Energy Extraction, Recapture, Generation, & Distribution Applications
Application Overview
How Our Products Support Your Industry
Key Applications and Solutions
Flow Measurement & Control
Applications of Flow Measurement & Control in Energy Extraction, Recapture, Generation, and Distribution Applications
- Flow meters measure landfill gas composition and volume to optimize gas collection and ensure efficient conversion into usable energy.
- Thermal mass flow meters help detect leaks and inefficiencies in methane extraction systems.
- Ultrasonic and Coriolis flow meters track biogas flow rates for processing into RNG and injection into pipeline systems.
- Flow control valves regulate steam and hot water distribution in wastewater treatment plant cogeneration systems.
- Magnetic flow meters measure wastewater and sludge movement, ensuring efficient energy recapture from anaerobic digestion.
- Vortex flow meters help monitor steam flow in heat recovery processes.
- Electromagnetic and ultrasonic flow meters measure water flow rates through turbines to optimize energy production.
- Steam flow meters regulate geothermal energy production by monitoring vapor movement from subterranean reservoirs.
- Differential pressure flow meters help maintain efficiency in superheated steam distribution.
- Coriolis and positive displacement meters measure fuel flow in refineries and ensure proper blending of petroleum products.
- Ultrasonic and turbine flow meters monitor pipeline gas and liquid flows, detecting leaks and ensuring precise custody transfer.
- Variable area flow meters provide reliable flow measurement for hydraulic fracturing and crude oil transport.
- Flow meters track thermal fluid movement in concentrated solar power plants, optimizing heat exchange efficiency.
- Mass flow controllers regulate hydrogen production via electrolysis, ensuring proper gas separation and storage.
- Ultrasonic and thermal flow meters monitor hydrogen distribution pipelines for safe and efficient transport.
Key Purchasing Considerations
- Ensure flow meters are suitable for gas (methane, hydrogen, steam) or liquid (crude oil, water, thermal fluids).
- Consider corrosion resistance in aggressive environments, such as landfill gas extraction or chemical processing.
- High-precision instruments like Coriolis and ultrasonic meters are crucial for custody transfer and fiscal metering.
- For applications with fluctuating flows, such as renewable energy systems, look for adaptive control mechanisms.
- Consider temperature, pressure, and viscosity variations when selecting flow meters.
- Space limitations may require compact or inline meters instead of large, intrusive devices.
- Select meters certified for industry standards such as API (oil & gas), AGA (natural gas), and ISO 5167 (differential pressure flow meters).
- Ensure compliance with environmental regulations, including emissions monitoring and carbon accounting.
- Choose smart flow meters with digital protocols (HART, Modbus, Profibus) for seamless integration into SCADA and PLC systems.
- Wireless and remote monitoring capabilities enhance real-time data collection and system diagnostics.
- Non-intrusive technologies like ultrasonic flow meters reduce maintenance needs by eliminating moving parts.
- Devices with self-diagnostic and predictive maintenance features minimize downtime and optimize operational efficiency
Pressure Monitoring & Regulation
Applications of Pressure Monitoring & Regulation in Energy Extraction, Recapture, Generation, and Distribution Applications
- Pressure transmitters monitor gas well extraction pressures, optimizing methane collection efficiency.
- Differential pressure (DP) sensors track pressure variations in gas cleaning and upgrading systems, ensuring proper filtration and separation of contaminants.
- Pressure regulators maintain consistent pressure in RNG injection into natural gas pipelines, preventing fluctuations that could impact grid stability.
- Pressure sensors in anaerobic digesters regulate biogas collection to prevent over-pressurization and ensure efficient gas storage.
- Steam pressure transmitters optimize energy recovery in cogeneration plants by ensuring proper steam turbine operation.
- Pump pressure monitoring helps maintain consistent flow rates in wastewater heat recovery systems.
- High-accuracy pressure sensors monitor water column pressures in hydroelectric dams, optimizing turbine efficiency.
- Steam pressure monitoring in geothermal plants ensures safe and efficient extraction from underground reservoirs.
- Subsurface pressure transmitters provide real-time data on reservoir performance and geothermal fluid dynamics.
- Pressure regulators maintain optimal levels in gas pipelines, preventing pressure drops that could disrupt downstream operations.
- Differential pressure meters ensure proper filtration efficiency in refineries, protecting downstream processing equipment.
- High-pressure transmitters monitor wellhead pressure in drilling and fracking applications, preventing blowouts and optimizing extraction.
