyzers monitor moisture contamination in fuel and hydraulic systems, preventing freezing and corrosion in high-altitude environments.
Electrochemical sensors detect degradation in ethylene glycol and thermal transfer fluids used in spacecraft and defense radar cooling systems.
Weapons & Defense System Performance Testing:
High-speed chromatography and thermal analysis ensure propellant stability and ignition performance in missile guidance systems.
Ballistic trajectory monitoring with spectroscopic sensors enhances precision-guided munition targeting and fuel burn efficiency.
Explosives trace detection (ETD) analyzers ensure safety in military ordnance storage and warhead handling facilities.
Key Purchasing Considerations
Selecting analytical instrumentation for aerospace and defense applications requires evaluating measurement precision, environmental durability, regulatory compliance, and data integration capabilities. The following considerations should guide decision-making:
Measurement Accuracy & Sensitivity:
High-resolution spectrometers (ppm/ppb detection limits) are required for trace contaminant analysis in fuel, lubricants, and air quality monitoring.
Ultra-low background noise chromatography systems improve sample purity verification in rocket fuels and specialty aerospace coatings.
Multi-channel gas analyzers allow simultaneous detection of volatile organic compounds (VOCs) and combustion byproducts in flight environments.
Environmental & Operational Durability:
Shock-resistant and high-vibration tolerant instruments are necessary for onboard aircraft and spacecraft diagnostics.
Cryogenic-compatible analyzers ensure accurate readings in LOX/LH₂ rocket fuel testing and deep-space environmental analysis.
Explosion-proof and intrinsically safe analytical sensors are required for fuel handling and military explosives testing.
Compliance with Aerospace & Military Standards:
Ensure compliance with FAA, NASA, MIL-STD, AS9100, and ITAR regulations for aerospace and defense analytical applications.
ISO 17025 calibration-certified analyzers provide traceable measurements for aviation maintenance, weapons testing, and propulsion research.
Instruments must meet DO-160 and MIL-STD-810 ruggedization standards for harsh environmental conditions in aerospace and defense settings.
Data Integration & Automation Capabilities:
SCADA, PLC, and cloud-based telemetry-compatible analyzers enable real-time monitoring of fuel quality, atmospheric conditions, and system integrity.
Automated spectrometric analysis with AI-driven pattern recognition enhances predictive maintenance in aviation and defense infrastructure.
Remote and portable gas chromatography systems allow field-deployable diagnostics in military bases, unmanned aerial vehicles (UAVs), and space missions.
Maintenance & Lifecycle Costs:
Self-calibrating and auto-zeroing analyzers reduce maintenance needs in long-duration space missions and military deployments.
Replaceable sensor modules extend operational life in jet engine emission monitoring and propellant storage analysis.
Multi-parameter analytical stations consolidate multiple functions, minimizing instrument footprint in aircraft and defense field operations.
Industry Standards & Regulatory Compliance
Aerospace and defense operations must adhere to strict regulatory and compliance standards to ensure safety, reliability, and mission success. Organizations such as the Federal Aviation Administration (FAA), National Aeronautics and Space Administration (NASA), Department of Defense (DoD), and international aerospace regulatory bodies establish comprehensive guidelines for aircraft systems, propulsion technologies, structural integrity, and environmental impact. Compliance with these standards requires advanced instrumentation, data logging systems, and real-time monitoring technologies to validate performance, detect anomalies, and maintain operational safety across military, commercial, and spaceflight applications.
FAA, NASA, and Military Compliance for Aerospace & Defense
The aerospace and defense industries must comply with FAA airworthiness regulations, NASA spaceflight safety standards, and military specifications (MIL-STD, AS9100, ITAR) to ensure quality, performance, and risk mitigation. Aircraft and spacecraft must meet DO-160 environmental testing requirements, governing factors such as vibration, electromagnetic interference (EMI), temperature resistance, and material durability. Military aviation and defense programs follow MIL-STD-810 for environmental ruggedization, MIL-STD-461 for EMI compliance, and MIL-STD-704 for electrical power system safety. Adherence to AS9100 quality management standards is essential for aerospace manufacturing, requiring rigorous traceability, testing, and documentation for all critical components. These regulations ensure that aerospace and defense systems perform under extreme environmental conditions and mission-critical scenarios while maintaining reliability, redundancy, and fail-safe operations.
