Water and Wastewater Process Control Applications
Quick Page Navigation:
🔹How Our Products Support Your Industry
🔹Key Applications & Solutions
Pressure & Temperature Regulation
Industrial Automation & Remote Process Management
Gas Detection & Environmental Monitoring
Energy Management & Efficiency Solutions
🔹Industry Standards & Regulatory Compliance
🔹Benefits of Working With Clipper Controls
​​Application Overview
Water and wastewater treatment facilities rely on precise process control to maintain efficiency, compliance, and system integrity. Accurate measurement and monitoring of flow, level, pressure, temperature, and chemical dosing are critical to ensuring stable operations. Effective control strategies help optimize energy use, reduce chemical consumption, and prevent equipment failures, leading to improved system performance and cost savings.
Reliable instrumentation and automation are essential for maintaining water quality and meeting regulatory requirements. SCADA systems, sensors, and controllers enable real-time data collection and process adjustments, allowing operators to respond quickly to changing conditions. Proper integration of these technologies ensures consistent treatment performance, minimizes downtime, and enhances overall plant reliability.
​​How Our Products Support Your Industry
​​Key Applications and Solutions
​​Flow Measurement & Control
Accurate flow measurement and control are essential in water and wastewater treatment to ensure efficient resource allocation, maintain system integrity, and meet regulatory compliance. Flow monitoring plays a critical role in managing water distribution networks, chemical dosing, wastewater discharge, and filtration processes. Poor flow measurement can lead to inconsistent treatment, excessive energy consumption, equipment failure, and regulatory fines.
Applications of Flow Measurement in Water & Wastewater Treatment
Flow measurement plays a vital role in optimizing processes, maintaining compliance, and improving efficiency across various stages of water and wastewater treatment. Different flow measurement technologies are suited for specific applications based on fluid properties, accuracy requirements, and environmental conditions.
Source Water Intake: Monitoring the volume of raw water entering a treatment facility ensures accurate allocation and efficient processing. Electromagnetic flow meters (magmeters) are commonly used due to their high accuracy and ability to handle large volumes of water with suspended solids.
Chemical Dosing & pH Control: Precise chemical dosing is essential for disinfection, coagulation, and pH balancing. Coriolis flow meters are ideal for this application because they measure mass flow directly, ensuring the correct chemical-to-water ratio. Ultrasonic and differential pressure (DP) flow meters can also be used where inline chemical measurement is needed.
Filtration & Membrane Processes: Sand filters, ultrafiltration (UF), reverse osmosis (RO), and activated carbon systems require controlled flow to maintain efficiency and prevent fouling. Electromagnetic and ultrasonic flow meters are commonly used due to their ability to measure flow without physical obstructions that could trap particulates or biofilm.
Pump & Pipeline Monitoring: Efficient pump operation prevents excessive energy use and mechanical failures. Vortex and differential pressure flow meters are suitable for monitoring pump performance, identifying cavitation, and ensuring optimal pipeline flow rates. In large distribution systems, ultrasonic flow meters help detect leaks and optimize water movement.
Effluent Discharge Compliance: Wastewater effluent must meet EPA, NPDES, and local environmental regulations regarding discharge limits. Electromagnetic and ultrasonic flow meters are ideal for monitoring treated wastewater discharge due to their ability to handle varying fluid compositions and flow conditions.
Sludge & Slurry Flow Measurement: Thickened sludge and slurry require specialized meters that can handle high viscosity and suspended solids. Electromagnetic flow meters provide reliable measurement without clogging, ensuring efficient sludge handling and processing.
ClipperView Flow Monitoring Software
ClipperView is a cloud-based monitoring and data management platform purpose-built for the water and wastewater sector. Designed to integrate with ISCO Signature, Duratracker, and industry-standard flow technologies—including LaserFlow, ultrasonic, bubbler, and area velocity meters—ClipperView provides utility teams with continuous visibility into collection system performance, regulatory thresholds, and system capacity.