- Pressure sensors track heat transfer fluid pressures in concentrated solar power plants, maintaining thermal efficiency.
- Hydrogen electrolysis systems rely on precise pressure regulation to ensure safe gas separation and storage.
- Hydrogen pipeline pressure monitoring prevents leaks and ensures safe distribution for industrial and transportation applications.
Key Purchasing Considerations
- Select sensors that can handle the expected pressure range, from low-pressure gas monitoring to high-pressure steam applications.
- High-precision pressure transmitters are essential for critical operations such as custody transfer, gas compression, and turbine regulation.
- Consider materials resistant to harsh environments, such as stainless steel or corrosion-resistant coatings for landfill gas and hydrogen applications.
- Ensure compatibility with high-temperature and high-moisture conditions in geothermal and steam-based energy systems.
- Ensure pressure instruments meet regulatory requirements, such as ASME, ANSI, API, and OSHA safety standards.
- Explosion-proof and intrinsically safe designs may be required for hazardous environments, such as hydrogen production and oil refining.
- Smart pressure transmitters with digital protocols (HART, Modbus, Profibus) enhance integration with SCADA and DCS systems.
- Wireless pressure monitoring solutions provide remote access and real-time alerts for critical systems.
- Choose devices with self-diagnostic capabilities for predictive maintenance, reducing downtime and operational disruptions.
- Non-contact and solid-state pressure sensors minimize wear and extend service life in demanding energy applications.
Temperature Sensing & Control
Applications of Temperature Sensing & Control in Energy Extraction, Recapture, Generation, and Distribution Applications
- Temperature sensors monitor landfill gas well temperatures, ensuring optimal methane extraction conditions.
- Infrared and RTD sensors control heat levels in gas upgrading systems to maximize the removal of contaminants like CO₂ and H₂S.
- Thermal flow controllers regulate temperatures in pipeline injection systems, preventing condensation and energy loss.
- Temperature transmitters measure anaerobic digester heat levels to optimize biogas production and microbial activity.
- Steam temperature monitoring ensures efficient energy recovery in wastewater cogeneration plants.
- Heat exchanger sensors regulate wastewater temperature in heat recapture systems to maximize efficiency.
- RTD and thermocouple sensors measure water and steam temperatures in hydroelectric and geothermal plants to optimize turbine performance.
- Subsurface geothermal sensors track reservoir heat levels, ensuring efficient and sustainable energy extraction.
- High-temperature thermocouples monitor steam pipelines, ensuring proper distribution and preventing thermal stress.
- Temperature sensors in crude oil refining control heat levels during distillation and cracking processes.
- Thermal monitoring of natural gas pipelines prevents hydrate formation and ensures safe transport.
- Heat tracing systems use temperature sensors to prevent freezing in pipelines and ensure consistent flow.
- Infrared and RTD sensors monitor solar collector temperatures, optimizing heat transfer efficiency in concentrated solar power (CSP) plants.
- Electrolysis systems use temperature sensors to regulate hydrogen production, preventing overheating of electrodes and membranes.
- Thermal sensors in hydrogen storage and distribution systems detect temperature fluctuations that could impact safety and efficiency.
Key Purchasing Considerations
- Choose sensors with appropriate temperature range capabilities for applications from cryogenic LNG storage to high-temperature geothermal steam monitoring.
- High-accuracy RTDs are preferred for precise thermal control in critical energy processes.
- Thermocouples provide fast response times, making them ideal for dynamic temperature fluctuations in combustion and turbine applications.
- Infrared temperature sensors enable non-contact measurement for high-temperature processes and hazardous environments.
- RTDs offer long-term stability for consistent thermal monitoring in pipeline and refinery applications.
- Consider corrosion-resistant and explosion-proof sensor housings for use in harsh environments such as refineries and geothermal fields.
- High-pressure thermowells protect temperature probes in steam and high-temperature fluid applications.
- Ensure sensors meet industry standards such as ASTM, IEC, and ANSI for temperature measurement accuracy and reliability.
- Compliance with hazardous location certifications (ATEX, CSA, or UL) is essential for high-risk energy environments.
- Digital temperature transmitters with HART, Modbus, or Profibus compatibility facilitate integration with SCADA and control systems.
- Wireless temperature sensors provide real-time monitoring for remote energy applications.
- Select self-calibrating temperature sensors to minimize downtime and improve process efficiency.
- Devices with predictive maintenance capabilities enhance system reliability by detecting sensor drift or failure before issues arise.
