Mining & Aggregates Process Control Applications
Application Overview
Mining and aggregates operations demand precise monitoring and control solutions to ensure efficiency, safety, and compliance with environmental regulations. Harsh operating conditions, including extreme temperatures, abrasive materials, and high vibration levels, require rugged instrumentation capable of withstanding these challenges. Reliable level measurement, flow monitoring, and process automation play a critical role in optimizing material handling, minimizing downtime, and improving throughput. Effective control strategies enhance equipment longevity and reduce maintenance costs, making them essential for maintaining profitability in a competitive industry.
From material extraction to processing and transport, accurate instrumentation is crucial for maintaining consistent production and ensuring quality control. Level sensors help prevent overflows and ensure proper material inventory, while flow meters optimize water and slurry management in wash plants and tailings systems. Pressure and temperature monitoring are essential for equipment protection and process stability. Advanced control systems integrate these measurements to provide real-time data, enabling predictive maintenance and process optimization. By leveraging automation and industrial networking, mining and aggregate facilities can achieve greater efficiency, reduce waste, and meet regulatory requirements with confidence.
How Our Products Support Your Industry
Clipper Controls provides specialized instrumentation and control solutions tailored to the demanding conditions of the mining and aggregates industry. We offer rugged and reliable level, flow, pressure, and temperature measurement devices designed to withstand abrasive materials, extreme temperatures, and harsh environmental conditions. Our solutions help operations improve efficiency, reduce maintenance costs, and enhance process reliability, ensuring continuous production with minimal downtime.
Beyond instrumentation, we support mining and aggregate facilities with advanced automation, industrial networking, and process control solutions. Our expertise in integrating real-time monitoring systems enables predictive maintenance and process optimization, helping companies maximize throughput while maintaining regulatory compliance. With a focus on durability, accuracy, and efficiency, Clipper Controls delivers the tools and expertise needed to optimize material handling, water management, and equipment protection in mining and aggregates operations.
Key Applications and Solutions
Flow Measurement & Control
Accurate flow measurement and control are essential in mining and aggregates operations to ensure efficient resource utilization, maintain system integrity, and comply with regulatory standards. Effective flow monitoring is crucial for managing slurry transport, dewatering processes, and water usage, directly impacting operational efficiency and environmental compliance.
Applications of Flow Measurement & Control in Mining and Aggregates Processing
Flow measurement plays a vital role in optimizing processes, maintaining compliance, and improving efficiency across various stages of mining and aggregates operations. Different flow measurement technologies are suited for specific applications based on fluid properties, accuracy requirements, and environmental conditions.
Slurry Transport:Monitoring the flow of slurry mixtures is critical for efficient material processing and pipeline integrity. Electromagnetic flow meters (magmeters) are commonly used due to their ability to handle abrasive materials and provide accurate measurements without obstructions.
Dewatering Processes:Effective dewatering ensures stable mine operations and prevents equipment damage. Ultrasonic and submersible flow meters are ideal for measuring water extraction rates, aiding in maintaining dry working conditions and optimizing water recycling efforts.
Dust Suppression Systems:Controlling dust emissions is vital for environmental compliance and worker safety. Accurate flow measurement in water spray systems ensures proper dust suppression while minimizing water usage.
Cooling Systems:Monitoring flow rates in equipment cooling systems prevents overheating and extends machinery lifespan. Vortex and differential pressure flow meters are suitable for ensuring optimal coolant flow rates.
Leachate Management:In processes like heap leaching, precise flow control of leachate solutions is essential for effective mineral extraction. Coriolis flow meters provide accurate measurements of chemical dosing and leachate circulation.
Key Purchasing Considerations
Selecting the right flow measurement and control solutions for mining and aggregates processing requires careful evaluation of operational conditions, media characteristics, and industry-specific challenges. Here are key factors to consider when purchasing flow meters and control systems:
- Media Type & Composition: Mining applications involve abrasive slurries, viscous materials, and water with varying levels of particulates. Choose flow meters with durable linings (such as ceramic or rubber for magmeters) to withstand harsh conditions.
