Refining & Chemical Process Control Applications
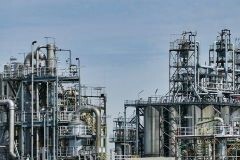
Application Overview
Refining and chemical processing facilities require precise instrumentation, control systems, and analyzers to ensure operational efficiency, safety, and regulatory compliance. Process variables such as pressure, temperature, flow, and level must be continuously monitored and adjusted to maintain optimal conditions in reactors, distillation columns, and heat exchangers. Advanced control strategies, including proportional-integral-derivative (PID) loops and model predictive control (MPC), help refine complex chemical processes while minimizing variability and energy consumption. Additionally, integrating real-time data from process analyzers enables operators to detect anomalies, optimize yield, and reduce waste, ensuring both economic and environmental objectives are met.
In these demanding environments, selecting the right instrumentation and analyzers is critical for maintaining process integrity and product quality. Corrosive chemicals, high temperatures, and variable pressure conditions require robust sensors and measurement devices that can withstand extreme conditions while delivering accurate, real-time data. Modern process control systems integrate smart sensors and Industrial Internet of Things (IIoT) technologies to enhance predictive maintenance and reduce unplanned downtime. By leveraging these advanced solutions, facilities can improve asset reliability, enhance operational agility, and meet the stringent demands of today’s refining and chemical processing industries.
How Our Products Support Your Industry
Clipper Controls supports the refining and chemical processing industry by providing high-quality instrumentation, control solutions, and analytical systems designed for precision, reliability, and durability in demanding environments. With a comprehensive range of measurement and control products, Clipper Controls helps engineers and plant operators monitor critical process variables such as pressure, temperature, flow, and level with confidence. The company offers cutting-edge solutions, including smart sensors, advanced control systems, and real-time process analyzers, ensuring accurate data collection and process optimization. These technologies help facilities maintain operational efficiency, improve safety, and comply with industry regulations while minimizing downtime and reducing maintenance costs.
Beyond providing instrumentation, Clipper Controls delivers expert guidance in selecting the right solutions for complex applications. With deep industry knowledge and technical expertise, the company assists in system design, integration, and ongoing support to enhance process performance. Whether implementing predictive maintenance strategies, optimizing control loops, or integrating IIoT-enabled technologies, Clipper Controls partners with customers to improve operational resilience and maximize productivity. By offering tailored solutions and ongoing technical support, Clipper Controls plays a vital role in helping refining and chemical processing facilities meet the challenges of modern industrial operations.
Key Applications and Solutions
Flow Measurement & Control
Flow measurement and control are fundamental to refining and chemical processing operations, where precise monitoring of liquids, gases, and slurries ensures safety, efficiency, and regulatory compliance. Process engineers rely on a range of flow measurement technologies, including Coriolis, magnetic, ultrasonic, thermal mass, vortex, and differential pressure (DP) flow meters, to optimize material usage, energy consumption, and process stability. In high-stakes environments where accuracy is critical, integrating smart sensors, multivariable transmitters, and industrial communication protocols (e.g., HART, Modbus, Profibus, and Ethernet/IP) ensures real-time data collection and process automation. Selecting the right instrumentation helps mitigate risks such as leaks, inefficiencies, and equipment failures, ultimately improving operational performance and profitability.
Applications of Flow Measurement & Control in Refining and Chemical Processing
- Crude Oil and Feedstock Handling: In refineries, crude oil must be measured and regulated before processing. Coriolis and ultrasonic flow meters provide highly accurate mass flow and volumetric measurements, ensuring precise allocation of feedstock into distillation units. Turbine and positive displacement meters are also used in custody transfer applications, where financial transactions depend on accurate flow readings.
- Distillation and Fractionation Control: Distillation columns separate hydrocarbons based on boiling points, requiring precise feed and reflux flow control. Magnetic and vortex flow meters are commonly used for liquid and steam flow measurement, maintaining process stability and maximizing product purity. Differential pressure flow meters, often paired with smart DP transmitters, help optimize vapor flow rates and column efficiency.
- Catalytic Cracking and Hydroprocessing: Flow control is essential in fluid catalytic cracking (FCC) and hydrocracking, where catalysts and reactants must be precisely metered to optimize chemical reactions. Coriolis meters provide accurate mass flow measurements for hydrocarbon feeds and hydrogen injection, improving conversion rates and process efficiency. Thermal mass flow meters are often used for hydrogen and gas-phase flow measurement in hydroprocessing units.
- Chemical Injection and Additive Dosing: Many refining and chemical processes require precise injection of catalysts, corrosion inhibitors, and other additives. Positive displacement and Coriolis flow meters are ideal for low-flow, high-accuracy dosing applications, ensuring consistent chemical ratios and preventing overdosing, which can lead to product defects or equipment damage.