Level Detection & Management
Applications of Level Detection & Management in Energy Extraction, Recapture, Generation, and Distribution Applications
- Radar level sensors monitor condensate levels in gas collection wells to prevent liquid accumulation that could restrict gas flow.
- Ultrasonic level transmitters track levels in digester tanks and biogas storage units, ensuring optimal gas production.
- Capacitive level sensors detect foam buildup in gas scrubbing units, optimizing chemical dosing for gas purification.
- Float switches and radar sensors monitor liquid levels in anaerobic digesters, optimizing biogas yield and preventing overflow.
- Guided wave radar level transmitters control hot water and steam levels in cogeneration boilers, ensuring safe and efficient operation.
- Hydrostatic level sensors manage sludge levels in energy recovery processes, optimizing solid-liquid separation.
- Ultrasonic level sensors track reservoir water levels to ensure optimal hydroelectric turbine operation.
- High-temperature guided wave radar sensors monitor geothermal brine levels in flash steam plants to optimize power generation.
- Subsurface level detection systems monitor geothermal resource depletion, ensuring sustainable energy extraction.
- Radar level gauges monitor crude oil and refined fuel storage tanks for inventory management and leak prevention.
- Differential pressure level sensors measure liquid levels in distillation columns, ensuring optimal refining efficiency.
- Non-contact ultrasonic level sensors detect levels in pressurized natural gas storage tanks, preventing overfilling and ensuring regulatory compliance.
- Capacitive level sensors monitor thermal fluid levels in concentrated solar power (CSP) plants, ensuring efficient heat transfer.
- Hydrogen electrolysis systems use ultrasonic and guided wave radar sensors to track water levels for consistent hydrogen production.
- Cryogenic level sensors provide accurate measurements in liquid hydrogen storage tanks, ensuring safety and efficiency in fuel cell applications.
Key Purchasing Considerations
- Radar sensors offer reliable performance in challenging environments, such as steam-filled geothermal plants and high-pressure oil refineries.
- Ultrasonic sensors provide non-contact level measurement, ideal for hazardous and corrosive liquid storage applications.
- Float switches and hydrostatic sensors are cost-effective solutions for basic level monitoring in wastewater and cogeneration applications.
- Consider compatibility with liquids, slurries, and gases when selecting level sensors.
- High-temperature and pressure-resistant sensors are essential for geothermal, steam, and refinery applications.
- Corrosion-resistant materials are required for aggressive chemical environments, such as landfill gas and hydrogen production.
- Choose sensors with high accuracy for critical applications such as custody transfer and pipeline storage management.
- Look for self-cleaning or maintenance-free sensors to ensure long-term reliability in dirty or high-viscosity applications.
- Ensure level sensors meet industry standards such as API, ASME, and IEC for energy and industrial applications.
- Explosion-proof and intrinsically safe designs may be required for hazardous locations, such as oil refineries and hydrogen storage facilities.
- Smart level sensors with HART, Modbus, and Profibus compatibility enable seamless integration into SCADA and industrial automation systems.
- Wireless level sensors provide remote monitoring capabilities, improving real-time process control and operational efficiency.
- Opt for sensors with predictive maintenance features to reduce downtime and operational disruptions.
- Consider total cost of ownership, including installation, calibration, and long-term reliability, when selecting level management solutions.
Gas & Flame Detection for Safety Compliance
Gas and flame detection is essential in the energy sector to protect personnel, assets, and the environment from hazardous leaks, fires, and explosions. Effective detection systems ensure compliance with safety regulations while preventing catastrophic failures in extraction, recapture, generation, and distribution processes. Advanced sensors, alarms, and automated shutdown systems help mitigate risks by providing early warning of combustible gases, toxic vapors, and fire hazards.
Applications of Gas & Flame Detection in Energy Extraction, Recapture, Generation, and Distribution Applications
- Methane (CH₄) sensors detect leaks in gas collection and processing systems, preventing fire and explosion risks.
- Hydrogen sulfide (H₂S) gas detectors protect workers from toxic exposure in landfill gas upgrading facilities.
- Infrared flame detectors provide early fire detection in biogas storage and flaring systems.
- Gas sensors monitor biogas storage tanks for methane, carbon dioxide (CO₂), and hydrogen sulfide buildup.
- Catalytic bead sensors detect leaks in anaerobic digesters, preventing ignition hazards in confined spaces.
- UV/IR flame detectors ensure fire suppression systems are activated in cogeneration plants using waste heat recovery.
