Facilities & HVAC Process Control Applications
Application Overview
Efficient instrumentation, controls, and analyzers are essential for Facilities & HVAC process control applications, ensuring optimal energy efficiency, air quality, temperature regulation, and system reliability. Advanced flow meters, pressure sensors, temperature controllers, and gas analyzers provide real-time monitoring and automation for HVAC systems, air handling units (AHUs), chillers, boilers, and building automation systems (BAS). These technologies enable precise environmental control, energy conservation, and compliance with ASHRAE, LEED, and EPA standards while reducing operational costs.
Accurate humidity, air pressure, and airflow control are critical for maintaining comfort, safety, and air quality in commercial buildings, hospitals, data centers, and industrial facilities. Smart HVAC controls and predictive maintenance systems use IoT-enabled sensors and SCADA integration to optimize air circulation, ventilation rates, and energy consumption while ensuring proper filtration and pollutant removal. With increasing emphasis on sustainability and regulatory compliance, modern HVAC systems incorporate carbon dioxide (CO₂) monitoring, refrigerant leak detection, and heat recovery systems, improving indoor air quality (IAQ) and overall system performance.
How Our Products Support Your Industry
Clipper Controls provides advanced instrumentation, automation, and monitoring solutions to optimize Facilities & HVAC process control applications. Our flow meters, pressure sensors, temperature controllers, and gas analyzers ensure precise airflow regulation, energy efficiency, and indoor air quality (IAQ) compliance in commercial buildings, hospitals, data centers, and industrial facilities.
With expertise in building automation systems (BAS) integration, SCADA connectivity, and predictive maintenance solutions, Clipper Controls helps facility managers reduce energy consumption, improve HVAC reliability, and meet ASHRAE, LEED, and EPA compliance standards. Our IoT-enabled sensors and smart monitoring systems provide real-time diagnostics and automated controls, ensuring efficient ventilation, humidity control, and refrigerant leak detection for sustainable and high-performance facility operations.
Key Applications and Solutions
Flow Measurement & Control
Precise flow measurement and control are critical for maintaining energy efficiency, indoor air quality (IAQ), and optimal system performance in HVAC and facility operations. Proper monitoring of airflow, water flow, and steam distribution ensures consistent temperature regulation, humidity control, and energy conservation. Advanced flow meters, automated control valves, and SCADA-integrated monitoring systems help optimize ventilation rates, chilled and hot water circulation, and boiler efficiency, reducing operational costs while ensuring compliance with ASHRAE, LEED, and EPA standards.
Flow Measurement & Control Applications in HVAC & Facility Systems
HVAC and facility systems depend on accurate and responsive flow control solutions to optimize thermal comfort, system efficiency, and resource management. Key applications include:
Airflow Measurement in Ventilation & Duct Systems:
Thermal mass and differential pressure airflow sensors ensure precise air distribution in air handling units (AHUs), ducts, and ventilation systems, optimizing indoor air quality (IAQ).
Ultrasonic airflow meters help regulate supply, return, and exhaust air rates, preventing energy losses and maintaining compliance with ASHRAE 62.1 ventilation standards.
Variable air volume (VAV) system flow sensors adjust airflow dynamically based on occupancy levels and temperature demands, improving efficiency.
Water Flow Monitoring for Chillers & Boiler Systems:
Magnetic and ultrasonic flow meters measure chilled water, hot water, and condenser water circulation, optimizing energy efficiency in chiller plants and hydronic heating systems.
Differential pressure and vortex flow sensors help maintain boiler feedwater and steam flow control, preventing scaling and improving heat transfer efficiency.
Flow-based pump control systems regulate cooling tower water circulation, ensuring optimal heat rejection and minimal water wastage.
Cooling Tower & Heat Exchanger Flow Control:
Electromagnetic and ultrasonic flow meters monitor evaporative cooling water flow, reducing excess consumption and ensuring legionella risk management.
Flow-based chemical dosing systems maintain proper biocide and corrosion inhibitor levels, improving cooling tower efficiency.
Heat exchanger flow monitoring systems optimize water and refrigerant circulation, preventing overheating and energy inefficiencies.
Steam Flow Control for Building Heating & Humidification:
Vortex and differential pressure steam flow meters ensure proper distribution of steam for space heating, humidification, and sterilization in hospitals, commercial buildings, and industrial facilities.
Smart steam trap monitoring systems detect leaks and inefficiencies, reducing energy waste and ensuring optimal steam usage.
Automated steam control valves with flow measurement integration prevent pressure fluctuations in HVAC humidification systems, ensuring comfort and regulatory compliance.
Domestic Water & Process Flow Control in Facilities:
Ultrasonic and positive displacement flow meters monitor potable water distribution in commercial buildings, ensuring compliance with water conservation standards.
Flow-based leak detection systems in facility water networks help prevent pipe bursts and excessive water usage, optimizing sustainability efforts.
Automated irrigation flow control for facility landscaping ensures proper water distribution, reducing consumption while maintaining green spaces.
Key Purchasing Considerations
Choosing the right flow measurement and control solutions for HVAC and facility systems requires evaluating fluid characteristics, system integration needs, and regulatory compliance. The following considerations should guide decision-making:
Accuracy & Sensor Sensitivity:
Ultrasonic and thermal mass flow meters provide high-accuracy measurement for air and water flow control in HVAC systems.
