Theme Parks & Ride Safety Process Control Applications
Application Overview
How Our Products Support Your Industry
Key Applications and Solutions
Flow Measurement & Control
Flow Measurement & Control Applications in Theme Park Operations
Flow monitoring technology plays a crucial role in amusement rides, pools, fountains, and HVAC systems, ensuring smooth operation, water conservation, and safety compliance. Key applications include:
Hydraulic and Pneumatic Ride Systems:
Turbine and electromagnetic flow meters regulate hydraulic fluid circulation in roller coasters, drop towers, and motion simulators, ensuring smooth and safe ride operation.
Thermal mass flow meters measure airflow in compressed air-powered attractions, preventing pressure imbalances and maintaining ride integrity.
Flow controllers and automated valves adjust fluid distribution in hydraulic braking and launch systems, ensuring consistent ride performance.
Water Attractions and Pool Systems:
Ultrasonic and electromagnetic flow meters measure water circulation in wave pools, lazy rivers, and splash pads, ensuring proper water movement and guest safety.
Vortex flow meters regulate water flow in water slides and flume rides, preventing excessive velocity that could impact rider safety.
Smart flow monitoring systems optimize pump operations in fountains, artificial rivers, and play areas, reducing energy consumption while maintaining ideal flow rates.
Cooling Systems and Facility Water Management:
Coriolis and differential pressure flow meters control coolant distribution in ride motor cooling systems, preventing overheating and mechanical failures.
Flow sensors in HVAC systems help maintain efficient chilled water circulation, ensuring proper climate control for indoor attractions and guest areas.
Flow measurement in irrigation and landscape water features ensures sustainable water use, preventing waste in decorative fountains and park greenery.
Water Treatment and Filtration Processes:
Totalizer flow meters track water usage in filtration and chemical treatment systems for pools and water attractions, ensuring compliance with health and safety standards.
Automated dosing systems with integrated flow control regulate chlorine, bromine, and UV disinfection in pools and water features.
Flow-based chemical analyzers ensure proper pH and turbidity control, maintaining water clarity and safety for guests.
Key Purchasing Considerations
Selecting the right flow measurement and control instrumentation for theme park applications requires evaluating fluid properties, environmental conditions, and system integration needs. The following factors should guide decision-making:
Accuracy & Reliability:
High-precision electromagnetic and ultrasonic flow meters ensure accurate water flow measurement in pools, wave machines, and fountains.
Vortex and turbine meters provide consistent performance in high-velocity water attractions like water slides and lazy rivers.
Environmental Durability & Safety:
Corrosion-resistant materials (stainless steel, PVC, or epoxy-coated components) are essential for chlorinated and treated water applications.
IP-rated and submersible flow meters should be used in outdoor or submerged installations to withstand weather and water exposure.
Integration with Automated Control Systems:
Flow meters with HART, Modbus, or Profibus communication protocols enable seamless integration with SCADA, PLC, and ride control systems.
Wireless flow sensors provide real-time remote monitoring and data logging for facility-wide water usage tracking.
Energy Efficiency & Cost Savings:
Smart flow control systems optimize pump and valve operation, reducing energy consumption in HVAC, cooling, and water circulation systems.
Automated flow monitoring solutions help detect leaks and inefficiencies, preventing unnecessary water loss and operational downtime.
Pressure Monitoring & Regulation
Pressure Monitoring & Regulation Applications for Ride Safety and Performance
Proper pressure measurement and regulation in theme park attractions is crucial for ensuring guest safety, ride performance, and operational efficiency. Key applications include:
Hydraulic Systems in Amusement Rides:
Pressure transmitters and regulators monitor hydraulic fluid pressure in roller coasters, drop towers, and free-fall rides, ensuring smooth acceleration and braking.
Differential pressure sensors optimize hydraulic force distribution in launch mechanisms, preventing ride misalignment or excessive wear on components.
Automated pressure control valves regulate hydraulic actuators in themed animatronics, mechanical show elements, and motion platforms, ensuring precise movement and synchronization.
Pneumatic Systems for Ride Operation & Safety:
Air pressure sensors ensure proper operation of pneumatic launch and braking systems in high-speed rides.
Compressed air pressure regulators maintain consistent airflow for safety harness locking mechanisms, ensuring proper restraint engagement for riders.
Leak detection sensors identify air pressure drops in pneumatic rides, preventing sudden ride malfunctions or operational delays.
Water Attractions & Fluid Pressure Control:
Pressure transmitters monitor water flow in wave pools, lazy rivers, and water slides, ensuring proper pressure levels for optimal ride experience.