- Hydrogen gas sensors prevent accumulation in generator cooling systems, reducing the risk of explosions.
- Sulfur dioxide (SO₂) and hydrogen sulfide (H₂S) detectors monitor geothermal emissions to ensure compliance with air quality regulations.
- Multi-spectrum flame detectors provide rapid fire detection in steam turbine enclosures and high-temperature environments.
- Fixed and portable gas detectors monitor volatile organic compounds (VOCs) and hydrocarbon vapors in refineries.
- Infrared gas detectors provide real-time monitoring of pipeline leaks, reducing environmental and safety risks.
- Explosion-proof flame detectors are deployed in hazardous locations to detect fires caused by fuel leaks or vapor ignition.
- Hydrogen (H₂) gas sensors detect leaks in electrolyzers, preventing the risk of flash fires and explosions.
- Oxygen (O₂) deficiency sensors ensure worker safety in enclosed spaces where hydrogen production occurs.
- Optical flame detectors safeguard concentrated solar power (CSP) plants from fire risks associated with high-temperature operations.
Key Purchasing Considerations
- Infrared gas detectors are ideal for hydrocarbon detection, offering fast response times and low maintenance.
- Electrochemical sensors provide accurate detection of toxic gases like hydrogen sulfide (H₂S) and carbon monoxide (CO).
- Catalytic bead sensors are effective for combustible gas monitoring in landfill gas and biogas applications.
- Ultraviolet (UV) flame detectors are suitable for detecting fires caused by hydrogen and other non-carbon-based fuels.
- Infrared (IR) flame detectors work well in outdoor environments and high-temperature industrial areas.
- Multi-spectrum flame detection systems enhance reliability by minimizing false alarms from welding, sunlight, or hot surfaces.
- Explosion-proof and intrinsically safe gas detectors are essential for hazardous areas such as refineries and hydrogen storage facilities.
- Corrosion-resistant sensors protect against aggressive chemical environments in geothermal and landfill applications.
- Weatherproof enclosures are necessary for outdoor installations in pipelines, landfill gas extraction systems, and offshore platforms.
- Ensure detectors comply with safety regulations such as OSHA, NFPA, IECEx, ATEX, and ANSI standards.
- Calibration and maintenance requirements should align with industry best practices for continuous safety assurance.
- Compliance with EPA and air quality regulations is crucial for facilities handling methane, CO₂, and sulfur-based emissions.
- Smart gas detectors with digital outputs (HART, Modbus, BACnet) enable seamless integration into SCADA and PLC systems.
- Wireless connectivity provides real-time monitoring and remote alert capabilities for large-scale energy facilities.
- Automated emergency shutdown systems should be integrated with gas and flame detection networks for rapid response to hazards.
- Choose self-diagnostic gas detectors with predictive maintenance features to minimize false alarms and ensure reliability.
- Calibration-free or long-life sensors reduce operational costs in remote or hard-to-reach installations.
- Redundant sensor systems provide additional safety layers for critical energy applications.
Industry Standards & Regulatory Compliance
Key Regulatory Frameworks and Standards for Energy Facilities
- Requires facilities to control and monitor emissions of CO₂, NOx, SO₂, particulate matter (PM), carbon monoxide (CO), and volatile organic compounds (VOCs).
- Continuous Emissions Monitoring Systems (CEMS) must be used in fossil fuel power plants and large combustion units to report real-time emissions data.
- Title V operating permits mandate emissions tracking, performance standards for control technologies, and documentation for EPA and state agencies.
- Power plants and combined heat and power (CHP) systems with water discharges must obtain a National Pollutant Discharge Elimination System (NPDES) permit.
- Monitoring of discharge temperature, pH, total suspended solids (TSS), metals, and chemical additives is required.
- Closed-cycle cooling water systems and blowdown monitoring help ensure compliance with thermal pollution and chemical discharge limits.
- Applies to facilities handling flammable or toxic chemicals such as natural gas, ammonia, or hydrogen.
- Requires implementation of automated safety shutdown systems, gas leak detection, pressure relief systems, and emergency response procedures.
- Instrumentation used in safety-critical processes must be rated for hazardous environments and tested regularly for reliability.
- ASME Boiler and Pressure Vessel Code (BPVC): Governs design, operation, and inspection of boilers, heat exchangers, and pressure vessels.
- NFPA 85 & NFPA 70E: Cover burner management systems, combustion safety, and electrical safety programs.