- Accuracy & Reliability: In high-value material transport and processing, precision is critical. Flow meters should offer stable and repeatable measurements, even in turbulent or variable flow conditions.
- Durability & Maintenance Needs: Given the harsh environments of mining sites, flow meters must be resistant to wear, corrosion, and high vibration. Non-intrusive flow technologies, such as ultrasonic and electromagnetic meters, reduce maintenance needs and extend service life.
- Installation & Compatibility: Ensure that flow meters integrate seamlessly with existing SCADA and PLC systems for real-time monitoring and automated control. Wireless and remote monitoring capabilities can further enhance operational efficiency.
- Compliance & Environmental Considerations: Regulatory requirements for water usage, slurry disposal, and dust suppression necessitate accurate flow measurement. Select certified flow measurement devices that align with industry standards.
Level Measurement & Control
Effective level measurement and control is essential in mining and aggregates processing to ensure operational efficiency, material inventory management, and equipment protection. Given the harsh conditions in mining environments—such as dust, vibration, and extreme temperatures—reliable level monitoring solutions help prevent costly downtime, improve safety, and optimize production.
Applications of Level Measurement & Control in Mining and Aggregates Processing
Key Purchasing Considerations
Selecting the right level measurement technology for mining and aggregates processing requires an in-depth understanding of environmental conditions, material characteristics, and operational needs. Here are the most important factors to consider:
- Material Type & Behavior: Bulk solids, slurries, and liquids have different flow properties. Radar and laser level sensors excel in dusty environments, while submersible hydrostatic sensors are better suited for liquid level monitoring.
- Environmental Conditions: Mining operations often experience extreme temperatures, high vibration, and heavy dust. Choose sensors with rugged enclosures (IP67 or higher) and corrosion-resistant materials to withstand harsh conditions.
- Accuracy & Measurement Range: Some applications require millimeter precision, while others need approximate level detection. Guided wave radar (GWR) and ultrasonic sensors provide high accuracy for both small and large storage vessels.
- Maintenance & Installation Considerations: Non-contact level sensors such as radar and laser technologies reduce maintenance needs by preventing material buildup on sensor surfaces. Wireless or remote-monitoring solutions further minimize operational disruptions.
- Integration with Control Systems: Level measurement devices should seamlessly connect to SCADA, PLCs, and industrial automation networks for real-time monitoring, process optimization, and predictive maintenance alerts.
- Regulatory Compliance & Safety: Mining operations must adhere to strict environmental and workplace safety regulations. Choosing certified explosion-proof and intrinsically safe sensors is essential for hazardous locations.
Pressure & Temperature Monitoring
Accurate pressure and temperature monitoring is critical in mining and aggregates processing to maintain equipment efficiency, ensure worker safety, and optimize various processes. Mining environments are harsh, with extreme temperatures, high pressures, and abrasive materials that can quickly degrade equipment. Implementing reliable temperature and pressure sensors helps prevent equipment failure, reduce maintenance costs, and improve process control.
Applications of Pressure & Temperature Monitoring in Mining and Aggregates Processing
Key Purchasing Considerations
When selecting pressure and temperature monitoring solutions for mining and aggregates applications, it’s essential to consider the extreme operating conditions and the specific needs of each process. Key factors include:
- Operating Environment: Mining operations involve high vibration, extreme heat, cold, and dust exposure. Choose rugged, industrial-grade sensors with protective enclosures (IP67 or IP68) for long-term durability.
- Pressure & Temperature Ranges: Different applications require varying levels of pressure and temperature resistance. High-pressure transducers are necessary for hydraulic systems, while high-temperature thermocouples are required for kilns and steam applications.
- Sensor Material & Durability: Corrosion-resistant materials such as stainless steel or ceramic help sensors withstand abrasive slurries, corrosive chemicals, and extreme conditions in mining operations.
