Agriculture & Agribusiness Process Control Applications
Application Overview
Precision instrumentation, controls, and analyzers play a crucial role in agriculture and agribusiness, ensuring efficiency, sustainability, and regulatory compliance in modern farming and food production. Accurate monitoring of water usage, soil conditions, fertilizer application, and climate control optimizes crop yields while minimizing resource waste. Advanced flow meters, pressure sensors, level detectors, and environmental analyzers provide real-time data to automate irrigation, manage greenhouse environments, and ensure optimal conditions for livestock operations and food processing facilities.
In agribusiness, process control solutions enhance storage, transportation, and processing of agricultural products, ensuring quality and safety standards are met. Temperature and humidity sensors maintain ideal conditions for grain storage, while gas detectors and air quality monitors help regulate controlled-atmosphere storage for perishables. Automated fertilizer blending, feed mixing, and wastewater management systems rely on precise flow, pressure, and level control to optimize efficiency and meet environmental regulations. By integrating advanced instrumentation with SCADA and IoT-based monitoring systems, agribusiness operations can reduce operational costs, improve sustainability, and maintain compliance with industry standards.
How Our Products Support Your Industry
Clipper Controls provides advanced instrumentation, automation, and process control solutions tailored for the agriculture and agribusiness industry. Our flow meters, pressure sensors, level detectors, and environmental analyzers help optimize irrigation, fertilizer application, and livestock facility management, ensuring efficient resource use and regulatory compliance.
With expertise in precision monitoring and industrial automation, we support grain storage, food processing, wastewater management, and controlled-environment agriculture. Our SCADA-integrated solutions provide real-time data for climate control, soil moisture monitoring, and chemical dosing, helping agribusinesses reduce waste, improve sustainability, and enhance product quality in an evolving industry.
Key Applications and Solutions
Flow Measurement & Control
Accurate flow measurement and control are essential in agriculture and agribusiness to optimize irrigation, regulate fluid distribution, and improve operational efficiency. Whether managing water for irrigation, monitoring fertilizer and pesticide application, or controlling fluid flow in food processing, precise instrumentation helps reduce waste, conserve resources, and ensure regulatory compliance. Flow meters, control valves, and automated monitoring systems provide real-time data to enhance decision-making and optimize resource allocation. By integrating advanced flow measurement solutions with SCADA, IoT, and remote monitoring technologies, agribusinesses can improve sustainability, lower costs, and enhance productivity.
Applications of Flow Measurement & Control in Agriculture and Agribusiness
Flow measurement plays a critical role in agriculture, irrigation systems, livestock management, and food processing, ensuring precise fluid control for efficiency and compliance. The right instrumentation ensures that water, fertilizers, chemicals, and other liquid resources are used effectively without overuse or waste.
Irrigation & Water Distribution Systems:
Electromagnetic and ultrasonic flow meters measure water flow in canals, pipelines, and drip irrigation systems, ensuring precise water distribution. Flow meters help verify distribution uniformity and support compliance with local water district reporting requirements.
Variable area flow meters regulate flow in central pivot irrigation systems, optimizing crop hydration while reducing water waste.
Remote telemetry systems provide real-time flow monitoring, allowing farmers to adjust irrigation schedules based on actual field conditions.
Fertilizer & Pesticide Application:
Coriolis and turbine flow meters monitor the exact volume of liquid fertilizers and pesticides applied to fields, preventing over-application and runoff contamination.
Automated control valves ensure precise dosing of fertilizers in fertigation systems, optimizing nutrient delivery to crops.
Flow switches detect blockages in spray nozzles and chemical distribution lines, preventing uneven application and wasted resources.
Livestock Watering & Waste Management:
Ultrasonic flow meters track water consumption in automated livestock watering systems, ensuring proper hydration levels for cattle, poultry, and swine.
Positive displacement flow meters regulate the distribution of nutrient-enriched water for dairy and feedlot operations.
Flow measurement systems in manure management help control the transport of liquid waste to treatment facilities, ensuring environmental compliance.
Greenhouse & Hydroponic Systems:
Low-flow Coriolis and thermal mass flow meters monitor nutrient solution circulation in hydroponic farms, ensuring precise delivery to plant roots.
Flow regulators maintain consistent water flow in humidity, misting, and cooling systems, optimizing greenhouse climate control.
Automated dosing pumps with integrated flow sensors adjust pH and nutrient levels in controlled-environment agriculture.
Food & Beverage Processing:
Sanitary flow meters ensure accurate measurement of milk, juices, syrups, and liquid food products during processing and packaging.
Flow controllers regulate liquid transfer in breweries, dairy farms, and grain processing plants, ensuring batch consistency.