Differential pressure-based flow meters optimize steam and compressed air flow monitoring, ensuring efficiency and reliability.
Environmental Durability & Installation Flexibility:
Non-invasive, clamp-on ultrasonic flow meters reduce installation complexity in chilled water and HVAC pipe networks.
Corrosion-resistant and high-temperature flow sensors are required for boiler, steam, and chemical dosing applications.
Integration with Building Automation & SCADA Systems:
Digital flow sensors with BACnet, Modbus, and HART compatibility enable seamless integration with HVAC control systems and facility automation platforms.
Wireless and IoT-enabled flow meters allow remote monitoring of airflow rates, water consumption, and process efficiency, optimizing predictive maintenance.
Compliance with Industry Standards & Regulations:
Flow meters should meet ASHRAE 90.1 energy efficiency standards, EPA water conservation guidelines, and LEED sustainability benchmarks.
Steam and humidification system flow sensors must comply with ANSI and OSHA indoor air quality (IAQ) regulations for occupant safety.
Maintenance & Lifecycle Costs:
Self-cleaning, drift-resistant flow meters reduce maintenance needs in chiller loops, boiler feedwater, and air handling systems.
Smart diagnostics and real-time alerts improve reliability and enable proactive maintenance, minimizing downtime in critical HVAC operations.
Pressure Monitoring & Regulation
Accurate pressure monitoring and regulation are essential for efficient airflow distribution, system safety, and energy optimization in HVAC and facility management applications. Proper differential pressure control, static pressure regulation, and fluid pressure monitoring ensure optimal air handling unit (AHU) performance, boiler and chiller efficiency, and ventilation system reliability. Advanced pressure sensors, transmitters, and automated control valves help maintain balanced airflow, prevent leaks, and enhance system responsiveness, reducing energy consumption and maintenance costs while ensuring compliance with ASHRAE, LEED, and EPA indoor air quality (IAQ) standards.
Pressure Monitoring & Regulation Applications for HVAC Performance
Maintaining precise air, steam, and water pressure control is crucial for optimizing HVAC efficiency, indoor comfort, and facility safety. Key applications include:
Differential Pressure Control in Air Handling Units (AHUs):
Differential pressure transmitters monitor filter loading and duct static pressure, ensuring efficient air distribution and timely filter replacement alerts.
VAV (Variable Air Volume) system pressure sensors regulate airflow adjustments based on occupancy levels, reducing energy waste and improving climate control.
Smart pressure monitoring in exhaust and supply air fans ensures balanced ventilation rates, preventing air stagnation and negative building pressurization.
Chilled & Hot Water System Pressure Regulation:
Differential pressure sensors and flow-integrated pressure transmitters optimize chilled water and hot water circulation, maintaining boiler and chiller performance.
Hydronic pressure sensors regulate water flow through heat exchangers, fan coil units, and radiators, improving temperature consistency across facility zones.
Automated pressure-regulated valves prevent overpressurization in closed-loop HVAC water systems, extending equipment lifespan.
Static Pressure Monitoring in Ductwork & VAV Systems:
Static pressure sensors track air movement in duct systems, adjusting fan speeds and damper positions for optimal airflow control.
Room pressurization control sensors maintain cleanroom, hospital, and laboratory environments, preventing airborne contamination.
Pressure-based demand-controlled ventilation (DCV) systems optimize fresh air intake, reducing unnecessary HVAC workload.
Boiler & Steam System Pressure Management:
High-temperature pressure transmitters monitor boiler steam pressure, ensuring efficient combustion and heat transfer while preventing overpressure risks.
Condensate return pressure sensors track steam trap performance, reducing energy waste and preventing water hammer effects.
Automated steam control valves with pressure feedback optimize humidification in HVAC systems, improving occupant comfort.
Refrigerant & Cooling System Pressure Control:
Pressure sensors integrated with chillers and cooling towers ensure consistent refrigerant flow and compressor efficiency.
Subcooling and superheating pressure monitoring optimizes HVAC system efficiency, reducing energy consumption.
Automated refrigerant leak detection pressure sensors help maintain EPA compliance and prevent costly refrigerant losses.
Key Purchasing Considerations
Selecting the right pressure monitoring and regulation instrumentation for HVAC and facility applications requires evaluating accuracy, environmental resilience, and system compatibility. The following factors should guide decision-making:
Accuracy & Sensor Sensitivity:
Low-range differential pressure sensors (0.1 Pa accuracy) optimize AHU filter monitoring and duct static pressure control.
Fast-response, high-resolution pressure transmitters ensure accurate readings in high-pressure steam and boiler systems.
Environmental Durability & Sensor Longevity:
Corrosion-resistant, stainless steel pressure sensors withstand high-humidity, high-temperature HVAC environments.
Explosion-proof and intrinsically safe pressure monitors are essential for refrigerant storage and steam plant applications.
Integration with HVAC Automation & SCADA Systems:
Pressure sensors with BACnet, Modbus, or HART communication ensure seamless integration into BAS and SCADA control platforms.
