Marine & Shipping Process Control Applications
Application Overview
Marine and shipping operations rely on advanced instrumentation, control systems, and analyzers to ensure safety, efficiency, and environmental compliance in demanding maritime conditions. From fuel flow monitoring and ballast water management to engine performance diagnostics and emissions control, precise measurement and automation are critical for optimizing vessel operations. Flow meters, pressure sensors, level detectors, and gas analyzers enable real-time monitoring of key shipboard systems, ensuring compliance with IMO, MARPOL, and EPA regulations while enhancing fuel efficiency, equipment reliability, and crew safety.
In addition to propulsion and fuel management, temperature sensing, vibration monitoring, and structural health diagnostics play a crucial role in maintaining engine performance, cargo integrity, and onboard environmental conditions. SCADA-integrated automation systems allow for remote monitoring of engine cooling systems, HVAC, and fire suppression systems, reducing the risk of failures and ensuring proactive maintenance. With increasing focus on decarbonization and sustainable shipping, emission monitoring, ballast water treatment, and waste management technologies help vessels meet global environmental standards while improving overall fleet performance.
How Our Products Support Your Industry
Clipper Controls provides high-precision instrumentation, automation, and monitoring solutions for the marine and shipping industry, ensuring efficient vessel operations, regulatory compliance, and environmental sustainability. Our flow meters, pressure sensors, level detectors, and gas analyzers enable real-time monitoring of fuel consumption, ballast water systems, emissions, and engine performance, helping ship operators optimize fuel efficiency, reduce emissions, and enhance operational safety.
With expertise in IMO, MARPOL, and EPA compliance, Clipper Controls offers SCADA-integrated solutions for automated data collection, remote diagnostics, and predictive maintenance. Our rugged, marine-grade sensors and analyzers are designed to withstand harsh saltwater environments, extreme temperatures, and continuous operation, ensuring reliable performance in commercial shipping, naval defense, and offshore applications. By integrating advanced process control technology, we help maritime operators improve safety, efficiency, and sustainability across their fleets.
Key Applications and Solutions
Flow Measurement & Control
Efficient flow measurement and control are crucial for maintaining fuel efficiency, regulatory compliance, and operational safety in marine and shipping applications. Ships rely on precise fuel monitoring, ballast water control, wastewater discharge, and cooling system regulation to meet IMO, MARPOL, and EPA standards while optimizing performance and reducing costs. Advanced flow meters, automated control valves, and real-time monitoring systems provide ship operators with the ability to track fuel consumption, regulate fluid transfers, and improve emissions compliance. SCADA-integrated automation solutions ensure efficient flow control across critical onboard systems, helping ships maintain optimal performance, prevent system failures, and improve sustainability.
Flow Measurement & Control Applications in Marine & Shipping Operations
Effective flow measurement technology is essential in various shipboard systems to optimize efficiency, ensure compliance, and enhance operational safety. Key applications include:
Fuel Flow Monitoring for Engine Performance & Emissions Compliance:
Coriolis and ultrasonic flow meters track fuel consumption in propulsion engines and auxiliary generators, providing real-time efficiency data.
Mass flow meters and thermal flow sensors ensure accurate measurement of heavy fuel oil (HFO), marine diesel oil (MDO), and liquefied natural gas (LNG), preventing overconsumption and fuel discrepancies.
SCADA-integrated fuel monitoring systems assist in compliance with IMO’s Energy Efficiency Existing Ship Index (EEXI) and Carbon Intensity Indicator (CII) regulations by optimizing fuel use and emissions reporting.
Ballast Water Flow Measurement & Treatment:
Electromagnetic and ultrasonic flow meters control ballast water intake, discharge, and exchange, ensuring compliance with IMO Ballast Water Management Convention (BWMC).
Turbine flow meters and automated control valves manage UV disinfection and filtration processes, preventing the spread of invasive aquatic species.
Flow-based data logging systems maintain detailed records of ballast water treatment and discharge, aiding in regulatory audits.
Cooling & Lubrication System Flow Control:
Positive displacement and vortex flow meters regulate lubrication oil circulation in main engines, turbines, and gearbox systems, preventing overheating and mechanical failures.
Thermal mass flow sensors monitor cooling water flow rates in heat exchangers, jacket water cooling, and engine intercoolers, ensuring effective temperature regulation.
Automated flow control in hydraulic cooling systems optimizes performance in steering and propulsion control units, preventing excessive pressure fluctuations.
Bilge & Wastewater Discharge Monitoring:
Flow meters integrated with oil-in-water analyzers ensure compliance with MARPOL Annex I regulations by preventing unauthorized discharges of oily water.
Turbine and magnetic flow meters measure bilge water movement through separators, filtration units, and discharge systems to prevent environmental contamination.
Automated chemical dosing systems use flow-based regulation to maintain correct pH balance and disinfection levels in onboard wastewater treatment plants.
Cargo Transfer & Bunkering Operations:
Coriolis mass flow meters provide high-accuracy fuel bunkering measurements, preventing disputes over fuel quantities and ensuring proper recordkeeping.
Ultrasonic and differential pressure flow meters regulate the transfer of liquid cargoes such as crude oil, chemicals, and LNG, ensuring compliance with terminal safety and loading guidelines.