Mass flow meters monitor the movement of vegetable oils, syrups, and extracts, preventing loss and ensuring proper formulation.
Key Purchasing Considerations
Selecting the right flow measurement and control technology for agriculture and agribusiness applications requires evaluating fluid properties, environmental conditions, and integration requirements. The following factors should guide decision-making:
Accuracy & Repeatability:
High-accuracy flow meters (e.g., Coriolis and electromagnetic meters) are essential for fertilizer dosing, pesticide application, and hydroponic systems.
Repeatable and stable measurements ensure consistent delivery of water, chemicals, and nutrients across various farming operations.
Environmental Durability & Installation Requirements:
Weatherproof and corrosion-resistant flow meters are necessary for outdoor irrigation systems, wastewater treatment, and chemical applications.
Submersible and inline flow meters provide reliable measurement in high-humidity environments like greenhouses and livestock facilities.
Fluid Type & Flow Characteristics:
Non-contact ultrasonic and electromagnetic meters are ideal for measuring dirty or sediment-laden water in open channel irrigation and runoff systems.
Low-flow Coriolis and positive displacement meters ensure precise measurement in low-volume dosing applications like fertigation and greenhouse misting.
Regulatory Compliance & Sustainability:
Flow meters used in food and beverage processing should meet FDA and 3-A sanitary standards to ensure product safety.
Water conservation regulations require accurate flow monitoring to comply with local and federal water usage guidelines.
Integration with Automation & Data Systems:
Flow sensors with digital communication protocols (e.g., HART, Modbus, BACnet) allow for seamless integration with SCADA, IoT, and remote monitoring systems.
Wireless telemetry flow meters provide real-time flow data for precision farming and automated irrigation control.
Maintenance & Long-Term Reliability:
Non-mechanical, self-cleaning flow meters reduce maintenance needs in irrigation, wastewater, and manure management applications.
Sensors with built-in diagnostics help detect leaks, blockages, and efficiency losses before they become costly issues.
Pressure Monitoring & Regulation
Pressure monitoring and regulation play a vital role in the performance, safety, and longevity of agricultural systems. From irrigation networks and fertigation setups to livestock watering systems and chemical delivery lines, maintaining proper pressure ensures that systems operate efficiently and reliably. Overpressure can damage equipment, cause inconsistent application, or result in safety hazards, while underpressure can lead to system failure or inadequate distribution of water or nutrients. Accurate pressure control is especially critical in drip and micro-irrigation systems, where even small variations can impact crop health and yield.
Pressure instrumentation—such as pressure transducers, gauges, transmitters, and regulators—is also essential in greenhouses, food processing facilities, and manure management systems, where pressurized lines carry water, air, or chemicals. In many cases, pressure monitoring systems are integrated with automated control valves and SCADA platforms to support remote oversight, alarm triggering, and precise adjustments. By leveraging pressure monitoring, agricultural operations can reduce energy waste, improve equipment reliability, and meet compliance and sustainability targets.
Applications of Pressure Monitoring & Regulation in Agriculture and Agribusiness
Pressure control technologies are implemented in a range of agricultural environments to improve system stability and ensure uniform delivery:
Drip and Micro-Irrigation Systems:
Pressure regulators and sensors ensure consistent output across emitters, minimizing variation in water and nutrient delivery.
Maintains optimal pressure range to prevent emitter clogging or bursting.
Pump and Booster Stations:
Pressure transmitters monitor pump performance and control booster operations in large irrigation networks and water transfer systems.
Helps maintain uniform pressure along long distribution lines, especially in uneven terrain.
Greenhouse and Indoor Farming:
Used to control misting, fogging, and climate control systems, where pressure consistency affects humidity, CO₂ delivery, and ventilation.
Prevents system damage and supports energy-efficient environmental control.
Livestock Facilities and Automated Washdown Systems:
Ensures adequate pressure for animal watering systems, disinfectant spraying, and sanitation cycles.
Protects piping, valves, and spray nozzles from wear caused by overpressure or pressure spikes.
Chemical and Fertilizer Injection Systems:
Monitors pressure in fertigation or chemigation lines to ensure consistent dosing accuracy and safe chemical handling.
Enables automatic shutdown in the event of pressure loss or fluctuations.
Key Purchasing Considerations
When selecting pressure monitoring and regulation equipment for agricultural applications, consider the following:
Material Compatibility & Environmental Resistance:
Devices must withstand aggressive chemicals, variable pH, and outdoor exposure (e.g., UV radiation, dust, moisture).
316 stainless steel, PVDF, or polymer housings are common for corrosive or caustic applications.
Sensor Range and Accuracy:
Choose sensors that match the expected operating pressure range with appropriate overrange protection.