IoT-enabled wireless pressure sensors allow for remote monitoring, predictive maintenance, and real-time alerts.
Compliance with Industry Standards & Regulations:
Ensure compliance with ASHRAE, LEED, and EPA indoor air quality (IAQ) requirements for differential pressure monitoring in cleanrooms and laboratories.
Steam pressure control systems should meet ANSI, OSHA, and NFPA safety guidelines for boiler operations.
Maintenance & Lifecycle Considerations:
Self-calibrating and long-life pressure sensors reduce maintenance frequency in AHUs, chillers, and hydronic HVAC systems.
Multi-redundancy pressure monitoring with fail-safe alarms ensures continued operation in critical facility environments.
Temperature Sensing & Control
Accurate temperature sensing and control are essential for energy efficiency, occupant comfort, and equipment longevity in building management and HVAC systems. Facilities rely on precise temperature monitoring in air handling units (AHUs), boilers, chillers, and ventilation systems to optimize heating, cooling, and humidity control. Advanced RTDs (Resistance Temperature Detectors), thermocouples, infrared sensors, and digital thermostats provide real-time temperature regulation and system automation, ensuring compliance with ASHRAE, LEED, and EPA energy efficiency standards.
Temperature Sensing & Control Applications in Building Management
Effective temperature monitoring and control improve HVAC performance, energy savings, and indoor environmental quality (IEQ) in commercial, industrial, and institutional buildings. Key applications include:
Smart Temperature Regulation for Energy Efficiency:
RTDs and thermocouples ensure precise temperature control in hydronic heating and cooling loops, optimizing chiller and boiler efficiency.
Digital thermostats and temperature sensors regulate HVAC zoning and variable air volume (VAV) systems, reducing unnecessary heating and cooling.
IoT-enabled temperature sensors enable real-time monitoring and predictive maintenance, improving energy savings in smart building automation systems.
Thermal Monitoring in Boilers, Chillers & Heat Exchangers:
High-temperature thermocouples monitor boiler combustion temperatures, optimizing fuel efficiency and reducing emissions.
Immersion temperature sensors track chilled water and condenser loop temperatures, preventing system inefficiencies and energy losses.
Infrared temperature sensors detect heat exchanger fouling and blockages, improving thermal transfer efficiency in HVAC operations.
Air Handling Unit (AHU) & Duct Temperature Control:
Duct-mounted temperature sensors provide real-time data for supply air and return air regulation, ensuring consistent thermal comfort.
Outside air temperature sensors optimize economizer control, adjusting ventilation rates to reduce mechanical cooling loads.
Integrated temperature and humidity sensors maintain proper dew point control, preventing condensation and mold risks in ventilation ducts.
Refrigeration & Cold Storage Temperature Monitoring:
Wireless temperature sensors track refrigeration and freezer unit temperatures, preventing spoilage in food storage and pharmaceutical facilities.
Thermocouple-based temperature probes ensure compliance with HACCP and FDA guidelines for temperature-sensitive inventory storage.
Alarmed temperature monitoring systems provide alerts for temperature fluctuations, preventing costly product losses.
Data Center & Server Room Temperature Regulation:
High-precision RTDs and thermal sensors monitor server rack temperatures, preventing overheating and hardware failure.
Liquid cooling system temperature sensors regulate heat dissipation in high-density computing environments.
AI-driven temperature optimization systems adjust cooling loads dynamically, improving energy efficiency in mission-critical facilities.
Key Purchasing Considerations
Choosing the right temperature sensing and control solutions for building management requires evaluating sensor accuracy, durability, integration capabilities, and regulatory compliance. The following factors should guide decision-making:
Accuracy & Response Time:
Platinum RTDs (Class A, ±0.1°C accuracy) provide high-precision temperature measurement in HVAC applications.
Fast-response thermocouples ensure instantaneous temperature monitoring in boiler, chiller, and heat exchanger systems.
Environmental Durability & Sensor Longevity:
Corrosion-resistant RTDs and thermocouples (stainless steel, Inconel, and PTFE coatings) withstand harsh HVAC conditions.
High-temperature thermocouples (up to 2,200°F/1,200°C) are essential for boiler and industrial furnace monitoring.
Integration with Building Automation & SCADA Systems:
Temperature sensors with BACnet, Modbus, or CAN bus compatibility enable seamless integration with building management systems (BMS) and SCADA platforms.
Wireless IoT-enabled temperature sensors allow for remote monitoring, predictive maintenance, and automated system adjustments.
Compliance with Industry Standards & Regulations:
Ensure compliance with ASHRAE 90.1 energy efficiency standards, EPA indoor air quality (IAQ) regulations, and LEED sustainability guidelines.
Temperature monitoring in pharmaceutical and food storage facilities should meet FDA and HACCP temperature control requirements.
Reliability & Maintenance Considerations:
Self-calibrating and drift-resistant temperature sensors reduce long-term maintenance in HVAC, refrigeration, and hydronic heating applications.
Redundant temperature monitoring with fail-safe alarms ensures consistent system performance in critical facility environments.
