Oil & Gas Pipeline Process Control Applications
Application Overview
Oil and gas pipeline operations rely on advanced instrumentation, controls, and analyzers to ensure safe, efficient, and regulatory-compliant transport of crude oil, natural gas, and refined products. Pipeline systems must be continuously monitored for flow rate, pressure stability, temperature variations, leak detection, and corrosion risk to prevent operational failures, environmental hazards, and costly downtime. Real-time SCADA integration, IoT-enabled sensors, and automated control valves allow for remote monitoring and rapid response to fluctuations in pipeline conditions, improving operational reliability and compliance with API, PHMSA, and EPA standards.
To maintain pipeline integrity, industries implement multi-layered safety systems, predictive maintenance strategies, and inline analytical instrumentation for quality assurance. Ultrasonic and magnetic flow meters track volumetric throughput with high accuracy, while pressure and vibration sensors detect anomalies that could indicate structural weakness or pipeline damage. Gas chromatographs and moisture analyzers ensure product composition integrity and detect contaminants, optimizing transportation efficiency and preventing equipment degradation. With the integration of real-time leak detection systems, smart pigging technologies, and automated shutdown protocols, pipeline operators can mitigate risks, enhance energy efficiency, and ensure uninterrupted fuel delivery.
How Our Products Support Your Industry
Clipper Controls provides high-precision instrumentation, automation, and monitoring solutions to ensure the safety, efficiency, and regulatory compliance of oil and gas pipeline operations. Our flow meters, pressure sensors, gas analyzers, and SCADA-integrated control systems enable real-time monitoring of flow rates, leak detection, and equipment performance, minimizing downtime and environmental risks while optimizing transportation efficiency.
With expertise in pipeline integrity management, regulatory compliance, and predictive maintenance, Clipper Controls offers customized solutions for flow assurance, corrosion monitoring, and gas quality analysis. Our IoT-enabled sensors, smart pigging technologies, and automated shutdown systems enhance pipeline safety, prevent failures, and reduce operational costs. Whether monitoring liquid and gas flow, detecting anomalies, or ensuring adherence to PHMSA, API, and EPA standards, Clipper Controls provides the technology and expertise needed for reliable and compliant pipeline operations.
Key Applications and Solutions
Flow Measurement & Control
Flow Measurement & Control Applications in Oil & Gas Pipelines
Flow measurement and control systems are essential for ensuring pipeline integrity, operational efficiency, and regulatory compliance in various oil and gas transport applications. Key applications include:
Ultrasonic & Coriolis Flow Meters for Liquid & Gas Transport:
Ultrasonic transit-time flow meters provide non-intrusive, high-accuracy flow measurement for crude oil, natural gas, and LNG pipelines, reducing pressure loss and maintenance needs.
Coriolis mass flow meters enable direct mass measurement of liquid hydrocarbons, ensuring precise flow rate tracking for custody transfer applications.
Turbine and positive displacement (PD) meters are commonly used in refined product pipelines where high repeatability and reliability are required.
Volumetric & Mass Flow Monitoring for Custody Transfer:
Multi-path ultrasonic flow meters ensure accurate measurement of gas volume flow in natural gas transmission pipelines, meeting AGA-9 and API MPMS standards.
Coriolis meters provide direct density and flow measurement, ensuring compliance with API MPMS Chapter 5 for custody transfer of petroleum liquids.
Differential pressure (DP) flow meters with orifice plates, venturi tubes, or wedge elements are widely used in pipeline metering stations to track fluid movement with high accuracy.
Automated Flow Control for Pipeline Efficiency & Leak Detection:
Flow control valves adjust pressure and flow rates based on real-time SCADA data, optimizing energy use and preventing pipeline surges.
Remote flow monitoring sensors detect flow rate deviations, alerting operators to potential leaks, theft, or equipment failures.
Pipeline balancing and batching systems regulate the movement of multiple petroleum products, preventing cross-contamination and ensuring operational efficiency.
LNG & Cryogenic Flow Measurement for Gas Transport:
Ultrasonic flow meters designed for cryogenic applications accurately measure liquefied natural gas (LNG) flow rates in transport and storage applications.
Coriolis meters in LNG pipelines provide density, temperature, and mass flow measurement, ensuring safe and efficient gas transport.
Vortex flow meters help optimize steam and gas flow control in LNG regasification plants.
Key Purchasing Considerations
Selecting the right flow measurement and control systems for oil and gas pipelines requires consideration of accuracy, durability, and compliance with industry standards. The following factors should guide decision-making:
Measurement Accuracy & Repeatability:
Ultrasonic flow meters (multi-path) provide high-precision, non-intrusive flow measurement, minimizing pressure drop.
Coriolis meters offer direct mass flow measurement, improving custody transfer accuracy and ensuring compliance with API MPMS standards.
Differential pressure meters with orifice plates are ideal for high-pressure gas pipeline metering, ensuring consistent flow rate readings.
Environmental Durability & Sensor Reliability:
Explosion-proof and intrinsically safe flow sensors meet ATEX and IECEx certification for hazardous oil and gas environments.
High-pressure-rated and corrosion-resistant flow meters extend equipment life in offshore and extreme temperature applications.
Self-diagnostic and self-calibrating flow meters reduce maintenance needs and ensure long-term operational stability.
Integration with Pipeline SCADA & Automation Systems:
Flow sensors with Modbus, HART, or BACnet communication ensure seamless integration into SCADA and industrial automation platforms.