Pump pressure sensors regulate filtration and chemical dosing systems in pools and aquatic attractions, ensuring clean, safe water conditions.
Surge tank pressure monitors prevent sudden water pressure fluctuations in wave pools, ensuring smooth wave generation.
Compressed Air & HVAC Systems:
Differential pressure sensors regulate airflow in HVAC and ventilation systems, ensuring comfortable temperature control in indoor attractions.
Gas pressure regulators and safety valves monitor and control compressed air for animatronics, ride control panels, and pneumatic braking systems.
Environmental pressure monitoring ensures compliance with safety regulations in enclosed attractions, tunnels, and simulation rides.
Key Purchasing Considerations
Choosing the right pressure monitoring and regulation instrumentation for theme park applications requires evaluating system requirements, environmental factors, and compliance considerations. The following factors should guide decision-making:
Accuracy & Response Time:
High-precision pressure transmitters with rapid response times are essential for hydraulic braking systems and pneumatic ride launches.
Real-time digital pressure monitoring provides instant alerts on pressure fluctuations, reducing safety risks and operational downtime.
Material Durability & Environmental Conditions:
Corrosion-resistant, IP-rated pressure sensors are necessary for water attractions, chemical treatment systems, and humid environments.
Explosion-proof and intrinsically safe pressure transmitters are required for high-pressure air systems and enclosed ride environments.
Integration with Ride Control Systems:
Pressure sensors with HART, Modbus, or Profibus protocols ensure seamless SCADA and PLC system integration for ride automation.
Wireless pressure monitoring solutions provide remote alerts and data logging, improving predictive maintenance strategies.
Safety & Regulatory Compliance:
Ensure compliance with ASTM F2291 (Standard Practice for Amusement Ride Safety) and OSHA regulations for pressure systems.
Select pressure control devices with fail-safe mechanisms, preventing over-pressurization in hydraulic and pneumatic systems.
Maintenance & Lifecycle Costs:
Self-diagnosing pressure sensors reduce maintenance needs and provide predictive failure alerts.
Non-intrusive pressure sensors minimize downtime during installation and calibration, ensuring seamless integration into existing systems.
Temperature Sensing & Control
Precise temperature sensing and control are essential in theme park operations to ensure guest safety, ride performance, and equipment longevity. Mechanical, electrical, and fluid systems in amusement rides generate heat due to friction, electrical currents, and hydraulic operations, requiring continuous temperature monitoring to prevent overheating, reduce equipment wear, and optimize performance. Additionally, water attractions, HVAC systems, and food storage facilities rely on accurate temperature regulation to maintain environmental comfort, water quality, and health standards. Advanced RTDs, thermocouples, infrared sensors, and automated control systems provide real-time monitoring, enabling predictive maintenance, automated safety shutdowns, and energy efficiency improvements.
Temperature Sensing & Control Applications for Ride and Facility Safety
Temperature monitoring is crucial for preventing mechanical failures, optimizing energy consumption, and maintaining safe environmental conditions in theme parks. Key applications include:
Ride Mechanical Systems & Motor Cooling:
Thermocouples and RTDs monitor hydraulic fluid and gearbox temperatures in roller coasters, motion simulators, and animatronics to prevent overheating.
Infrared temperature sensors track heat buildup in bearings, motors, and braking systems, ensuring proper cooling and preventing ride failures.
Temperature-regulated cooling systems optimize electrical panel and control cabinet performance, preventing overheating of safety-critical systems.
Water Attractions & Pool Temperature Control:
Digital temperature controllers maintain optimal water temperatures in wave pools, lazy rivers, and spa areas, ensuring guest comfort and compliance with health regulations.
Inline temperature sensors regulate heat in hydrotherapy pools, geysers, and heated play structures, preventing excessive temperature fluctuations.
Smart control systems integrate with filtration and disinfection processes, optimizing energy efficiency in chlorination and UV water treatment.
HVAC & Climate Control in Indoor Attractions:
Smart temperature sensors adjust HVAC systems in indoor rides, themed attractions, and entertainment venues, ensuring guest comfort while reducing energy costs.
Duct-mounted temperature probes optimize air circulation and prevent humidity buildup in tunnels, theaters, and enclosed ride systems.
Ambient temperature sensors help regulate conditions in interactive experiences, simulation rides, and enclosed queue areas, ensuring a comfortable environment.