High-resolution transmitters are critical in drip and fertigation systems, where pressure differences may be minimal but significant.
Power Requirements & Data Connectivity:
For remote fields, low-power and battery-operated sensors with wireless telemetry or LoRaWAN compatibility are preferred.
For integrated systems, 4–20 mA or Modbus RTU outputs allow seamless SCADA or controller communication.
Ease of Maintenance and Calibration:
Rugged, field-serviceable designs help reduce downtime.
Some models offer built-in diagnostics or zeroing functions to simplify upkeep in harsh environments.
System Integration & Safety Functions:
Look for instruments with programmable alarms, setpoints, or control relays to automate system shutdowns or alerts during abnormal pressure events.
Pressure regulators with built-in relief valves enhance safety in sensitive systems.
Temperature Sensing & Control
Precise temperature sensing and control is essential in modern agriculture and agribusiness to support everything from crop health and post-harvest storage to livestock management and food processing. Temperature fluctuations can have a direct impact on plant development, animal welfare, product shelf life, and energy use, making real-time temperature monitoring a critical component of operational success. Agricultural environments often rely on temperature sensors to automate climate control systems, manage heating and cooling cycles, and ensure compliance with quality and safety standards.
Temperature control systems are widely used in greenhouses, poultry houses, dairy barns, aquaculture operations, and cold storage facilities, where maintaining consistent environmental conditions can dramatically improve outcomes and reduce loss. Integrated with building management systems or SCADA platforms, temperature instrumentation enables automated ventilation, heating, chilling, and alarm triggering to protect assets and optimize production.
Applications of Temperature Sensing & Control in Agriculture and Agribusiness
Temperature monitoring and control play a key role across a wide range of agricultural and food production applications:
Greenhouse and Controlled Environment Agriculture (CEA):
RTDs and thermistors are used to control ventilation fans, heaters, and shade systems, maintaining ideal growing conditions.
Ensures day/night temperature cycling for plant growth and disease prevention.
Livestock Facilities (Poultry, Swine, Dairy):
Temperature sensors help regulate barn heating and cooling systems to maintain animal comfort and productivity.
Automated systems reduce risk of heat stress or hypothermia, improving health and feed conversion rates.
Cold Storage & Post-Harvest Cooling:
Sensors maintain precise temperature control in refrigerated storage units and transport containers, preserving produce, dairy, or meat quality.
Integrated with data logging and alarm systems for HACCP compliance and inventory protection.
Aquaculture and Hydroponics:
Water temperature monitoring is critical in aquaculture tanks and hydroponic reservoirs to support optimal nutrient absorption and oxygen levels.
Systems often tie into chillers or heaters based on real-time feedback.
Food and Beverage Processing:
Temperature control ensures pasteurization, fermentation, and washdown systems operate within safety thresholds.
Essential for quality control and regulatory compliance in value-added processing facilities.
Key Purchasing Considerations
Selecting the right temperature sensing and control equipment for agriculture and agribusiness requires attention to several performance and environmental factors:
Sensor Type & Accuracy:
RTDs (Resistance Temperature Detectors) offer high accuracy and stability for critical applications such as cold storage or processing systems.
Thermistors and thermocouples are suitable for broader field use where faster response times or ruggedness are prioritized.
Environmental Protection & Durability:
Sensors should be rated for moisture, dust, chemical exposure, and outdoor temperature swings.
IP-rated or weatherproof housings are essential for outdoor or washdown environments.
Mounting & Measurement Configuration:
Consider immersion probes, surface sensors, or air temperature sensors depending on the application (e.g., fluid tanks vs. ambient air monitoring).
In livestock or greenhouse settings, non-invasive sensors may be preferred to minimize disturbance and maintenance.
System Integration & Control Output:
Look for models with 4–20 mA, Modbus, or wireless connectivity to enable integration with automation systems.
Temperature controllers should offer setpoint adjustment, alarm outputs, and relay actuation for real-time climate management.
Data Logging & Compliance Features:
For regulated environments, sensors with built-in data logging and traceability support food safety standards like HACCP and FSMA.
Alarms and event history tracking help mitigate risk in perishable goods storage and transport.
Level Detection & Management for Liquids and Bulk Materials
Accurate level detection and management is essential in agriculture and agribusiness operations where liquids, grains, feed, fertilizers, and chemicals are stored, mixed, or distributed. From irrigation water tanks and slurry pits to grain silos and feed hoppers, having real-time visibility into material levels improves inventory control, process efficiency, and safety. Effective level monitoring ensures timely refills, prevents costly overflows or runouts, and supports automated control of pumps, valves, and conveyors.