Wireless IoT-enabled flow meters allow for remote monitoring, predictive maintenance, and real-time alerts.
AI-driven analytics platforms optimize flow balancing and anomaly detection, improving pipeline efficiency and reducing downtime.
Compliance with Industry Standards & Regulatory Requirements:
Ensure flow meters meet API MPMS, AGA-3, AGA-7, and AGA-9 standards for custody transfer applications.
Offshore flow monitoring systems must comply with BSEE, PHMSA, and MMS safety regulations.
Custody transfer meters should align with OIML R117 and ISO 6976 standards for accurate volume and energy calculations.
Maintenance & Lifecycle Considerations:
Long-term calibration stability and self-diagnostic capabilities reduce the frequency of recalibration.
Fail-safe automation features with built-in redundancy prevent downtime due to sensor failure.
Predictive maintenance tools integrated with SCADA systems help identify wear and tear before failure occurs.
Pressure Measurement & Control
Accurate pressure monitoring and regulation are essential for ensuring pipeline integrity, operational efficiency, and safety in oil and gas transportation networks. Pressure fluctuations can lead to pipeline failures, leaks, and product loss, making real-time pressure measurement and control systems a critical component of pipeline management. Advanced pressure transmitters, differential pressure sensors, and automated pressure control valves help maintain stable operating conditions, prevent overpressure incidents, and optimize flow distribution. SCADA-integrated monitoring solutions allow operators to track real-time pressure data, detect anomalies, and automate emergency shutdowns, ensuring compliance with PHMSA, API, and ASME pipeline safety standards.
Pressure Monitoring & Regulation Applications in Pipeline Systems
Effective pressure control and monitoring solutions enhance pipeline safety, reduce energy consumption, and improve regulatory compliance. Key applications include:
Differential Pressure Sensors for Pipeline Integrity:
Differential pressure (DP) transmitters measure pressure drops across pipeline sections, helping detect blockages, leaks, or flow imbalances.
Orifice plate DP meters optimize gas and liquid flow measurement, ensuring compliance with API MPMS Chapter 14.3 standards.
Multivariable pressure transmitters provide real-time pressure, temperature, and flow readings, improving pipeline efficiency and safety monitoring.
Automated Pressure Control for Leak Prevention & Pipeline Safety:
Remote-controlled pressure regulating valves (PRVs) adjust pressure levels dynamically, preventing overpressure conditions.
Surge protection and transient pressure monitoring systems mitigate the risks of sudden pressure spikes caused by valve closures or pump failures.
Pipeline rupture detection algorithms use pressure drop analysis to trigger emergency shutdowns, reducing the impact of leaks.
High-Pressure Pipeline Monitoring in Offshore & High-Risk Areas:
Subsea and offshore pressure sensors ensure safe transport of hydrocarbons through deepwater pipelines.
Explosion-proof and high-temperature-rated pressure transmitters provide reliable readings in LNG, crude oil, and natural gas pipelines.
Pipeline pigging pressure monitoring ensures effective cleaning and inspection operations without disrupting flow.
Gas Compression & Pressure Management in Transmission Pipelines:
Discharge and suction pressure monitoring in compressor stations ensures optimal gas flow and efficiency.
Pressure relief valves (PRVs) and emergency shutdown (ESD) systems prevent hazardous overpressures.
Real-time pressure balancing in multi-phase pipeline networks reduces energy consumption and improves flow stability.
Key Purchasing Considerations
Selecting the right pressure monitoring and regulation systems requires evaluating sensor accuracy, durability, automation capabilities, and compliance with industry standards. The following factors should guide decision-making:
Measurement Accuracy & Sensor Sensitivity:
High-resolution differential pressure transmitters ensure precise monitoring of flow restrictions and pipeline integrity.
Multivariable sensors with integrated temperature and flow measurement improve data accuracy and system efficiency.
Smart pressure sensors with self-calibration features minimize drift and ensure long-term accuracy.
Environmental Durability & Sensor Longevity:
Corrosion-resistant, explosion-proof, and high-pressure-rated pressure transmitters withstand harsh oil and gas environments.
Subsea and high-temperature sensors ensure reliable operation in LNG terminals, offshore rigs, and high-pressure gas pipelines.
Wireless pressure sensors with IoT integration enable remote monitoring in hard-to-reach locations.
Integration with SCADA & Pipeline Automation Systems:
Pressure sensors with Modbus, HART, and BACnet communication integrate seamlessly with SCADA systems for centralized monitoring.
AI-driven predictive maintenance platforms analyze pressure trends to prevent failures before they occur.
Remote shutdown and pressure control systems improve response time in emergency situations.
Compliance with Pipeline Safety & Environmental Regulations:
Ensure compliance with PHMSA, API 521, and ASME B31.8 pipeline safety standards for high-pressure gas and liquid transport.
Offshore and subsea pressure monitoring systems should meet BSEE and MMS regulatory requirements.
Emergency shutdown (ESD) systems must align with OSHA and NFPA hazardous materials handling guidelines.
Reliability & Maintenance Considerations:
Fail-safe pressure transmitters with built-in redundancy ensure continuous operation.
Self-diagnostic sensors and AI-enabled anomaly detection improve long-term system reliability.
Wireless remote monitoring capabilities reduce maintenance needs and enhance operational efficiency.