Food & Beverage Storage & Safety:
Temperature probes in refrigeration systems ensure proper cooling of perishable food and beverage storage, complying with FDA and HACCP regulations.
Wireless temperature monitoring systems track temperature fluctuations in concession stands, restaurants, and cold storage units, preventing spoilage and foodborne illness.
High-precision RTDs and thermocouples regulate temperature in food preparation equipment, ensuring consistent cooking and safe food handling.
Fire Safety & Emergency Monitoring:
Heat sensors in ride enclosures and tunnels provide early detection of abnormal temperature rises, preventing fire risks.
Infrared temperature scanners monitor electrical panels, transformers, and control rooms to detect overheating and potential fire hazards.
Smart temperature monitoring with automated alarms integrates into fire suppression and emergency ventilation systems for real-time safety response.
Key Purchasing Considerations
Selecting the right temperature sensing and control solutions for theme park applications requires evaluating system compatibility, environmental durability, and response accuracy. The following factors should guide decision-making:
Accuracy & Response Time:
High-accuracy RTDs and thermocouples are essential for motor cooling, hydraulic system monitoring, and electronic equipment protection.
Infrared temperature sensors with fast response times provide real-time heat detection in ride components and electrical systems.
Environmental & Installation Conditions:
Waterproof and corrosion-resistant temperature sensors are necessary for water attractions, pools, and misting systems.
High-temperature sensors are required for braking systems, motors, and heat-intensive environments.
Integration with Control & Safety Systems:
SCADA-compatible temperature sensors enable real-time monitoring and data logging, ensuring compliance with ride safety regulations.
Wireless and IoT-enabled temperature monitoring allows for remote alerts and predictive maintenance.
Regulatory Compliance & Safety Standards:
Temperature control solutions should comply with OSHA, ASTM, and FDA food safety regulations, depending on their application.
Sensors with automated alerts and fail-safe features ensure safety in ride operation, HVAC systems, and fire prevention protocols.
Maintenance & Lifecycle Costs:
Non-contact infrared sensors reduce maintenance needs in high-wear mechanical components.
Self-diagnosing temperature sensors improve reliability by detecting calibration drift and sending alerts before failures occur.
Level Detection & Management
Effective level detection and management are critical in theme park operations to ensure the safe and efficient operation of water attractions, ride hydraulics, storage tanks, and facility infrastructure. From wave pools and reservoirs to cooling systems and wastewater management, maintaining precise liquid levels prevents overflows, equipment damage, and operational disruptions. Advanced radar, ultrasonic, capacitive, and hydrostatic level sensors help park operators monitor and automate fluid control, ensuring compliance with safety and environmental regulations while enhancing efficiency and water conservation.
Level Detection & Management Applications in Theme Park Attractions
Reliable level monitoring technology is essential in amusement rides, water attractions, and facility operations, where fluid levels must be carefully controlled for safety, efficiency, and compliance. Key applications include:
Water Attractions & Pool Systems:
Ultrasonic and radar level sensors monitor water levels in wave pools, lazy rivers, and splash pads, ensuring safe operation and preventing overflow or dry running.
Float switches and hydrostatic level transmitters regulate water levels in wave generation tanks, maintaining the right water volume for wave production.
Automated level controllers ensure optimal water balance in water play structures and spray fountains, preventing system malfunctions.
Hydraulic & Pneumatic Ride Systems:
Capacitive and guided wave radar sensors detect fluid levels in hydraulic reservoirs, ensuring adequate oil supply for roller coasters, drop towers, and animatronics.
Differential pressure sensors monitor hydraulic fluid in braking and launch systems, preventing mechanical failures due to low oil levels.
Leak detection systems with integrated level monitoring help prevent hydraulic fluid loss, reducing maintenance and downtime.
Water Storage & Irrigation Tanks:
Non-contact radar sensors measure water levels in reservoirs and storage tanks, ensuring proper water supply for landscaping, cooling systems, and guest amenities.
Float-based level monitoring in irrigation tanks ensures efficient water distribution to maintain park aesthetics while reducing waste.
SCADA-integrated level sensors provide real-time monitoring of water usage and storage, optimizing water conservation efforts.
Cooling & HVAC System Management:
Level monitoring in cooling towers prevents low water conditions, protecting ride components and facility climate control systems.
Capacitive level sensors regulate glycol and coolant fluid levels in air conditioning systems for indoor attractions, ensuring continuous operation.
Automated condensate level control in HVAC units prevents overflow and system failure in enclosed spaces like theaters, tunnels, and dark rides.