SCADA-controlled flow monitoring systems enable ship operators to detect anomalies in bunkering flow rates, reducing the risk of fuel theft and operational inefficiencies.
Key Purchasing Considerations
Choosing the right flow measurement and control instrumentation for marine and shipping applications requires evaluating fluid characteristics, system conditions, and environmental challenges. The following factors should guide decision-making:
Accuracy & Measurement Reliability:
Coriolis and ultrasonic flow meters ensure high-precision fuel consumption tracking, improving efficiency and emissions reporting.
Low-drift, temperature-compensated flow meters provide stable readings for ballast water treatment and cooling system control.
Environmental Durability & Marine-Grade Construction:
Corrosion-resistant materials such as stainless steel, titanium, and PTFE coatings are required for saltwater exposure and aggressive chemical handling.
Explosion-proof and intrinsically safe flow meters are critical for LNG bunkering, chemical cargo transfer, and hazardous fuel storage applications.
Integration with Ship Automation & SCADA Systems:
Flow sensors with HART, Modbus, or CAN bus communication ensure seamless integration with engine monitoring, ballast control, and fuel management platforms.
Wireless and IoT-enabled flow meters allow for remote data logging, real-time diagnostics, and predictive maintenance alerts.
Compliance with Maritime Regulations:
Ensure flow meters meet IMO, MARPOL, USCG, and EPA environmental discharge standards for fuel efficiency, ballast water treatment, and wastewater management.
Bunkering and liquid cargo transfer flow meters should comply with ISO 22192 and MID (Measuring Instruments Directive) regulations for accurate commercial fuel transactions.
Lifecycle Costs & Maintenance Requirements:
Non-intrusive ultrasonic flow meters reduce maintenance needs in high-salinity and particulate-laden water environments.
Self-diagnosing flow sensors with automated calibration improve reliability in high-pressure fuel and lubrication systems.
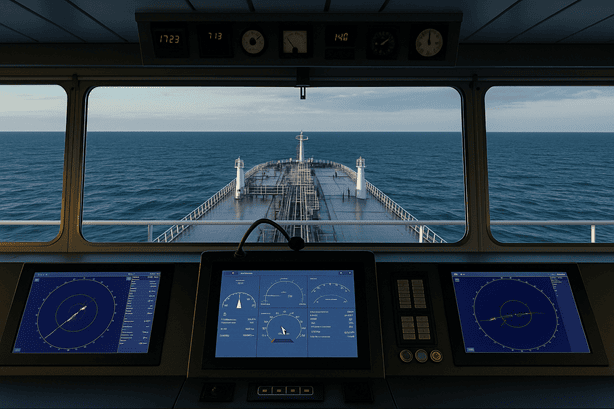
Pressure Monitoring & Regulation
Pressure Monitoring & Regulation Applications for Shipboard Systems
Shipboard operations involve multiple pressurized systems that require continuous monitoring to maintain operational efficiency and safety compliance. Key applications include:
Hydraulic & Pneumatic Pressure Control in Marine Engines:
High-precision pressure transmitters regulate hydraulic systems in steering gear, stabilizers, and propulsion control units, ensuring optimal performance.
Differential pressure sensors monitor compressed air and pneumatic control systems in engine starting mechanisms, ballast tank air vents, and valve actuators.
Pressure relief valves and regulators protect hydraulic circuits in cargo handling cranes, winches, and mooring systems, preventing system overload.
Boiler & Steam System Pressure Monitoring for Vessel Safety:
Steam pressure sensors and safety valves regulate boiler operation in auxiliary and propulsion steam systems, ensuring compliance with IMO and SOLAS safety guidelines.
Differential pressure sensors in heat recovery systems optimize fuel-to-steam conversion in waste heat boilers, improving energy efficiency.
Automated pressure control in superheated steam systems ensures precise temperature and pressure regulation, reducing boiler stress and prolonging system life.
Fuel Transfer & Bunkering Pressure Control:
Inline pressure transmitters and flow-based pressure regulators optimize fuel transfer between storage tanks, bunkering stations, and propulsion engines, ensuring smooth delivery.
Pressure relief valves and safety shut-off systems prevent over-pressurization in LNG, marine diesel oil (MDO), and heavy fuel oil (HFO) storage tanks.
Automated pressure control in fuel filtration systems ensures clean, debris-free fuel for engine combustion, preventing injector clogging and component wear.
Cooling Water & Lubrication System Pressure Regulation:
Differential pressure sensors and automatic control valves regulate cooling water flow in heat exchangers, engine cooling jackets, and condenser systems, preventing overheating.
Lubrication oil pressure sensors ensure proper lubrication in marine diesel engines, gearboxes, and auxiliary generators, reducing mechanical wear.
SCADA-integrated pressure monitoring enables real-time diagnostics and predictive maintenance of onboard cooling and lubrication systems.
Ballast Water & Bilge System Pressure Management:
Hydrostatic pressure sensors monitor ballast water tank levels, ensuring proper distribution and stability for vessel operation.
Bilge pump pressure sensors prevent system failure by detecting anomalies in bilge water discharge and oily water separation, ensuring compliance with MARPOL Annex I.
Automated pressure-regulated ballast water treatment systems optimize filtration, UV disinfection, and chemical dosing processes, improving efficiency while meeting IMO Ballast Water Management Convention (BWMC) standards.