Temperature Sensing & Control
Accurate temperature sensing and control are critical in oil and gas pipeline operations to ensure safe transport, product integrity, and regulatory compliance. Temperature variations can affect fluid viscosity, gas density, and material expansion, leading to flow inconsistencies, pipeline stress, and energy inefficiencies. High-precision temperature sensors, thermal monitoring systems, and automated control solutions help operators maintain optimal operating conditions, prevent thermal expansion issues, and ensure efficient transport of hydrocarbons. Integration with SCADA and IoT-enabled temperature control systems allows for real-time monitoring, predictive maintenance, and process optimization across pipeline networks.
Temperature Sensing & Control Applications in Pipeline Operation
Temperature monitoring is essential for preventing material degradation, optimizing energy efficiency, and maintaining safe operating conditions in oil and gas pipelines. Key applications include:
Thermal Monitoring for Product Quality & Flow Stability:
Resistance Temperature Detectors (RTDs) and thermocouples track temperature variations along pipelines, ensuring optimal flow conditions for crude oil, LNG, and refined products.
Infrared temperature sensors provide non-contact temperature measurement, useful for detecting temperature inconsistencies along pipeline surfaces.
Distributed Temperature Sensing (DTS) with fiber optic technology enables real-time temperature monitoring over long distances, helping detect leaks and flow disruptions.
Heat Management in LNG & Crude Oil Transport:
Cryogenic temperature sensors ensure safe handling and storage of LNG, preventing gas boil-off and thermal stress.
Heat tracing and insulation monitoring systems regulate pipeline temperature, ensuring viscosity control in heavy crude and waxy oil transport.
Smart temperature controllers optimize steam tracing in pipeline heating systems, reducing energy costs while maintaining flow efficiency.
Pipeline Integrity & Stress Monitoring in Extreme Environments:
High-temperature sensors monitor expansion and contraction in high-temperature pipeline operations, preventing thermal stress-induced damage.
Subsea pipeline temperature monitoring systems ensure stable transport conditions in deepwater and offshore environments.
Corrosion-resistant thermocouples provide accurate readings in high-pressure, chemically reactive pipeline environments.
Temperature Compensation for Gas & Liquid Measurement:
Temperature-compensated flow meters adjust readings for gas expansion and contraction, ensuring accurate mass flow measurement.
Automated temperature compensation in custody transfer systems ensures precise billing and compliance with API MPMS standards.
SCADA-integrated temperature sensors provide real-time data for flow adjustments, optimizing energy efficiency in pipeline operations.
Key Purchasing Considerations
Selecting the right temperature sensing and control solutions for pipeline applications requires evaluating sensor accuracy, durability, system compatibility, and regulatory compliance. The following factors should guide decision-making:
Measurement Accuracy & Sensor Sensitivity:
Platinum RTDs (Class A, ±0.1°C accuracy) provide high-precision temperature measurement in oil and gas pipelines.
Fast-response thermocouples (Type K, J, or N) ensure instantaneous temperature monitoring in high-temperature crude and gas transmission.
Infrared and fiber optic DTS sensors provide continuous thermal profiling for pipeline leak detection and stress analysis.
Environmental Durability & Sensor Longevity:
Corrosion-resistant, high-pressure-rated sensors withstand harsh environments in offshore, subsea, and high-temperature pipeline applications.
Explosion-proof and intrinsically safe temperature sensors meet ATEX, IECEx, and API safety certifications.
Cryogenic temperature probes ensure reliable operation in LNG and low-temperature applications.
Integration with SCADA & Automation Systems:
Temperature sensors with Modbus, HART, or BACnet communication enable seamless integration into SCADA, pipeline automation, and leak detection systems.
Wireless IoT-enabled temperature sensors allow for remote monitoring, predictive analytics, and automated alarms.
AI-driven thermal analytics platforms enhance predictive maintenance and failure prevention.
Compliance with Industry Standards & Regulations:
Ensure compliance with API MPMS, ASME B31.3, and PHMSA temperature monitoring requirements.
Cryogenic and LNG transport temperature sensors must meet ISO 21903 and NFPA safety guidelines.
Pipeline integrity monitoring systems should align with DOT and ASTM standards for material stress analysis.
Reliability & Maintenance Considerations:
Self-calibrating and drift-resistant temperature sensors reduce maintenance needs and ensure long-term stability.
Multi-redundancy temperature monitoring with fail-safe alarms ensures continued operation in critical infrastructure.
Thermal imaging and predictive diagnostics improve early detection of anomalies and maintenance scheduling.
Gas Quality & Composition Analysis
Accurate gas quality and composition analysis is essential in oil and gas pipeline operations to ensure safe transport, regulatory compliance, and process optimization. The composition of natural gas and other hydrocarbons varies depending on the source, requiring continuous monitoring of energy content, contaminants, and moisture levels. Gas chromatographs, moisture analyzers, and infrared (IR) spectrometers provide real-time measurement of hydrocarbons, CO₂, H₂S, oxygen, and water vapor, helping pipeline operators maintain pipeline integrity, prevent corrosion, and optimize combustion efficiency. SCADA-integrated and IoT-enabled gas analysis systems support automated data logging, predictive maintenance, and regulatory reporting, ensuring adherence to AGA, API, and EPA standards.
Gas Quality & Composition Analysis Applications
Precise gas quality monitoring ensures efficient pipeline operations, protects critical infrastructure, and enables compliance with environmental and safety regulations. Key applications include:
Moisture & Contaminant Detection in Natural Gas Pipelines:
Dew point analyzers detect water vapor content in natural gas, preventing condensation, hydrate formation, and pipeline corrosion.
