
Precision Level Measurement & Control Solutions
At Clipper Controls, we offer a comprehensive range of precision level measurement and control solutions designed to meet the demanding needs of industrial processes. Whether you're working with liquids, solids, or interfaces, our technologies deliver accurate, reliable performance in a wide variety of environments. From continuous and point level measurement to advanced interface detection, we provide the instrumentation and expertise to help you maintain safety, improve efficiency, and ensure process consistency. Explore our range of level measurement and control instrumentation below:
Continuous Level Measurement
Radar Level
Application: Radar level devices use microwave signals to provide accurate, non-contact level measurement in liquids, solids, or slurries. Ideal for challenging conditions such as high pressure, temperature, vapor, or dust.

Ultrasonic Level
Application: Ultrasonic level sensors use high-frequency sound waves for non-contact level measurement in tanks, bins, and open channels. Reliable for liquids and solids in clean, stable environments.
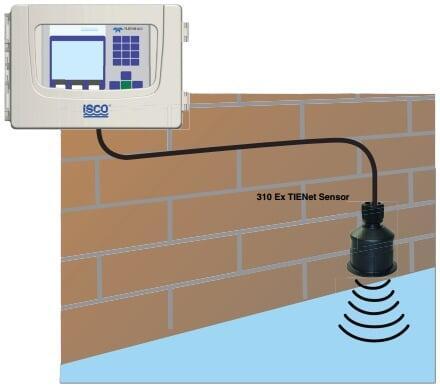
Bubbler Level
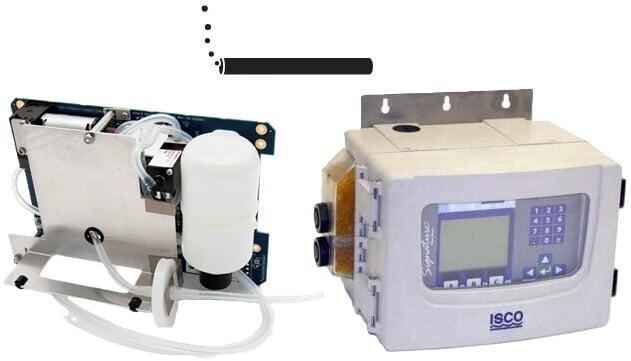
Pressure Level
Application: Pressure level devices calculate level by measuring the hydrostatic pressure at the bottom of a tank or vessel. Suitable for pressurized or open systems, and compatible with many liquid types.
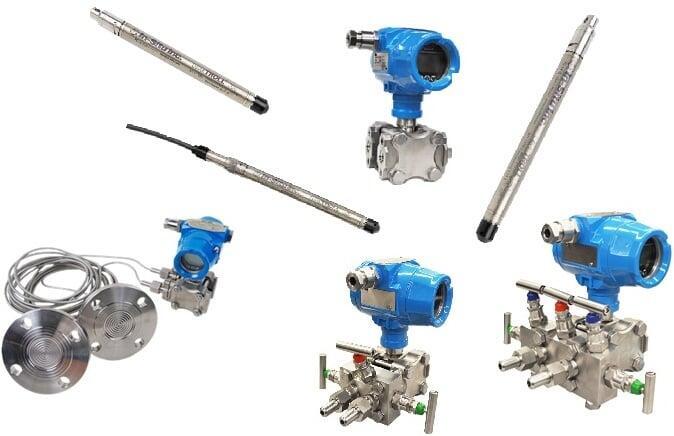
Capacitance Level
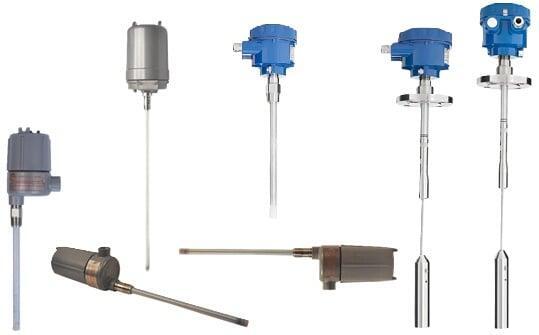
Vision Level
Application: Vision-based systems provide level detection using optical cameras or sensors. Used in specialty applications requiring visual confirmation or analysis of level and interface layers.