Wastewater & Drainage Systems:
Float switches and conductivity sensors monitor wastewater collection tanks, ensuring proper disposal and compliance with environmental regulations.
Level sensors in stormwater management systems prevent flooding in low-lying park areas, tunnels, and underground ride systems.
Automated level alarms provide alerts for rapid response to unexpected drainage issues, improving park safety and operational continuity.
Key Purchasing Considerations
Selecting the right level detection and management solutions for theme park applications requires careful evaluation of process conditions, system requirements, and compliance factors. The following considerations should guide decision-making:
Accuracy & Reliability:
Radar and ultrasonic level sensors provide precise, non-contact measurement for water attractions, storage tanks, and wastewater management.
Hydrostatic and pressure-based level transmitters offer stable readings in high-pressure hydraulic systems and cooling applications.
Environmental & Fluid Compatibility:
Corrosion-resistant level sensors (made of stainless steel or PTFE coatings) are required for chlorinated water, cooling systems, and hydraulic fluid applications.
Sensors with IP-rated waterproof enclosures should be used in wave pools, fountains, and open-air attractions exposed to humidity and weather conditions.
Integration with Park Automation Systems:
SCADA-compatible level sensors with HART, Modbus, or Profibus communication enable real-time monitoring and remote control.
Wireless level monitoring solutions allow operators to track tank levels, detect leaks, and automate filling processes from a central control room.
Safety & Compliance Standards:
Ensure sensors comply with ASTM and OSHA safety regulations for ride hydraulic systems and water storage.
Level detection systems in wastewater treatment and chemical storage must meet EPA and environmental safety requirements.
Maintenance & Longevity:
Self-cleaning and non-contact level sensors reduce maintenance needs in high-contaminant environments like wastewater tanks and water parks.
Fail-safe level monitoring with automatic alarms ensures rapid response to fluid level abnormalities in critical systems.
Vibration & Structural Monitoring
Ensuring the structural integrity and mechanical reliability of amusement rides is essential for guest safety, regulatory compliance, and operational efficiency. Over time, continuous stress, environmental conditions, and ride operation cycles can lead to wear, fatigue, and mechanical degradation in structural components, motors, and track systems. Advanced vibration and structural health monitoring (SHM) systems utilize accelerometers, strain gauges, displacement sensors, and real-time data analytics to detect abnormal vibrations, excessive stress loads, and material fatigue before they become critical failures. SCADA-integrated predictive maintenance solutions allow operators to monitor ride conditions remotely, automate inspections, and implement proactive maintenance schedules, reducing the risk of unexpected ride malfunctions and downtime.
Vibration & Structural Monitoring Applications for Ride Integrity
Structural health and vibration monitoring systems provide real-time diagnostics for amusement rides, ensuring early detection of mechanical stress, track misalignment, and component wear. Key applications include:
Roller Coasters & High-Speed Rides:
Accelerometers and vibration sensors detect track misalignment, wheel assembly wear, and excessive vibrations, preventing structural fatigue in steel and wooden coasters.
Displacement and tilt sensors monitor track expansion and contraction due to temperature fluctuations and operational stress, ensuring track alignment.
Load sensors in braking systems measure dynamic forces during deceleration, identifying wear in hydraulic and magnetic braking mechanisms.
Drop Towers & Motion-Based Attractions:
Strain gauges and load cells measure structural stress and force distribution in vertical drop rides, ensuring proper load balancing and frame integrity.
High-speed vibration sensors detect anomalies in motor-driven drop and launch systems, preventing failures due to excessive force loads.
Displacement monitoring systems track tower sway and structural bending, ensuring compliance with safety tolerances.
Simulators & Dark Rides:
Vibration sensors in motion platforms ensure smooth operation and detect excessive oscillations that could affect guest comfort and system durability.
Shock and impact sensors monitor sudden load changes in robotic and motion-based attractions, helping prevent excessive mechanical strain.
Structural monitoring systems detect early signs of fatigue in ride enclosures, suspended track sections, and moving scenery components.
Water Rides & Floating Track Systems:
Underwater vibration sensors track wave-induced stress on floating ride platforms, docks, and log flume tracks, preventing premature wear.
Corrosion-resistant strain gauges measure structural load distribution on fiberglass flume rides and splash-down attractions.
Tilt and displacement sensors ensure proper alignment of water slide support structures, preventing gradual shifting due to water erosion.
Bridges, Platforms & Themed Structures:
Structural health monitoring systems (SHM) detect material fatigue in suspended bridges, queue structures, and elevated guest areas.