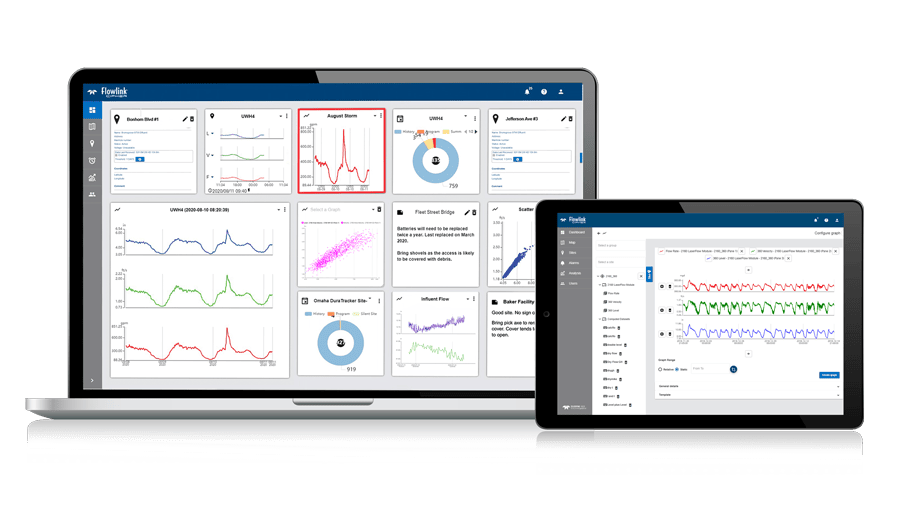
Built for Utilities and Sewer System Operators
Continuous Flow & Level Monitoring
Eliminate manual data retrieval with automated uploads from remote sites—ideal for manholes, interceptors, and CSO/SSO risk areas.Proactive Compliance Management
Receive real-time alerts when wet weather flow, surcharge levels, or design thresholds are exceeded—helping teams stay ahead of permit violations.Visual Analytics for I&I and Capacity Studies
Overlay rainfall, diurnal patterns, and historical flow to identify inflow and infiltration, track surcharge frequency, and support capital improvement planning.Interjurisdictional Billing Support
Deliver defensible data for industrial user billing, cost recovery, and municipal service agreements.Easy Deployment—No IT Required
Cloud-hosted with optional cellular connectivity. Get up and running without procurement delays or infrastructure investment.


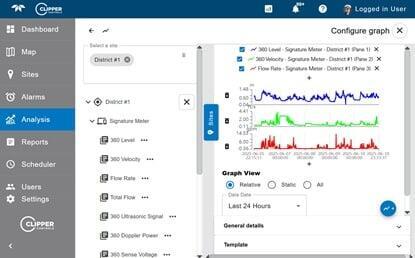
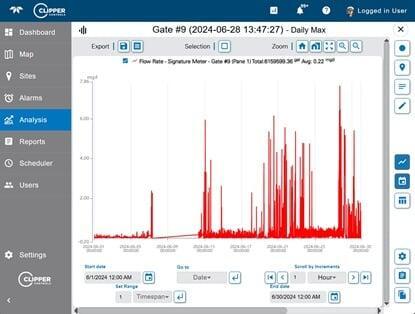
Talk to an Expert About ClipperView
Key Purchasing Considerations
When choosing the right solution, there are several important factors to keep in mind. But you don’t have to figure it out alone—we’re here to help! Our knowledgeable crew is happy to guide you through the options and find the best fit for your needs. Whether you prefer a quick call or a message through our contact form, we’re ready to assist you every step of the way. Let’s work together to make sure you get the most reliable and efficient solution!
- Fluid Type & Composition: Consider whether the medium is clean water, wastewater with suspended solids, chemicals, or sludge, as different meters are optimized for specific conditions.
- Flow Rate & Accuracy Requirements: Higher accuracy is needed for chemical dosing, custody transfer, and regulatory reporting, while standard applications may tolerate minor deviations.
- Installation Constraints: Some meters require pipe modifications, while others, like clamp-on ultrasonic meters, offer non-intrusive installation for easy retrofitting.
- Maintenance & Durability: Magmeters and ultrasonic meters require minimal maintenance, whereas mechanical meters may have moving parts prone to wear.
- Pressure & Temperature Ratings: Ensure the chosen meter can withstand the operating pressure and temperature conditions of the treatment facility.