Environmental and Safety Standards in Defense & Space Applications
The aerospace and defense sectors must also comply with environmental safety and emissions regulations, ensuring sustainable operations while minimizing hazardous exposure risks. The Environmental Protection Agency (EPA) and Department of Defense (DoD) enforce regulations for fuel emissions, hazardous material handling, and waste disposal to reduce the environmental impact of military and aerospace operations. Clean Air Act (CAA) and ICAO emissions standards set limits on aircraft engine emissions, requiring continuous combustion gas analysis and air quality monitoring. In space applications, NASA planetary protection protocols and space debris mitigation policies regulate fuel handling, launch vehicle emissions, and spacecraft end-of-life disposal. Additionally, radiation safety compliance is enforced through IAEA and NASA space radiation exposure guidelines, ensuring astronaut health and system protection in deep-space environments. These regulatory frameworks and compliance standards guide the industry in maintaining mission readiness, operational safety, and environmental responsibility while advancing aerospace and defense technologies.
Benefits of Working With Clipper Controls
Clipper Controls provides high-precision instrumentation and automation solutions for aerospace and defense applications, ensuring compliance, safety, and operational efficiency. Our flow meters, pressure sensors, gas analyzers, and vibration monitors support propulsion testing, fuel management, structural health monitoring, and environmental control, optimizing mission-critical systems.
Our ruggedized, high-accuracy instrumentation withstands extreme aerospace conditions, from hypersonic flight to deep-space missions. By partnering with us, aerospace and defense organizations can enhance performance, minimize risks, and achieve mission success.
Case Studies & Success Stories
Explore real-world examples of how Clipper Controls has helped aerospace and defense organizations optimize fuel management, enhance structural integrity, and ensure regulatory compliance.
Click here to read our aerospace & defense case studies.
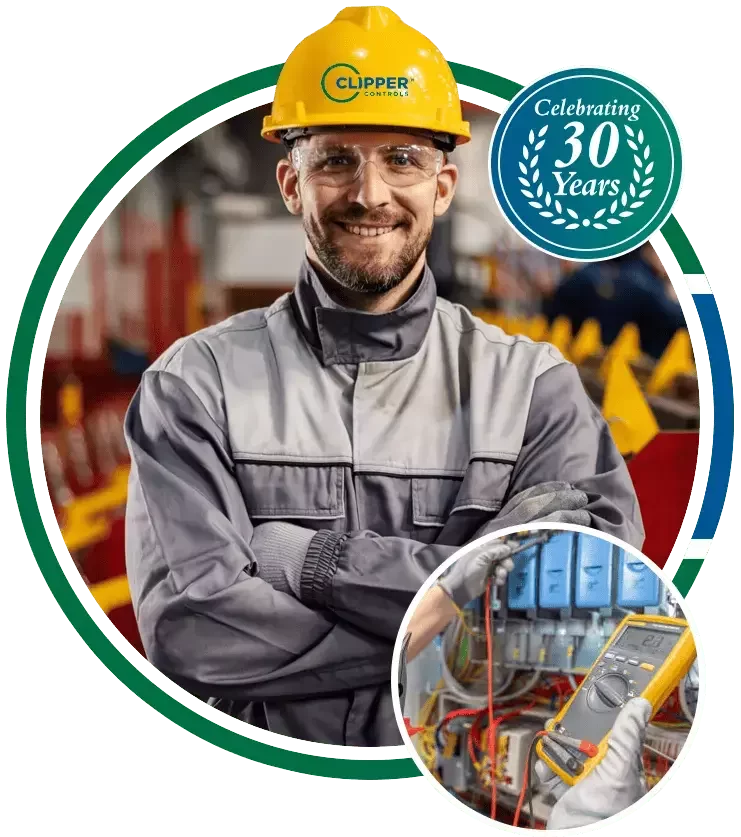
Real Results, Real Impact:
Thanks to Clipper Controls, our wastewater treatment plant improved efficiency & compliance with top-tier flow meters. Reliable solutions, great support! We recommend Clipper Controls to all our partner companies.
~ John Smith, Controls Engineer @ ABC Company
Clipper Controls helped our city upgrade water monitoring systems, ensuring accuracy & compliance. Reliable solutions & excellent customer service!
~ Nancy Patel, Procurement @ ABC Company
~ John Smith, Controls Engineer @ ABC Company
Ready to Work With Us?
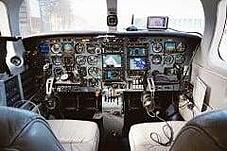
Quick Page Navigation:
🔹How Our Products Support Your Industry
Pressure Monitoring & Regulation
Temperature Sensing & Control
Vibration & Structural Monitoring
Gas Detection & Environmental Monitoring
Analytical Instrumentation for Compliance
🔹Industry Standards & Regulatory Compliance
🔹Benefits of Working With Clipper Controls