Seismic and wind load sensors provide real-time feedback on extreme weather impact, ensuring rapid response and guest safety.
Remote monitoring systems integrate with SCADA platforms, enabling automated inspections of ride structures and foundations.
Key Purchasing Considerations
Selecting the right vibration and structural monitoring systems for amusement rides requires evaluating ride dynamics, material composition, and compliance factors. The following considerations should guide decision-making:
Sensor Accuracy & Sensitivity:
High-frequency accelerometers and vibration sensors are essential for detecting minor oscillations and mechanical imbalances in high-speed rides.
Load cells and strain gauges should have high precision to measure small deformations and stress concentrations in steel and wood structures.
Environmental Durability & Weather Resistance:
Waterproof and corrosion-resistant vibration sensors should be used for water rides, outdoor coasters, and high-humidity environments.
High-temperature sensors should be installed in braking systems and hydraulic motors, where excessive heat can cause mechanical failure.
Integration with Ride Control & Safety Systems:
SCADA-compatible monitoring systems with HART, Modbus, or Profibus communication enable real-time diagnostics and automated safety alerts.
Wireless vibration monitoring solutions allow for remote predictive maintenance, reducing downtime and manual inspections.
Regulatory Compliance & Ride Safety Standards:
Structural health monitoring solutions should meet ASTM F2291 (Standard Practice for Amusement Ride Design & Safety) and OSHA workplace safety regulations.
Vibration monitoring must comply with ISO 10816, ensuring ride components operate within safe vibration limits.
Maintenance & Lifecycle Costs:
Self-diagnosing vibration sensors help detect early-stage wear, reducing expensive ride overhauls.
Modular and scalable monitoring systems allow parks to expand structural monitoring coverage as attractions evolve.
Gas Detection & Environmental Monitoring
Gas Detection & Environmental Monitoring Applications for Safety
Real-time gas monitoring is essential for ensuring clean air, safe chemical usage, and environmental compliance in various theme park operations. Key applications include:
Indoor Attractions & Enclosed Ride Systems:
Fixed gas detectors continuously monitor CO₂ and oxygen (O₂) levels in dark rides, underground tunnels, and enclosed theaters, preventing air quality deterioration.
Carbon monoxide (CO) sensors ensure proper ventilation in parking garages, ride maintenance facilities, and generator rooms.
VOC analyzers detect airborne contaminants in indoor attractions with fog machines, special effects, and animatronics, protecting guests and staff from prolonged exposure.
Water Attractions & Chemical Monitoring:
Chlorine (Cl₂) and ozone (O₃) sensors ensure proper disinfection levels in wave pools, lazy rivers, and splash pads, preventing overexposure to chemicals.
Dissolved oxygen (DO) and pH analyzers monitor water quality in aquariums, artificial lakes, and interactive water features, ensuring compliance with EPA and health safety standards.
Ammonia (NH₃) and hydrogen sulfide (H₂S) sensors detect potential chemical leaks from water treatment and filtration systems, preventing hazardous conditions.
Boiler Rooms, Mechanical Facilities & Utility Areas:
Combustible gas detectors provide early warning of natural gas (methane) leaks in heating systems and fuel storage areas.
Nitrogen dioxide (NO₂) and CO sensors monitor exhaust emissions in boiler rooms, HVAC units, and backup power systems, preventing toxic air buildup.
Flame detection systems integrate with gas sensors to automate emergency shutoffs in engine rooms and mechanical spaces.
Kitchens, Food Courts & Refrigeration Units:
CO₂ and ammonia (NH₃) sensors monitor commercial refrigeration systems, ensuring safe storage of perishable food and preventing hazardous gas leaks.
Grease vapor and hydrocarbon sensors detect excessive airborne pollutants in food preparation areas and commercial kitchens, maintaining compliance with OSHA and FDA air quality guidelines.
Ventilation control systems with gas monitoring adjust airflow rates in enclosed dining areas, improving indoor air quality.
Weather & Environmental Monitoring:
Particulate matter (PM) sensors track air pollution levels, ensuring guest safety during high-smog or wildfire-prone conditions.
Weather stations with wind and lightning detection allow real-time monitoring for outdoor ride shutdown protocols, preventing weather-related incidents.
Air quality sensors in queue areas and outdoor attractions ensure proper dust and pollen monitoring, minimizing discomfort for guests with respiratory sensitivities.