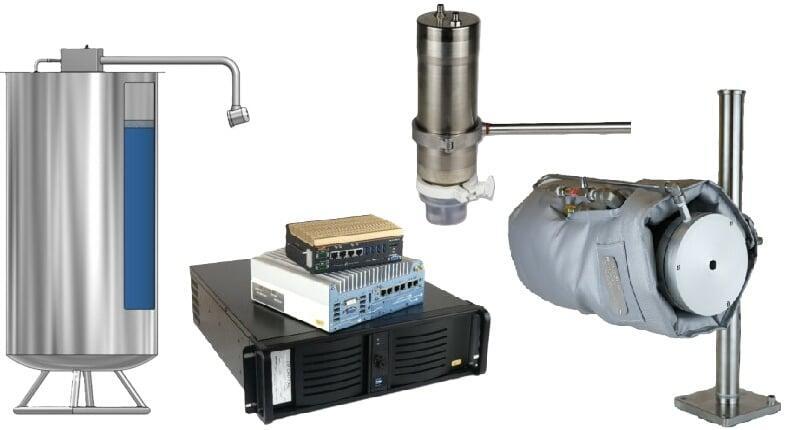
Plumb Bob Level
Magnetic Level
Application: Magnetic level indicators (MLIs) provide visual and/or remote level indication using a float with magnetic coupling. Ideal for high-pressure or hazardous liquid applications.
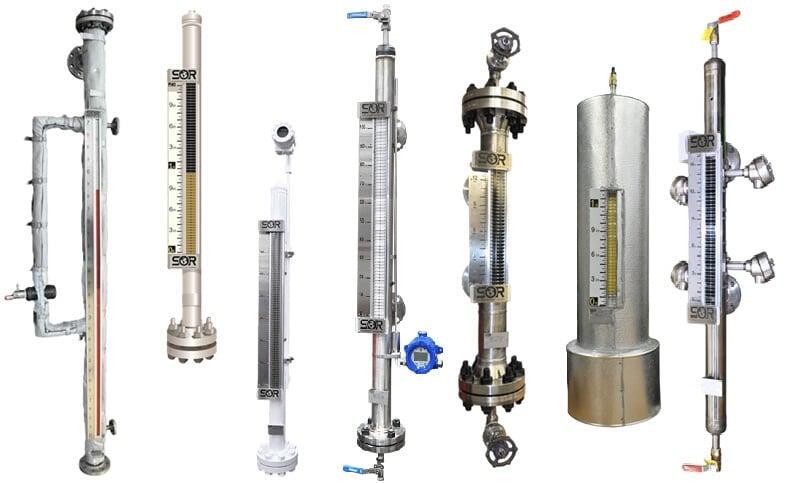
Point Level Measurement
Mechanical Float Level
Application: These devices use a tethered float to mechanically actuate a switch or indicator. They are rugged, economical solutions for basic on/off or visual level control.
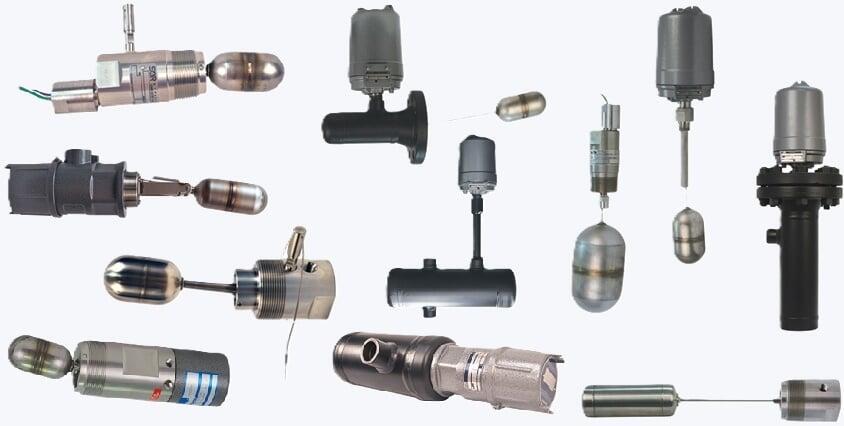
Mechanical Displacer Level
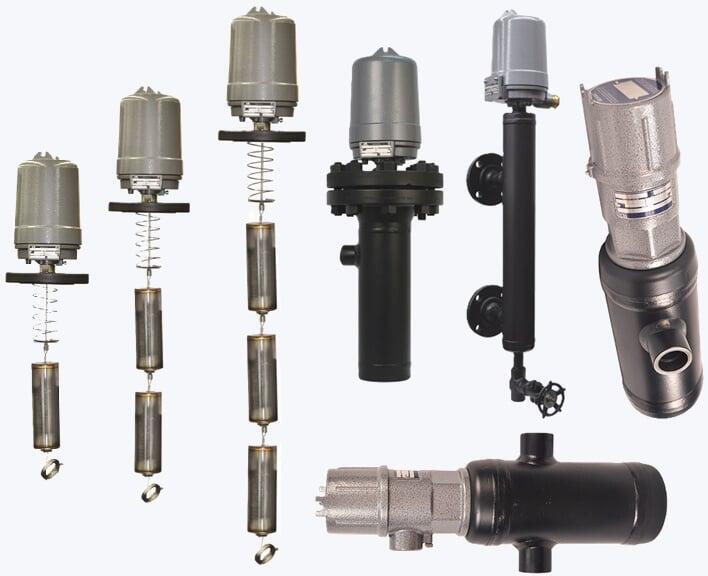
Ultrasonic Gap Level
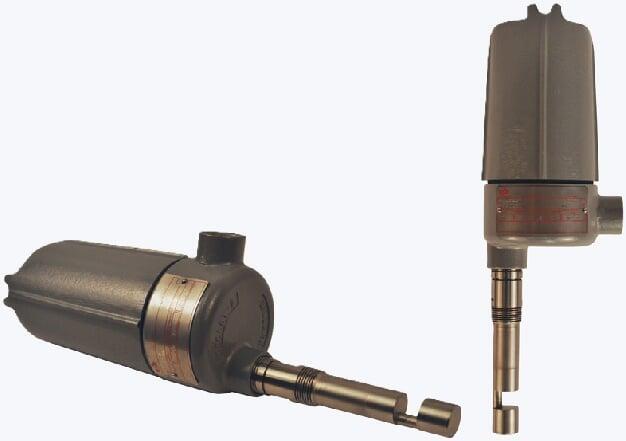
Vibration Fork Level