- Integration with SCADA & IoT Systems: Many modern flow meters offer digital connectivity, remote monitoring, and real-time data transmission, improving operational efficiency.
​​Level Monitoring & Management
Effective level monitoring and management are essential in water and wastewater treatment to prevent overflows, optimize storage capacity, regulate pumping systems, and maintain operational efficiency. Proper level measurement ensures consistent process control in tanks, reservoirs, clarifiers, and lift stations, helping to prevent equipment damage, environmental contamination, and regulatory non-compliance. Inaccurate level readings can lead to system failures, inefficient chemical dosing, excessive energy consumption, and costly downtime.
Applications of Level Measurement in Water & Wastewater Treatment
Level measurement plays a crucial role in ensuring stable operation across various treatment processes. Different level sensing technologies are available depending on tank size, fluid characteristics, environmental conditions, and accuracy requirements.
Water Storage & Reservoirs: Monitoring water levels in storage tanks and reservoirs is critical for distribution system stability and demand forecasting. Radar and ultrasonic level sensors provide non-contact measurement, making them ideal for large tanks and open reservoirs where debris or waves may interfere with accuracy.
Chemical & Sludge Tank Monitoring: Proper chemical and sludge level management is essential for accurate dosing, sludge dewatering, and chemical feed control. Guided wave radar (GWR) and hydrostatic pressure sensors are well-suited for high-viscosity materials, foaming liquids, and aggressive chemicals.
Clarifiers & Sedimentation Basins: Maintaining proper water levels in clarifiers and sedimentation basins ensures efficient solids settling and sludge removal. Ultrasonic and float-based level sensors are commonly used, offering real-time monitoring of sludge blanket levels to prevent system inefficiencies.
Pumping Station Control & Lift Stations: Effective pump control depends on accurate level measurement to prevent pump dry runs, overflows, and inefficiencies. Float switches, hydrostatic level sensors, and ultrasonic sensors help optimize pump activation and deactivation, ensuring proper wastewater transport.
Stormwater & Overflow Monitoring: Stormwater management requires precise level monitoring to prevent flooding, combined sewer overflows (CSOs), and environmental contamination. Radar and ultrasonic sensors provide continuous level measurement in open channels, retention ponds, and stormwater basins.
Key Purchasing Considerations
When selecting a level monitoring solution, several factors should be considered to ensure compatibility with process requirements and environmental conditions.
- Measurement Range & Accuracy: Choose a sensor with a suitable range for your tank size or basin depth while ensuring the required level of accuracy.
- Fluid Properties: Consider whether the liquid is clean, sludge-like, foamy, corrosive, or prone to vapor interference, as this impacts sensor performance.
- Environmental Conditions: Exposure to high humidity, temperature fluctuations, and aggressive chemicals requires robust and corrosion-resistant sensors.
- Installation Constraints: Some sensors require direct contact with the liquid (hydrostatic and guided wave radar), while others provide non-contact measurement (ultrasonic and radar) for easier installation and maintenance.
- Maintenance & Durability: Non-contact sensors like radar and ultrasonic require minimal maintenance, while float-based sensors may need regular cleaning and calibration.
- Integration with SCADA & Remote Monitoring: Advanced level sensors support SCADA systems, remote alarms, and IoT-enabled connectivity, enabling real-time monitoring and automated control.
​​Pressure & Temperature Regulation
Proper pressure and temperature regulation is essential in water and wastewater treatment to maintain system stability, optimize energy usage, and protect critical equipment. Fluctuations in pressure and temperature can lead to pump failures, pipeline ruptures, inefficient filtration, and chemical dosing imbalances. Monitoring these parameters ensures safe operation, compliance with regulatory standards, and extended equipment lifespan in treatment plants, distribution networks, and industrial processes.
Applications of Pressure & Temperature Regulation in Water & Wastewater Treatment
Pressure and temperature monitoring are critical across various treatment stages, with different sensor technologies suited for specific applications based on fluid type, operating conditions, and precision requirements.