Facilities that manage liquid fertilizers, pesticides, dairy process water, or animal waste also require level instrumentation that can withstand corrosive, viscous, or foaming media. In bulk storage applications like grain bins or silage bunkers, level sensors help operators monitor usage trends and reduce manual checks, while integrated systems support remote monitoring and real-time decision-making across distributed sites. SCADA-ready solutions and rugged sensors are key in ensuring accuracy and durability in harsh or variable agricultural environments.
Applications of Level Detection & Management in Agriculture and Agribusiness
Level sensors and controllers are widely used in both liquid and solid material management throughout agricultural operations. These applications span liquid handling, chemical dosing, grain storage, feed distribution, and waste containment, each requiring different types of sensors and integration depending on the material characteristics and environmental conditions.
Irrigation Water Tanks & Pump Systems: Water storage tanks are common in both open-field and greenhouse operations, where water is drawn from wells, canals, or collected rainwater systems. Submersible pressure transducers or ultrasonic level sensors are used to monitor tank levels in real time, ensuring that pumps do not run dry, irrigation schedules are met, and water usage is optimized. These sensors can also trigger automated valve control or pump shutoff when levels fall below safe thresholds.
Liquid Fertilizer, Herbicide, and Pesticide Storage Tanks: Bulk storage tanks containing ammonium nitrate, urea solutions, glyphosate, or other agricultural chemicals require precise, non-contact level measurement due to corrosive properties, fumes, and the presence of foam. Radar or guided wave radar sensors are ideal for these applications, offering accurate readings even in vaporous, sticky, or agitated environments. This helps prevent overfilling, supports safe chemical blending, and enables automated refill alerts for mobile spraying units.
Grain Silos, Feed Bins, and Bulk Solid Storage: In animal agriculture and commodity storage facilities, level measurement is vital to prevent overfilling during pneumatic truck deliveries and to manage inventory for automated feed distribution systems. Radar and laser level sensors, resistant to dust and vibration, provide continuous readings of grain height and feed quantities. This data is also used to forecast consumption rates and trigger restocking before supplies run out—reducing labor and avoiding costly feed interruptions.
Manure Pits, Slurry Tanks, and Lagoons: Livestock operations generate large volumes of waste that must be stored, treated, or reused responsibly. Slurry pits and lagoons are monitored with robust ultrasonic or hydrostatic level sensors to detect rising levels that may signal the need for pump-out or spreading. These sensors must operate in high-solid, fibrous, or corrosive media, often in outdoor, unprotected environments. Accurate readings help avoid environmental violations by preventing unintentional overflows into surrounding land or water systems.
Milk Tanks, Mixing Vats, and CIP (Clean-in-Place) Systems in Dairy Processing: In dairy and food production facilities, maintaining strict control over tank levels is essential for batch integrity, process consistency, and regulatory compliance. Sanitary-grade capacitance or radar sensors monitor levels in milk silos, cream separators, and ingredient mixing vats. In CIP systems, level sensors confirm cleaning fluid volumes and transitions between rinse, wash, and sanitize phases, helping meet FDA and USDA standards for cleanliness and traceability.
Aquaculture & Hydroponics Systems: In aquaculture tanks and nutrient solution reservoirs, continuous level monitoring ensures proper water volumes are maintained for fish health and root system immersion. These systems often experience fluctuating flow and can be prone to biofilm or sediment buildup, so non-contact ultrasonic sensors or self-cleaning pressure transducers are often selected for long-term stability and minimal maintenance.
Key Purchasing Considerations
When choosing level instrumentation for agricultural use, operators should evaluate several important factors to ensure long-term performance and reliability:
Type of Media and Application Environment:
Liquids, slurries, and bulk solids all require specific sensor technologies, such as float switches, hydrostatic, radar, or capacitance.
Consider chemical compatibility, solids content, and presence of foam, dust, or vapor.
Mounting Flexibility and Installation Constraints:
Choose sensors that suit the tank geometry, venting, and access points.
Compact or remote-mounted designs are beneficial for tight spaces or high tanks.
Signal Output and System Integration:
Look for sensors with analog (4–20 mA), relay, Modbus, or wireless outputs to integrate with existing SCADA or irrigation automation systems.
Battery-powered and solar-compatible options are ideal for remote field deployments.
Sensor Durability and Maintenance Requirements:
Sensors should be rated for IP67 or higher for dust and water resistance.
Self-cleaning capabilities or non-stick coatings may be beneficial in slurry or sticky feed materials.
Accuracy and Range:
Ensure the chosen technology can handle the height and material density range of your storage system.
Non-contact sensors are ideal for deep silos or tanks with aggressive or sanitary media.
