Life Science Process Control Applications
Application Overview
How Our Products Support Your Industry
Key Applications and Solutions
Flow Measurement & Control
Applications of Flow Measurement & Control in Life Science Manufacturing
Flow control plays a vital role in critical life science applications, ensuring precise material delivery, optimizing reaction conditions, and maintaining sterile process environments. The right instrumentation helps regulate flow rates in both liquid and gas applications while ensuring compliance with stringent industry standards.
Biopharmaceutical Processing & Fermentation:
Coriolis and electromagnetic flow meters provide highly accurate monitoring of nutrient and buffer solution delivery into bioreactors and fermenters, ensuring optimal microbial and cell culture growth.
Mass flow controllers regulate the precise dosing of oxygen, carbon dioxide, and nitrogen gases in cell culture aeration systems, optimizing gas exchange and metabolic efficiency.
Single-use flow sensors are used in disposable bioprocessing assemblies, offering real-time monitoring while minimizing cross-contamination risks.
Purified Water & Water for Injection (WFI) Systems:
Ultrasonic and electromagnetic flow meters ensure precise flow measurement of reverse osmosis (RO), deionized (DI), and WFI systems, ensuring compliance with USP <645> standards for pharmaceutical-grade water.
Clamp-on flow meters are widely used for non-invasive monitoring of high-purity water distribution systems, reducing the risk of bacterial contamination.
Sterile Filtration & Buffer Preparation:
Positive displacement and turbine flow meters monitor fluid movement in sterile filtration systems, ensuring proper flow rates to optimize membrane performance.
Flow control valves help regulate liquid flow during buffer and media preparation, ensuring accurate mixing and pH control.
Clean-in-Place (CIP) & Steam-in-Place (SIP) Systems:
Magnetic and Coriolis flow meters monitor detergent and disinfectant flow in CIP systems, ensuring effective cleaning and decontamination.
Vortex and differential pressure flow meters regulate steam flow in SIP systems, ensuring proper sterilization of processing equipment.
Medical Device & Diagnostic Manufacturing:
Ultrasonic and microfluidic flow sensors control the precise dispensing of reagents and biological samples in diagnostic instruments, ensuring accuracy and repeatability in laboratory automation.
Thermal mass flow meters regulate gas flow in medical device sterilization chambers, ensuring optimal ethylene oxide (EtO) or hydrogen peroxide exposure.
Key Purchasing Considerations
Selecting the right flow measurement and control devices for life science applications requires careful evaluation of process conditions, accuracy requirements, material compatibility, and regulatory compliance. The following factors should be considered:
Accuracy & Repeatability:
High-precision flow meters, such as Coriolis, ultrasonic, and thermal mass meters, are ideal for applications requiring tight flow control tolerances.
Consistent and repeatable measurements are critical for batch processing, chromatography, and drug formulation to ensure uniform product quality.
Material Compatibility & Sterility:
Wetted parts must be made from biocompatible and FDA-approved materials, such as 316L stainless steel, PFA, or PTFE, to prevent contamination.
Single-use flow sensors are preferred in disposable bioprocessing applications to maintain sterility and eliminate cleaning validation requirements.
Regulatory Compliance & Validation:
Ensure flow meters meet USP, FDA, ISO 13485, and ASME-BPE standards for biopharmaceutical and medical applications.
Flow sensors used in regulated environments should support electronic batch record (EBR) integration and compliance with FDA 21 CFR Part 11 for data integrity.
Integration with Process Control Systems:
Flow meters should be compatible with SCADA, PLC, and DCS systems for automated process control and real-time monitoring.
Digital communication protocols such as HART, Modbus, or Profibus enable seamless integration with industrial control networks.
Hygienic Design & Maintenance:
Hygienic flow meters should have crevice-free and self-draining designs to prevent microbial growth.
Non-invasive, clamp-on ultrasonic meters reduce maintenance requirements and contamination risks by eliminating contact with process fluids.
Environmental & Process Conditions:
Consider temperature, pressure, and viscosity variations when selecting flow measurement technology, especially in steam sterilization, viscous media, and cryogenic applications.
Devices used in explosive environments, such as ethylene oxide sterilization chambers, should have intrinsically safe and ATEX-rated designs.