- Steam and Utility Flow Management: Steam is used extensively for heating, stripping, and power generation. Vortex and DP flow meters measure steam flow in high-temperature environments, while ultrasonic and thermal mass flow meters monitor natural gas and compressed air usage, optimizing energy efficiency. Proper steam flow control also prevents water hammer and ensures safe operation of boilers and turbines.
- Wastewater and Effluent Flow Monitoring: Refineries and chemical plants must comply with environmental regulations governing wastewater discharge. Magnetic flow meters are widely used for wastewater flow measurement, as they handle conductive fluids and provide high accuracy. Open-channel ultrasonic flow meters measure effluent discharge in treatment systems, ensuring compliance with local and federal regulations.
Key Purchasing Considerations
- Fluid Properties: The type of flow meter selected depends on viscosity, density, conductivity, phase (liquid/gas), and chemical compatibility. Coriolis meters excel in mass flow applications, magnetic meters are ideal for conductive liquids, and ultrasonic meters provide non-intrusive measurement for both liquids and gases.
- Measurement Accuracy and Repeatability: High-precision applications, such as custody transfer, reactor feed control, and blending, require Coriolis and ultrasonic flow meters, which offer superior accuracy and repeatability. Less critical applications, such as steam monitoring and utility flow tracking, can use vortex or DP meters with acceptable precision levels.
- Operating Environment and Installation Constraints: Refining and chemical facilities often operate in extreme conditions with high temperatures, pressures, and corrosive environments. Orifice plates and DP meters withstand harsh conditions, while ceramic-lined magnetic meters resist chemical corrosion. Clamp-on ultrasonic meters offer a non-invasive solution for retrofitting flow measurement systems without process interruption.
- Maintenance and Lifecycle Costs: Coriolis and ultrasonic flow meters have no moving parts, reducing maintenance requirements and increasing long-term reliability. Turbine and positive displacement meters, while cost-effective, require regular calibration and servicing. Smart diagnostic capabilities in HART-enabled or FOUNDATION Fieldbus-compatible flow meters support predictive maintenance and minimize unplanned downtime.
- Integration with Control Systems: Flow meters must seamlessly integrate with DCS, SCADA, and PLC systems for process automation and data analytics. Digital communication protocols, such as HART, Modbus, Profibus, and Ethernet/IP, enable remote monitoring, diagnostics, and real-time adjustments, improving process efficiency and compliance tracking.
Pressure Monitoring & Regulation
Pressure monitoring and regulation are vital in refining and chemical processing, where stable pressure levels ensure safe and efficient operations. Many processes involve high temperatures, corrosive substances, and varying pressure conditions, making reliable pressure measurement critical for maintaining system integrity and preventing hazardous incidents. Pressure instrumentation, including gauge pressure sensors, differential pressure (DP) transmitters, absolute pressure transmitters, and mechanical pressure switches, provides real-time data to regulate operations and protect equipment. Integrated with distributed control systems (DCS) and programmable logic controllers (PLCs), advanced pressure monitoring solutions enhance automation, predictive maintenance, and compliance with safety regulations.
Applications of Pressure Monitoring & Regulation in Refining and Chemical Processing
- Reactor Pressure Control: Maintaining precise pressure in reactors is crucial for optimizing reaction kinetics and preventing dangerous overpressure conditions. Absolute pressure transmitters are used to measure total system pressure, while differential pressure transmitters monitor pressure drops across catalyst beds or filters, ensuring optimal reaction performance.
- Distillation Column Pressure Control: Proper pressure regulation in distillation columns impacts separation efficiency and energy consumption. Gauge pressure transmitters help maintain stable overhead pressure, ensuring proper boiling points and preventing product loss. DP transmitters are used to monitor pressure differences between column trays, helping operators optimize reflux ratios and improve separation quality.
- Boiler and Steam System Pressure Monitoring: In refineries and chemical plants, steam is used for process heating, stripping, and power generation. Bourdon tube pressure gauges provide local pressure readings, while high-accuracy pressure transmitters feed real-time data to control loops that regulate steam flow and boiler performance. Overpressure protection is ensured by pressure relief valves (PRVs) and safety shutdown systems.
- Compressor and Pump Monitoring: Compressors and pumps are critical for moving gases and liquids through refining and chemical processes. Pressure sensors and switches detect abnormal pressure levels, triggering alarms or shutdowns to prevent equipment damage. Vibration and pressure monitoring systems enhance predictive maintenance, reducing downtime and repair costs.