H₂S and CO₂ gas analyzers measure corrosive contaminants that can compromise pipeline materials and reduce gas quality.
Electrochemical oxygen sensors monitor O₂ levels in natural gas transport, ensuring compliance with pipeline safety standards.
Gas Chromatography for Hydrocarbon Composition Analysis:
Gas chromatographs (GCs) determine BTU value, methane (CH₄), ethane (C₂H₆), propane (C₃H₈), and heavier hydrocarbons, ensuring precise energy content measurement.
Chromatographic analysis verifies compliance with AGA 8 and GPA 2261 standards for natural gas custody transfer and billing.
Portable gas chromatographs allow for on-site analysis of gas quality, reducing operational risks and downtime.
Real-Time Monitoring for Process Optimization & Leak Detection:
Mass spectrometers and IR absorption sensors provide continuous monitoring of gas purity and leak detection.
Ultrasonic and thermal conductivity gas analyzers help optimize gas compression and transmission efficiency.
SCADA-integrated monitoring systems provide automated alerts for off-spec gas composition, ensuring quick adjustments to maintain pipeline quality.
Compliance with Regulatory & Environmental Standards:
Gas quality analyzers detect sulfur compounds and VOCs, preventing environmental violations.
Continuous monitoring of flared gas composition ensures compliance with EPA regulations on methane and VOC emissions.
Real-time analysis of CO₂ and hydrogen levels ensures adherence to carbon capture and sequestration (CCS) protocols.
Key Purchasing Considerations
Selecting the right gas quality and composition analysis solutions requires evaluating sensor precision, integration capabilities, and regulatory compliance. The following factors should guide decision-making:
Measurement Accuracy & Sensor Sensitivity:
Gas chromatographs with high-resolution separation columns ensure accurate hydrocarbon composition analysis.
NDIR (Non-Dispersive Infrared) analyzers provide real-time detection of CO₂, CH₄, and other gases.
Electrochemical and optical sensors detect ppm/ppb levels of H₂S, CO₂, and oxygen impurities.
Environmental Durability & Sensor Longevity:
Explosion-proof, ATEX-certified gas analyzers ensure safety in hazardous oil and gas environments.
Corrosion-resistant, high-pressure-rated gas sensors extend operational life in subsea and offshore pipelines.
Self-calibrating gas analyzers reduce maintenance needs and ensure long-term accuracy.
Integration with SCADA & Pipeline Monitoring Systems:
Gas quality analyzers with Modbus, HART, or BACnet communication allow seamless integration into SCADA and process control platforms.
IoT-enabled gas sensors enable remote monitoring, predictive maintenance, and automated compliance reporting.
Cloud-based analytics platforms provide real-time visualization of gas composition trends and performance metrics.
Compliance with Industry & Environmental Regulations:
Ensure compliance with AGA 8, API 14.1, and GPA 2261 standards for natural gas measurement and reporting.
Gas quality monitoring for pipeline transmission must align with PHMSA and DOT safety regulations.
Emission tracking systems must meet EPA Clean Air Act requirements for methane and VOC monitoring.
Reliability & Maintenance Considerations:
Self-calibrating and auto-zeroing gas analyzers ensure continuous accuracy and low maintenance.
Multi-sensor redundancy and fail-safe alarms improve reliability in critical pipeline monitoring applications.
Real-time predictive maintenance systems help reduce downtime and improve long-term pipeline performance.
Leak Detection & Pipeline Integrity Monitoring
Ensuring pipeline integrity and early leak detection is critical for preventing environmental contamination, reducing product loss, and maintaining regulatory compliance in oil and gas transportation systems. Leaks, ruptures, and structural failures can result in significant safety hazards, costly downtime, and regulatory penalties. Implementing advanced leak detection and integrity monitoring systems, including fiber optic sensing, acoustic sensors, flow imbalance detection, and real-time pressure monitoring, enables operators to identify and respond to leaks before they escalate. Integration with SCADA and IoT-based monitoring platforms allows for continuous pipeline surveillance, predictive maintenance, and automated emergency response, ensuring adherence to PHMSA, API 1175, and EPA safety standards.
Leak Detection & Pipeline Integrity Monitoring Applications
Comprehensive leak detection and structural health monitoring solutions help oil and gas pipeline operators enhance safety, optimize performance, and comply with regulatory requirements. Key applications include:
Fiber Optic Sensing for Real-Time Leak Detection:
Distributed Acoustic Sensing (DAS) and Distributed Temperature Sensing (DTS) provide continuous real-time monitoring along entire pipeline routes, detecting pressure changes, leaks, and tampering.
DTS systems identify temperature variations caused by escaping gas or liquids, ensuring early detection of small leaks before they become hazardous.
Pipeline strain and vibration monitoring using fiber optics helps detect land movement, mechanical stress, and external interference.
Acoustic & Ultrasonic Leak Detection in Pipeline Systems:
Ultrasonic flow sensors and acoustic emission sensors detect changes in flow patterns and vibrations, indicating potential leaks or cracks.
Hydrophone-based acoustic monitoring enables the detection of leaks in liquid and gas pipelines by capturing sound anomalies.
SCADA-integrated leak detection algorithms analyze flow data, pressure changes, and sound waves to pinpoint leak locations accurately.