Application: Tuning fork sensors vibrate at a set frequency and detect level when immersed in material. Common in fail-safe point level detection for liquids or fine solids.
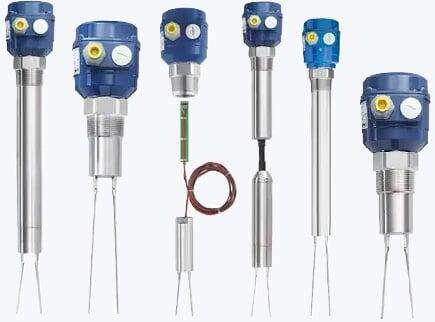
Vibration Rod Level
Application: Like vibration forks, these sensors vibrate and detect level upon dampening. Suitable for point level detection in powders and bulk solids, especially in silos.
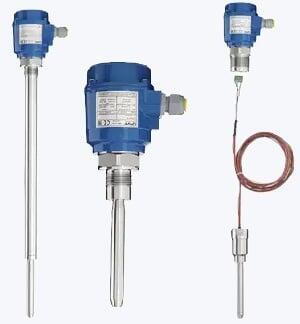
Thermal Level
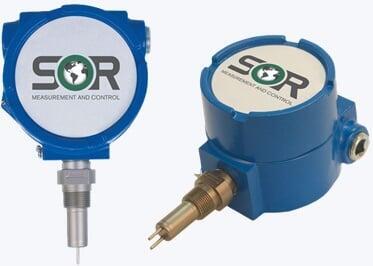
Capacitance Level
Application: Capacitance probes detect level by measuring changes in electrical capacitance between the sensor and tank wall. Effective for both liquid and bulk solids, especially where space is limited.