- Pipeline and Flow Control Pressure Regulation: Pipelines transporting crude oil, natural gas, and chemicals require continuous pressure monitoring to prevent leaks, ruptures, and pressure fluctuations. Smart pressure transmitters integrated with remote telemetry units (RTUs) allow operators to monitor pipeline pressures in real time and adjust flow control valves as needed. Differential pressure flow meters are also used to regulate fluid velocity and ensure consistent throughput.
- Tank Level and Vapor Space Pressure Control: Storage tanks for crude oil, refined products, and chemicals require pressure monitoring to prevent over-pressurization or vacuum conditions. Hydrostatic pressure sensors measure liquid levels, while pressure relief valves and vacuum breakers maintain safe operating conditions. In volatile applications, intrinsically safe pressure transmitters ensure compliance with explosion-proof safety standards.
Key Purchasing Considerations
- Pressure Range and Accuracy: The required measurement range should align with process operating conditions. Absolute and gauge pressure transmitters provide highly accurate readings for high-pressure applications, while low-range DP transmitters are used for sensitive pressure measurements such as filter monitoring.
- Material Compatibility and Corrosion Resistance: Process fluids may be corrosive, abrasive, or high-temperature, requiring robust materials like stainless steel, Hastelloy, or ceramic-coated diaphragms for pressure sensors. Sealed and isolated pressure transmitters protect against chemical exposure, ensuring long-term performance in harsh environments.
- Safety and Compliance Standards: Pressure measurement devices must comply with industry regulations such as ASME, API, IECEx, ATEX, and SIL (Safety Integrity Level) standards for hazardous environments. Intrinsically safe pressure transmitters and explosion-proof housings are necessary in volatile applications such as hydrogen or hydrocarbon processing.
- Response Time and Stability: Fast response times are crucial in applications where sudden pressure changes occur, such as compressor discharge and steam regulation. Digital pressure transmitters with smart diagnostics improve response time and provide self-calibration capabilities, ensuring stable and reliable readings.
- Integration with Control Systems: Modern pressure sensors should support HART, Modbus, Profibus, or Foundation Fieldbus communication protocols for seamless integration with SCADA, DCS, and PLC systems. Wireless pressure transmitters can also be used in remote or hard-to-reach locations, reducing installation costs and enhancing data collection for predictive analytics.
- Maintenance and Lifecycle Costs: Mechanical pressure switches and gauges are low-cost but require frequent calibration and replacement. Smart digital pressure transmitters provide self-diagnostics and predictive maintenance alerts, reducing downtime and extending instrument life. Flush-mounted pressure sensors minimize clogging in slurries and viscous fluids, lowering maintenance efforts.
Temperature Sensing & Control
Temperature plays a critical role in refining and chemical processing, directly affecting reaction kinetics, product quality, energy efficiency, and equipment longevity. Precise temperature monitoring ensures that processes operate within optimal limits, preventing overheating, thermal degradation, and equipment failure. The selection of thermocouples, resistance temperature detectors (RTDs), infrared sensors, and bimetallic temperature switches depends on the specific requirements of the application, including temperature range, response time, environmental conditions, and accuracy. Advanced smart temperature transmitters, integrated with SCADA and DCS systems, allow for real-time process optimization, predictive maintenance, and compliance with safety and environmental regulations.
Applications of Temperature Sensing & Control in Refining and Chemical Processing
- Furnace and Heater Temperature Control: Furnaces and process heaters in refineries and chemical plants must operate within strict temperature limits to maximize heat transfer efficiency and fuel economy. Thermocouples with ceramic or metal sheaths are widely used due to their ability to withstand extreme temperatures. Infrared pyrometers provide non-contact temperature measurement, ideal for monitoring flame and refractory surface temperatures.
- Distillation Column Temperature Profiling: In crude oil refining and chemical distillation, precise temperature control ensures efficient separation of hydrocarbons and chemical compounds. RTDs and thermocouples are installed at various column trays to monitor temperature gradients, helping operators optimize reflux ratios, pressure control, and energy consumption.
- Reactor Temperature Control: Chemical reactors often require precise temperature monitoring to maintain reaction stability and maximize yield. RTDs offer high-accuracy temperature measurement in reactors operating within moderate temperature ranges. Thermocouples, often housed in thermowells, are used in high-temperature catalytic and cracking reactions where rapid response time is required. Fiber optic temperature sensors are also used for multi-point temperature profiling in reactors with extreme temperature gradients.
- Heat Exchanger Monitoring: Temperature differential monitoring in heat exchangers helps detect fouling, scaling, and reduced heat transfer efficiency. Surface-mounted RTDs and thermocouples measure inlet and outlet temperatures of process fluids, ensuring efficient thermal performance. Wireless temperature sensors allow for remote monitoring of heat exchanger performance in distributed processing units.