Smart Pigging & Inline Inspection (ILI) Technologies:
Magnetic flux leakage (MFL) pigs detect metal loss, corrosion, and mechanical defects in pipeline walls.
Ultrasonic intelligent pigs assess pipeline thickness, weld integrity, and internal damage, ensuring long-term structural health.
Caliper pigs provide geometry measurement and dent detection, identifying pipeline deformations that could lead to failures.
Flow Imbalance & Pressure Drop Monitoring for Leak Prevention:
Mass balance and real-time transient model (RTTM) monitoring track discrepancies between inflow and outflow rates, detecting hidden leaks.
Pressure wave detection systems analyze sudden pressure drops and surges, providing early warnings for ruptures or valve failures.
Automated emergency shutdown (ESD) systems integrate with leak detection to rapidly isolate affected pipeline sections and prevent further damage.
Key Purchasing Considerations
Selecting the right leak detection and pipeline integrity monitoring solutions requires evaluating sensitivity, response time, environmental resilience, and compliance standards. The following considerations should guide decision-making:
Detection Accuracy & Response Time:
Fiber optic DTS/DAS systems provide continuous, real-time data with high spatial accuracy for early leak detection.
Ultrasonic and acoustic sensors ensure high-resolution leak localization, reducing false alarms.
Multi-layered detection strategies (flow balance, pressure monitoring, and acoustics) improve reliability and reduce detection time.
Environmental Durability & Sensor Longevity:
Explosion-proof, high-temperature-rated, and corrosion-resistant sensors ensure long-term performance in harsh oil and gas environments.
Subsea and high-pressure leak detection sensors are critical for offshore and deepwater pipelines.
Wireless and remote sensing technologies improve monitoring coverage in difficult-to-access locations.
Integration with SCADA & Pipeline Management Systems:
Leak detection sensors with Modbus, HART, or BACnet connectivity allow seamless integration with SCADA and real-time monitoring platforms.
AI-driven anomaly detection and predictive maintenance systems provide automated early warning alerts and historical trend analysis.
Cloud-based monitoring solutions enable remote access, real-time visualization, and compliance reporting.
Compliance with Pipeline Safety & Environmental Regulations:
Ensure compliance with PHMSA (49 CFR Part 195), API 1175, and DOT leak detection requirements for hazardous liquid and gas pipelines.
Environmental monitoring systems must align with EPA spill prevention and control (SPCC) regulations.
Offshore and subsea leak detection must meet BSEE and MMS standards for deepwater integrity monitoring.
Reliability & Maintenance Considerations:
Self-calibrating and self-learning leak detection algorithms reduce false positives and improve long-term accuracy.
Redundant monitoring systems with fail-safe alarms ensure uninterrupted pipeline surveillance and emergency response.
Predictive maintenance analytics help operators identify weaknesses before failures occur, reducing operational risks.
Corrosion Monitoring & Erosion Monitoring
Corrosion and erosion present significant challenges in oil and gas infrastructure, impacting pipeline integrity, asset lifespan, and operational efficiency. Exposure to harsh chemicals, moisture, high-pressure flows, and temperature extremes can accelerate metal degradation, leading to leaks, pipeline ruptures, and costly unplanned maintenance. Implementing real-time corrosion and erosion monitoring solutions, such as electrochemical sensors, ultrasonic thickness gauges, and corrosion coupons, helps operators detect early-stage material loss, optimize protective coatings and cathodic protection systems, and ensure compliance with API, NACE, and PHMSA industry standards. By integrating SCADA and IoT-based corrosion monitoring platforms, oil and gas operators can enable predictive maintenance, prevent catastrophic failures, and reduce infrastructure downtime.
Corrosion & Erosion Monitoring Applications in Oil & Gas Infrastructure
Effective corrosion and erosion detection is essential for maintaining pipeline longevity, offshore platform safety, and refinery equipment reliability. Key applications include:
Real-Time Corrosion Rate Analysis for Pipeline Longevity:
Electrochemical corrosion monitoring sensors measure corrosion rate, pH levels, and metal ion concentration, ensuring early detection of pipeline degradation.
Ultrasonic thickness gauges provide non-destructive monitoring of pipeline wall thickness, identifying areas affected by corrosion, pitting, and erosion.
Hydrogen permeation sensors help detect corrosion-related hydrogen embrittlement in high-pressure gas pipelines.
Cathodic Protection & Coating Performance Monitoring:
Cathodic protection (CP) monitoring systems measure voltage potential in pipelines and storage tanks, preventing electrochemical corrosion.
Remote monitoring of CP rectifiers and anode systems ensures continuous protection against external corrosion in buried or submerged pipelines.
Protective coating integrity sensors track the degradation of epoxy, polyurethane, and fusion-bonded epoxy (FBE) coatings used in offshore and underground pipeline protection.
Erosion Detection in High-Velocity Gas & Liquid Pipelines:
Acoustic sand and erosion monitors detect erosion caused by high-velocity flow, entrained particles, and turbulent conditions.
Ultrasonic erosion sensors measure wall thinning in high-pressure pipelines, elbows, and bends, preventing structural failures.
Differential pressure-based erosion monitoring identifies erosion-prone locations in gas compressor stations and downstream processing units.
Subsea & Offshore Corrosion Monitoring for Marine Environments:
Deepwater corrosion probes and environmental exposure sensors track metal loss in subsea pipelines, risers, and offshore platforms.
Biofouling and chloride monitoring systems detect salt-induced corrosion risks in offshore drilling and marine infrastructure.