Pressure Monitoring & Regulation
Accurate pressure monitoring and regulation are essential for maintaining safety, efficiency, and compliance in life science facilities. From biopharmaceutical manufacturing to medical device sterilization and laboratory operations, precise pressure control ensures optimal process conditions, prevents contamination, and safeguards critical equipment. In applications such as cleanroom environments, fermentation systems, sterile filtration, and ultrapure water distribution, maintaining stable pressure levels is crucial for product quality and regulatory compliance. Advanced pressure sensors and regulators enable real-time monitoring, automated control, and data logging to support GMP, FDA, and ISO 13485 requirements.
Applications of Pressure Monitoring & Regulation in Life Science Facilities
Pressure measurement and control are integral to ensuring the reliability and efficiency of life science processes. Whether regulating compressed gases, monitoring cleanroom pressure differentials, or optimizing filtration systems, precision instrumentation is required to maintain process integrity.
Bioreactors & Fermentation Systems:
Differential pressure sensors ensure proper gas flow and aeration rates in bioreactors, optimizing oxygen transfer for microbial and cell culture growth.
Pressure transmitters monitor headspace pressure in fermentation tanks, preventing over-pressurization and ensuring controlled CO₂ off-gassing.
Sterile diaphragm pressure sensors maintain precise pressure control in harvest and feed lines, protecting sensitive biological cultures.
Sterile Filtration & Chromatography:
High-accuracy pressure sensors monitor differential pressure across sterile membrane filters, ensuring proper filtration efficiency and preventing filter clogging.
Automated pressure regulators optimize flow rates in chromatography systems, ensuring consistent separation and purification of biologics and pharmaceuticals.
Vacuum pressure transducers control pressure levels in lyophilization (freeze-drying) processes, ensuring product stability.
Cleanroom & Containment Pressure Control:
Room pressure monitors ensure positive pressure in cleanrooms to prevent contamination from outside air.
Negative pressure monitoring in biosafety cabinets and containment zones prevents the escape of hazardous biological agents.
Digital pressure transmitters provide continuous monitoring of HVAC and air handling systems, ensuring regulatory compliance.
Medical Gas Delivery & Distribution:
Pressure regulators and transmitters ensure consistent delivery of oxygen, nitrogen, and carbon dioxide in hospital and laboratory settings.
Monitoring systems detect leaks and fluctuations in compressed air and gas pipelines, ensuring safe operation.
Digital pressure sensors maintain precise dosing of gases in cryogenic storage and liquid nitrogen applications for biomedical preservation.
Steam & Compressed Air Systems in Sterilization & CIP/SIP Processes:
Pressure transmitters monitor steam sterilizers (autoclaves) to ensure proper pressure and temperature profiles for sterilization cycles.
Compressed air pressure sensors optimize CIP and SIP system performance, ensuring efficient cleaning and sterilization of process lines.
High-temperature pressure sensors are used in ethylene oxide (EtO) sterilization chambers to maintain precise sterilization conditions.
Key Purchasing Considerations
Choosing the right pressure monitoring and regulation devices for life science applications requires careful consideration of process requirements, regulatory compliance, and environmental conditions. The following factors should guide decision-making:
Accuracy & Sensitivity:
High-precision pressure transmitters with 0.1% accuracy or better are required for applications such as sterile filtration, bioreactor aeration, and chromatography.
Differential pressure sensors should have low-pressure detection capabilities for applications like cleanroom monitoring and filter integrity testing.
Material Compatibility & Sterility:
Wetted materials should be 316L stainless steel, Hastelloy, PTFE, or other biocompatible materials to prevent contamination in sterile processes.
Sensors used in pharmaceutical and bioprocessing applications must have sanitary diaphragm seals to meet ASME-BPE standards.
Environmental & Process Conditions:
High-temperature sensors are needed for steam sterilization (SIP) and autoclaves, while cryogenic-compatible sensors are required for liquid nitrogen applications.
Explosion-proof or intrinsically safe designs should be considered for hazardous environments, such as EtO sterilization or volatile chemical storage.
Regulatory Compliance & Validation:
Ensure pressure sensors and regulators meet FDA, GMP, USP, and ISO 13485 standards for pharmaceutical and medical applications.
Devices should support data integrity and audit trail compliance with FDA 21 CFR Part 11.