Gas & Environmental Monitoring for Safety & Compliance
Agriculture and agribusiness operations are increasingly adopting gas detection and environmental monitoring systems to support worker safety, regulatory compliance, air quality control, and environmental stewardship. Whether managing animal housing facilities, fertilizer storage areas, grain silos, or composting sites, exposure to hazardous gases like ammonia (NH₃), methane (CH₄), hydrogen sulfide (H₂S), and carbon dioxide (CO₂) presents serious risks to both personnel and livestock. Simultaneously, environmental regulations require monitoring of dust, greenhouse gas emissions, and ambient air quality, especially in large-scale livestock or crop operations.
By implementing fixed or portable gas detectors, air quality analyzers, and environmental sensors, agricultural operators can detect unsafe conditions early, trigger automated responses, and maintain compliance with OSHA, EPA, and local agricultural air quality standards. In addition, integrated monitoring systems provide historical data for regulatory reporting, emissions control planning, and sustainability certifications.
Applications of Gas & Environmental Monitoring in Agriculture and Agribusiness
Gas detection and environmental sensing are essential in various agricultural applications where harmful gases or environmental hazards may arise:
Livestock Housing (Poultry, Swine, and Dairy Facilities): High-density animal confinement areas often experience the accumulation of ammonia from waste, carbon dioxide from respiration, and methane from anaerobic decomposition. Fixed gas monitors installed in barns and enclosures measure gas levels and trigger ventilation fans, alarms, or feed system adjustments to protect animal health and worker safety. Prolonged exposure to even moderate levels of ammonia or CO₂ can result in respiratory issues, reduced animal performance, and OSHA violations.
Anaerobic Digesters and Manure Handling Systems: Biogas systems and slurry storage produce methane and hydrogen sulfide, which are flammable and toxic at low concentrations. Continuous gas monitoring ensures safe operation of digesters, gas flares, and storage lagoons. Sensors integrated into SCADA systems help operators detect leaks, ensure proper gas capture, and monitor oxygen levels in confined areas before maintenance entry.
Grain Storage & Milling Facilities: Dust accumulation and spoilage in grain bins or silos can lead to combustible dust explosions or CO₂ buildup from fermentation. Gas and dust monitors are used to measure oxygen displacement, monitor CO₂ levels, and ensure compliance with NFPA 61 standards for combustible dust control. Many facilities also monitor ambient temperature and humidity to prevent grain degradation and mold growth.
Greenhouses & Indoor Grow Environments: CO₂ is commonly injected to stimulate plant growth, but concentrations above safe levels can pose risks to workers. CO₂ sensors help maintain optimal enrichment levels while ensuring safety compliance. Additionally, airflow, humidity, and temperature sensors are used to maintain controlled conditions critical to crop quality and yield.
Fertilizer & Pesticide Storage Areas: Improper storage or spills of nitrogen-based fertilizers and fumigants can lead to the release of hazardous gases like nitrous oxide or phosphine. Gas detection in these areas ensures early identification of leaks, preventing environmental harm and accidental overexposure to workers.
Composting & Organic Waste Sites: Composting operations release volatile organic compounds (VOCs), ammonia, and methane during decomposition. Environmental monitors help track air quality near the site boundary to meet local emissions thresholds and provide data for community transparency or permit compliance.
Key Purchasing Considerations
When selecting gas and environmental monitoring equipment for agricultural applications, it’s important to consider the unique challenges of the farm or facility environment:
Target Gases and Required Detection Ranges:
Choose sensors capable of detecting specific gases present in your operation: NH₃, H₂S, CH₄, CO₂, VOCs, or O₂ deficiency.
Ensure that measurement ranges align with both occupational exposure limits and operational control thresholds.
Sensor Durability and Environmental Protection:
Devices must withstand exposure to dust, moisture, extreme temperatures, and corrosive gases.
Look for enclosures with IP65+ ratings and sensors designed for ammonia and H₂S resistance.
Integration and Alarm Capabilities:
Select sensors with 4–20 mA, Modbus, or wireless outputs to integrate with SCADA, PLC, or ventilation control systems.
Audible/visual alarms or relay outputs are useful for triggering fans, dampers, or emergency shutdowns.
Power and Portability Requirements:
Fixed detectors are ideal for continuous monitoring in barns or storage rooms.
Portable gas detectors are necessary for confined space entry or mobile spot-checks.
Maintenance, Calibration, and Replacement Costs:
Choose sensors with automated calibration options or field-replaceable cartridges to reduce maintenance burden.
Some agricultural gases, like H₂S, degrade sensors quickly—select equipment designed for high-concentration environments.
Regulatory and Certification Compliance:
Ensure equipment meets OSHA PELs, NIOSH, NFPA, and EPA guidelines.
Look for UL, ATEX, or CSA certifications if installed in potentially explosive or hazardous zones.