- IEEE 1547 & 519: Apply to distributed energy integration and power quality management in grid-connected systems.
Energy Efficiency, Carbon Reporting & Future Regulations
- Requires large facilities to monitor and report GHG emissions, including CO₂ from combustion and CH₄ from fuel handling.
- Emissions monitoring instruments must be EPA-certified and support electronic data submission.
- Promotes continuous energy performance improvement through process optimization and system-level monitoring.
- Requires integration of real-time flow, power, temperature, and efficiency data into energy dashboards.
- As new energy technologies emerge, regulations around hydrogen safety, battery storage fire risk, and power conversion are expanding.
- Instrumentation used in these systems must be compliant with IECEx, ATEX, and emerging UL safety standards.
Benefits of Working With Clipper Controls
Clipper Controls provides energy facilities with precision instrumentation and control solutions that support safe, efficient, and compliant operations. Our expertise spans flow, pressure, temperature, emissions monitoring, and SCADA integration—helping teams optimize performance while meeting regulatory demands.
We offer field-proven products for power generation, district energy, and cogeneration systems, backed by deep technical knowledge and responsive support. Whether you're modernizing plant infrastructure or improving data accuracy, Clipper Controls delivers tailored solutions that enhance reliability, reduce downtime, and streamline compliance reporting.
Case Studies & Success Stories
Click here to read our energy case studies.
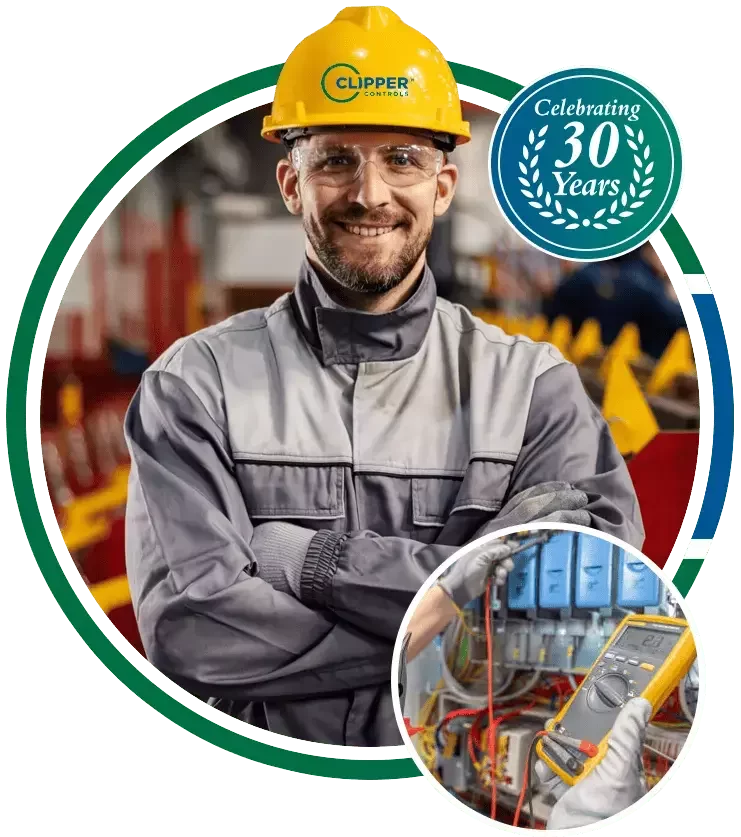
Real Results, Real Impact:
Thanks to Clipper Controls, our wastewater treatment plant improved efficiency & compliance with top-tier flow meters. Reliable solutions, great support! We recommend Clipper Controls to all our partner companies.
~ John Smith, Controls Engineer @ ABC Company
Clipper Controls helped our city upgrade water monitoring systems, ensuring accuracy & compliance. Reliable solutions & excellent customer service!
~ Nancy Patel, Procurement @ ABC Company
~ John Smith, Controls Engineer @ ABC Company
Ready to Work With Us?
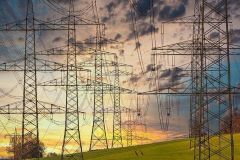
Quick Page Navigation:
🔹How Our Products Support Your Industry
Pressure Monitoring & Regulation
Gas & Flame Detection for Safety Compliance
🔹Industry Standards & Regulatory Compliance
🔹Benefits of Working With Clipper Controls
Case Studies & Success Stories
Real Results, Real Impact:
🔹Featured Products for Energy Applications