Humidity & Air Quality Monitoring
Maintaining optimal humidity and indoor air quality (IAQ) is essential for occupant comfort, health, and energy efficiency in commercial buildings, healthcare facilities, data centers, and industrial environments. Excess humidity can lead to mold growth, material degradation, and bacterial proliferation, while low humidity can cause static electricity buildup and respiratory issues. Additionally, poor IAQ resulting from high carbon dioxide (CO₂), volatile organic compounds (VOCs), and particulate matter (PM) can compromise health, reduce productivity, and increase HVAC energy loads. Advanced humidity sensors, CO₂ monitors, particulate sensors, and VOC analyzers provide real-time data and automated adjustments to ensure regulated humidity levels, fresh air circulation, and compliance with ASHRAE, LEED, and EPA air quality standards.
Humidity & Air Quality Monitoring Applications for Indoor Environments
Effective humidity and air quality monitoring solutions enhance HVAC efficiency, indoor environmental quality, and regulatory compliance across a range of facility applications. Key applications include:
CO₂ & VOC Monitoring for Ventilation Optimization:
NDIR CO₂ sensors continuously monitor carbon dioxide levels in conference rooms, offices, and classrooms, ensuring adequate fresh air intake and ventilation control.
VOC analyzers detect airborne pollutants such as formaldehyde and benzene, optimizing filtration and exhaust ventilation systems.
Demand-controlled ventilation (DCV) systems use real-time CO₂ and VOC sensor feedback to adjust ventilation rates dynamically, reducing energy waste.
Humidity Control for Critical Facilities & Cleanrooms:
Capacitive humidity sensors regulate humidity levels in hospitals, laboratories, and pharmaceutical manufacturing, preventing contamination and ensuring sterility.
Dew point sensors prevent condensation in cold storage, server rooms, and archival facilities, protecting sensitive equipment and documents.
Automated humidification and dehumidification controls maintain regulated humidity levels, ensuring compliance with ASHRAE 55 comfort standards.
Particulate Matter (PM) Monitoring in Air Handling Systems:
Laser-based PM2.5 and PM10 sensors detect dust, allergens, and airborne pollutants in HVAC ductwork and return air systems, ensuring proper filtration efficiency.
Integrated air quality sensors in air handling units (AHUs) provide real-time alerts for clogged filters, high airborne contaminants, and poor ventilation efficiency.
Electrostatic and HEPA filtration monitoring systems use PM sensors to optimize air purification performance in hospitals, office buildings, and schools.
Indoor Air Quality (IAQ) Compliance & Safety Monitoring:
Ammonia (NH₃) and hydrogen sulfide (H₂S) sensors provide early warnings of hazardous gas leaks in industrial and wastewater treatment facilities.
Oxygen (O₂) depletion sensors protect workers in mechanical rooms and confined spaces, ensuring safe air quality levels.
Real-time IAQ monitoring dashboards integrate multiple air quality sensors to ensure compliance with EPA, OSHA, and LEED air quality requirements.
Key Purchasing Considerations
Selecting the right humidity and air quality monitoring solutions for indoor environments requires evaluating sensor accuracy, system compatibility, and regulatory compliance. The following factors should guide decision-making:
Accuracy & Sensor Sensitivity:
Capacitive and resistive humidity sensors ensure precise humidity control in HVAC and building management systems.
Laser-based particulate sensors (PM2.5/PM10) provide high-resolution air quality measurements in critical applications.
NDIR CO₂ sensors with ±50 ppm accuracy ensure accurate ventilation rate calculations in high-occupancy buildings.
Durability & Environmental Stability:
Ruggedized humidity and gas sensors with temperature compensation ensure stability in HVAC ductwork, air handling units, and mechanical rooms.
Explosion-proof and intrinsically safe air quality sensors are required for hazardous areas such as chemical storage rooms and laboratories.
Integration with Building Automation & SCADA Systems:
Air quality sensors with BACnet, Modbus, or HART communication enable seamless integration into building management systems (BMS) and SCADA platforms.
Wireless and IoT-enabled IAQ monitors allow real-time tracking, predictive analytics, and automated HVAC adjustments.
Compliance with Indoor Air Quality & Environmental Regulations:
Ensure compliance with ASHRAE 62.1 ventilation standards, LEED IAQ monitoring requirements, and EPA Clean Air Act regulations.
Humidity control systems in cleanrooms and hospitals must meet ISO 14644 and FDA Good Manufacturing Practices (GMP) guidelines.
Reliability & Maintenance Considerations:
Self-calibrating and long-life humidity and gas sensors reduce maintenance costs in commercial HVAC and air purification systems.
Automated IAQ monitoring with real-time alerts improves facility management and enhances occupant safety.
Gas Detection & Environmental Monitoring
Accurate gas detection and environmental monitoring are critical in commercial buildings, industrial plants, laboratories, and healthcare facilities to ensure air quality, safety, and regulatory compliance. Harmful gases such as carbon monoxide (CO), carbon dioxide (CO₂), volatile organic compounds (VOCs), refrigerants, and hazardous industrial gases can pose health risks, fire hazards, and environmental concerns. Advanced gas sensors, air quality analyzers, and SCADA-integrated monitoring systems provide real-time data, early leak detection, and automated ventilation controls, ensuring compliance with ASHRAE, OSHA, EPA, and LEED indoor air quality (IAQ) standards while improving energy efficiency and occupant safety.