Analytical Instrumentation for Agricultural Process Optimization
Modern agriculture and agribusiness operations are increasingly dependent on analytical instrumentation to drive data-informed decision-making, process efficiency, and environmental sustainability. These instruments help monitor key physical and chemical parameters—such as pH, conductivity, dissolved oxygen, nutrient concentration, and turbidity—across a wide range of applications including irrigation, hydroponics, soil analysis, wastewater management, and fertilizer blending.
Analytical sensors and analyzers support both precision agriculture and post-harvest processing, enabling farmers and facility managers to optimize resource use, improve crop yields, and meet regulatory and quality standards. Whether deployed in the field, integrated with fertigation systems, or installed in food processing and dairy facilities, these tools play a critical role in maximizing productivity while minimizing waste and environmental impact.
Applications of Analytical Instrumentation in Agriculture and Agribusiness
Analytical instrumentation supports a wide range of high-value applications across the agriculture and agribusiness landscape by providing real-time chemical and physical insights into the materials, water, and processes involved in food and crop production. These tools enable precise control, compliance assurance, and data-driven optimization in a variety of environments:
Fertigation & Nutrient Management in Field Crops: In precision agriculture, inline nutrient analyzers are used in fertigation systems to measure nitrate (NO₃⁻), phosphate (PO₄³⁻), potassium (K⁺), and pH levels in real time as water and nutrients are delivered through irrigation lines. This allows growers to dynamically adjust dosing to match crop demand and soil absorption rates. Conductivity sensors provide a quick assessment of total dissolved solids, giving operators a baseline indication of nutrient concentration before it reaches the root zone.
Greenhouse and Hydroponic System Control: In hydroponic or controlled environment agriculture (CEA), plant roots are immersed in or misted by water-based nutrient solutions. These systems use a suite of analytical instruments to monitor electrical conductivity (EC), pH, dissolved oxygen (DO), and oxidation-reduction potential (ORP). Maintaining stable values is critical to nutrient uptake, root respiration, and pathogen control. For instance, DO sensors ensure sufficient oxygen in water to prevent root rot, while pH sensors prevent nutrient lockout.
Soil Health Monitoring in Precision Farming: Portable soil analyzers are used before planting or between growing cycles to assess macro and micronutrient availability, salinity, and acidity/alkalinity (pH). This information supports variable-rate application of fertilizers and lime, helping growers avoid nutrient excess or deficiency. Some systems pair with GPS-enabled tools to create soil nutrient maps that guide automated spreaders and irrigation systems for maximum efficiency.
Water Quality Control for Irrigation Sources: When using surface water, reclaimed water, or well water, growers must monitor for pH, turbidity, suspended solids, and salinity to protect crops and prevent emitter clogging or salt buildup in soil. Real-time analyzers installed at pump stations or in-line with drip systems allow operators to trigger alarms or filtration steps when thresholds are exceeded. Turbidity sensors, for example, can detect silt that may damage emitters, while salinity meters help avoid stress in salt-sensitive crops.
Livestock & Dairy Effluent Monitoring for Regulatory Compliance: Large livestock operations must treat or manage manure lagoon effluent before land application or discharge. Analytical instruments monitor ammonia (NH₃), nitrate, total nitrogen (TN), phosphorus, chemical oxygen demand (COD), and pH to ensure nutrient loads remain within permitted levels. This data is also critical to support nutrient management plans (NMPs) and protect downstream ecosystems from nutrient leaching or algal blooms.
Dairy and Food Processing Facilities: In value-added agribusiness operations such as milk processing, produce washing, or meat handling, analytical instruments monitor process parameters like product temperature, turbidity, pH, and organic load (TOC/BOD) in both the production and wastewater streams. In Clean-in-Place (CIP) systems, analyzers ensure that sanitizers are applied at the correct concentration and that rinse water meets quality targets before final product contact resumes. This ensures regulatory compliance and product safety.
Compost Quality and Environmental Impact Management: In composting operations, temperature, moisture, and ammonia/VOC emission levels are monitored to optimize decomposition and minimize odor complaints or emissions violations. Instruments may also be used to assess final compost maturity and nutrient content, supporting quality control for on-farm reuse or off-site sale.
Aquaculture Systems within Agribusiness Settings: For farms raising fish or shellfish as part of integrated operations, analytical instrumentation monitors DO, pH, salinity, temperature, and ammonia levels to maintain healthy aquatic environments. These parameters are closely managed to maximize feed conversion efficiency, reduce stress, and prevent disease outbreaks.
Key Purchasing Considerations
Choosing the right analytical instrumentation depends on your application, environment, and data integration needs. Here are key considerations:
Parameter Specificity & Measurement Range:
Select instruments based on the specific chemical or physical parameter being measured (e.g., nitrate, pH, turbidity).