Key Purchasing Considerations
Selecting the right pressure monitoring and regulation solutions for marine and shipping applications requires evaluating system demands, environmental conditions, and integration capabilities. The following factors should guide decision-making:
Accuracy & Stability:
High-precision pressure transmitters (±0.1% accuracy) ensure stable pressure readings in hydraulic, steam, and fuel delivery systems.
Fast-response differential pressure sensors improve real-time monitoring of cooling circuits, lubrication pumps, and ballast systems.
Environmental Durability & Corrosion Resistance:
Stainless steel, titanium, and ceramic-coated pressure sensors withstand saltwater exposure and corrosive fluids in fuel and ballast tanks.
Explosion-proof and intrinsically safe pressure devices are essential for LNG bunkering, volatile fuel handling, and confined shipboard environments.
Integration with Marine Automation & SCADA Systems:
Digital pressure sensors with Modbus, HART, or CAN bus connectivity enable seamless integration with engine control, ballast management, and ship automation platforms.
Wireless and IoT-enabled pressure monitoring systems provide remote diagnostics, predictive maintenance insights, and regulatory reporting.
Compliance with Maritime Regulations:
Ensure sensors meet IMO, SOLAS, MARPOL, and USCG (United States Coast Guard) safety standards for steam boilers, fuel handling, and bilge systems.
Pressure control systems for fuel delivery and bunkering should comply with ISO 8217 fuel standards and bunkering measurement regulations.
Maintenance & Lifecycle Considerations:
Self-diagnosing and drift-resistant pressure sensors reduce maintenance costs in long-term marine deployments.
Fail-safe pressure monitoring with automatic shutoff valves prevents over-pressurization, ensuring safe operations in engine rooms and fuel distribution systems.
Temperature Sensing & Control
Effective temperature sensing and control is crucial in marine and shipping operations to maintain engine efficiency, equipment longevity, fuel optimization, and onboard safety. Shipboard systems—including main propulsion engines, auxiliary generators, HVAC, cargo refrigeration, and cooling circuits—must be carefully monitored to prevent overheating, mechanical wear, and fuel inefficiencies. RTDs (Resistance Temperature Detectors), thermocouples, infrared sensors, and thermal controllers provide real-time monitoring, predictive maintenance, and automated safety measures for critical systems, ensuring compliance with IMO, SOLAS, and MARPOL regulations.
Temperature Sensing & Control Applications in Marine Applications
Maintaining precise temperature control across various marine and offshore systems ensures optimal performance, safety, and energy efficiency. Key applications include:
Engine Cooling & Exhaust Temperature Monitoring:
RTDs and thermocouples monitor coolant temperature in main propulsion engines and auxiliary generators, preventing overheating and ensuring fuel efficiency.
Exhaust gas temperature sensors track post-combustion heat levels, optimizing engine performance and reducing NOx emissions in compliance with IMO Tier III emission regulations.
Thermal control sensors in intercoolers and heat exchangers ensure efficient cooling of turbochargers and engine air intake systems, improving overall efficiency.
Fuel Heating & Viscosity Control:
Inline temperature probes regulate fuel preheating for heavy fuel oil (HFO) and marine diesel oil (MDO), ensuring proper viscosity for combustion.
Self-regulating heating elements with thermal sensors prevent fuel solidification in cold-weather shipping routes, reducing clogging risks in fuel injectors.
Smart temperature controllers automate fuel heating adjustments based on ambient conditions, optimizing combustion efficiency.
Cargo Hold, Refrigeration, & HVAC System Temperature Control:
Wireless temperature sensors monitor and adjust airflow, humidity, and temperature in refrigerated cargo holds, ensuring perishable goods remain within required temperature ranges.
Duct-mounted and ambient temperature sensors regulate HVAC systems in passenger ships, cruise liners, and crew quarters, maintaining comfort and energy efficiency.
Temperature alarms and fail-safe monitoring systems prevent cargo spoilage and alert operators to refrigeration failures in reefer container transport.
Lube Oil & Hydraulic Fluid Temperature Regulation:
Immersion temperature sensors measure lubrication oil temperatures in propulsion shafts, gearboxes, and auxiliary systems, ensuring optimal viscosity and reducing wear.
Hydraulic system temperature monitors regulate fluid temperature in steering gear, winches, and ballast control systems, preventing overheating and maintaining mechanical stability.
Inline thermal sensors in cooling loops prevent thermal expansion issues in high-pressure hydraulic circuits, improving system longevity.
Boiler & Steam System Temperature Monitoring:
High-temperature thermocouples ensure boiler steam temperatures remain within safe operating limits, preventing overpressure and thermal inefficiencies.
Temperature sensors in heat recovery steam generators (HRSGs) optimize energy reuse from exhaust gases, improving fuel economy.
Infrared thermal sensors detect heat loss in boiler insulation and steam lines, preventing energy waste.
Key Purchasing Considerations
Selecting temperature sensing and control instrumentation for marine applications requires evaluating system conditions, environmental durability, and integration capabilities. The following factors should guide decision-making:
Accuracy & Sensor Sensitivity:
Platinum RTDs (Class A, ±0.1°C accuracy) ensure high-precision temperature readings in engine coolant, fuel heating, and lubrication monitoring.