- Accuracy & Response Time: In fast-moving processes like slurry transport and combustion systems, real-time monitoring is critical. Select sensors with high accuracy and rapid response times to detect fluctuations before they cause operational issues.
- Integration with Control Systems: Pressure and temperature sensors should be compatible with SCADA, PLCs, and industrial automation platforms for seamless data integration and remote monitoring. Wireless and IoT-enabled sensors can enhance predictive maintenance capabilities.
- Regulatory Compliance & Safety Ratings: Many mining environments are classified as hazardous locations. Choose sensors with explosion-proof, ATEX, or intrinsically safe certifications to comply with industry regulations and ensure worker safety.
Pump & Valve Automation
Automating pumps and valves in mining and aggregates processing enhances operational efficiency, reduces manual intervention, and improves system reliability. Harsh mining environments demand rugged automation solutions to handle high-pressure slurries, abrasive materials, and variable flow rates while ensuring continuous operation. Implementing automated pump and valve control helps optimize material transport, water management, and chemical dosing, reducing energy consumption and maintenance costs.
Applications of Pump & Valve Automation in Mining and Aggregates Processing
Key Purchasing Considerations
Selecting the right automated pumps and valves for mining and aggregates applications requires evaluating operating conditions, control requirements, and durability factors. Key considerations include:
- Material Durability & Corrosion Resistance: Pumps and valves must withstand abrasive slurries, corrosive chemicals, and extreme conditions. Choose wear-resistant materials such as hardened stainless steel, ceramic-lined components, or rubber-lined valves to extend service life.
- Flow Control & Precision: Mining applications often require variable flow rates depending on material characteristics and process demands. Electrically actuated or pneumatically controlled valves provide precise throttling for optimized flow regulation.
- Automation & Integration with Control Systems: Pumps and valves should be compatible with SCADA, PLCs, and industrial automation networks for remote monitoring and process optimization. IoT-enabled devices allow for predictive maintenance and real-time performance tracking.
- Energy Efficiency & Cost Savings: Mining operations consume large amounts of energy. Variable frequency drives (VFDs) for pump motors help optimize power usage by adjusting speed based on demand, reducing energy waste.
- Fail-Safe & Emergency Shutdown Features: Safety is a top priority in mining. Automated valves with fail-safe shutoff capabilities help prevent catastrophic failures by stopping flow in case of leaks, overpressure, or pump failures.
- Operating Environment & Pressure Ratings: High-pressure pipelines and extreme environmental conditions require rugged actuators and high-performance seals to withstand temperature fluctuations, vibration, and dust exposure.
- Maintenance & Lifecycle Costs: Consider pumps and valves with self-cleaning mechanisms and easy-access designs to minimize maintenance time and labor costs in remote or hard-to-reach installations.
Water Quality Monitoring
Water plays a critical role in mining and aggregates processing, from material washing and dust suppression to slurry transport and wastewater treatment. Effective water quality monitoring ensures compliance with environmental regulations, optimizes water reuse, and prevents contamination of surrounding ecosystems. By continuously measuring key parameters such as pH, turbidity, conductivity, dissolved oxygen, and heavy metal concentrations, mining operations can proactively manage water resources and mitigate potential environmental risks.
Applications of Water Quality Monitoring in Mining & Aggregates Processing
Key Purchasing Considerations
Choosing the right water quality monitoring solutions for mining and aggregates applications requires careful evaluation of measurement accuracy, durability, and integration capabilities. Key factors to consider include:
- Measurement Parameters & Sensor Selection: Different mining processes require monitoring of specific water quality indicators such as pH, conductivity, turbidity, dissolved oxygen, and heavy metals. Multiparameter sensors provide comprehensive water quality assessments.
- Sensor Durability & Environmental Resistance: Mining water often contains abrasive particles, extreme pH levels, and harsh chemicals. Rugged sensors with corrosion-resistant materials (titanium, stainless steel, or PVC-coated probes) ensure long-lasting performance.