- Storage Tank and Pipeline Temperature Monitoring: Temperature control is essential in crude oil, chemical, and LNG storage tanks to prevent thermal expansion, phase separation, and product degradation. Thermocouples and RTDs are placed at different levels of large storage tanks to monitor temperature distribution. Self-regulating heat trace systems with temperature sensors are used on pipelines to maintain flow assurance and prevent freezing in colder environments.
- Safety and Fire Detection in Hazardous Areas: Infrared temperature sensors and thermocouples are used for fire and heat detection in hazardous areas where flammable gases and vapors are present. These sensors provide early warnings for overheating electrical equipment, leaks, and potential combustion sources, improving plant safety and emergency response.
Key Purchasing Considerations
- Measurement Accuracy and Response Time: High-precision applications such as reactor control and distillation profiling require RTDs, which provide higher accuracy and stability compared to thermocouples. However, thermocouples offer faster response times and are preferred in high-temperature or rapidly fluctuating processes.
- Operating Temperature Range: Different sensor types have temperature limitations:
- RTDs: Typically operate in -200°C to 600°C and are ideal for moderate-temperature processes requiring high accuracy.
- Thermocouples: Handle extreme conditions up to 1,800°C, making them suitable for furnaces, kilns, and high-temperature reactors.
- Infrared Pyrometers: Provide non-contact temperature measurement in extreme heat environments such as flame monitoring and refractory surface analysis.
- Environmental and Chemical Resistance: Sensors used in corrosive, high-pressure, and hazardous environments must be built with durable materials such as Hastelloy, Inconel, or ceramic coatings. Thermowells protect temperature sensors from erosion, corrosion, and high-pressure conditions in pipelines and reactors.
- Integration with Control Systems: Smart temperature transmitters with HART, Modbus, or Profibus communication protocols allow seamless integration with SCADA, PLCs, and DCS systems for automated process control. Wireless temperature sensors provide additional flexibility for remote and hard-to-access locations.
- Safety and Compliance Considerations: Temperature sensors used in hazardous environments must meet ATEX, IECEx, and SIL (Safety Integrity Level) standards. Explosion-proof temperature transmitters and flameproof enclosures ensure safety in volatile applications such as hydrocarbon processing, hydrogen reforming, and chemical manufacturing.
- Maintenance and Lifecycle Costs: RTDs require periodic calibration but offer long-term stability with minimal drift. Thermocouples have a shorter lifespan in aggressive environments but are easily replaceable. Infrared sensors and fiber optic temperature sensors reduce maintenance requirements by eliminating physical contact with process materials.
Level Detection & Level Control
Level measurement is a critical aspect of refining and chemical processing, ensuring accurate inventory management, process stability, and safety compliance. The ability to monitor and control liquid, solid, and interface levels in tanks, reactors, and pipelines is essential for preventing overfills, optimizing feed rates, maintaining separation processes, and ensuring safe storage of hazardous materials. Various level measurement technologies, including guided wave radar, ultrasonic sensors, differential pressure transmitters, capacitance probes, and float switches, are used depending on the specific application, material properties, and environmental conditions. Smart level sensors integrated with SCADA, DCS, and PLC systems provide real-time data for automated control, predictive maintenance, and enhanced plant safety.
Applications of Level Detection & Level Control in Refining and Chemical Processing
- Crude Oil and Product Storage Tanks: Accurate level measurement in large storage tanks prevents overfills, product loss, and compliance violations. Radar and guided wave radar (GWR) level transmitters are commonly used due to their ability to penetrate vapor, foam, and temperature variations while providing highly accurate continuous level readings. Hydrostatic pressure sensors offer an alternative for level measurement in pressurized tanks.
- Distillation Column Interface and Liquid Level Control: Distillation columns require precise interface level detection between hydrocarbon fractions to maintain efficient separation. Differential pressure (DP) level transmitters measure liquid levels between trays, while capacitance level sensors detect phase boundaries in separation processes. Displacer-type level transmitters are used in high-temperature environments where electronic sensors may degrade.
- Reactor and Mixing Vessel Level Monitoring: Maintaining proper liquid levels in reactors and mixing vessels ensures consistent reaction kinetics and prevents hazardous pressure build-ups. Ultrasonic and radar level sensors provide non-contact measurement for aggressive chemicals, while vibrating fork level switches ensure high and low-level alarms to prevent overflow or dry running conditions.
- Foam and Emulsion Detection in Chemical Processing: Chemical reactions and separation processes often generate foam and emulsions, which can interfere with accurate level readings. Capacitive and radar level sensors are used to differentiate between liquid and foam layers, preventing process inefficiencies and pump cavitation.