Pump System Efficiency & Protection: Proper pressure regulation is necessary to prevent cavitation, over-pressurization, and energy waste in pump systems. Pressure transmitters and differential pressure (DP) sensors help monitor and maintain optimal pump performance and water flow consistency.
Filtration & Membrane Processes: In systems such as sand filters, ultrafiltration (UF), and reverse osmosis (RO), pressure fluctuations can impact filtration efficiency and membrane integrity. Differential pressure sensors detect filter clogging and membrane fouling, while temperature sensors ensure optimal operating conditions for water purification.
Boiler & Heat Exchanger Monitoring: Many industrial water treatment processes involve boilers, heat exchangers, and steam systems that require precise temperature and pressure control. RTD (Resistance Temperature Detectors) and thermocouples are commonly used to maintain stable heat transfer and prevent overheating.
Chemical Dosing & Reaction Control: Temperature variations can affect chemical reaction rates in water treatment, altering the effectiveness of processes like coagulation, oxidation, and pH adjustment. Temperature probes and digital pressure sensors help maintain process stability and ensure accurate chemical dosing.
Pipeline & Distribution System Monitoring: Maintaining consistent pressure in water distribution networks and wastewater pipelines prevents leaks, bursts, and service disruptions. Smart pressure sensors and IoT-enabled monitoring systems provide real-time data for predictive maintenance and leak detection.
Sludge Handling & Dewatering Systems: In sludge processing, pressure regulation is essential for efficient dewatering, thickening, and pressurized filtration. High-precision pressure sensors ensure optimal operation of belt presses, centrifuges, and filter presses.
Key Purchasing Considerations
Selecting the right pressure and temperature sensors requires evaluating several critical factors to ensure they meet application-specific demands and environmental conditions.
- Operating Range & Accuracy: Ensure sensors can handle the expected pressure and temperature variations while maintaining the required accuracy for process control.
- Fluid Compatibility: Consider whether the sensor materials are resistant to water, wastewater, sludge, chemicals, or corrosive gases to ensure long-term durability.
- Response Time & Sensitivity: Fast response times are crucial for real-time adjustments in high-precision applications like chemical dosing and membrane filtration.
- Installation & Maintenance Requirements: Some sensors require direct contact with process fluids, while others provide remote measurement for easier installation and maintenance.
- Integration with SCADA & Automation Systems: Modern pressure and temperature transmitters offer digital connectivity, remote monitoring, and real-time alerts, improving system efficiency and reducing downtime.
​​Industrial Automation & Remote Process Management
Automation is revolutionizing water and wastewater treatment by enhancing efficiency, accuracy, and reliability across critical processes. Industrial automation and remote process management enable facilities to reduce manual intervention, minimize operational costs, and improve compliance with environmental regulations. By integrating smart sensors, SCADA systems, programmable logic controllers (PLCs), and IoT-enabled monitoring, operators gain real-time insights and precise control over water treatment processes, ensuring optimal performance and rapid response to system changes.
Applications of Industrial Automation in Water & Wastewater Treatment
Automated systems play a crucial role in optimizing process control, data analysis, and remote monitoring. Various technologies support different automation applications based on system complexity, scalability, and integration needs.
Automated Water Sampling & Remote Monitoring: Automated water sampling plays a vital role in industrial automation for water and wastewater treatment, enabling precise, consistent, and time-efficient collection of water samples for analysis. By integrating samplers with control systems, facilities can monitor water quality parameters such as pH, turbidity, nutrient levels, and contaminants in real time or at programmed intervals. This automation reduces manual labor, enhances regulatory compliance, and improves process optimization by providing reliable data for informed decision-making. Ultimately, automated sampling helps utilities maintain environmental standards, ensure public health, and optimize chemical dosing and treatment efficiency.
SCADA Systems & Remote Monitoring: Supervisory Control and Data Acquisition (SCADA) systems enable centralized monitoring and control of pumps, valves, chemical dosing, and filtration systems. By integrating with IoT-enabled sensors and cloud-based analytics, operators can receive real-time alerts and predictive maintenance insights, reducing downtime and improving operational efficiency.