Gas Detection & Environmental Monitoring Applications in Facilities
Effective gas detection and air quality monitoring solutions help facility managers mitigate safety risks, optimize HVAC performance, and ensure compliance with indoor air quality regulations. Key applications include:
Refrigerant Leak Detection & Compliance Monitoring:
Infrared (IR) refrigerant gas sensors detect leaks in HVAC chillers, refrigeration units, and cold storage rooms, preventing energy losses and environmental damage.
Continuous refrigerant monitoring systems ensure compliance with EPA Section 608 Clean Air Act regulations, helping reduce ozone depletion and greenhouse gas emissions.
SCADA-integrated refrigerant leak detection alarms provide real-time alerts and automated ventilation control in data centers, commercial buildings, and industrial cooling systems.
Indoor Air Quality (IAQ) Sensors for Occupant Safety:
Carbon dioxide (CO₂) sensors monitor air quality in offices, schools, and conference rooms, optimizing ventilation rates to prevent drowsiness and respiratory discomfort.
VOC and formaldehyde (HCHO) analyzers detect chemical off-gassing from furniture, carpets, and cleaning products, ensuring a healthy indoor environment.
Smart air quality monitoring systems integrate temperature, humidity, CO₂, and VOC sensors, providing real-time IAQ dashboards and alerts for facility managers.
Toxic & Combustible Gas Monitoring in Mechanical & Industrial Spaces:
Carbon monoxide (CO) and nitrogen dioxide (NO₂) sensors track airborne pollutants from fuel-burning appliances, parking garages, and boiler rooms, preventing exposure to hazardous fumes.
Hydrogen sulfide (H₂S) and ammonia (NH₃) sensors detect toxic gas leaks in wastewater treatment facilities, chemical plants, and laboratories, improving workplace safety.
Combustible gas detectors for methane (CH₄) and propane (C₃H₈) provide early leak detection in kitchens, gas furnaces, and fuel storage areas, preventing fire and explosion risks.
Oxygen Depletion & Confined Space Monitoring:
Oxygen (O₂) sensors monitor enclosed spaces such as storage tanks, underground utility rooms, and maintenance tunnels, preventing asphyxiation hazards.
Fixed and portable gas monitors provide real-time alerts for hazardous gas buildup, ensuring worker safety in confined spaces.
SCADA-integrated gas detection systems automate emergency ventilation and alarm triggers, enhancing safety protocols in industrial and commercial facilities.
Emission & Environmental Air Quality Compliance:
Continuous Emission Monitoring Systems (CEMS) track NOx, SOx, and particulate matter (PM) emissions in industrial exhaust systems, ensuring compliance with EPA Clean Air Act regulations.
Airborne particulate (PM2.5/PM10) sensors monitor indoor and outdoor pollution levels, optimizing air filtration and HVAC operation.
Air quality monitoring stations in smart cities and industrial zones provide real-time data for environmental impact assessments and regulatory reporting.
Key Purchasing Considerations
Choosing the right gas detection and environmental monitoring solutions requires evaluating sensor accuracy, durability, integration capabilities, and compliance standards. The following considerations should guide decision-making:
Accuracy & Sensor Sensitivity:
Electrochemical and NDIR gas sensors provide high-precision detection for CO, CO₂, VOCs, and refrigerants.
Photoionization detectors (PIDs) offer real-time VOC measurement, improving indoor air quality compliance.
Durability & Environmental Stability:
Corrosion-resistant gas sensors (stainless steel, PTFE, and explosion-proof enclosures) ensure long-term reliability in mechanical and industrial spaces.
Temperature and humidity-compensated sensors maintain accuracy in variable environmental conditions.
Integration with Building Automation & SCADA Systems:
Gas sensors with BACnet, Modbus, or HART connectivity allow seamless integration into building management and automation systems (BMS).
IoT-enabled gas monitors provide remote tracking, automated ventilation control, and real-time alerts.
Compliance with Industry Safety & Environmental Standards:
Ensure compliance with ASHRAE 62.1, LEED IAQ requirements, EPA Clean Air Act, and OSHA workplace air quality standards.
Industrial gas monitoring solutions should meet NFPA hazardous area classifications and ATEX explosion-proof requirements.
Reliability & Maintenance Considerations:
Self-calibrating and long-life gas sensors reduce maintenance in HVAC, industrial, and commercial air monitoring applications.
Automated gas detection networks with fail-safe alarms ensure rapid response to air quality hazards and gas leaks.
Vibration & Structural Health Monitoring
Continuous vibration and structural health monitoring are essential in HVAC systems and building infrastructure to prevent equipment failures, optimize energy efficiency, and reduce maintenance costs. Compressors, pumps, fans, and cooling towers operate under constant mechanical stress, leading to imbalances, misalignments, and premature wear if not properly monitored. Advanced vibration sensors, accelerometers, and structural health monitoring (SHM) systems enable real-time diagnostics, predictive maintenance, and failure prevention. Integrating SCADA and IoT-enabled monitoring solutions allows facility managers to track system performance, reduce downtime, and enhance operational reliability while ensuring compliance with ASHRAE, LEED, and OSHA standards.