- Sump and Wastewater Level Monitoring: Refining and chemical plants manage wastewater and byproducts that require precise level monitoring for pump control, treatment efficiency, and environmental compliance. Float switches and ultrasonic sensors are commonly used for open sump applications, while submersible hydrostatic level transmitters are ideal for corrosive or sludge-heavy waste streams.
- Liquefied Gas and Cryogenic Storage: Cryogenic storage tanks used for LNG, ammonia, and other liquefied gases require specialized level measurement solutions that withstand extreme temperatures and pressure variations. Differential pressure transmitters and guided wave radar sensors are commonly used in these applications, ensuring accurate readings despite vaporization effects and thermal expansion.
Key Purchasing Considerations
- Material Properties and Process Conditions: Level sensors must be compatible with the fluid density, viscosity, dielectric constant, and chemical composition. Radar level sensors are ideal for volatile hydrocarbons, while capacitance probes work well in low-dielectric materials like dry powders or certain refined products.
- Non-Contact vs. Contact Measurement:
- Non-contact sensors: (radar, ultrasonic, laser) are ideal for aggressive chemicals, high-temperature environments, and sanitary applications where the sensor should not touch the material.
- Contact-based sensors: (guided wave radar, capacitance, float, and DP transmitters) provide stable and accurate readings in pressurized vessels, foamy applications, and high-viscosity fluids.
- Tank and Vessel Design Constraints: Level instruments must fit the physical layout of the storage or processing vessel. Top-mounted radar sensors are ideal for large tanks, while side-mounted DP level transmitters or displacer sensors are preferred for narrow columns and high-pressure vessels.
- Environmental and Safety Regulations: Level measurement devices must meet API, ASME, ATEX, and IECEx safety standards for hazardous and flammable environments. Intrinsically safe sensors and explosion-proof housings are necessary for applications in hydrocarbon storage, chemical reactors, and distillation columns.
- Integration with Process Control Systems: Modern level sensors should support HART, Modbus, Profibus, and Ethernet/IP protocols for seamless communication with SCADA, DCS, and PLC systems. Wireless level sensors can be deployed in remote or hard-to-access locations, reducing installation costs and enhancing monitoring capabilities.
- Maintenance and Longevity:
- Radar and ultrasonic sensors have minimal maintenance needs as they have no moving parts and do not come into contact with process materials.
- Float switches and DP level transmitters require periodic cleaning and calibration but offer high reliability in traditional applications.
- Self-diagnostic smart sensors provide predictive maintenance alerts, reducing downtime and improving asset reliability.
Gas & Flame Detection for Safety Monitoring
Safety is paramount in refining and chemical processing facilities, where flammable gases, toxic vapors, and combustible materials pose significant hazards. Effective gas and flame detection systems are essential for preventing fires, explosions, and exposure to hazardous substances. These systems continuously monitor the air for combustible gases, toxic leaks, and flames, triggering alarms and safety shutdowns when dangerous conditions are detected. Technologies such as infrared (IR) and catalytic bead gas detectors, electrochemical sensors, flame ionization detectors (FIDs), and ultraviolet/infrared (UV/IR) flame sensors are used to enhance plant safety. Integration with distributed control systems (DCS) and emergency shutdown systems (ESD) ensures rapid response and regulatory compliance with industry safety standards, including NFPA, OSHA, and API.
Applications of Gas & Flame Detection for Safety Monitoring in Refining and Chemical Processing
- Hydrocarbon Gas Leak Detection in Processing Units: Refining operations involve the handling of volatile hydrocarbons, such as methane, propane, butane, and benzene, which pose fire and explosion risks. Fixed infrared (IR) gas detectors continuously monitor gas leaks in hydrocrackers, reformers, and distillation units, providing rapid detection and automated safety responses. Catalytic bead gas sensors are used in confined spaces and enclosed processing areas to detect lower explosive limit (LEL) concentrations of flammable gases.
- Toxic Gas Monitoring in Chemical Processing: Many chemical processes generate toxic byproducts, including hydrogen sulfide (H₂S), ammonia (NH₃), chlorine (Cl₂), and carbon monoxide (CO). Electrochemical gas detectors are deployed in production areas, pipelines, and storage facilities to provide early warning of toxic gas accumulation. Wireless gas detectors allow real-time monitoring in remote areas or locations with limited infrastructure.
- Refinery and Storage Tank Fire Protection: Large storage tanks containing crude oil, refined products, and chemical feedstocks require continuous flame detection to prevent catastrophic fires. Ultraviolet/infrared (UV/IR) and multi-spectrum infrared (MSIR) flame detectors detect fires from hydrocarbon combustion sources and differentiate between real flames and false alarms (e.g., sunlight, welding arcs).