Ensure the measurement range aligns with expected concentrations in water, soil, or process fluid.
Sensor Accuracy & Response Time:
In fast-changing systems like fertigation or hydroponics, sensors must provide real-time, high-resolution data for effective control.
Stability and repeatability are critical for reliable automation.
Environmental Conditions & Durability:
Instruments used in outdoor, high-moisture, or corrosive environments (e.g., manure pits or chemical tanks) must be rugged, sealed, and chemically compatible.
Look for IP-rated housings, self-cleaning sensors, and materials resistant to fouling.
Integration with Control Systems:
Choose devices with Modbus, 4–20 mA, or wireless connectivity to tie into irrigation controllers, SCADA systems, or automation platforms.
Some advanced analyzers support data logging, cloud access, or mobile app integration.
Calibration & Maintenance Requirements:
Evaluate how often sensors need calibration, cleaning, or replacement, especially for critical parameters like pH or nitrate.
Consider models with pre-calibrated cartridges or auto-calibration features for ease of maintenance.
Regulatory Compliance & Data Reporting:
For applications subject to environmental permits or food safety audits, choose instruments that store historical data and support audit trails.
Ensure instruments align with local and federal standards (e.g., EPA discharge limits or USDA food processing guidelines).
Industry Standards & Regulatory Compliance
Agriculture and agribusiness operations are increasingly governed by a combination of federal, state, and local regulations, alongside industry-specific standards designed to ensure environmental sustainability, food safety, water conservation, and worker health. Regulatory oversight impacts areas such as water usage, nutrient runoff, livestock emissions, pesticide application, waste handling, and energy consumption. Compliance is essential not only for legal operation and eligibility for subsidies or grants, but also for maintaining public trust, food supply integrity, and ecosystem health.
Instrumentation and process control systems play a vital role in helping farms and agribusinesses meet these growing compliance requirements. By integrating flow meters, gas detectors, nutrient analyzers, and automation platforms, operators can ensure accurate monitoring, data collection, and system responses aligned with both operational targets and regulatory mandates.
Key Regulatory Frameworks and Standards in Agriculture & Agribusiness
Environmental Protection Agency (EPA) – Clean Water Act (CWA): Under the National Pollutant Discharge Elimination System (NPDES), large farms and food processing facilities must monitor runoff, discharge water, and effluent quality, especially when dealing with animal waste or nutrient-laden process water. Flow meters, pH probes, and nutrient analyzers help ensure compliance with discharge permits and watershed protection plans.
EPA – Clean Air Act (CAA) & Air Quality Regulations: Concentrated Animal Feeding Operations (CAFOs) and large compost or manure systems may be subject to air quality monitoring under local and federal guidelines, especially for emissions of ammonia, methane, hydrogen sulfide, and volatile organic compounds (VOCs). Facilities may be required to install continuous gas monitoring systems and report emissions levels annually.
OSHA Agricultural Safety Standards (29 CFR 1928): OSHA enforces workplace safety in agricultural operations, including requirements for confined space entry, gas detection, chemical handling, and process safety management. Proper use of sensors and control systems supports compliance by ensuring real-time monitoring of hazardous conditions.
Natural Resources Conservation Service (NRCS) Standards: NRCS programs often require precision irrigation water measurement, fertilizer application tracking, and runoff control verification to maintain eligibility for EQIP and CSP funding programs. Measurement tools such as flow meters, soil moisture sensors, and nutrient monitors are often essential for reporting compliance.
State-Level Water & Fertilizer Regulations (e.g., CA SB 88): States like California require flow measurement and annual reporting for all water right holders diverting more than a specific threshold volume. Fertilizer use is increasingly regulated to reduce nitrate contamination, requiring monitoring tools for fertigation and irrigation management.
Ensuring Compliance with Environmental & Food Safety Regulations
Maintaining regulatory compliance in agriculture involves monitoring water conservation, nutrient runoff, emissions, and food production safety. Flow meters, chemical analyzers, air quality sensors, and automated monitoring systems help agribusinesses adhere to EPA water discharge permits, FDA food safety guidelines, and HACCP contamination prevention standards. Precision controls in pesticide spraying, manure management, and fertilizer application prevent overuse and contamination, ensuring compliance with NPDES (National Pollutant Discharge Elimination System) and Clean Water Act regulations. In food and beverage production, real-time temperature, pressure, and level monitoring ensures products meet FSMA (Food Safety Modernization Act) and GMP (Good Manufacturing Practice) requirements for processing, storage, and distribution.