Vibration & Structural Health Monitoring Applications in HVAC Equipment
Proper vibration and structural monitoring enhance equipment longevity, energy savings, and operational efficiency across a range of HVAC and facility applications. Key applications include:
Predictive Maintenance for Compressors, Pumps & Fans:
Tri-axial accelerometers and MEMS vibration sensors detect bearing wear, rotor imbalance, and cavitation in chillers, compressors, and hydronic pumps.
Piezoelectric vibration sensors monitor excessive motor vibration, preventing misalignment and unbalanced operation in air handling units (AHUs) and exhaust fans.
Automated SCADA-based diagnostics provide real-time alerts for developing mechanical faults, enabling scheduled maintenance rather than reactive repairs.
Vibration Analysis for Chillers & Cooling Towers:
Wireless vibration monitoring systems track oscillation patterns in cooling tower fans and chiller compressors, ensuring proper load distribution.
Shock and impact sensors detect excessive mechanical stress, helping to prevent fan blade failures and motor damage in large-scale HVAC systems.
Automated condition monitoring optimizes cooling efficiency by detecting early-stage vibration issues, reducing energy consumption and repair costs.
Structural Health Monitoring for Rooftop HVAC Systems:
Structural vibration sensors detect foundation shifting and excessive load stress on rooftop HVAC installations, preventing long-term damage.
Fiber-optic strain sensors monitor the integrity of building support structures, ensuring HVAC units are securely mounted and properly balanced.
Continuous load tracking and thermal expansion monitoring improve HVAC unit stability in high-rise buildings and large commercial facilities.
Dynamic Balancing & Noise Reduction in HVAC Equipment:
Vibration-based noise level sensors track excessive oscillations in air handling units, duct silencers, and ventilation fans, improving indoor acoustic comfort.
Smart motor balancing sensors adjust fan speed and airflow dynamically, reducing energy waste and mechanical strain.
Real-time vibration damping systems enhance HVAC efficiency while maintaining quiet operation in hospitals, office spaces, and residential buildings.
Key Purchasing Considerations
Selecting the right vibration and structural health monitoring solutions for HVAC equipment requires evaluating sensor precision, durability, system integration, and compliance standards. The following factors should guide decision-making:
Accuracy & Sensor Sensitivity:
Tri-axial accelerometers and high-frequency MEMS sensors provide detailed vibration diagnostics for compressors, pumps, and motorized HVAC components.
Low-noise piezoelectric vibration sensors improve detection of early-stage mechanical faults, enabling preventative maintenance strategies.
Environmental Durability & Sensor Longevity:
Corrosion-resistant vibration sensors (stainless steel, PTFE-coated, or sealed enclosures) ensure long-term performance in high-humidity and outdoor HVAC installations.
Explosion-proof and intrinsically safe sensors must be used for gas-powered HVAC systems and hazardous facility zones.
Integration with Building Automation & SCADA Systems:
Vibration monitoring sensors with BACnet, Modbus, or HART connectivity enable seamless integration into building management systems (BMS) and SCADA platforms.
Wireless IoT-enabled vibration monitors provide remote performance tracking, predictive maintenance scheduling, and real-time alerts.
Compliance with HVAC Equipment Safety & Performance Standards:
Ensure compliance with ASHRAE, OSHA, and LEED sustainability requirements for vibration monitoring in HVAC and building automation systems.
Noise and vibration control systems should meet ISO 10816 and ANSI S2.41 guidelines for HVAC equipment vibration thresholds.
Maintenance & Lifecycle Considerations:
Self-calibrating and drift-resistant vibration sensors reduce maintenance costs and improve long-term equipment reliability.
Fail-safe vibration monitoring systems with automatic shutdown controls enhance HVAC system protection and operational safety.
Analytical Instrumentation for Energy Efficiency & Compliance
Achieving energy efficiency and regulatory compliance in HVAC and building management systems requires precise measurement, analysis, and automation. Analytical instrumentation, including energy meters, power quality analyzers, combustion efficiency monitors, and environmental sensors, plays a crucial role in optimizing heating, cooling, and ventilation systems. These instruments provide real-time data on energy consumption, emissions, air quality, and thermal efficiency, enabling predictive maintenance, cost reduction, and sustainability. Advanced SCADA-integrated and IoT-enabled monitoring systems support ASHRAE, LEED, and EPA regulatory requirements, ensuring that buildings meet modern energy efficiency and sustainability goals.
Analytical Instrumentation Applications for Energy Efficiency & Compliance
High-precision analytical instrumentation enhances energy conservation, HVAC system efficiency, and compliance with green building initiatives. Key applications include:
Energy Consumption Monitoring for LEED & ASHRAE Standards:
Digital energy meters and sub-metering systems track power usage in HVAC equipment, lighting, and facility automation systems, ensuring compliance with ASHRAE 90.1 energy efficiency standards.
Power quality analyzers monitor voltage, frequency, and power factor imbalances, preventing inefficiencies in HVAC and electrical distribution systems.
Smart demand-side energy monitoring systems help optimize peak load management, reducing energy costs and carbon footprint.
Smart Building Automation & SCADA Integration:
Cloud-based analytics platforms aggregate data from HVAC sensors, flow meters, and power analyzers, improving system-wide energy optimization.