- Loading, Unloading, and Transport Safety: Truck, railcar, and marine vessel loading stations handle highly flammable substances, requiring gas detection systems to monitor vapor emissions and leaks. Open-path infrared gas detectors are installed along loading racks and transfer lines to provide wide-area coverage for hydrocarbon gas leaks.
- Confined Space Entry Monitoring: Maintenance activities in tanks, boilers, and underground pipelines expose workers to potential oxygen deficiency and toxic gas buildup. Portable multi-gas detectors allow personnel to assess atmospheric conditions before and during confined space entry. These devices detect oxygen (O₂) levels, combustible gases, and toxic vapors in real-time, ensuring worker safety.
- Fugitive Emissions and Environmental Compliance: Refineries and chemical plants must comply with emissions regulations by detecting and controlling fugitive gas leaks. Flame ionization detectors (FIDs) and photoionization detectors (PIDs) are used for volatile organic compound (VOC) monitoring at equipment interfaces, valves, and flare stacks, helping operators meet EPA Leak Detection and Repair (LDAR) program requirements.
Key Purchasing Considerations
- Detection Method and Sensor Type:
The selection of gas and flame detectors depends on the nature of the hazardous gases, vapors, and fire risks - Infrared (IR) Gas Detectors: Ideal for detecting hydrocarbon gas leaks in open spaces and industrial environments.
- Electrochemical Gas Sensors: Used for toxic gas detection, including H₂S, CO, and NH₃, in process areas and worker safety zones.
- Catalytic Bead Sensors: Effective for detecting combustible gases in enclosed areas with LEL measurement capabilities.
- UV/IR and MSIR Flame Detectors: Provide rapid and false-alarm-resistant fire detection in high-risk areas.
- Detection Range and Coverage
- Point gas detectors provide localized monitoring near leak-prone equipment such as valves, pumps, and compressors.
- Open-path (line-of-sight) gas detectors cover larger areas, such as tank farms, loading docks, and pipelines, ensuring early detection of gas plumes.
- Response Time and Alarm Thresholds
- Fast response time is critical for preventing fire escalation and toxic gas exposure.
- Gas detectors should have adjustable alarm thresholds to align with industry safety regulations and process-specific risks.
- Hazardous Area Ratings and Safety Certifications: Gas and flame detectors must comply with OSHA, NFPA, IECEx, ATEX, and API safety standards. Explosion-proof and intrinsically safe (IS) certified detectors ensure safe operation in Class I, Division 1 and Division 2 hazardous areas.
- Integration with Control and Shutdown Systems: Detection systems must integrate seamlessly with SCADA, DCS, and ESD systems to enable real-time safety responses, such as:
- Activating ventilation systems to disperse gas leaks.
- Triggering alarms and emergency shutdowns in case of hazardous conditions.
- Activating fire suppression systems, including water deluge and chemical suppression agents.
- Maintenance and Calibration Requirements:
- Fixed gas detectors require periodic calibration and sensor replacement to ensure long-term reliability.
- Self-testing and self-diagnostic capabilities in modern detectors reduce maintenance costs and improve system availability.
- Wireless gas detection systems simplify deployment and reduce installation costs in remote areas.
Environmental Compliance Monitoring
Environmental compliance monitoring is essential in refining and chemical processing industries to ensure adherence to emissions regulations, wastewater discharge limits, and hazardous material containment. Regulatory agencies such as the Environmental Protection Agency (EPA), Occupational Safety and Health Administration (OSHA), and local air quality management districts enforce strict guidelines for air, water, and soil quality. Continuous monitoring of airborne pollutants, effluent discharges, and fugitive emissions is necessary to mitigate environmental impact, avoid regulatory fines, and maintain operational sustainability. Advanced continuous emissions monitoring systems (CEMS), water samplers, water quality analyzers, particulate matter sensors, and volatile organic compound (VOC) detectors help facilities track compliance metrics in real time. Integration with SCADA, DCS, and environmental reporting systems enables automated data logging, trend analysis, and regulatory reporting.
Applications of Environmental Compliance Monitoring in Refining and Chemical Processing
- Continuous Emissions Monitoring (CEMS) for Air Quality Compliance: Refineries and chemical plants are major sources of sulfur oxides (SOₓ), nitrogen oxides (NOₓ), carbon monoxide (CO), carbon dioxide (CO₂), and particulate matter (PM). CEMS analyzers use gas chromatography, infrared absorption, and chemiluminescence techniques to measure pollutant concentrations and ensure compliance with EPA Clean Air Act standards. These systems are deployed in stacks, flares, and process vents to continuously monitor emissions and optimize combustion efficiency.
- VOC and Fugitive Emissions Detection: Volatile organic compounds (VOCs) are released from refining processes, storage tanks, and chemical reactors. Photoionization detectors (PIDs) and flame ionization detectors (FIDs) detect and quantify VOC leaks in compliance with EPA Leak Detection and Repair (LDAR) programs. Optical gas imaging (OGI) cameras allow for visual detection of gas leaks in hard-to-access locations, improving early detection and remediation efforts.