Fast-response thermocouples provide instantaneous heat measurement in exhaust gas and steam boiler applications.
Environmental Durability & Marine Conditions:
Corrosion-resistant sensors (stainless steel, Inconel, and titanium) are required for high-salinity and extreme humidity environments.
Shock-resistant and vibration-proof temperature probes improve durability in marine diesel engines, propeller shafts, and onboard hydraulic systems.
Integration with Marine Automation & SCADA Systems:
Temperature sensors with HART, Modbus, or CAN bus communication ensure seamless integration into engine management and ship automation systems.
Wireless and IoT-enabled temperature monitors allow remote diagnostics and real-time alerts for critical system temperature changes.
Compliance with Maritime Regulations:
Ensure sensors meet IMO, SOLAS, and MARPOL requirements for engine exhaust emissions, HVAC safety, and fuel heating systems.
Temperature monitoring systems in refrigerated cargo holds and reefer containers should comply with ISO 1496-2 container refrigeration standards.
Reliability & Maintenance Efficiency:
Self-calibrating and drift-resistant RTDs reduce long-term maintenance needs in engine, boiler, and HVAC systems.
Multi-sensor redundancy improves safety in boiler pressure vessels and engine room fire detection systems.
Level Detection & Management
Accurate level detection and management are crucial for marine vessels and offshore operations, ensuring efficient fuel usage, ballast control, cargo handling, and wastewater management. Ships rely on precise tank level monitoring to optimize stability, safety, and regulatory compliance with IMO, MARPOL, and SOLAS standards. Advanced radar, ultrasonic, capacitive, and guided wave level sensors provide real-time monitoring, automation, and early leak detection, preventing overfills, system failures, and environmental hazards. With SCADA-integrated level monitoring, marine operators can achieve better operational efficiency, reduced maintenance, and improved safety for crew and cargo.
Level Detection & Management Applications for Marine Vessels
Marine and offshore operations require accurate level measurement across multiple shipboard systems to ensure safe and efficient fluid management. Key applications include:
Fuel & Lubricant Storage Tank Level Management:
Radar and guided wave level sensors provide real-time fuel level tracking in bunker fuel tanks, diesel storage, and LNG containment systems.
Capacitive and ultrasonic level sensors prevent fuel shortages or overfills, ensuring optimal fuel allocation for long voyages.
SCADA-connected fuel level monitoring systems support compliance with IMO Energy Efficiency Existing Ship Index (EEXI) and Carbon Intensity Indicator (CII) regulations.
Ballast Water & Bilge Level Monitoring:
Hydrostatic level sensors track ballast water levels in tanks and ballast pumping stations, optimizing vessel stability and draft.
Float-based level switches and pressure transmitters monitor bilge water accumulation, ensuring timely discharge and compliance with MARPOL Annex I oily water separation rules.
Automated ballast control systems integrate with pneumatic level sensors to maintain vessel trim, list, and draft balance.
Freshwater, Potable Water, & Wastewater Management:
Submersible hydrostatic level sensors provide accurate readings for drinking water storage, desalination plants, and greywater tanks.
Capacitive and optical level sensors prevent tank overflow and depletion, ensuring a continuous water supply for crew and onboard operations.
Ultrasonic level sensors in wastewater treatment systems regulate discharge processes, maintaining compliance with IMO and MARPOL effluent treatment guidelines.
Cargo Tank & Liquid Transfer Level Control:
Radar level transmitters measure liquid cargo levels in chemical tankers, crude oil carriers, and LNG transport vessels, preventing spillage.
TDR (Time-Domain Reflectometry) sensors ensure precise volume measurement for bulk liquid transfers, ensuring compliance with terminal and port authority safety regulations.
Overfill prevention sensors and alarms provide real-time cargo level tracking, reducing the risk of environmental contamination.
Key Purchasing Considerations
Choosing the right level detection and management solutions for marine applications requires evaluating fluid properties, vessel system requirements, and regulatory compliance. The following factors should guide decision-making:
Accuracy & Sensor Sensitivity:
Radar and guided wave level sensors ensure high-accuracy fuel and ballast water level measurement.
Hydrostatic and pressure-based level sensors provide stable readings in high-pressure storage tanks and wastewater systems.
Environmental Durability & Corrosion Resistance:
Stainless steel, titanium, and corrosion-resistant sensors withstand saltwater exposure and aggressive chemical environments.
Explosion-proof and intrinsically safe level sensors are required for fuel storage, LNG bunkering, and hazardous liquid cargo applications.
Integration with Ship Automation & SCADA Systems:
SCADA-compatible level sensors with HART, Modbus, or CAN bus communication enable real-time monitoring and remote control.
Wireless and IoT-enabled level monitoring solutions allow operators to track tank levels, detect leaks, and automate filling processes.
Compliance with Maritime Regulations:
Ensure sensors meet IMO, MARPOL, and USCG requirements for ballast water management, bilge treatment, and cargo handling.
Level detection systems in wastewater treatment and fuel management must meet EPA and environmental safety requirements.
Maintenance & Lifecycle Costs:
Self-cleaning and non-contact level sensors reduce maintenance needs in fuel, ballast, and wastewater applications.
Fail-safe level monitoring with automatic alarms ensures rapid response to fluid level abnormalities in shipboard systems.