Integration with Process Control Systems:
Digital pressure transmitters should be compatible with SCADA, PLC, and DCS systems for automated process monitoring and control.
HART, Modbus, or Profibus communication protocols ensure seamless integration with existing facility automation networks.
Maintenance & Calibration Requirements:
Devices with self-calibrating or remote diagnostic features reduce downtime and improve operational efficiency.
Hygienic and flush-mounted sensors minimize contamination risks and facilitate CIP/SIP cleaning procedures.
Temperature Sensing & Control
Precise temperature sensing and control are fundamental to maintaining product quality, process consistency, and regulatory compliance in life science applications. Temperature fluctuations can impact reaction rates, microbial growth, protein stability, and sterilization effectiveness, making real-time monitoring essential in biopharmaceutical manufacturing, cleanroom environments, medical device production, and laboratory research. Advanced temperature sensors and controllers ensure accurate thermal regulation in applications such as fermentation, sterilization, chromatography, lyophilization, and cold chain storage, helping facilities comply with GMP, FDA, and ISO 13485 standards.
Applications of Temperature Sensing & Control for Critical Processes
Temperature monitoring is essential across various life science applications to ensure precise thermal control, prevent deviations, and maintain sterile conditions. High-accuracy sensors and control systems optimize efficiency while safeguarding sensitive biological and pharmaceutical materials.
Bioreactors & Fermentation Systems:
RTDs (resistance temperature detectors) and thermocouples monitor temperature in bioreactors, ensuring optimal conditions for microbial and mammalian cell culture growth.
Precision temperature control systems regulate heat exchangers to maintain consistent thermal conditions during fermentation.
Infrared temperature sensors provide non-contact monitoring of reactor vessel surfaces to prevent overheating or cold spots.
Sterilization & Clean-In-Place (CIP) / Steam-In-Place (SIP) Systems:
High-temperature thermocouples and RTDs measure steam sterilization temperatures in autoclaves, ensuring compliance with USP and FDA sterilization guidelines.
Temperature sensors in SIP systems verify that required heat levels are reached to effectively eliminate microbial contamination in process equipment.
Infrared and wireless temperature sensors ensure CIP systems maintain proper detergent and rinse temperatures for effective cleaning cycles.
Chromatography & Pharmaceutical Formulation:
Temperature sensors in HPLC (high-performance liquid chromatography) systems maintain precise column temperatures to optimize separation efficiency.
Real-time temperature monitoring in pharmaceutical compounding and formulation ensures consistent product stability.
Heat exchanger temperature controls regulate drug crystallization and purification processes, preventing thermal degradation.
Lyophilization (Freeze-Drying) & Cold Storage:
Cryogenic temperature sensors regulate lyophilization processes, ensuring controlled sublimation and preservation of biologic materials.
Precision temperature probes in vaccine and biologic storage freezers ensure compliance with WHO and CDC cold chain requirements.
Digital temperature loggers track storage conditions in ultra-low temperature freezers and liquid nitrogen storage tanks for cell and gene therapy applications.
Cleanroom & Environmental Monitoring:
Room temperature sensors provide continuous monitoring in GMP cleanrooms, ensuring compliance with environmental control requirements.
HVAC-integrated temperature sensors regulate airflow and heat levels in aseptic processing areas to prevent deviations.
Wireless monitoring systems track temperature fluctuations in biosafety cabinets and containment areas, ensuring controlled conditions for hazardous material handling.
Key Purchasing Considerations
Selecting the right temperature sensing and control equipment for life science applications requires careful evaluation of process requirements, regulatory standards, and environmental conditions. The following factors should guide decision-making:
Accuracy & Response Time:
RTDs (e.g., PT100, PT1000) provide highly accurate temperature readings, making them ideal for bioreactors, chromatography, and pharmaceutical manufacturing.
Thermocouples offer rapid response times for applications with high-temperature fluctuations, such as SIP systems and sterilization processes.
Infrared sensors provide non-contact temperature monitoring for sterilization, cleanroom, and bioreactor surface applications.
Material Compatibility & Sterility:
Sensors used in pharmaceutical and bioprocessing environments should have sanitary, stainless steel, or PTFE-coated designs to ensure compliance with ASME-BPE standards.
Devices used in high-purity applications should have crevice-free, flush-mounted configurations to prevent contamination.