IoT-enabled predictive maintenance systems use real-time temperature, pressure, and airflow data to detect inefficiencies before system failure occurs.
Automated fault detection and diagnostics (FDD) software integrates with SCADA and BMS platforms, providing AI-driven performance optimization.
Combustion & Boiler Efficiency Monitoring:
Flue gas analyzers measure oxygen (O₂), carbon monoxide (CO), and nitrogen oxides (NOx) levels, optimizing boiler combustion efficiency and reducing emissions.
Infrared and thermal imaging sensors detect heat losses in steam pipes, heat exchangers, and ventilation systems, minimizing waste.
Steam system performance analyzers monitor condensate return efficiency and steam trap operation, improving overall heating system performance.
Air Quality & Emissions Compliance Monitoring:
Continuous Emission Monitoring Systems (CEMS) track CO₂, NOx, and SOx emissions from fuel-burning HVAC systems, ensuring compliance with EPA Clean Air Act regulations.
Particulate matter (PM2.5/PM10) sensors detect airborne pollutants, enabling real-time air filtration adjustments for better indoor air quality.
Humidity, CO₂, and VOC sensors optimize fresh air intake and demand-controlled ventilation (DCV) strategies, ensuring compliance with ASHRAE 62.1 ventilation guidelines.
Cooling System & Refrigerant Efficiency Analysis:
Refrigerant leak detectors and analyzers track chiller and HVAC refrigerant efficiency, preventing GHG emissions and excessive energy consumption.
Thermal energy meters (BTU meters) measure cooling and heating loads in hydronic HVAC systems, optimizing performance and energy use.
Ultrasonic flow meters ensure precise measurement of water circulation rates in cooling towers, reducing water waste and improving efficiency.
Key Purchasing Considerations
Selecting the right analytical instrumentation for energy efficiency and compliance requires evaluating measurement accuracy, environmental durability, system integration, and regulatory compliance. The following factors should guide decision-making:
Measurement Precision & Real-Time Data Capabilities:
High-resolution energy meters and BTU analyzers ensure accurate HVAC power consumption tracking.
Gas analyzers with ppm/ppb sensitivity provide detailed combustion efficiency and emissions reporting.
Cloud-connected monitoring systems allow for real-time energy usage visualization and AI-driven efficiency analysis.
Environmental Durability & Sensor Longevity:
Corrosion-resistant and high-temperature sensors withstand harsh environments in boilers, steam systems, and HVAC cooling circuits.
Waterproof and dust-resistant analyzers improve long-term performance in outdoor air quality and refrigerant monitoring applications.
Integration with Building Automation & SCADA Systems:
Analytical instruments with BACnet, Modbus, or HART connectivity ensure seamless integration into smart building automation and energy management platforms.
Wireless IoT-enabled sensors allow for remote monitoring, predictive analytics, and real-time compliance reporting.
Compliance with Energy Efficiency & Environmental Regulations:
Ensure compliance with ASHRAE 90.1, LEED certification requirements, and EPA air quality standards for energy efficiency and emissions control.
Refrigerant and combustion efficiency monitoring must meet EPA Section 608 and ISO 14001 environmental management standards.
Reliability & Maintenance Considerations:
Self-calibrating and drift-resistant gas analyzers reduce maintenance costs in combustion efficiency and emissions monitoring applications.
Automated data logging with AI-powered diagnostics improves facility performance and streamlines compliance reporting.
Industry Standards & Regulatory Compliance
Facilities and HVAC systems must meet a broad range of regulatory requirements and industry standards to ensure occupant comfort, indoor air quality, energy efficiency, and equipment safety. These standards are enforced and guided by agencies and organizations such as the Environmental Protection Agency (EPA), Occupational Safety and Health Administration (OSHA), ASHRAE (American Society of Heating, Refrigerating and Air-Conditioning Engineers), and the International Code Council (ICC). Facilities that support critical infrastructure—such as hospitals, laboratories, data centers, and high-occupancy commercial buildings—face even more stringent requirements, especially for air handling, humidity control, emissions, and energy consumption.
Key regulations such as ASHRAE 62.1 (Ventilation for Acceptable Indoor Air Quality) and ASHRAE 90.1 (Energy Standard for Buildings Except Low-Rise Residential) define the minimum performance criteria for HVAC system design and operation. Compliance with EPA Clean Air Act regulations may be required for facilities with boilers, chillers, and combustion-based systems, especially when monitoring for NOx, CO, or refrigerant emissions. For energy reporting and certification programs like LEED, ENERGY STAR, and ISO 50001, facilities must demonstrate precise control and monitoring of energy and environmental performance.
Instrumentation & Monitoring Requirements for Compliance
To meet regulatory obligations and performance benchmarks, facility managers and HVAC professionals rely on accurate, real-time instrumentation across critical areas of building systems:
Air Quality & Ventilation Compliance (ASHRAE 62.1 / OSHA / EPA):
CO₂ sensors, volatile organic compound (VOC) detectors, and particulate monitors ensure adequate fresh air supply and contaminant control.
Differential pressure sensors are used to verify pressurization in cleanrooms, healthcare spaces, and controlled environments.