High-pressure, high-temperature (HPHT) corrosion sensors assess metal integrity in deepwater oil and gas extraction.
Key Purchasing Considerations
Selecting the right corrosion and erosion monitoring solutions requires evaluating sensor precision, environmental resilience, system integration, and regulatory compliance. The following factors should guide decision-making:
Measurement Accuracy & Sensor Sensitivity:
Electrochemical and electrical resistance (ER) corrosion sensors provide real-time corrosion rate data with high sensitivity.
High-resolution ultrasonic thickness gauges ensure precise wall thickness measurements for early erosion detection.
Acoustic and optical-based erosion monitors improve reliability in high-velocity gas and liquid applications.
Environmental Durability & Sensor Longevity:
Corrosion-resistant, explosion-proof sensors extend lifespan in offshore, high-pressure, and high-temperature environments.
Subsea-rated corrosion probes with waterproof enclosures ensure durability in deepwater applications.
Self-cleaning biofouling-resistant coatings improve sensor reliability in marine and coastal infrastructure.
Integration with SCADA & Predictive Maintenance Systems:
Corrosion monitoring systems with HART, Modbus, and wireless IoT connectivity ensure seamless integration into SCADA and asset management platforms.
Predictive analytics and AI-driven diagnostics enable proactive maintenance and reduce unplanned downtime.
Remote monitoring platforms with real-time alerts improve pipeline and facility integrity tracking.
Compliance with Industry Standards & Safety Regulations:
Ensure compliance with API 570 (Piping Inspection), API 510 (Pressure Vessel Inspection), and API 653 (Storage Tank Inspection) standards.
Pipeline corrosion monitoring systems must adhere to NACE SP0169 and PHMSA corrosion prevention guidelines.
Cathodic protection monitoring must comply with DOT 49 CFR Part 192/195 regulations for hazardous liquid and gas pipelines.
Reliability & Maintenance Considerations:
Self-calibrating corrosion sensors with drift compensation reduce maintenance costs and enhance long-term accuracy.
Automated data logging with remote access capabilities ensures continuous monitoring without frequent site visits.
SCADA-integrated predictive maintenance systems detect early-stage pipeline degradation, preventing costly failures.
Remote Monitoring & SCADA
Remote monitoring systems and Supervisory Control and Data Acquisition (SCADA) play a critical role in oil and gas pipeline operations by providing real-time data acquisition, process automation, and remote control capabilities. These systems enable operators to monitor flow rates, pressure, temperature, leak detection, and pipeline integrity across vast geographic areas, ensuring efficiency, safety, and regulatory compliance. SCADA-integrated IoT sensors, AI-driven analytics, and cloud-based dashboards help detect anomalies, automate emergency response, and optimize maintenance schedules. By leveraging real-time data visualization, predictive diagnostics, and remote accessibility, oil and gas companies can enhance operational reliability, minimize unplanned downtime, and improve overall pipeline performance.
Remote Monitoring & SCADA Applications for Pipeline Operations
SCADA and remote monitoring technologies support critical pipeline management functions, allowing for automated control, enhanced safety, and operational efficiency. Key applications include:
Real-Time Pipeline Performance Monitoring & Control:
SCADA-integrated flow meters, pressure transmitters, and temperature sensors provide continuous, real-time tracking of pipeline conditions.
Remote-controlled valve automation ensures precise pressure regulation, leak mitigation, and emergency shutdown (ESD) activation.
Automated alerts and trend analysis dashboards help operators predict flow disruptions and potential failures.
IoT-Enabled Predictive Maintenance & Anomaly Detection:
Machine learning and AI-driven predictive analytics analyze pipeline sensor data to detect early warning signs of equipment failure.
Smart vibration and acoustic sensors monitor for pipeline stress, corrosion, and mechanical integrity issues.
Digital twin modeling and simulation enable real-time pipeline condition assessment for proactive maintenance.
Leak Detection & Environmental Compliance Automation:
SCADA-integrated fiber optic sensing (DAS & DTS) detects temperature and pressure anomalies indicating leaks or unauthorized pipeline activity.
Automated mass balance and transient model analysis provide rapid leak detection with instant remote alerts.
SCADA-connected compliance reporting tools ensure adherence to PHMSA, API, and EPA pipeline safety regulations.
Remote Surveillance & Asset Protection for Critical Infrastructure:
Satellite, cellular, and radio telemetry enable pipeline monitoring in remote and offshore locations.
Surveillance drones and AI-enhanced imaging analytics provide real-time pipeline inspections and security monitoring.
GPS-based tracking of pipeline assets and maintenance crews improves operational coordination and safety compliance.
Key Purchasing Considerations
Selecting the right SCADA and remote monitoring solutions requires evaluating scalability, integration capabilities, cybersecurity, and regulatory compliance. The following factors should guide decision-making:
System Scalability & Integration Capabilities:
SCADA systems must support multi-site integration, allowing centralized control of onshore, offshore, and cross-border pipelines.
Compatibility with Modbus, DNP3, HART, and OPC protocols ensures seamless connectivity with existing industrial automation systems.
IoT-enabled wireless sensors and cloud-based SCADA provide remote access and monitoring without requiring on-site infrastructure expansion
.
Cybersecurity & Data Protection:
Advanced encryption, multi-factor authentication (MFA), and firewall protection ensure SCADA system security.