Environmental Conditions & Operating Range:
High-temperature sensors are required for steam sterilization, autoclaves, and CIP/SIP systems.
Cryogenic temperature sensors must handle extreme cold environments for vaccine storage, lyophilization, and liquid nitrogen applications.
Wireless and remote temperature sensors are ideal for cleanroom environmental monitoring and logistics tracking.
Regulatory Compliance & Validation:
Ensure sensors meet compliance requirements for FDA 21 CFR Part 11, GMP, USP, ISO 13485, and WHO cold chain guidelines.
Temperature sensors should integrate with SCADA, PLC, and DCS systems for automated monitoring and regulatory record-keeping.
Maintenance & Calibration:
Choose self-calibrating temperature sensors for minimal downtime and continuous compliance.
Devices should support NIST-traceable calibration standards for validation in pharmaceutical and biotech environments.
Select sensors with long-term stability to reduce recalibration frequency and improve process reliability.
Level Detection & Management
Accurate level detection and management are essential in life science applications to ensure process stability, prevent contamination, and comply with regulatory standards. From biopharmaceutical production to medical device manufacturing and laboratory research, precise monitoring of liquid and gas levels is crucial for fermentation, buffer preparation, ultrapure water storage, bioreactors, and cryogenic applications. Advanced level sensors help maintain precise control of process fluids, minimize waste, and optimize batch consistency while adhering to GMP, FDA, USP, and ISO 13485 standards.
Applications of Level Detection & Management for Liquids and Gases
Reliable level measurement is required in life science applications to monitor liquids, gases, and cryogenic substances in storage and process vessels. The right instrumentation ensures accurate material handling, prevents process interruptions, and supports regulatory compliance.
Bioreactors & Fermentation Tanks:
- Guided wave radar and capacitive level sensors monitor liquid media levels in bioreactors to maintain precise feed rates.
- Ultrasonic level sensors detect foam buildup in fermentation tanks, helping regulate anti-foam agent dosing.
- Hydrostatic and differential pressure sensors track headspace gas levels, ensuring proper gas exchange for microbial and mammalian cell cultures.
Sterile Filtration & Chromatography Columns:
- Radar and float-based level sensors ensure precise monitoring of buffer and reagent reservoirs, preventing process disruptions.
- Optical and capacitive sensors regulate levels in chromatography columns, ensuring optimal separation of proteins and biologics.
- Load cell-based level measurement provides real-time weight-based level monitoring in filtration skids and mixing vessels.
Purified Water & WFI (Water for Injection) Systems:
- Ultrasonic and capacitive sensors measure water levels in storage tanks, ensuring compliance with USP <645> purity requirements.
- Non-contact radar sensors are used in high-purity water loops, preventing contamination in pharmaceutical-grade water systems.
- Continuous level monitoring in WFI and RO water storage vessels ensures proper supply for drug formulation and aseptic processing.
Cryogenic & Gas Storage Applications:
- Differential pressure and capacitive sensors measure liquid nitrogen levels in cryogenic storage tanks used for cell therapy and vaccine preservation.
- Thermal mass flow meters track gas levels in oxygen, nitrogen, and CO₂ tanks, ensuring safe and efficient gas distribution.
- Radar and guided wave level sensors provide real-time monitoring of cryogenic storage for biological samples and clinical materials.
Clean-in-Place (CIP) & Waste Handling Systems:
- Float switches and hydrostatic level sensors track detergent and rinse solution levels in CIP/SIP systems, ensuring effective cleaning cycles.
- Radar and optical level sensors monitor waste liquid levels in containment tanks to prevent overflow and regulatory violations.
- Conductivity-based level sensors help distinguish between cleaning agents, rinse water, and wastewater, ensuring proper process validation.
Key Purchasing Considerations
Choosing the right level detection and management technology for life science applications requires evaluating fluid properties, process requirements, and compliance considerations. The following factors should guide decision-making:
Measurement Accuracy & Sensitivity:
Radar and ultrasonic sensors provide high-accuracy level monitoring in bioreactors, chromatography columns, and sterile liquid tanks.
Capacitive and guided wave radar sensors detect low and high-level thresholds, ensuring precise batch control.
Load cell-based level detection offers gravimetric measurement, ideal for applications requiring weight-based accuracy.