Energy Efficiency & Reporting Standards (ASHRAE 90.1 / LEED / ISO 50001):
BTU meters, power meters, and flow sensors support energy tracking and optimization in heating and cooling loops.
Building automation systems (BAS) integrated with real-time instrumentation provide actionable data for meeting energy performance targets.
Boiler & Combustion Equipment Regulations (EPA / NFPA 85 / Local Air Districts):
Facilities with on-site boilers must monitor stack temperature, oxygen, NOx, and CO emissions to comply with regional air quality management rules.
Flame detectors, gas pressure sensors, and safety shutoff systems are required for combustion safety compliance.
Refrigerant Management & Leak Detection (EPA Section 608 / F-Gas Regulations):
Refrigerant gas leak detectors ensure early detection of HFC and CFC leaks to minimize environmental impact and meet EPA and international F-Gas rules.
Facilities must maintain detailed records of refrigerant use and recovery per EPA guidelines.
Water Quality and Legionella Prevention (ASHRAE 188 / CDC Guidelines):
Temperature sensors, flow monitors, and biocide dosing controls support monitoring and control of conditions that contribute to Legionella growth in cooling towers and domestic hot water systems.
Benefits of Working With Clipper Controls
Clipper Controls provides high-precision instrumentation and automation solutions to help facility managers optimize HVAC performance, energy efficiency, and indoor air quality. Our flow meters, pressure sensors, gas analyzers, and vibration monitors support real-time monitoring, predictive maintenance, and regulatory compliance, reducing operational costs and downtime.
With expertise in ASHRAE, LEED, and EPA compliance, Clipper Controls offers SCADA-integrated solutions for energy optimization, air quality monitoring, and emissions control. Our durable, high-accuracy sensors and analyzers ensure reliable performance in HVAC, building automation, and industrial facility applications, helping clients achieve sustainability goals, improve occupant comfort, and enhance overall system reliability.
Case Studies & Success Stories
Explore how Clipper Controls has helped facilities and HVAC operators enhance energy efficiency, improve air quality, and ensure compliance with industry standards.
Click here to read our HVAC case studies.
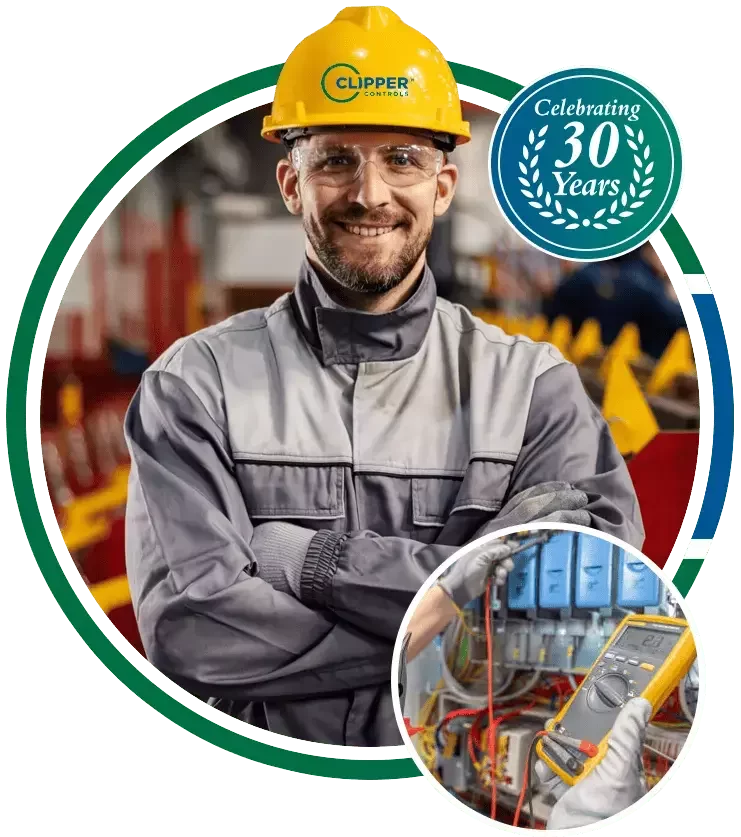
Real Results, Real Impact:
Thanks to Clipper Controls, our wastewater treatment plant improved efficiency & compliance with top-tier flow meters. Reliable solutions, great support! We recommend Clipper Controls to all our partner companies.
~ John Smith, Controls Engineer @ ABC Company
Clipper Controls helped our city upgrade water monitoring systems, ensuring accuracy & compliance. Reliable solutions & excellent customer service!
~ Nancy Patel, Procurement @ ABC Company
~ John Smith, Controls Engineer @ ABC Company
Ready to Work With Us?
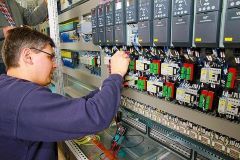
Quick Page Navigation:
🔹How Our Products Support Your Industry
Pressure Monitoring & Regulation
Humidity & Air Quality Monitoring
Gas Detection & Environmental Monitoring
Vibration & Structural Health Monitoring
Instrumentation for Energy Efficiency & Compliance
🔹Industry Standards & Regulatory Compliance
🔹Benefits of Working With Clipper Controls