Rotating Paddle Level
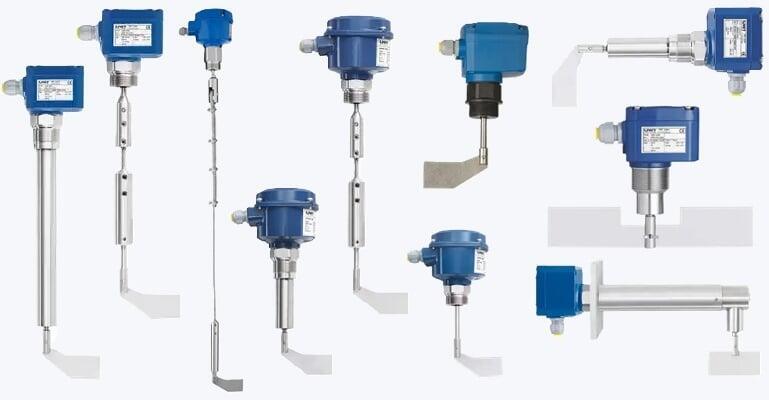
Liquid-Liquid Interface Level Measurement
Guided Wave Radar Level
Application: GWR instruments transmit microwave pulses along a probe to detect level. Known for high accuracy in challenging conditions, including foam, vapor, or varying dielectric media.
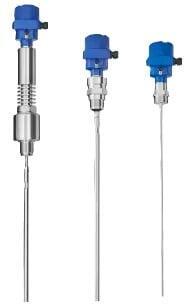
Liquid-Solid Interface Level Measurement
Plumb Bob Level
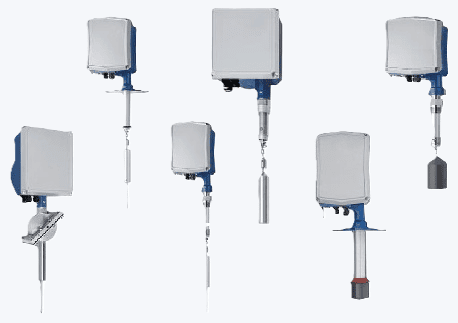
Infrared Attenuation Level
Application: Sonar systems use acoustic waves to detect level in bulk solids, slurries, or liquids. Ideal for deep, dusty, or turbulent environments where other sensors may struggle.
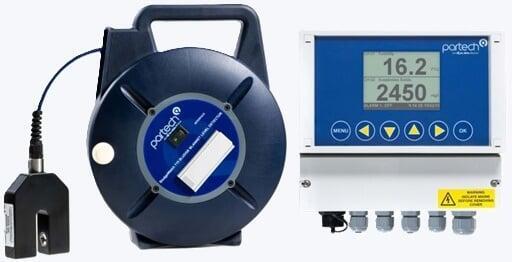
Need Help?
Our Crew is Here To Serve You!
Level Technology Comparison Table
Technology | Contact / Non-Contact | Best Suited For | Advantages | Limitations |
---|---|---|---|---|
Radar | Non-Contact | Liquids, Solids, Vapors, Harsh Environments | Highly accurate, works in vapor/foam | May require calibration |
Ultrasonic | Non-Contact | Liquids, Simple Solids, Open Channels | Cost-effective, easy setup | Affected by vapor, temperature, and turbulence |
Bubbler | Contact | Liquids with High Contamination or Viscosity | Simple and reliable, no moving parts | Requires air supply, slow response time |
Hydrostatic Pressure | Contact | Liquids in Ventilated Tanks, Wells | Low cost, good for deep tanks | Affected by temperature/density changes |
Capacitance | Contact | Liquids or Solids (Conductive/Non-Conductive) | Versatile, compact, no moving parts | May need calibration for media type |
Float | Contact | Basic Water and Utility Applications | Mechanical simplicity, low cost | Limited accuracy, mechanical wear |
Plumb Bob | Contact | Bulk Solids, Powders, Tall Silos | Ideal for dusty/dirty solids | Slow measurement cycle |
Guided Wave Radar | Contact | Interfaces, High Temp/Pressure Liquids | Excellent for challenging fluids & interfaces | Requires clean probe area, dielectric dependency |
Vision-Based | Non-Contact | Visual Level, Foam Detection, Stratified Layers | Real-time imaging, intuitive verification | Requires line-of-sight, cleaning system |
Vibration Fork/Rod | Contact | Point Level for Powders or Liquids | Reliable point level, unaffected by dust/foam | Not for continuous measurement |
Thermal Dispersion | Contact | Liquid Interfaces, High/Low Point Detection | Works in extreme temperatures and viscosity | Limited to clean or homogenous media |
Mechanical Displacer | Contact | Liquids and Interfaces in High Pressure/Temperature Vessels | Simple design, high-temperature/pressure capability | Mechanical wear, not suitable for fast-changing levels |
Ultrasonic Gap | Contact | Point level detection in clean liquids | No moving parts, reliable in sanitary applications | Not suitable for solids or dirty fluids |
Rotating Paddle | Contact | Bulk solids like grain, cement, plastic pellets | Cost-effective, easy to install and maintain | Not suitable for liquids, mechanical parts may wear |
Infrared Attenuation | Non-Contact | Foam detection, interface monitoring | Non-intrusive, visual and level data combined | Requires clear optical path, may need cleaning |
Level Measurement & Control Product Applications
Water & Wastewater Treatment