Sterility & Material Compatibility:
Sensors must be constructed from biocompatible, FDA-compliant materials such as 316L stainless steel, PTFE, or PFA to prevent contamination.
Devices in WFI, purified water, and drug formulation applications should feature crevice-free, sanitary designs to meet ASME-BPE standards.
Single-use level sensors should be considered for disposable bioprocessing systems, eliminating cleaning validation steps.
Process Environment & Fluid Properties:
Non-contact ultrasonic or radar sensors are ideal for aggressive chemicals, viscous fluids, and sterile water storage.
High-pressure and high-temperature sensors are required for autoclaves, SIP systems, and cryogenic storage tanks.
Foam detection capabilities should be included for applications in fermentation, buffer preparation, and protein separation.
Regulatory Compliance & Validation:
Ensure level sensors meet GMP, FDA, USP, ISO 13485, and 21 CFR Part 11 compliance for data integrity and traceability.
Devices used in regulated environments should support SCADA, PLC, and industrial automation integration for real-time data logging.
Integration & Communication Protocols:
Digital level sensors should support HART, Modbus, or Profibus for seamless system integration.
Wireless level sensors can provide remote monitoring for cleanroom, storage, and laboratory applications.
Maintenance & Lifecycle Costs:
Non-invasive, self-cleaning level sensors reduce maintenance requirements and prevent contamination risks.
Redundant level detection systems should be considered for critical applications like cryogenic storage, fermentation, and sterilization processes.
Gas & Contaminant Detection
Applications of Gas & Contaminant Detection for Life Science Safety & Compliance
Gas detection and air quality monitoring play a crucial role in maintaining safe working environments, protecting product integrity, and ensuring regulatory adherence. Various sensor technologies—such as infrared (IR), electrochemical, photoionization detectors (PID), and particulate counters—are used for continuous detection and control of contaminants.
Cleanroom Air Quality & Contamination Control:
Particle counters ensure compliance with ISO 14644 cleanroom classification by detecting airborne contaminants in sterile manufacturing areas.
Differential pressure sensors monitor airflow between cleanroom zones, ensuring proper air exchange rates to prevent cross-contamination.
VOC sensors detect chemical emissions from solvents and cleaning agents, protecting cleanroom environments from airborne contaminants.
Pharmaceutical & Biotech Laboratory Safety:
Oxygen (O₂) deficiency monitors prevent asphyxiation risks in cryogenic storage areas, where liquid nitrogen and carbon dioxide displace breathable air.
Chemical vapor sensors detect hazardous fume hood leaks and solvent emissions, ensuring worker safety in research and analytical labs.
Real-time air monitoring systems detect microbial contaminants and endotoxins in sterile environments, ensuring compliance with USP <797> and <800>.
Compressed Gas & Cryogenic Storage Monitoring:
Gas detectors ensure safe storage and distribution of oxygen (O₂), nitrogen (N₂), carbon dioxide (CO₂), and hydrogen (H₂) in laboratories and manufacturing sites.
Cryogenic gas sensors track liquid nitrogen levels in cell banking, tissue storage, and vaccine preservation applications.
Thermal mass flow meters measure gas flow rates in bioreactors, chromatography columns, and medical gas delivery systems.
Solvent & Chemical Vapor Detection in Pharmaceutical Manufacturing:
PID sensors monitor residual solvent vapors in drug formulation and compounding facilities to ensure compliance with exposure limits.
Continuous gas monitoring detects ethylene oxide (EtO) and hydrogen peroxide (H₂O₂) vapor leaks in sterilization chambers.
Infrared gas analyzers identify leaks in compressed air and nitrogen systems, optimizing process safety and efficiency.
CO₂ Monitoring in Bioprocessing & Incubation Systems:
Infrared CO₂ sensors regulate gas levels in incubators for cell culture growth and biopharmaceutical production.
Multi-gas analyzers optimize aeration control in fermentation and cell culture systems, ensuring stable metabolic conditions.
High-precision CO₂ detectors prevent gas buildup in sealed laboratory environments where asphyxiation risks exist.