AI-driven cybersecurity analytics detect and prevent anomalous network activity and cyber threats targeting industrial control systems (ICS).
Compliance with NIST, ISA/IEC 62443, and TSA pipeline cybersecurity guidelines safeguards pipeline operations.
Reliability & Real-Time Data Processing:
Redundant data logging and real-time failover solutions prevent system downtime.
Edge computing capabilities in remote monitoring units (RTUs) improve response time and reduce data transmission latency.
AI-powered anomaly detection and predictive analytics enhance decision-making and proactive maintenance strategies.
Compliance with Industry Standards & Regulatory Requirements:
Ensure SCADA and remote monitoring solutions align with PHMSA (49 CFR Part 195), API 1165 (SCADA Display Design), and API 1164 (Cybersecurity for Pipeline SCADA Systems).
Pipeline integrity monitoring solutions must meet DOT, BSEE, and EPA regulatory compliance.
Automated compliance reporting and real-time audit tracking streamline adherence to environmental and safety mandates.
Operational Efficiency & Maintenance Considerations:
Self-diagnostic remote terminal units (RTUs) and programmable logic controllers (PLCs) minimize manual maintenance.
SCADA-based automated work order systems optimize maintenance scheduling and crew dispatching.
Cloud-integrated SCADA dashboards enhance cross-departmental collaboration and decision-making.
Selecting the right corrosion and erosion monitoring solutions requires evaluating sensor precision, environmental resilience, system integration, and regulatory compliance. The following factors should guide decision-making:
Measurement Accuracy & Sensor Sensitivity:
Electrochemical and electrical resistance (ER) corrosion sensors provide real-time corrosion rate data with high sensitivity.
High-resolution ultrasonic thickness gauges ensure precise wall thickness measurements for early erosion detection.
Acoustic and optical-based erosion monitors improve reliability in high-velocity gas and liquid applications.
Environmental Durability & Sensor Longevity:
Corrosion-resistant, explosion-proof sensors extend lifespan in offshore, high-pressure, and high-temperature environments.
Subsea-rated corrosion probes with waterproof enclosures ensure durability in deepwater applications.
Self-cleaning biofouling-resistant coatings improve sensor reliability in marine and coastal infrastructure.
Integration with SCADA & Predictive Maintenance Systems:
Corrosion monitoring systems with HART, Modbus, and wireless IoT connectivity ensure seamless integration into SCADA and asset management platforms.
Predictive analytics and AI-driven diagnostics enable proactive maintenance and reduce unplanned downtime.
Remote monitoring platforms with real-time alerts improve pipeline and facility integrity tracking.
Compliance with Industry Standards & Safety Regulations:
Ensure compliance with API 570 (Piping Inspection), API 510 (Pressure Vessel Inspection), and API 653 (Storage Tank Inspection) standards.
Pipeline corrosion monitoring systems must adhere to NACE SP0169 and PHMSA corrosion prevention guidelines.
Cathodic protection monitoring must comply with DOT 49 CFR Part 192/195 regulations for hazardous liquid and gas pipelines.
Reliability & Maintenance Considerations:
Self-calibrating corrosion sensors with drift compensation reduce maintenance costs and enhance long-term accuracy.
Automated data logging with remote access capabilities ensures continuous monitoring without frequent site visits.
SCADA-integrated predictive maintenance systems detect early-stage pipeline degradation, preventing costly failures.
Industry Standards & Regulatory Compliance
Ensuring pipeline safety, environmental protection, and regulatory compliance is critical in oil and gas transportation. Pipelines must adhere to strict federal, state, and international regulations to prevent leaks, emissions, and structural failures that could cause environmental damage, safety hazards, and financial penalties. Regulatory bodies such as PHMSA (Pipeline and Hazardous Materials Safety Administration), API (American Petroleum Institute), and the EPA (Environmental Protection Agency) establish guidelines for pipeline integrity management, leak detection, emissions monitoring, and emergency response planning. Adopting advanced instrumentation, SCADA-integrated monitoring systems, and predictive maintenance strategies ensures that oil and gas operators meet these compliance requirements while optimizing pipeline efficiency and operational reliability.
PHMSA, API, & EPA Regulations for Pipeline Safety
Oil and gas pipelines must comply with industry safety and performance standards to maintain structural integrity, prevent leaks, and reduce environmental risks. Key regulatory requirements include:
PHMSA Pipeline Safety Standards (49 CFR Parts 192 & 195):
49 CFR Part 192 establishes safety standards for natural gas pipelines, including pressure testing, corrosion control, and leak detection.
49 CFR Part 195 applies to hazardous liquid pipelines, requiring inline inspection (ILI), integrity management programs (IMP), and emergency response planning.
PHMSA’s Integrity Management Program (IMP) mandates continuous risk assessment, preventative maintenance, and pipeline integrity verification.
API Standards for Pipeline Design & Operation:
API 1160: Pipeline Integrity Management for Hazardous Liquid Pipelines.
API 1165: Recommended Practice for SCADA Display Systems.
API 1175: Leak Detection Program Management for pipelines, ensuring proactive leak prevention, real-time detection, and rapid response strategies.
API 570 & API 510: Inspection requirements for piping and pressure vessels to prevent corrosion and material degradation.
EPA Clean Air Act (CAA) & Clean Water Act (CWA) Compliance:
Leak detection and repair (LDAR) requirements for controlling VOC and methane emissions in pipeline compressor stations and gas processing facilities.