- Wastewater Effluent Monitoring: Refining and chemical processing generate wastewater containing heavy metals, hydrocarbons, and chemical contaminants that must be treated before discharge. Water quality analyzers measure parameters such as pH, turbidity, total organic carbon (TOC), chemical oxygen demand (COD), and biological oxygen demand (BOD) to ensure compliance with National Pollutant Discharge Elimination System (NPDES) permits. Oil-in-water analyzers detect hydrocarbon contamination, preventing environmental damage and regulatory violations.
- Stormwater and Runoff Monitoring: Refineries and chemical plants must manage stormwater runoff to prevent contamination of local water sources. Flow meters, total suspended solids (TSS) analyzers, and conductivity sensors help monitor stormwater discharge, ensuring it meets local environmental standards. Automated rainwater collection and treatment systems help reduce environmental impact.
- Hazardous Waste Storage and Soil Contamination Prevention: Facilities handling hazardous chemicals and waste materials must prevent leaks and spills that could contaminate soil and groundwater. Soil vapor analyzers and groundwater monitoring wells detect leaks from underground storage tanks (USTs) and waste disposal sites. Secondary containment sensors in storage areas ensure compliance with EPA Resource Conservation and Recovery Act (RCRA) regulations.
- Ambient Air Monitoring for Worker and Community Safety: Facilities near residential and industrial zones must monitor ambient air quality to protect workers and surrounding communities. Fixed air monitoring stations equipped with gas analyzers and particulate sensors track benzene, hydrogen sulfide (H₂S), ammonia, and fine particulate matter (PM2.5 and PM10) concentrations. Real-time data is used to issue safety alerts, adjust process controls, and report environmental conditions to regulatory bodies.
Key Purchasing Considerations
- Regulatory Compliance and Reporting Requirements: Environmental monitoring systems must comply with EPA, OSHA, NPDES, RCRA, and local air quality regulations. CEMS and water quality analyzers must meet regulatory certification standards (e.g., EPA Performance Specification Tests for CEMS) to ensure compliance and accurate reporting.
- Measurement Accuracy and Detection Limits:
- CEMS analyzers require low detection limits for gases such as NOₓ, SOₓ, and CO to meet air quality standards.
- Water quality sensors must detect trace levels of heavy metals and organic compounds for compliance with wastewater discharge permits.
- Gas leak and VOC detectors must have high sensitivity to detect small leaks before they become significant hazards.
- Real-Time Data Logging and Automation:
- Automated environmental monitoring systems should integrate with SCADA, DCS, and cloud-based reporting platforms for real-time data logging and trend analysis.
- Smart sensors with predictive analytics improve maintenance planning by detecting sensor drift, calibration needs, and system malfunctions before they impact compliance.
- Durability and Suitability for Harsh Environments:
- Outdoor monitoring stations must withstand temperature extremes, humidity, and corrosive conditions.
- Portable and fixed gas detectors should have intrinsically safe (IS) certifications for deployment in flammable and hazardous environments.
- Water quality analyzers should have self-cleaning capabilities to prevent fouling from industrial effluents.
- Integration with Environmental Compliance Reporting:
- Cloud-based environmental monitoring solutions enable remote access to compliance data, reducing the administrative burden of manual reporting.
- Automated alarm systems and real-time alerts improve regulatory response times, ensuring compliance with emission thresholds and discharge limits.
- Maintenance and Calibration Requirements:
- CEMS and water analyzers require regular calibration to maintain measurement accuracy.
- Self-diagnostic capabilities in modern sensors reduce maintenance costs and minimize downtime.
- Gas detectors with auto-calibration features improve efficiency in large-scale industrial facilities.
Industry Standards & Regulatory Compliance
EPA, OSHA, and Industry Standards for Refining & Chemical Processing
Refining and chemical facilities must meet comprehensive requirements designed to protect workers, the environment, and surrounding communities:
EPA Clean Air Act (CAA) – 40 CFR Parts 60, 63, and 98:
- Requires continuous monitoring of volatile organic compounds (VOCs), sulfur oxides (SOx), nitrogen oxides (NOx), carbon monoxide (CO), and greenhouse gases (GHGs).
- Facilities must operate Continuous Emissions Monitoring Systems (CEMS) to track and report emissions in compliance with National Emission Standards for Hazardous Air Pollutants (NESHAP) and New Source Performance Standards (NSPS).
- Flaring systems, combustion units, and storage tanks require leak detection and compliance verification through optical gas imaging, infrared sensors, or flame ionization detectors.