Key Purchasing Considerations
Selecting the right gas and contaminant detection system for life science applications requires evaluating process risks, sensor accuracy, regulatory standards, and integration requirements. The following considerations should guide decision-making:
Gas Type & Detection Sensitivity:
Electrochemical gas sensors offer high sensitivity for detecting toxic gases like CO, H₂S, and NO₂ in laboratory and cleanroom environments.
PID sensors are effective for detecting volatile organic compounds (VOCs) in pharmaceutical production and solvent-based processes.
Infrared (IR) sensors provide accurate, non-contact monitoring of CO₂, CH₄, and H₂O₂ vapors in sterilization, cell culture, and medical gas applications.
Airborne Particle & Contaminant Detection:
Select laser-based particle counters to meet ISO 14644 cleanroom classifications for biotech, pharmaceutical, and medical device manufacturing.
Microbial air samplers should be used in aseptic processing environments to detect airborne contaminants in real time.
Regulatory Compliance & Safety Standards:
Ensure gas detection systems meet OSHA, FDA, USP <797>, USP <800>, ISO 14644, and EPA air quality regulations.
Calibration and data logging features should support FDA 21 CFR Part 11 compliance for electronic record-keeping.
System Integration & Communication Protocols:
Smart gas detectors should support HART, Modbus, BACnet, or SCADA integration for automated process control.
Wireless connectivity enables remote monitoring of hazardous gas levels and cleanroom environmental conditions.
Environmental Durability & Placement:
Choose intrinsically safe and explosion-proof sensors for environments handling flammable gases or solvent vapors.
Select wall-mounted, portable, or inline analyzers based on facility layout and monitoring requirements.
Maintenance & Calibration Requirements:
Opt for self-calibrating gas sensors to reduce maintenance costs and improve long-term reliability.
Choose real-time monitoring with automatic alarm alerts to prevent delays in responding to hazardous conditions.
Analytical Instrumentation
Applications of Analytical Instrumentation for Life Science Process Optimization
Analytical instrumentation is crucial for monitoring biological, chemical, and physical parameters throughout life science processes. These measurements help maintain sterile conditions, optimize reactions, and ensure regulatory compliance in pharmaceutical, biotech, and medical device production.
Bioreactor & Fermentation Monitoring:
Dissolved oxygen (DO) sensors ensure optimal aeration and metabolic activity in microbial and cell culture fermentation.
pH and conductivity analyzers maintain precise culture conditions in biopharmaceutical production.
Optical density (OD) and turbidity sensors measure biomass concentration, optimizing growth phase transitions.
Water Purification & Utility Monitoring (WFI & RO Systems):
Total organic carbon (TOC) analyzers ensure high-purity water compliance with USP <643> and <645> standards.
Conductivity sensors verify water quality in reverse osmosis (RO) and deionized (DI) water systems for pharmaceutical applications.
Chlorine and ozone sensors monitor residual disinfectants in purified water distribution networks.
Sterile Filtration & Chromatography Optimization:
UV/VIS spectrophotometers measure protein and nucleic acid concentration in chromatography systems.
Pressure and flow analyzers optimize filtration efficiency by detecting membrane fouling or pressure imbalances.
Refractive index sensors ensure proper solvent gradient control in HPLC and preparative chromatography.
Clean-in-Place (CIP) & Steam-in-Place (SIP) Systems:
Conductivity and TOC sensors confirm complete detergent and rinse removal during CIP cycles.
Temperature and steam quality sensors validate SIP sterilization effectiveness to meet regulatory standards.
pH and turbidity sensors detect residues and contaminants in waste streams post-cleaning.
Medical Device & Diagnostic Manufacturing:
Spectroscopic and fluorescence analyzers verify biochemical properties of reagents and coatings used in diagnostics.
Gas chromatography (GC) and mass spectrometry (MS) analyzers ensure solvent purity and material compliance.
Laser-based particle counters detect airborne contaminants in medical device assembly cleanrooms.
Key Purchasing Considerations
Selecting the right analytical instrumentation requires careful evaluation of process conditions, measurement accuracy, material compatibility, and regulatory compliance. The following factors should guide decision-making:
Measurement Accuracy & Sensitivity:
Choose high-precision DO, pH, and TOC analyzers for bioprocessing, fermentation, and purified water monitoring.
Low-range TOC and conductivity meters ensure compliance with USP standards for WFI and RO water systems.