Pump & Flow Control Automation: Automated pump stations adjust flow rates, pressure, and energy consumption based on demand. Variable frequency drives (VFDs) and PLC-based pump controllers optimize performance, preventing cavitation, reducing wear, and improving energy efficiency.
Chemical Dosing & pH Regulation: Precise automation ensures accurate chemical dosing for coagulation, disinfection, and pH control, preventing overuse or underdosing. Automated dosing systems with flow-based feedback loops adjust chemical injection rates based on real-time water quality measurements.
Filtration & Membrane System Optimization: Advanced control algorithms and pressure monitoring sensors automate backwashing cycles, membrane cleaning, and differential pressure adjustments, enhancing filter performance and extending equipment lifespan.
Leak Detection & Water Distribution Automation: IoT-based sensors detect pipeline leaks, abnormal pressure fluctuations, and unauthorized water usage. Automated actuators and control valves adjust flow distribution in real-time, preventing water loss and ensuring system stability.
Energy Management & Predictive Maintenance: AI-powered analytics monitor power consumption, motor efficiency, and equipment wear to optimize energy use and maintenance scheduling. Smart automation platforms reduce operational costs by detecting inefficiencies before failures occur.
Key Purchasing Considerations
Choosing the right industrial automation and remote monitoring system depends on several key factors to ensure compatibility with existing infrastructure and future scalability.
- System Scalability & Integration: Ensure automation solutions integrate seamlessly with existing SCADA, PLCs, IoT devices, and cloud-based platforms for long-term flexibility.
- Data Communication & Security: Secure data transmission protocols, such as Modbus, MQTT, and OPC-UA, are crucial for protecting sensitive operational data and preventing cybersecurity threats.
- Reliability & Redundancy: Critical infrastructure demands high-availability automation solutions with built-in failover mechanisms to maintain continuous operation.
- Ease of Installation & Maintenance: Look for user-friendly interfaces, remote diagnostics, and plug-and-play sensor compatibility to simplify deployment and reduce maintenance requirements.
- Compliance & Regulatory Standards: Ensure automation solutions adhere to EPA, NPDES, ISO 14001, and local water treatment regulations for data reporting and operational transparency.
​​Gas Detection & Environmental Monitoring
Effective gas detection and environmental monitoring are essential in water and wastewater treatment facilities to protect workers, ensure regulatory compliance, and maintain a safe operating environment. Hazardous gases such as methane (CH₄), hydrogen sulfide (H₂S), chlorine (Cl₂), and ammonia (NH₃) are commonly present in treatment processes and can pose serious health and safety risks if not properly monitored. Implementing advanced gas detection systems and real-time environmental monitoring solutions helps prevent toxic exposure, equipment damage, and environmental contamination.
Applications of Gas Detection & Environmental Monitoring in Water & Wastewater Treatment
Gas detection and environmental monitoring systems are deployed across multiple areas of water treatment plants, sewer systems, and industrial facilities to enhance safety and compliance. Various sensor technologies and monitoring strategies are used depending on the type of gas, environmental conditions, and detection requirements.
Confined Space Monitoring: Wastewater treatment facilities contain underground vaults, pump stations, and sludge processing areas, where toxic gases like hydrogen sulfide (Hâ‚‚S) and methane (CHâ‚„) can accumulate. Fixed and portable gas detectors with electrochemical, infrared (IR), and catalytic bead sensors ensure worker safety before and during confined space entry.
Chlorine & Ammonia Leak Detection: Chlorine (Cl₂) and ammonia (NH₃) are widely used in disinfection and nutrient removal but can be hazardous if leaked. Electrochemical and semiconductor gas sensors provide real-time leak detection in chlorination and chemical storage rooms, triggering alarms and ventilation systems when gas levels exceed safe thresholds.
Aeration & Digester Gas Monitoring: Anaerobic digesters generate biogas containing methane (CHâ‚„) and carbon dioxide (COâ‚‚), which can be captured for energy recovery or must be properly vented to prevent buildup. Infrared and catalytic bead gas sensors help monitor gas concentrations to optimize biogas utilization and prevent explosive conditions.