- Automation & Remote Monitoring Capabilities: Many mining sites are remote and difficult to access. Wireless and IoT-enabled water quality sensors provide real-time data transmission to SCADA systems, allowing operators to monitor conditions without on-site presence.
- Calibration & Maintenance Requirements: Self-cleaning and auto-calibrating sensors reduce maintenance needs in high-fouling environments, such as tailings ponds and process water tanks, minimizing operational disruptions.
- Data Integration & Compliance Reporting: Water quality monitoring systems should seamlessly integrate with industrial control systems (PLCs, SCADA, cloud-based platforms) to provide historical data, trend analysis, and regulatory compliance reporting.
- Power Supply & Deployment Considerations: For remote mining locations, solar-powered or battery-operated water quality monitoring systems offer reliable performance where grid power is unavailable.
- Regulatory Certification & Compliance Standards: Ensure that water quality sensors meet EPA, ISO 14001, and local environmental standards for accurate and legally compliant water monitoring.
Data Logging & Remote Monitoring
Mining and aggregates operations rely on data logging and remote monitoring to track equipment performance, optimize processes, and ensure regulatory compliance. Given the harsh conditions of mining sites—often located in remote areas with extreme weather and limited access—automated data collection and real-time monitoring help operators make informed decisions, reduce downtime, and enhance safety. By continuously monitoring critical parameters such as equipment health, environmental conditions, and production efficiency, mining companies can improve operational control and prevent costly failures.
Applications of Data Logging & Remote Monitoring in Mining and Aggregates Processing
Key Purchasing Considerations
Choosing the right data logging and remote monitoring solutions for mining and aggregates applications requires evaluating connectivity, durability, scalability, and integration with existing systems. Key factors include:
- Data Transmission & Connectivity: Mining sites are often located in remote areas with limited infrastructure. Wireless, satellite, or cellular IoT-enabled data loggers ensure continuous data transmission even in off-grid environments.
- Durability & Environmental Resistance: Data loggers and sensors must withstand high temperatures, vibration, dust, and moisture. Look for IP67 or IP68-rated enclosures, explosion-proof designs, and corrosion-resistant materials for reliable operation.
- Storage Capacity & Logging Frequency: Some applications require real-time data streaming, while others need periodic logging. High-capacity loggers with adjustable sampling rates ensure adequate data collection without excessive power consumption.
- Battery Life & Power Requirements: For remote mining operations, low-power, solar-charged, or battery-operated data loggers provide long-term performance without frequent maintenance.
- Integration with SCADA & Cloud-Based Platforms: Ensure compatibility with SCADA systems, industrial IoT platforms, and cloud-based dashboards for centralized data visualization, analytics, and reporting.
- User Accessibility & Remote Control: Operators should be able to remotely access data logs via web-based dashboards, mobile apps, or automated alerts, allowing real-time decision-making without on-site presence.
- Regulatory Compliance & Data Security: Mining operations must securely store and transmit environmental and operational data to comply with industry regulations. Choose encrypted, tamper-proof logging systems to prevent data loss or manipulation.
Industry Standards & Regulatory Compliance
MSHA, EPA, and State Regulations for Mining & Aggregates Compliance
- Regulates worker exposure to dust, gases, noise, and structural hazards in underground and surface mines.
- Requires real-time monitoring and alarms for methane, hydrogen sulfide, oxygen deficiency, and combustible gases.
- Mandates regular inspections of dust suppression systems, vibration monitoring systems, and equipment guarding to reduce accident risk.
- Requires permits for stormwater runoff, process water discharge, and tailings effluent, governed by National Pollutant Discharge Elimination System (NPDES).
- Monitoring must include pH, total suspended solids (TSS), turbidity, heavy metals (e.g., arsenic, selenium, cadmium), and conductivity.
- Facilities may also be required to manage and monitor contact and non-contact water using automated samplers and flow-based composite sampling.
- Enforces particulate matter limits (PM10/PM2.5) from crushers, conveyors, haul roads, and screening operations.