Vibration & Structural Health Monitoring
Vibration & Structural Health Monitoring Applications for Marine Equipment
Proper structural and vibration analysis enhances ship performance, safety, and maintenance planning while reducing unexpected downtime and repair costs. Key applications include:
Engine & Propulsion System Vibration Analysis:
Tri-axial accelerometers and MEMS vibration sensors detect early signs of bearing wear, shaft misalignment, and torsional vibrations in main propulsion engines, generators, and gearboxes.
Piezoelectric vibration sensors monitor high-speed rotating components, preventing premature failure of turbochargers, auxiliary engines, and fuel pumps.
Real-time condition monitoring enables predictive maintenance, reducing engine downtime and improving fuel efficiency.
Propeller & Shaft Misalignment Detection:
Wireless vibration sensors monitor propeller shaft alignment, detecting cavitation-induced vibrations that may lead to mechanical stress or inefficiencies.
Torsional strain gauges and torque sensors provide data on propeller thrust imbalances, preventing damage to hull structures and propulsion bearings.
Automated shaft alignment monitoring improves vessel maneuverability and extends the lifespan of stern tube bearings and thrust blocks.
Hull & Structural Integrity Monitoring:
Fiber optic strain sensors continuously measure hull flexing, structural fatigue, and stress distribution in large cargo vessels, tankers, and naval ships.
Acoustic emission sensors detect cracks, corrosion, and impact damage in steel and composite ship structures.
Seismic and hull-mounted sensors provide early detection of wave-induced stress and extreme loading conditions, improving safety in offshore platforms and ice-class ships.
Rotating Machinery & HVAC System Vibration Detection:
Vibration monitoring systems in shipboard HVAC, refrigeration, and cooling systems ensure optimal performance and reduce noise pollution.
Dynamic balancing sensors detect anomalies in centrifugal fans, compressors, and marine ventilation units, preventing excessive vibrations.
Wireless vibration monitoring for auxiliary machinery enhances ship reliability by tracking generator, pump, and motor condition trends.
Seismic & Offshore Rig Structural Health Monitoring:
Structural monitoring systems (SHM) measure wave impact forces and stress accumulation on offshore oil rigs and floating production storage and offloading (FPSO) units.
Tilt and displacement sensors detect foundation shifting in seabed-anchored platforms, preventing failures in dynamic positioning and mooring systems.
Underwater sonar-based vibration analysis tracks subsea equipment stability, ensuring safe operations in deep-sea drilling and cable-laying vessels.
Key Purchasing Considerations
Selecting vibration and structural health monitoring solutions for marine applications requires evaluating sensor accuracy, environmental resistance, and integration with vessel systems. The following considerations should guide decision-making:
Accuracy & Sensitivity:
Tri-axial accelerometers and piezoelectric vibration sensors offer high-resolution monitoring of mechanical imbalances and resonance frequencies.
Strain gauges with fiber optic technology provide real-time stress and fatigue analysis for hull structures and propulsion shafts.
Environmental Durability & Marine-Grade Construction:
Corrosion-resistant sensors (stainless steel, titanium, and Inconel) are required for submerged and saltwater-exposed components.
Explosion-proof and intrinsically safe sensors should be used for hazardous areas such as LNG carriers and chemical tankers.
Integration with Marine Automation & SCADA Systems:
SCADA-compatible vibration and stress monitoring systems with Modbus, HART, or CAN bus communication enable real-time alerts and automated diagnostics.
Wireless and IoT-enabled vibration sensors allow remote performance tracking and predictive maintenance scheduling.
Compliance with Maritime Regulations:
Ensure compliance with IMO, SOLAS, ABS, and ClassNK requirements for structural integrity, propulsion system reliability, and onboard vibration control.
Hull stress monitoring and fatigue assessment systems should meet IACS (International Association of Classification Societies) standards.
Maintenance & Lifecycle Costs:
Self-calibrating and long-life vibration sensors reduce maintenance costs in high-load propulsion and power generation systems.
Redundant monitoring systems with automated fail-safes ensure continuous operation in mission-critical naval and commercial applications.
Gas Detection & Environmental Monitoring
Ensuring air quality and environmental safety is critical in marine and offshore applications, where confined spaces, fuel combustion, and cargo emissions create potential hazards for crew, passengers, and onboard systems. Toxic and combustible gas leaks, emissions from fuel burning, and oxygen depletion can pose significant risks, requiring continuous gas detection and environmental monitoring. Advanced infrared (IR), electrochemical, photoionization, and catalytic bead sensors provide real-time monitoring of hazardous gases, air quality tracking, and emissions control in compliance with IMO, MARPOL, and EPA maritime regulations.
Gas Detection & Environmental Monitoring Applications in Maritime Operations
Gas detection plays a crucial role in crew safety, fuel handling, confined space monitoring, and regulatory compliance across commercial ships, offshore platforms, and naval vessels. Key applications include:
Engine Room & Fuel Storage Gas Monitoring:
Electrochemical gas detectors monitor oxygen (O₂), carbon monoxide (CO), and nitrogen dioxide (NO₂) levels in engine rooms and auxiliary power units.
Catalytic and infrared (IR) gas sensors detect methane (CH₄), propane (C₃H₈), and hydrogen sulfide (H₂S) leaks in fuel bunkering stations, LNG storage tanks, and engine fuel lines.