Key Purchasing Considerations
Selecting the right gas detection and environmental monitoring systems for theme park applications requires evaluating safety risks, environmental conditions, and integration requirements. The following factors should guide decision-making:
Sensor Sensitivity & Accuracy:
Electrochemical gas sensors provide high-accuracy readings for toxic gases like CO, NO₂, and H₂S in confined spaces.
Infrared (IR) and catalytic bead sensors detect combustible gases such as methane (CH₄) and propane (C₃H₈) in fuel storage areas.
Photoionization detectors (PIDs) monitor VOCs in special effects areas, paint shops, and indoor ride environments.
Environmental Durability & Installation Conditions:
Waterproof, corrosion-resistant gas sensors are required for chlorine and ozone detection in water attractions.
Explosion-proof and intrinsically safe gas detectors are necessary for boiler rooms, kitchens, and fuel storage facilities.
Wireless and battery-operated gas sensors are ideal for remote locations, mobile food stands, and temporary event areas.
Integration with Control & Safety Systems:
SCADA-compatible gas detection systems with Modbus, HART, or BACnet connectivity enable seamless automation and data logging.
Multi-gas detectors with automated alarms integrate with fire suppression, ventilation, and ride shutdown protocols, ensuring rapid emergency response.
Cloud-based air quality monitoring systems provide real-time data access for facility-wide environmental tracking.
Compliance with Safety Standards & Regulations:
Ensure compliance with OSHA, EPA, NFPA, and ASTM safety regulations for gas exposure limits, emissions control, and chemical handling.
Select gas detection systems that meet NIOSH (National Institute for Occupational Safety and Health) exposure limits, ensuring worker safety.
Sensors should align with ASHRAE and IAQ (Indoor Air Quality) guidelines for theme park indoor environments.
Maintenance & Lifecycle Costs:
Self-calibrating gas detectors reduce maintenance frequency and ensure long-term accuracy.
Sensor redundancy and fail-safe designs provide added protection against system malfunctions and sensor drift.
Remote monitoring and diagnostic capabilities allow for early detection of sensor failures, reducing operational downtime.
Analytical Instrumentation for Water Quality & Compliance
Water quality is a critical factor in theme park operations, affecting guest safety, equipment longevity, and regulatory compliance. Attractions such as wave pools, lazy rivers, splash pads, and interactive fountains require constant monitoring to maintain proper chemical balance, prevent bacterial growth, and ensure clear water conditions. Advanced analytical instrumentation, including pH sensors, turbidity meters, chlorine analyzers, and dissolved oxygen sensors, allows operators to automate water treatment, optimize chemical dosing, and comply with health and safety standards such as those set by the EPA, CDC, and local water quality regulations.
Analytical Instrumentation Applications for Water Quality & Compliance
Water chemistry monitoring and treatment play a crucial role in maintaining safe, clear, and pathogen-free water across a variety of theme park attractions. Key applications include:
Wave Pools, Lazy Rivers, & Water Play Areas:
pH sensors and ORP (oxidation-reduction potential) meters ensure balanced water chemistry, preventing irritation to guests and prolonging the lifespan of pool surfaces.
Chlorine and bromine analyzers provide real-time monitoring of disinfectant levels, ensuring proper sanitization and compliance with public health standards.
Turbidity meters detect suspended particles, debris, and algae growth, ensuring optimal water clarity in high-traffic water attractions.
Splash Pads, Fountains, & Interactive Water Features:
Real-time chemical monitoring systems adjust chlorine and pH levels in zero-depth water play areas, preventing over- or under-dosing of sanitizing agents.
UV disinfection system controllers monitor UV intensity to optimize microbial control without excessive chemical use.
Flow-based dosing controllers regulate water circulation and chemical feed rates, maintaining uniform disinfection across distributed spray zones.
Aquariums & Artificial Lakes:
Dissolved oxygen (DO) sensors track oxygen levels to maintain healthy conditions for marine life in themed aquariums and ponds.
Ammonia and nitrate analyzers detect contamination from biological waste, preventing harmful water quality imbalances.
Conductivity sensors ensure the correct salinity levels in saltwater attractions, protecting aquatic exhibits.
Cooling & Water Filtration Systems:
Total organic carbon (TOC) analyzers help monitor organic contaminants in closed-loop cooling and HVAC water systems to prevent bacterial buildup.
Hardness analyzers measure mineral content in water treatment systems, ensuring scale prevention and proper chemical dosing.
Pressure and flow-based water quality sensors optimize backwashing cycles in filtration systems, reducing unnecessary water waste.