Real-time optical and fluorescence sensors improve reaction monitoring in chromatography and purification steps.
Material Compatibility & Sterility:
Sensors used in biopharmaceutical processes must be biocompatible, corrosion-resistant, and sterilizable (e.g., 316L stainless steel, PTFE, or sapphire optics).
Disposable single-use analyzers reduce contamination risk in disposable bioreactor and filtration systems.
Regulatory Compliance & Data Integrity:
Ensure analyzers meet FDA 21 CFR Part 11, USP <643>, USP <645>, GMP, and ISO 13485 standards for electronic records and process validation.
Instruments should support electronic batch records (EBR) and audit trails for compliance in regulated environments.
Integration with Process Control Systems:
Analytical instruments should support HART, Modbus, Profibus, and OPC communication protocols for seamless SCADA and PLC integration.
Wireless and IoT-enabled sensors improve real-time monitoring in remote and distributed process environments.
Environmental Conditions & Sensor Longevity:
Instruments used in harsh chemical environments (e.g., CIP/SIP cycles, solvents, and high-purity gases) must have chemical-resistant materials.
Self-cleaning sensors with automatic calibration reduce maintenance and extend operational life.
Maintenance & Calibration:
Choose low-drift, self-calibrating, or auto-diagnostic sensors to minimize manual recalibration and downtime.
Consider non-invasive or inline analytical sensors to reduce process disruptions and ensure real-time monitoring.
Industry Standards & Regulatory Compliance
Strict adherence to Good Manufacturing Practice (GMP), U.S. Food and Drug Administration (FDA) regulations, and International Organization for Standardization (ISO) standards is critical in life science manufacturing. Pharmaceutical, biotechnology, and medical device companies must comply with stringent guidelines to ensure product safety, process consistency, and regulatory approval. From sterile manufacturing environments to analytical instrumentation and cleanroom operations, process control solutions must meet industry standards for data integrity, validation, and traceability. Compliance-driven instrumentation, monitoring systems, and automated controls help manufacturers reduce contamination risks, enhance efficiency, and maintain product quality in highly regulated environments.
Adhering to GMP, FDA, and ISO Standards
Manufacturers operating in life science industries must meet rigorous global regulatory requirements for process control, cleanliness, and product safety. The following standards define industry best practices for pharmaceutical and biotech production:
Good Manufacturing Practice (GMP):
Ensures consistent quality in drug production, biopharmaceuticals, and medical devices.
Requires precise monitoring of temperature, pressure, humidity, and environmental conditions.
Enforces strict guidelines for cleanroom classification, sterilization, and contamination prevention.
FDA 21 CFR Part 11:
Governs electronic records and signatures for audit trails and compliance documentation.
Requires validated data integrity in SCADA, PLC, and distributed control systems (DCS).
Ensures traceability and security in automated process monitoring and analytical instrumentation.
ISO 13485 (Medical Device Quality Management System):
Defines quality control requirements for medical device and diagnostic manufacturing.
Enforces strict process validation for sterilization, material handling, and electronic component manufacturing.
Requires continuous monitoring of process variables, including gas purity, water quality, and cleanroom air quality.
USP <643> & <645> (Water for Injection & Purified Water Standards):
Establishes conductivity and TOC monitoring requirements for high-purity water systems.
Requires real-time analytical instrumentation to ensure pharmaceutical-grade water quality.
ISO 14644 (Cleanroom Standards):
Regulates airborne particle contamination limits for pharmaceutical and biotech production environments.
Requires advanced differential pressure monitoring, airflow control, and particulate counting in cleanrooms.
Compliance Considerations for Pharmaceutical and Biotech Processes
Achieving and maintaining regulatory compliance in pharmaceutical and biotech manufacturing requires advanced process instrumentation, automation, and real-time monitoring. Key considerations include:
Process Validation & Data Integrity:
Instruments must support 21 CFR Part 11-compliant electronic records for audit trails and regulatory submissions.
Automated systems should ensure real-time data logging, remote monitoring, and deviation alerts.
Sterility & Contamination Control:
Process control solutions must ensure cleanroom compliance, air quality monitoring, and contamination prevention.
Temperature, pressure, and level sensors should be sanitary, sterilizable, and resistant to biofilm formation.