Odor Control & Air Quality Monitoring: Hydrogen sulfide (Hâ‚‚S) and volatile organic compounds (VOCs) contribute to strong odors and air pollution around treatment plants. Continuous air quality sensors help regulate odor control systems, chemical scrubbers, and activated carbon filtration units to minimize environmental impact and community complaints.
EPA & OSHA Compliance Monitoring: Facilities must comply with EPA air emission regulations and OSHA workplace safety standards by maintaining accurate gas monitoring logs and automated reporting systems. IoT-enabled gas sensors provide continuous data collection and remote alerting to ensure compliance with regulatory thresholds.
Key Purchasing Considerations
Selecting the right gas detection and environmental monitoring system requires evaluating several key factors to ensure worker safety, regulatory compliance, and operational efficiency.
- Type of Gas Detected: Different sensors are optimized for toxic gases (H₂S, Cl₂, NH₃), combustible gases (CH₄, CO), and oxygen deficiency monitoring.
- Fixed vs. Portable Detection: Fixed gas detectors provide continuous monitoring in high-risk areas, while portable gas detectors offer personal safety for field workers and confined space entry.
- Sensor Sensitivity & Accuracy: Ensure gas detectors meet detection thresholds set by OSHA, NIOSH, and EPA regulations for early warning and emergency response.
- Calibration & Maintenance Requirements: Choose self-calibrating and long-life sensor technologies to minimize downtime and ongoing maintenance costs.
- Integration with SCADA & Alarm Systems: Modern gas detection networks connect with SCADA, remote monitoring platforms, and automated ventilation systems to improve real-time response and risk mitigation.
​​Energy Management & Efficiency Solutions
Optimizing energy management and efficiency is crucial in water and wastewater treatment facilities, where high energy consumption is required for pumping, aeration, filtration, and chemical processing. By implementing advanced energy monitoring systems, variable frequency drives (VFDs), high-efficiency motors, and predictive analytics, facilities can reduce operational costs, minimize carbon footprints, and improve overall sustainability. Effective energy optimization not only enhances efficiency but also ensures compliance with EPA energy regulations and sustainability initiatives.
Applications of Energy Management & Efficiency Solutions in Water & Wastewater Treatment
Energy efficiency strategies can be applied across various treatment processes to reduce power consumption, enhance equipment lifespan, and optimize system performance. Different technologies and automation solutions help improve energy usage in key operational areas.
Pump Optimization & Variable Frequency Drives (VFDs): Pumps account for a significant portion of energy use in water and wastewater systems. VFDs and smart pump controls allow for adaptive speed adjustments, reducing unnecessary energy waste and extending pump lifespan.
Aeration & Blower System Efficiency: Aeration is one of the most energy-intensive processes in biological treatment. Upgrading to high-efficiency blowers, fine-bubble diffusers, and dissolved oxygen monitoring sensors ensures optimal air delivery, minimizing over-aeration and reducing energy consumption.
Renewable Energy Integration (Solar, Biogas, & Hydropower): Many treatment plants are adopting renewable energy sources such as solar panels, biogas recovery from anaerobic digesters, and small-scale hydropower turbines to offset electricity costs and enhance energy sustainability.
SCADA & Smart Energy Monitoring Systems: Real-time SCADA-based energy management platforms provide detailed insights into power usage trends, peak demand periods, and equipment efficiency. Automated alerts and predictive analytics help prevent energy wastage and optimize load distribution.
Heat Recovery & Cogeneration (CHP) Systems: Combined Heat and Power (CHP) systems allow facilities to capture waste heat from engines, turbines, or digesters and convert it into usable thermal energy for heating or power generation, significantly improving overall energy efficiency.
Leak Detection & Distribution Network Optimization: Water loss from leaks and inefficient distribution systems increases both energy and operational costs. IoT-enabled pressure sensors, smart valves, and real-time monitoring help reduce energy-intensive water loss and improve system-wide efficiency.
Key Purchasing Considerations
When selecting energy management and efficiency solutions, several factors should be evaluated to maximize cost savings, improve performance, and ensure seamless integration into existing infrastructure.
- Energy Savings Potential: Assess potential return on investment (ROI) and long-term energy cost reductions when upgrading equipment.
- System Compatibility: Ensure solutions integrate with existing SCADA, monitoring systems, and automation platforms for real-time energy tracking.