Flame detection systems integrated with gas sensors provide early fire warning in boiler rooms and generator compartments, ensuring compliance with SOLAS fire safety regulations.
Exhaust Gas & Emission Monitoring for IMO & MARPOL Compliance:
NDIR (Non-Dispersive Infrared) analyzers track CO₂, NOx, and SOx levels in exhaust stacks, ensuring compliance with IMO Tier III emission control standards.
Particulate matter (PM) sensors monitor exhaust gas scrubber efficiency, optimizing fuel use and reducing airborne pollutants.
Continuous Emission Monitoring Systems (CEMS) provide real-time emissions data reporting, supporting compliance with MARPOL Annex VI fuel sulfur regulations.
Hazardous Cargo & Confined Space Gas Detection:
VOC (Volatile Organic Compound) analyzers detect hazardous fumes in chemical and crude oil tankers, ensuring safe cargo handling.
Multi-gas detectors monitor oxygen depletion, carbon dioxide buildup, and toxic gases in ballast tanks, enclosed holds, and wastewater treatment areas.
Portable gas monitors provide personal protection for crew members working in low-ventilation areas such as pump rooms and fuel bunkering stations.
Ballast Water & Bilge Gas Monitoring:
Dissolved oxygen (DO) and hydrogen sulfide (H₂S) sensors track anaerobic conditions in ballast tanks, preventing microbial contamination.
Gas detectors integrated into oily water separators ensure MARPOL Annex I compliance, reducing the risk of hydrocarbon emissions in wastewater discharge.
pH and salinity sensors optimize chemical treatment processes in ballast water management systems, ensuring proper neutralization before discharge.
Offshore & Subsea Environmental Monitoring:
Airborne gas sensors on offshore platforms track hydrocarbon leaks, drilling exhaust, and combustion gases, ensuring safe working conditions.
Methane and CO₂ sensors on subsea installations monitor gas seepage from underwater pipelines and wellheads, preventing environmental contamination.
Marine weather stations with real-time air quality monitoring ensure compliance with EPA and IMO environmental reporting requirements.
Key Purchasing Considerations
Selecting the right gas detection and environmental monitoring solutions for marine operations requires evaluating sensor accuracy, environmental durability, and regulatory requirements. The following factors should guide decision-making:
Accuracy & Sensor Sensitivity:
Electrochemical gas sensors provide high-precision detection for toxic gases and oxygen depletion in confined spaces.
Infrared (IR) and catalytic bead sensors detect combustible gas leaks in fuel storage and bunkering stations.
Photoionization detectors (PIDs) monitor VOC levels in chemical tanker holds and refinery offloading sites.
Environmental Durability & Marine-Grade Construction:
Explosion-proof and intrinsically safe gas detectors are required for LNG carriers, chemical tankers, and fuel storage areas.
Corrosion-resistant and waterproof gas sensors ensure long-term performance in high-humidity marine environments.
Shock-resistant gas detectors withstand vibrations in engines, pumps, and rotating machinery rooms.
Integration with Ship Automation & SCADA Systems:
Gas detection systems with HART, Modbus, or CAN bus communication ensure seamless integration into vessel safety automation systems.
Wireless and IoT-enabled sensors allow for remote air quality tracking in cargo holds, bunkering stations, and confined spaces.
Multi-gas analyzers with centralized control improve safety in fuel handling, emissions control, and hazardous material storage.
Compliance with Maritime Regulations:
Ensure gas detection systems comply with IMO, MARPOL Annex VI, SOLAS, and EPA requirements for ship emissions, hazardous gas exposure, and confined space entry.
Oxygen monitoring systems in enclosed spaces must meet ISGOTT (International Safety Guide for Oil Tankers and Terminals) recommendations.
Gas sensors for hazardous areas should comply with ATEX, IECEx, and UL explosion-proof certifications.
Reliability & Maintenance Considerations:
Self-calibrating and auto-zeroing gas sensors reduce maintenance costs in engine rooms, cargo holds, and wastewater systems.
Multi-redundant gas detection networks improve fail-safe reliability in high-risk areas such as LNG storage and oil refining terminals.
Remote diagnostics and cloud-based monitoring enable early detection of gas leaks and air quality issues, improving ship safety.
Analytical Instrumentation for Compliance
Maintaining water quality and environmental compliance is critical in marine and offshore operations to protect ecosystems, crew health, and onboard systems. Ships and offshore platforms must meet IMO, MARPOL, EPA, and USCG regulations governing wastewater discharge, ballast water treatment, and oil spill prevention. Advanced analytical instrumentation, including turbidity meters, pH sensors, conductivity analyzers, and oil-in-water monitors, ensures real-time monitoring and regulatory compliance for onboard water treatment systems. SCADA-integrated analytical solutions improve efficiency, reduce chemical usage, and prevent environmental violations, ensuring sustainable maritime operations.
Analytical Instrumentation for Water Quality Applications & Marine Compliance
Precise analytical measurement of shipboard and offshore water systems ensures safe operation, regulatory compliance, and minimal environmental impact. Key applications include:
Ballast Water Treatment & Compliance Monitoring:
Turbidity and UV transmittance sensors verify effective filtration and disinfection in ballast water treatment systems (BWTS), ensuring compliance with IMO Ballast Water Management Convention (BWMC).