Spill Prevention, Control, and Countermeasure (SPCC) plans require pipeline operators to implement containment and mitigation measures for hazardous liquid spills.
National Pollutant Discharge Elimination System (NPDES) permits regulate stormwater runoff from pipeline construction sites to protect water quality.
Leak Prevention & Environmental Compliance in Oil & Gas
Pipeline operators must implement comprehensive leak prevention and environmental compliance strategies to reduce risks associated with hazardous liquid and gas transportation.
Key compliance measures include:
Advanced Leak Detection & Monitoring Technologies:
Mass balance and real-time transient model (RTTM) monitoring detect discrepancies in flow rate and pressure, identifying potential leaks.
SCADA-integrated fiber optic sensing (DTS & DAS) detects pressure changes, temperature fluctuations, and acoustic signals associated with leaks.
Automated emergency shutdown (ESD) systems trigger immediate isolation of affected pipeline sections, preventing further environmental damage.
Corrosion & Erosion Control for Long-Term Pipeline Integrity:
Cathodic protection (CP) monitoring ensures compliance with DOT 49 CFR 192 & 195 corrosion control regulations.
Internal corrosion monitoring using inline inspection (ILI) pigs helps operators detect material degradation and wall thinning.
Protective coatings, chemical inhibitors, and environmental exposure monitoring minimize the risk of pipeline material degradation.
Emission Control & Air Quality Compliance in Pipeline Operations:
Continuous Emission Monitoring Systems (CEMS) track methane, VOCs, and CO₂ emissions in compliance with EPA Greenhouse Gas Reporting Program (GHGRP) standards.
Flare gas recovery and vapor control systems prevent excessive emissions from compressor stations and storage facilities.
Compliance with EPA’s New Source Performance Standards (NSPS) for volatile organic compounds (VOC) and hazardous air pollutants (HAPs).
Spill Containment & Environmental Response Planning:
Automated containment systems with real-time leak detection alerts help reduce environmental impact in case of a pipeline breach.
Pipeline operators must comply with PHMSA spill response plans and maintain emergency preparedness in high-risk areas.
Groundwater and soil monitoring sensors ensure compliance with EPA hazardous waste and remediation requirements.
Benefits of Working With Clipper Controls
Case Studies & Success Stories
Explore how Clipper Controls has helped pipeline operators enhance safety, improve leak detection, and ensure regulatory compliance.
Click here to read our oil & gas pipeline case studies.
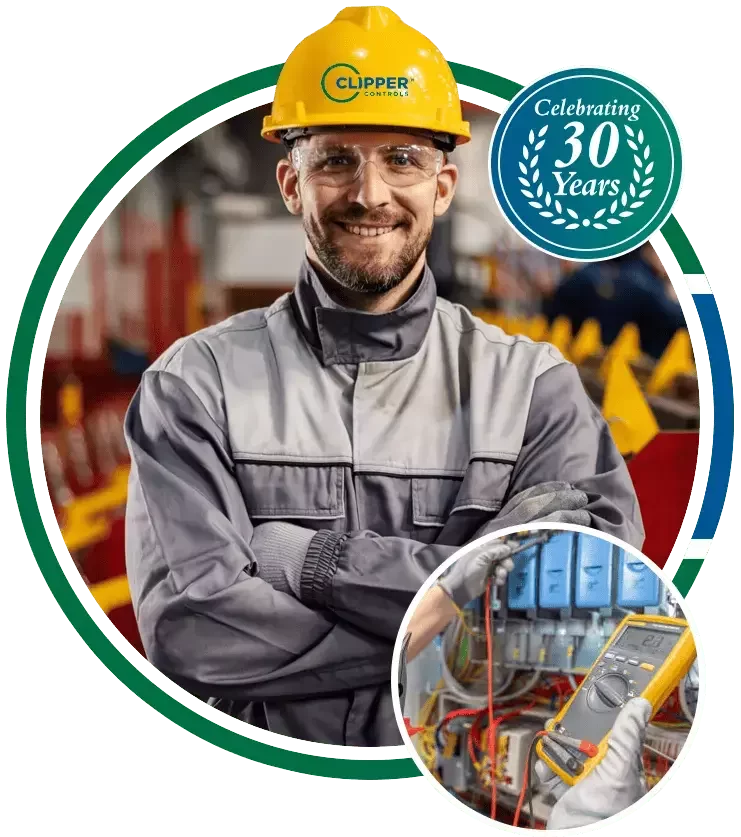
Real Results, Real Impact:
Thanks to Clipper Controls, our wastewater treatment plant improved efficiency & compliance with top-tier flow meters. Reliable solutions, great support! We recommend Clipper Controls to all our partner companies.
~ John Smith, Controls Engineer @ ABC Company
Clipper Controls helped our city upgrade water monitoring systems, ensuring accuracy & compliance. Reliable solutions & excellent customer service!
~ Nancy Patel, Procurement @ ABC Company
~ John Smith, Controls Engineer @ ABC Company
Ready to Work With Us?
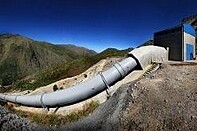
Quick Page Navigation:
🔹How Our Products Support Your Industry
Pressure Measurement & Control
Temperature Measurement & Control
Gas Composition Analysis
Leak Detection & Pipeline Integrity Monitoring
Corrosion Monitoring & Erosion Monitoring
🔹Industry Standards & Regulatory Compliance
🔹Benefits of Working With Clipper Controls