Wastewater & Drainage Treatment:
COD (chemical oxygen demand) and BOD (biochemical oxygen demand) analyzers monitor wastewater treatment efficiency, ensuring compliance with environmental discharge permits.
pH neutralization controllers regulate chemical balancing in wastewater and graywater reuse systems, minimizing environmental impact.
Automated data logging systems provide a historical record of water quality metrics, ensuring compliance with EPA discharge regulations.
Key Purchasing Considerations
Selecting the right analytical instrumentation for water quality monitoring requires evaluating chemical compatibility, environmental durability, and regulatory requirements. The following factors should guide decision-making:
Accuracy & Sensor Sensitivity:
High-precision pH, ORP, and chlorine analyzers are essential for splash pads, pools, and aquatic attractions where small variations in chemical balance can affect guest safety.
Low-range turbidity sensors provide early detection of water clarity issues, ensuring rapid response to changes in particle levels.
Dissolved oxygen sensors with fast response times are critical for aquatic exhibits and cooling water systems.
Durability & Environmental Suitability:
Corrosion-resistant sensors (titanium, stainless steel, or epoxy-coated) should be used in chlorinated and saltwater applications.
UV-resistant and submersible instrumentation is necessary for outdoor pools, fountains, and splash pad water features.
Self-cleaning probe designs prevent biofouling in high-organic load attractions such as lazy rivers and artificial lakes.
System Integration & Automation:
SCADA and PLC-compatible analytical instruments enable real-time remote monitoring and automated chemical dosing adjustments.
Wireless water quality sensors provide continuous tracking of pH, chlorine, and turbidity levels across multiple attractions.
Multi-parameter water quality analyzers reduce equipment footprint and maintenance by combining multiple measurement functions in one unit.
Regulatory Compliance & Safety Standards:
Ensure instrumentation meets EPA, NSF/ANSI Standard 50, and local health department regulations for theme park water treatment.
Automated reporting and data logging systems should comply with CDC Model Aquatic Health Code (MAHC) for public water attractions.
UV and ozone monitoring systems should meet safety standards for chemical-free disinfection alternatives.
Maintenance & Lifecycle Costs:
Sensors with automatic calibration and self-cleaning mechanisms minimize maintenance needs and reduce labor costs.
Long-life chlorine and pH probes ensure sustained performance with fewer replacement intervals.
Predictive maintenance features in modern analytical instruments provide early alerts to prevent sensor failures.
Industry Standards & Regulatory Compliance
Ensuring Compliance with ASTM, OSHA, and Local Safety Regulations
Theme park operations involve complex mechanical, hydraulic, pneumatic, and structural systems, all of which must meet established safety regulations. The following standards ensure safe ride operation, worker protection, and regulatory adherence:
ASTM F24 (Standard Practice for Amusement Ride Safety):
Governs structural integrity, ride controls, braking systems, and emergency procedures.
Requires vibration analysis, load monitoring, and stress testing for rides to detect material fatigue before failures occur.
Establishes guidelines for pressure regulation in hydraulic and pneumatic systems to prevent over-pressurization and mechanical failures.
OSHA (Occupational Safety and Health Administration) Compliance:
Mandates worker safety programs, including fall protection, confined space entry procedures, and hazardous gas exposure limits.
Requires gas detection systems in confined ride enclosures and mechanical maintenance areas to prevent CO, NO₂, and VOC exposure.
Ensures safe handling of compressed gases and hazardous chemicals used in water treatment and special effects.
Local & State Amusement Ride Safety Regulations:
Vary by jurisdiction but typically require routine inspections, maintenance logs, and accident reporting for all amusement rides.
Compliance often includes water quality testing, air quality monitoring, and environmental impact assessments.
Environmental & Water Quality Standards for Theme Parks
Theme parks rely heavily on water resources for attractions, landscaping, cooling systems, and sanitation. Compliance with environmental regulations ensures sustainable water use and prevents contamination. Key water quality and environmental standards include:
EPA (Environmental Protection Agency) Water Discharge & Reuse Regulations:
Requires monitoring of chemical levels in pools, wave machines, and water rides to prevent contamination.
Governs stormwater management and wastewater discharge, ensuring parks prevent pollutants from entering local waterways.
Mandates filtration and treatment systems to remove debris, bacteria, and chemical byproducts before water is reused or discharged.
CDC Model Aquatic Health Code (MAHC) for Public Water Attractions:
Establishes guidelines for pH balance, chlorine/bromine levels, turbidity, and bacterial contamination limits.
Requires continuous monitoring of chemical dosing systems to prevent over-chlorination or unsafe microbial conditions.