Chlorine and total dissolved solids (TDS) analyzers optimize chemical dosing in electro-chlorination ballast water treatment systems.
Real-time ballast water microbial sensors detect harmful bacteria and invasive species, preventing environmental contamination in discharge areas.
Bilge & Wastewater Discharge Quality Control:
Oil-in-water analyzers (OIW) with laser-induced fluorescence (LIF) detect hydrocarbon contamination, ensuring compliance with MARPOL Annex I oily water discharge regulations.
pH and dissolved oxygen (DO) sensors track water quality in shipboard wastewater treatment plants, optimizing aeration and neutralization processes.
COD (Chemical Oxygen Demand) and BOD (Biochemical Oxygen Demand) analyzers ensure treated wastewater meets IMO and EPA discharge requirements before overboard release.
Desalination & Freshwater System Monitoring:
Conductivity and total organic carbon (TOC) analyzers verify the purity of freshwater generated by reverse osmosis (RO) and evaporators onboard ships.
Nitrate and chlorine residual sensors ensure compliance with potable water safety standards for crew drinking water and food preparation.
UV disinfection system controllers optimize biological safety by monitoring UV intensity in freshwater treatment plants.
Cargo & Fuel Tank Water Contamination Detection:
Water-in-fuel sensors detect moisture contamination in marine diesel oil (MDO) and heavy fuel oil (HFO) storage tanks, preventing combustion inefficiencies.
Sulfur content analyzers measure compliance with IMO 2020 fuel sulfur regulations, ensuring proper fuel treatment.
Saltwater intrusion sensors protect cargo tanks and pipelines from corrosion caused by seawater ingress.
Cooling & Boiler Water Quality Management:
pH and conductivity analyzers regulate boiler water treatment, preventing scale buildup and corrosion in marine steam systems.
Silica and hardness analyzers ensure optimal chemical balance in cooling water systems, reducing fouling in heat exchangers and condensers.
Ammonia and phosphate sensors track chemical dosing in marine engine cooling circuits, ensuring longevity and efficiency.
Key Purchasing Considerations
Choosing the right analytical instrumentation for water quality monitoring in marine applications requires evaluating measurement accuracy, environmental durability, and integration capabilities. The following factors should guide decision-making:
Accuracy & Sensitivity:
High-resolution turbidity and UV transmittance sensors ensure precise ballast water treatment monitoring.
pH and dissolved oxygen analyzers with low detection limits improve wastewater treatment efficiency.
Marine-Grade Durability & Environmental Resistance:
Corrosion-resistant materials (stainless steel, PTFE, and titanium) are essential for seawater-exposed sensors.
Explosion-proof and intrinsically safe analyzers must be used in fuel and chemical cargo monitoring.
Integration with Marine Automation & SCADA Systems:
HART, Modbus, or CAN bus-enabled analytical sensors support seamless integration into shipboard water management systems.
Wireless IoT-enabled water quality analyzers allow for remote monitoring and automated regulatory reporting.
Compliance with Maritime Regulations:
Ensure analytical instrumentation meets IMO, MARPOL Annex I & IV, BWMC, and EPA discharge limits.
Ballast water treatment monitoring sensors should comply with USCG and International Maritime Organization (IMO) performance standards.
Reliability & Maintenance Considerations:
Self-cleaning and drift-resistant sensors reduce maintenance in seawater and wastewater applications.
Automated calibration and fail-safe alarms ensure continuous operation in mission-critical onboard systems.
Industry Standards & Regulatory Compliance
The marine and shipping industry operates under strict environmental and safety regulations to ensure the protection of marine ecosystems, crew safety, and efficient vessel operations. Compliance with international standards set by the International Maritime Organization (IMO), the Marine Pollution Convention (MARPOL), and the Environmental Protection Agency (EPA) is essential for controlling emissions, wastewater discharge, ballast water treatment, and fuel quality. Ships must integrate advanced instrumentation, automation systems, and real-time monitoring technologies to meet these regulatory requirements while optimizing efficiency, sustainability, and operational safety.
IMO, MARPOL, and EPA Compliance for Marine & Shipping
Vessels operating in international waters, ports, and offshore regions must adhere to global and regional maritime laws regulating fuel emissions, water discharge, and hazardous materials. Key compliance frameworks include:
IMO MARPOL Annex I & IV (Oil & Sewage Discharge Regulations):
Enforces bilge water treatment and oil-in-water monitoring, requiring vessels to install 15 ppm oil content monitors for wastewater discharge.
Regulates sewage treatment systems, ensuring that onboard wastewater meets effluent quality standards before discharge into the sea.
IMO MARPOL Annex VI (Air Emission & Fuel Sulfur Regulations):
Establishes fuel sulfur content limits, requiring vessels to use low-sulfur fuels (≤0.5% sulfur) or exhaust gas cleaning systems (scrubbers).
Implements NOx emission control areas (ECAs), requiring continuous monitoring of engine emissions and exhaust gas treatment systems.
IMO Ballast Water Management Convention (BWMC):
Mandates the use of ballast water treatment systems (BWTS) with UV disinfection, filtration, or electrochlorination to prevent the spread of invasive species.
Requires vessels to log and report ballast water treatment performance and discharge compliance.