- Operational Flexibility & Scalability: Choose modular energy-saving technologies that can adapt to facility expansions or process upgrades.
- Regulatory Compliance & Incentives: Many state and federal programs offer grants, rebates, and tax incentives for implementing energy-efficient solutions in water treatment operations.
- Maintenance & Lifecycle Costs: High-efficiency systems should reduce maintenance needs and offer long-term durability to minimize total cost of ownership (TCO).
​​Industry Standards & Regulatory Compliance
EPA, AWWA, and State Compliance for Water & Wastewater Treatment
Water and wastewater facilities must comply with federal mandates from the EPA and state-specific water quality control regulations that guide treatment methods, discharge limits, and public safety protocols. Key regulatory frameworks include:
- Requires treatment facilities to meet strict effluent limits for TSS, BOD, nitrogen, phosphorus, heavy metals, and pathogens before discharging to natural water bodies.
- Mandates the use of continuous online analyzers to monitor effluent quality and report exceedances or violations in real-time.
- Facilities must submit Discharge Monitoring Reports (DMRs) and maintain up-to-date compliance logs, subject to EPA or state audits.
- Regulates drinking water treatment plants (DWTPs) to ensure delivery of safe, potable water that meets maximum contaminant levels (MCLs) for lead, arsenic, nitrate, total coliforms, and disinfection byproducts (DBPs).
- Requires continuous measurement of chlorine residuals, pH, fluoride, and TOC, with strict recordkeeping and reporting requirements.
- Includes compliance with the Revised Total Coliform Rule (RTCR) and Stage 2 DBP Rule, both of which necessitate real-time instrumentation for accurate detection and control.
- Mandated by the America’s Water Infrastructure Act (AWIA) for community water systems serving over 3,300 people.
- Requires assessment of physical and cyber threats, and implementation of real-time monitoring, redundant instrumentation, and SCADA security protocols.
- Includes the need for chemical inventory control and fail-safes for critical processes such as disinfection and chemical feed.
Instrumentation Requirements for Compliance Monitoring
- Turbidity Sensors: Required for filtration systems, with EPA limits ≤ 0.3 NTU for most drinking water applications.
- Chlorine Analyzers: Used to monitor free and total chlorine residuals in both water treatment and disinfection processes.
- pH and Conductivity Sensors: Used to ensure water remains within safe acidity/alkalinity ranges and verify proper chemical dosing.
- Nutrient Analyzers: Including ammonia, nitrate, and phosphate analyzers to meet stringent nutrient removal goals under Total Maximum Daily Load (TMDL) programs.
- TOC & BOD Sensors: Required for surface water intakes and biological treatment processes, enabling process optimization and compliance with organic matter limits.
- Flow Meters: Used in compliance with 40 CFR Part 136 for accurate measurement of influent and effluent volumes, necessary for mass loading calculations.
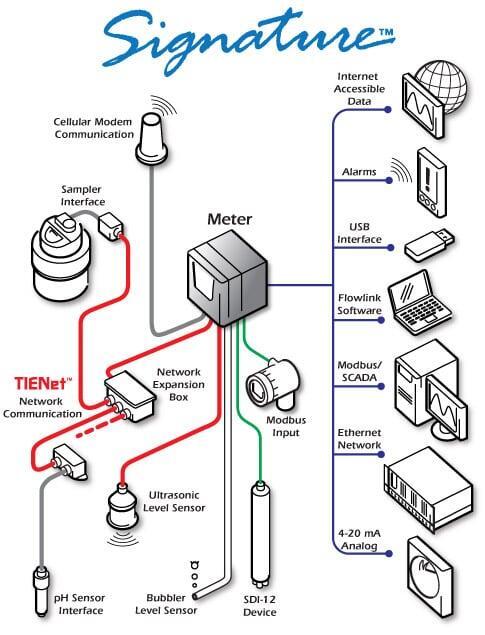
The Signature Effluent Flow Compliance System is a trusted solution for many municipalities and industrial companies worldwide.
State & Local Regulations and Reporting Requirements
- Title 22 (California) and similar state codes outline recycled water quality standards and instrumentation requirements for monitoring coliform, turbidity, and chlorine contact time (CT values).