- Requires the use of dust suppression systems and real-time particulate monitoring in areas prone to fugitive emissions.
- Emission sources like diesel generators or kilns may also require NOx, SO₂, and CO₂ analyzers for regulatory reporting.
- Governs storage and disposal of process chemicals, spent solvents, and leachate used in ore processing.
- Requires secondary containment monitoring, leak detection, and documentation of hazardous waste disposal practices.
Environmental Sustainability, Safety & Community Impact
- Monitoring of runoff flow rates, turbidity, and sediment load supports compliance with construction and general stormwater permits.
- Best Management Practices (BMPs) may require real-time water level monitoring in retention structures.
- Regulatory bodies increasingly require monitoring of pore pressure, seepage, and slope stability using advanced geotechnical instrumentation.
- Real-time monitoring platforms help predict and prevent catastrophic failures.
- Compliance with local ordinances often involves tracking vibration levels, decibel output, and ambient air quality near community boundaries.
- Environmental impact assessments may also require continuous monitoring of blasting or crushing operations.
Benefits of Working With Clipper Controls
Case Studies & Success Stories
Explore real-world examples of how Clipper Controls has helped mining and aggregates operations optimize their material processing, water management, and equipment performance. From enhancing system efficiency and reducing downtime to ensuring regulatory compliance and resource sustainability, our case studies highlight the tangible benefits of our expertise and innovative solutions.
Click here to read our mining & aggregates processing case studies.
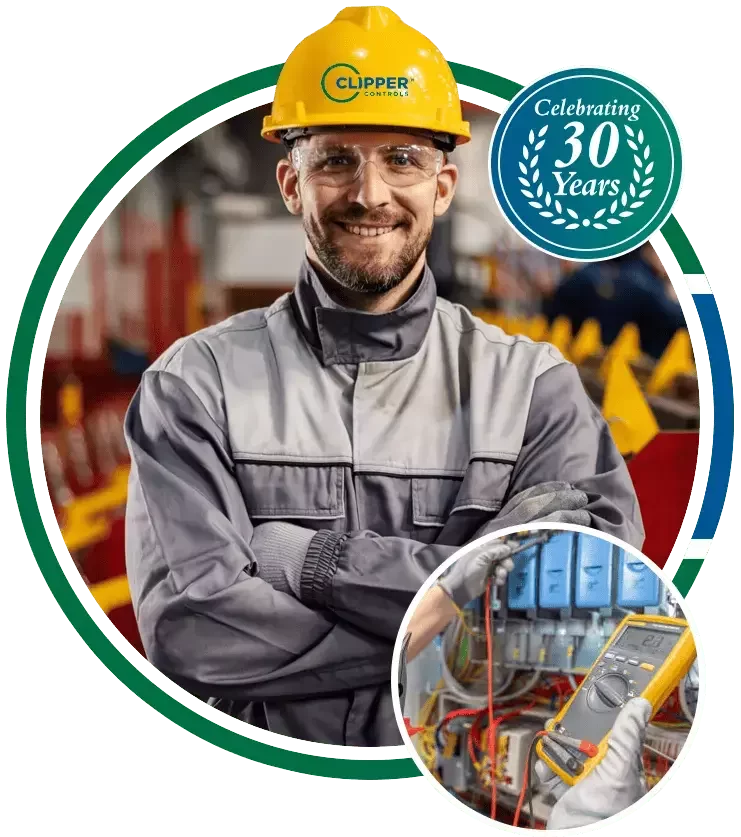
Real Results, Real Impact:
Thanks to Clipper Controls, our wastewater treatment plant improved efficiency & compliance with top-tier flow meters. Reliable solutions, great support! We recommend Clipper Controls to all our partner companies.
~ John Smith, Controls Engineer @ ABC Company
Clipper Controls helped our city upgrade water monitoring systems, ensuring accuracy & compliance. Reliable solutions & excellent customer service!
~ Nancy Patel, Procurement @ ABC Company
~ John Smith, Controls Engineer @ ABC Company