Water and wastewater treatment facilities rely heavily on accurate level measurement and control to manage tank levels, prevent overflows, and ensure consistent process flow through various treatment stages. Applications range from open channel flow monitoring and lift station control to sludge blanket detection and chemical dosing. Unique challenges in this industry include exposure to high humidity, foam, corrosive chemicals, variable tank geometry, and suspended solids—conditions that require robust and often non-contact solutions. Additionally, proper instrumentation plays a critical role in compliance with environmental regulations and in optimizing energy and chemical usage throughout the treatment cycle.
Recommended Level Products for Water & Wastewater Treatment
Fuel & Chemical Storage Tanks
Recommended Level Products for Fuel & Chemical Storage Tanks
Agricultural Irrigation & Fertilizer Systems
Recommended Products for Agricultural Irrigation & Fertilizer Systems
UWT Capanivo® CN 7000
Food & Beverage Processing
Recommended Products for Food & Beverage Processing
Mining & Mineral Processing
Recommended Products for Mining & Mineral Processing
Power Generation & Utility Systems
Recommended Products for Power Generation & Utility Systems
Stormwater, Environmental, & Coastal Monitoring
Recommended Products for Stormwater, Environmental, & Coastal Monitoring
Renewable Energy (Biogas, Solar Thermal, Biofuels)
Recommended Products for Renewable Energy Applications
Terms & Definitions
Understanding level measurement starts with the right terminology. Below are commonly used terms in the world of level sensing and control:
Accuracy:
The degree to which the measured value conforms to the actual level. Often expressed as a percentage of the span.
Calibration:
The process of setting or adjusting a level measurement device to ensure its output accurately reflects the true level. Calibration accounts for factors like sensor drift, installation variances, and environmental conditions.
Dead Band (Blanking Distance):
A zone near the sensor in which level cannot be measured accurately due to signal interference or design limitations.
Density:
Mass per unit volume of a material. Plays a role in pressure and float-based level measurement techniques.
Dielectric Constant (Relative Permittivity):
A material property affecting how radar or capacitance signals travel through it. Critical in radar and capacitance measurement accuracy.
Echo Loss:
In radar and ultrasonic systems, this refers to the loss of signal reflection caused by foam, turbulence, or low dielectric materials.
Hazardous Location (HazLoc):
An area with potential explosion risks due to flammable gases, vapors, or dust—requires certified sensors (e.g., ATEX, IECEx, FM).
Interface (in level measurement):
The boundary between two different materials, such as oil and water, which have different densities.
Mounting Orientation:
The physical positioning of a sensor (top-mounted, side-mounted, bottom-mounted), which affects installation and signal performance.
Repeatability:
The sensor's ability to produce consistent results under the same conditions over repeated measurements.
Resolution:
The smallest detectable change in level that a sensor can measure.
Response Time:
The amount of time it takes for a level sensor to respond to a change in level.
Span:
The range between the minimum and maximum levels a measurement device is calibrated to measure.
Turbulence:
Unstable or mixed material surface behavior that can cause signal scattering or inaccuracies in level reading.
Vapor Space:
The area in a tank above the liquid or material, which may contain vapors or gases that affect some measurement technologies.
Zero Point:
The reference level at which the device starts measuring (often the bottom of a tank or vessel).