- Municipal pretreatment programs often require industrial contributors to install flow, pH, and pollutant monitoring equipment at the point of discharge.
- Biosolids handling and disposal are regulated under EPA Part 503 and may require instrumentation to monitor pathogen reduction, vector attraction, and metal concentrations.
Safety & Environmental Sustainability Standards
- OSHA Process Safety Management (PSM) standards apply to chemical storage and dosing systems, requiring monitoring of gas leaks, pressure levels, and chemical feed rates.
- Energy and water conservation programs promote the use of smart sensors and real-time controls to optimize aeration, chemical usage, and pumping efficiency.
- ISO 14001 Environmental Management Systems encourage integration of automated compliance monitoring, emissions tracking, and data transparency for sustainable operations.
​​Benefits of Working With Clipper Controls
​​Case Studies & Success Stories
Explore real-world examples of how Clipper Controls has helped organizations optimize their water and wastewater treatment processes. From improving system efficiency to ensuring regulatory compliance, our case studies highlight the measurable benefits of our expertise and solutions.
Click here to read our water and wastewater case studies.
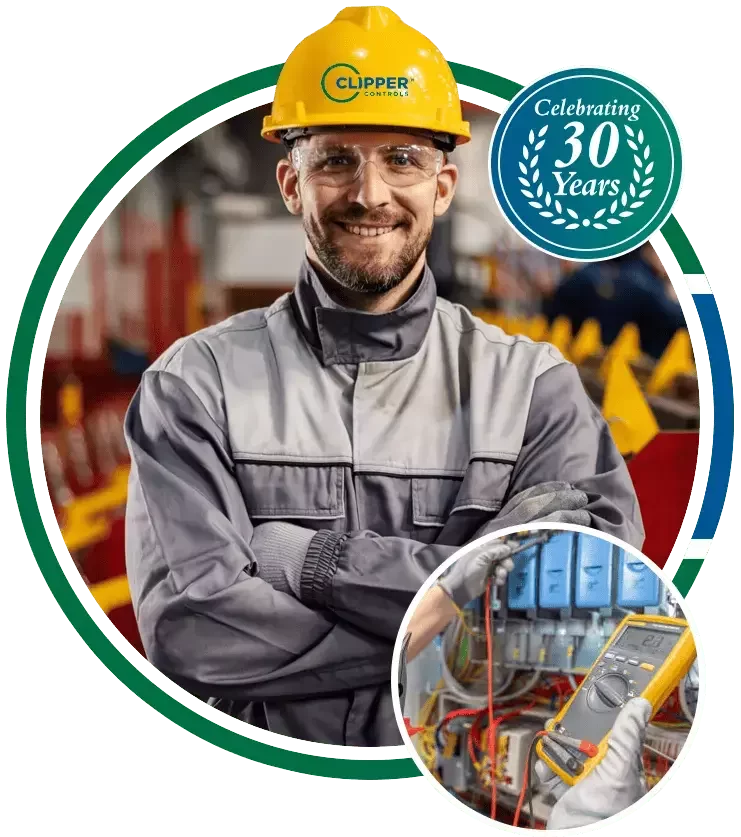
​​Real Results, Real Impact:
Thanks to Clipper Controls, our wastewater treatment plant improved efficiency & compliance with top-tier flow meters. Reliable solutions, great support! We recommend Clipper Controls to all our partner companies.
~ John Smith, Controls Engineer @ ABC Company
Clipper Controls helped our city upgrade water monitoring systems, ensuring accuracy & compliance. Reliable solutions & excellent customer service!
~ Nancy Patel, Procurement @ ABC Company
~ John Smith, Controls Engineer @ ABC Company
Ready to Work With Us?
Quick Page Navigation:
🔹How Our Products Support Your Industry
🔹Key Applications & Solutions
Pressure & Temperature Regulation
Industrial Automation & Remote Process Management
Gas Detection & Environmental Monitoring
Energy Management & Efficiency Solutions
🔹Industry Standards & Regulatory Compliance
🔹Benefits of Working With Clipper Controls