EPA Clean Water Act (CWA) & NPDES Permitting:
- Mandates treatment and monitoring of process wastewater, stormwater runoff, and cooling tower blowdown prior to discharge.
- Facilities must use flow meters, pH probes, turbidity sensors, and chemical analyzers to monitor BOD, COD, TSS, oil & grease, and heavy metals in accordance with NPDES permit requirements.
- Discharge data must be logged and reported regularly for regulatory compliance.
OSHA Process Safety Management (PSM) – 29 CFR 1910.119:
- Requires detailed analysis and control of hazards associated with toxic, reactive, flammable, or high-pressure chemicals.
- Instrumentation must be rated for hazardous environments (Class I, Div 1/2 or Zone 0/1/2) and integrated into emergency shutdown systems, interlocks, and alarms.
- Facilities must perform regular calibration, testing, and documentation of instruments used in safety-critical applications.
API, NFPA, and ISA Standards:
- API 670 (Machinery Protection Systems) and API 682 (Mechanical Seals) guide vibration monitoring and rotating equipment protection.
- API 2350 applies to overfill protection in storage tanks, requiring reliable level instrumentation and high-level alarms.
- ISA 84 / IEC 61511 sets standards for the design and validation of safety instrumented systems (SIS), including redundancy, diagnostics, and proof testing intervals.
Emissions Reporting, Safety, and Environmental Stewardship
- Requires real-time monitoring and reporting of CO₂, CH₄, and N₂O emissions, particularly from combustion, flaring, and process vents.
- Mass flow sensors and gas analyzers must be EPA-certified and calibrated regularly.
- Facilities must track fugitive emissions from valves, flanges, pumps, and compressors, using portable and fixed gas detectors.
- LDAR programs are typically governed by NESHAP Subparts F, G, H, and I, depending on the chemicals in use.
- Fixed flame and gas detection systems are required in hazardous areas, especially in refinery units, loading racks, and chemical storage areas.
- Integrated with SIS and ESD systems, these instruments provide fast response and reduce risk of major incidents.
Benefits of Working With Clipper Controls
Case Studies & Success Stories
Click here to read our Refinery & Chemical Processing case studies.
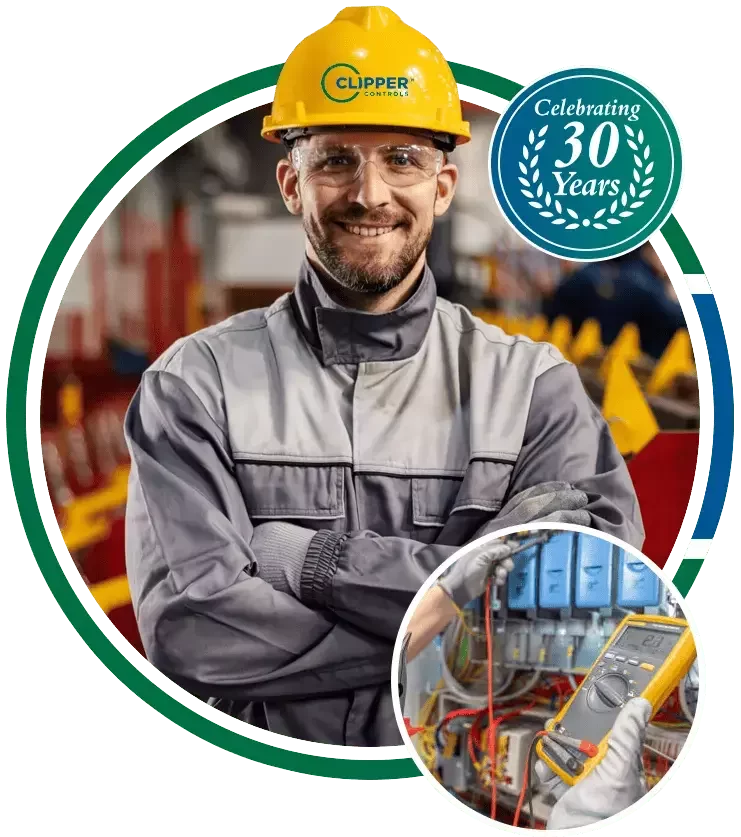
Real Results, Real Impact:
Thanks to Clipper Controls, our wastewater treatment plant improved efficiency & compliance with top-tier flow meters. Reliable solutions, great support! We recommend Clipper Controls to all our partner companies.
~ John Smith, Controls Engineer @ ABC Company
Clipper Controls helped our city upgrade water monitoring systems, ensuring accuracy & compliance. Reliable solutions & excellent customer service!
~ Nancy Patel, Procurement @ ABC Company
~ John Smith, Controls Engineer @ ABC Company