EPA Vessel General Permit (VGP) & USCG Regulations:
Regulates discharge of graywater, ballast water, and bilge water from vessels in U.S. waters, ensuring compliance with effluent quality limits.
Enforces scrubber washwater discharge monitoring, requiring pH, turbidity, and heavy metal content analysis.
Environmental & Safety Standards for Offshore & Maritime Operations
Maritime operations require compliance with safety and environmental protection protocols to mitigate pollution risks, structural failures, and hazardous exposure. Key standards include:
SOLAS (Safety of Life at Sea) Regulations:
Governs fire detection, gas monitoring, emergency shutoff systems, and hull integrity monitoring for vessel and crew safety.
Mandates lifeboat, engine room, and cargo hold safety instrumentation to detect fire, gas leaks, or flooding.
IACS (International Association of Classification Societies) & ABS (American Bureau of Shipping) Standards:
Regulate hull stress monitoring, vibration analysis, and fatigue assessment for vessel structural integrity.
Require automated warning systems and structural health sensors for ships operating in harsh environments.
IMO & EPA Marine Plastic & Waste Disposal Regulations:
Require onboard waste separation, incineration monitoring, and marine pollution tracking.
Mandate wastewater treatment systems for onboard graywater and food waste processing before discharge.
Benefits of Working With Clipper Controls
Clipper Controls provides high-precision instrumentation and automation solutions to help marine and shipping operators ensure regulatory compliance, optimize efficiency, and enhance safety. Our flow meters, level sensors, gas analyzers, and water quality monitors support fuel management, ballast water treatment, emissions control, and structural health monitoring, improving vessel performance.
Clipper Controls offers SCADA-integrated solutions for real-time diagnostics, predictive maintenance, and automated regulatory reporting. Our marine-grade sensors and analyzers withstand harsh saltwater environments, extreme temperatures, and high-vibration conditions, ensuring long-term reliability. Partnering with us helps ship operators reduce downtime, improve sustainability, and maintain smooth operations at sea.
Case Studies & Success Stories
Explore how Clipper Controls has helped marine and offshore operators enhance fuel efficiency, improve emissions compliance, and optimize water treatment systems.
Click here to read our marine & shipping case studies.
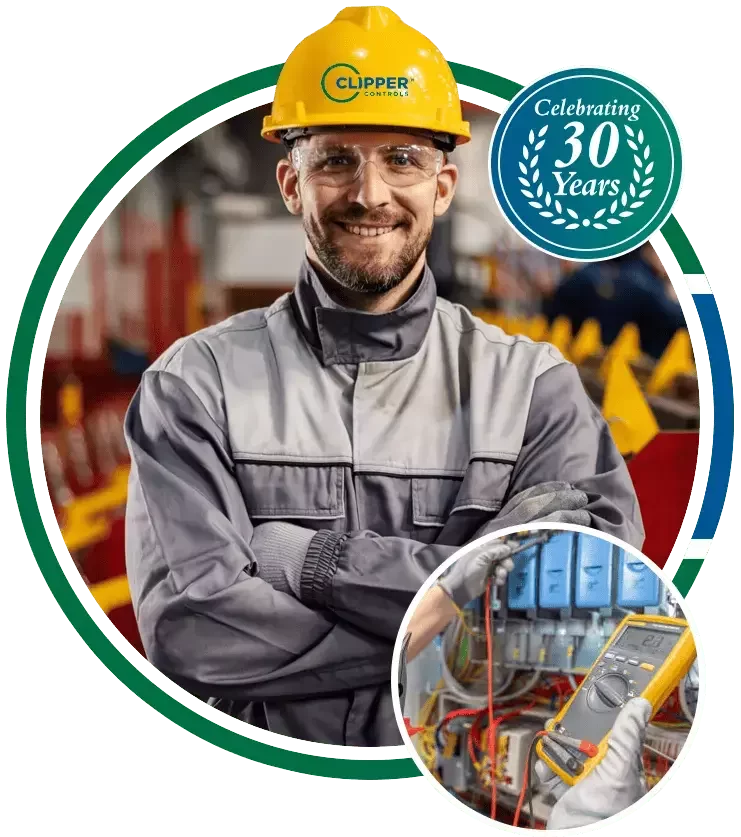
Real Results, Real Impact:
Thanks to Clipper Controls, our wastewater treatment plant improved efficiency & compliance with top-tier flow meters. Reliable solutions, great support! We recommend Clipper Controls to all our partner companies.
~ John Smith, Controls Engineer @ ABC Company
Clipper Controls helped our city upgrade water monitoring systems, ensuring accuracy & compliance. Reliable solutions & excellent customer service!
~ Nancy Patel, Procurement @ ABC Company
~ John Smith, Controls Engineer @ ABC Company
Ready to Work With Us?
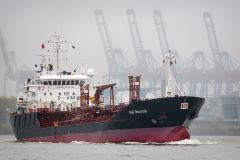
Quick Page Navigation:
🔹How Our Products Support Your Industry
Pressure Monitoring & Regulation
Temperature Sensing & Control
Vibration & Structural Monitoring
Gas Detection & Environmental Monitoring
Analytical Instrumentation for Compliance
🔹Industry Standards & Regulatory Compliance
🔹Benefits of Working With Clipper Controls