Calibration & Quality Assurance:
Sensors and analyzers must be regularly calibrated and meet NIST-traceable standards.
Automated self-calibrating instrumentation improves accuracy and reduces downtime.
Integration with Facility Monitoring Systems (FMS):
Smart instrumentation should integrate with SCADA, PLC, and building automation systems for comprehensive process control.
Wireless monitoring solutions enable remote compliance tracking and predictive maintenance.
Benefits of Working With Clipper Controls
Clipper Controls provides industry-leading process instrumentation and control solutions tailored for life science applications. Our precision sensors, analyzers, and automation systems ensure regulatory compliance, process reliability, and contamination prevention in pharmaceutical, biotech, and medical device manufacturing. With expert technical support, we help clients optimize efficiency and maintain GMP standards.
By partnering with Clipper Controls, manufacturers gain access to best-in-class flow, pressure, level, and analytical measurement technologies. Our solutions integrate seamlessly with SCADA, PLC, and DCS systems, providing real-time monitoring, automated reporting, and compliance tracking. With a focus on quality and innovation, we deliver reliable instrumentation that enhances process control, product consistency, and regulatory compliance.
Case Studies & Success Stories
Click here to read our life science case studies.
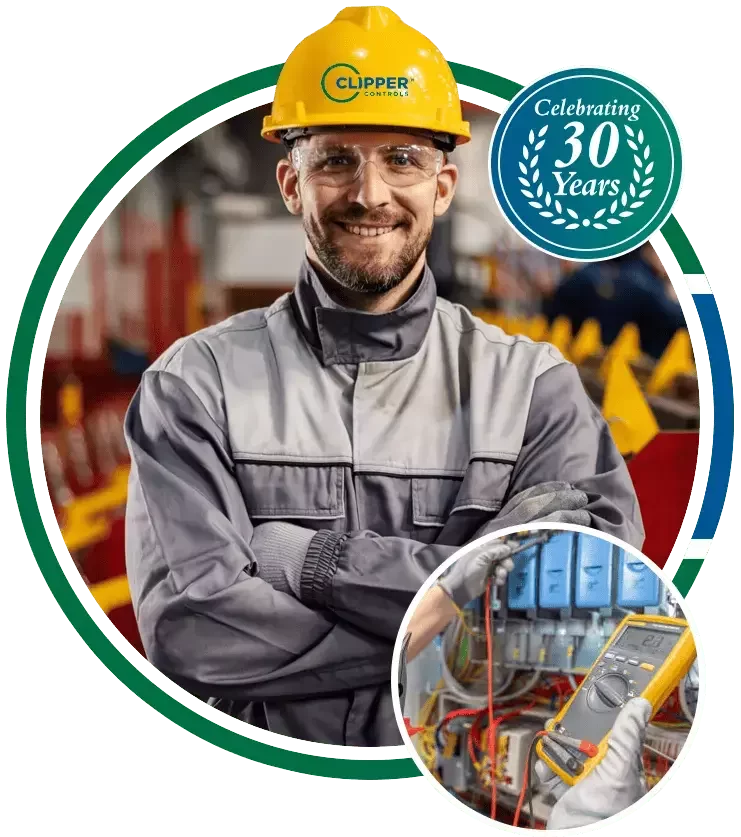
Real Results, Real Impact:
Thanks to Clipper Controls, our wastewater treatment plant improved efficiency & compliance with top-tier flow meters. Reliable solutions, great support! We recommend Clipper Controls to all our partner companies.
~ John Smith, Controls Engineer @ ABC Company
Clipper Controls helped our city upgrade water monitoring systems, ensuring accuracy & compliance. Reliable solutions & excellent customer service!
~ Nancy Patel, Procurement @ ABC Company
~ John Smith, Controls Engineer @ ABC Company
Ready to Work With Us?
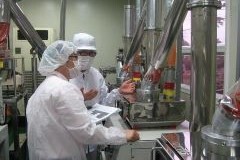
Quick Page Navigation:
🔹How Our Products Support Your Industry
Pressure Monitoring & Regulation
Analytical Instrumentation
🔹Industry Standards & Regulatory Compliance
🔹Benefits of Working With Clipper Controls
Case Studies & Success Stories
Real Results, Real Impact:
🔹Featured Products for Semiconductor & Electronics Manufacturing Applications