Sustainable Practices and Precision Agriculture Innovations
Certifications and Industry Guidelines
GlobalG.A.P., USDA Organic, and LEED for Agriculture: Voluntary certifications may require instrumentation to validate environmental controls, process repeatability, and traceability. These certifications are key for accessing certain export markets or fulfilling retailer sourcing requirements.
ISO 22000 (Food Safety Management) and ISO 14001 (Environmental Management): Agribusiness operations seeking global recognition often adopt ISO standards that necessitate automated data logging, environmental monitoring, and process validation—all supported by the integration of instrumentation and control systems.
Key Takeaway:
By implementing instrumentation and process control solutions that align with these regulatory frameworks, agricultural operations can ensure compliance, optimize resource use, reduce environmental impact, and future-proof their operations against evolving policy landscapes. Clipper Controls provides tools and expertise to help farmers and agribusinesses meet these requirements with confidence, accuracy, and operational transparency.
Benefits of Working With Clipper Controls
Clipper Controls provides advanced instrumentation and automation solutions tailored for agriculture and agribusiness applications. Our flow meters, level sensors, pressure monitors, and analytical instruments ensure efficient water management, precision chemical application, and regulatory compliance. We help optimize irrigation, food processing, and environmental monitoring for improved productivity.
By partnering with Clipper Controls, agribusinesses gain access to cutting-edge monitoring and control technologies that integrate seamlessly with SCADA, IoT, and precision agriculture systems. Our expert support, high-quality instrumentation, and real-time data solutions enhance resource efficiency, sustainability, and food safety compliance. With our solutions, you can reduce waste, improve process control, and maximize operational efficiency.
Case Studies & Success Stories
Explore how Clipper Controls has helped agriculture and agribusiness operations optimize water management, precision fertilization, and food processing efficiency.
Click here to read our agriculture & agribusiness case studies.
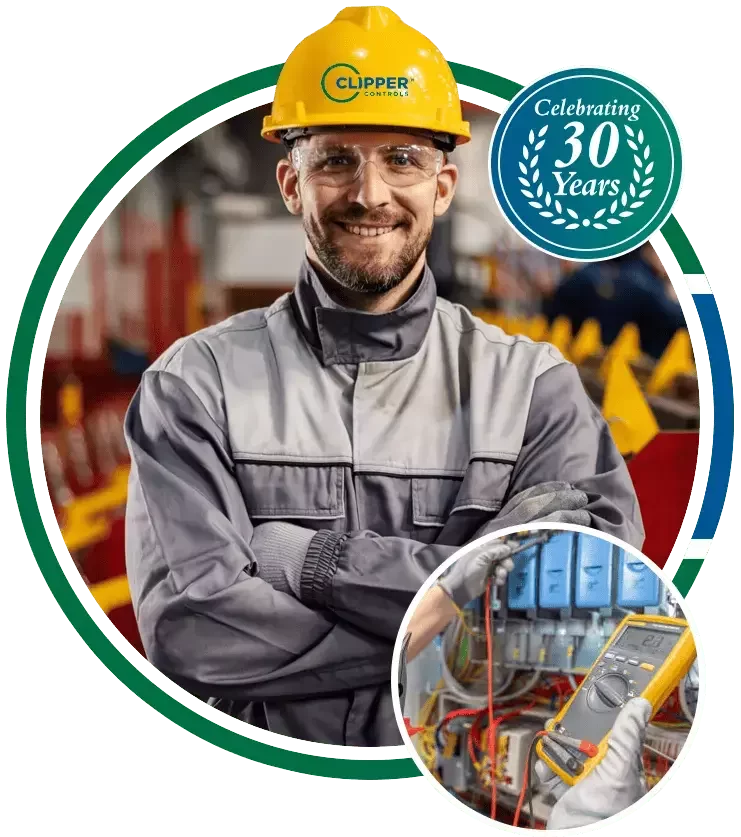
Real Results, Real Impact:
Thanks to Clipper Controls, our wastewater treatment plant improved efficiency & compliance with top-tier flow meters. Reliable solutions, great support! We recommend Clipper Controls to all our partner companies.
~ John Smith, Controls Engineer @ ABC Company
Clipper Controls helped our city upgrade water monitoring systems, ensuring accuracy & compliance. Reliable solutions & excellent customer service!
~ Nancy Patel, Procurement @ ABC Company
~ John Smith, Controls Engineer @ ABC Company
Ready to Work With Us?
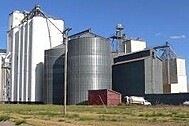
Quick Page Navigation:
🔹How Our Products Support Your Industry
Flow Measurement & Control
Pressure Monitoring & Regulation
Gas & Environmental Monitoring
Analytical Instrumentation for Process Optimization
🔹Industry Standards & Regulatory Compliance
🔹Benefits of Working With Clipper Controls