Ensures water treatment facilities maintain accurate records and real-time monitoring of water chemistry.
ASHRAE & IAQ (Indoor Air Quality) Standards for Enclosed Attractions:
Regulates HVAC ventilation rates in enclosed rides, queue areas, and theaters to maintain healthy air circulation.
Requires particulate and gas detection systems to prevent guest exposure to excess carbon dioxide, nitrogen dioxide, and VOCs from special effects.
By integrating advanced instrumentation, automation, and regulatory compliance tools, theme parks can enhance safety, minimize environmental impact, and ensure adherence to industry standards. Investing in real-time monitoring, automated reporting, and predictive maintenance allows operators to meet compliance requirements while improving operational efficiency and guest experience.
Benefits of Working With Clipper Controls
Clipper Controls provides advanced instrumentation and automation solutions to ensure ride safety, water quality, and environmental compliance in theme parks. Our flow meters, pressure sensors, gas detectors, and analytical instruments enable real-time monitoring, predictive maintenance, and automated control, helping parks minimize risks and optimize efficiency.
By partnering with Clipper Controls, theme parks gain access to high-precision monitoring systems that integrate seamlessly with SCADA, PLC, and IoT platforms. Our expert guidance, reliable instrumentation, and data-driven solutions help operators improve ride performance, maintain regulatory compliance, and enhance the guest experience while reducing downtime and operational costs.
Case Studies & Success Stories
Explore real-world examples of how Clipper Controls has helped theme parks enhance ride safety, water quality management, and environmental compliance.
Click here to read our theme park & ride safety case studies.
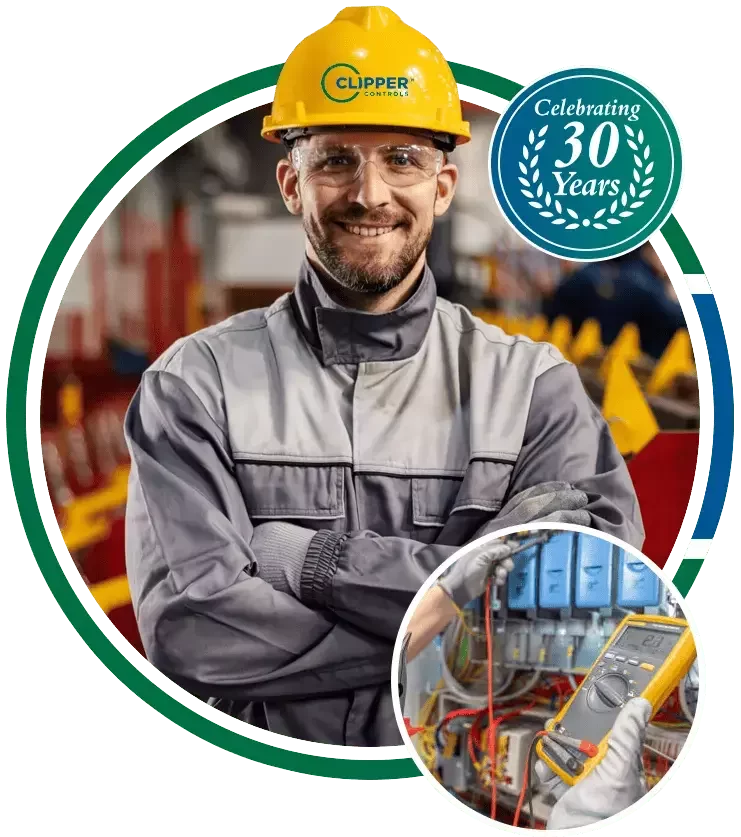
Real Results, Real Impact:
Thanks to Clipper Controls, our wastewater treatment plant improved efficiency & compliance with top-tier flow meters. Reliable solutions, great support! We recommend Clipper Controls to all our partner companies.
~ John Smith, Controls Engineer @ ABC Company
Clipper Controls helped our city upgrade water monitoring systems, ensuring accuracy & compliance. Reliable solutions & excellent customer service!
~ Nancy Patel, Procurement @ ABC Company
~ John Smith, Controls Engineer @ ABC Company
Ready to Work With Us?

Quick Page Navigation:
🔹How Our Products Support Your Industry
Pressure Monitoring & Regulation
Vibration & Structural Monitoring
Gas Detection & Environmental Monitoring
Analytical Instrumentation for Water Quality & Compliance
🔹Industry Standards & Regulatory Compliance
🔹Benefits of Working With Clipper Controls