
Vibration Monitoring Equipment
At Clipper Controls, we offer a comprehensive selection of vibration monitoring equipment engineered to safeguard critical machinery, optimize maintenance strategies, and prevent costly downtime. From advanced sensors and transmitters to complete condition monitoring systems, our solutions deliver precise measurement and real-time insights across a wide range of industrial and utility applications. Whether you’re managing rotating equipment, heavy process machinery, or sensitive assets in challenging environments, we provide proven technologies supported by technical expertise and trusted manufacturer partnerships.
What is Condition Monitoring?
Condition Monitoring refers to any method used to monitor the health and performance of machinery and equipment. The goal is to detect signs of wear, degradation, or failure before a breakdown happens. It can include vibration analysis, oil analysis, infrared thermography, acoustic monitoring, motor current analysis, ultrasonic testing, and temperature monitoring.
What is Vibration Monitoring?
Vibration Monitoring is one specific method within condition monitoring. It focuses on analyzing vibrational data from rotating equipment (pumps, fans, compressors, motors, etc.) to detect imbalances, misalignments, bearing wear, looseness, and resonance issues.
Vibration Condition Monitoring Solutions
Vibration Sensors🔗
Application: Vibration sensors are essential instruments for monitoring the health of rotating machinery, motors, pumps, fans, and other critical assets. By detecting changes in vibration patterns, they help identify early signs of imbalance, misalignment, bearing wear, or mechanical faults. This allows operators to schedule maintenance proactively, minimize unplanned downtime, and extend equipment life across industrial, utility, and manufacturing environments.
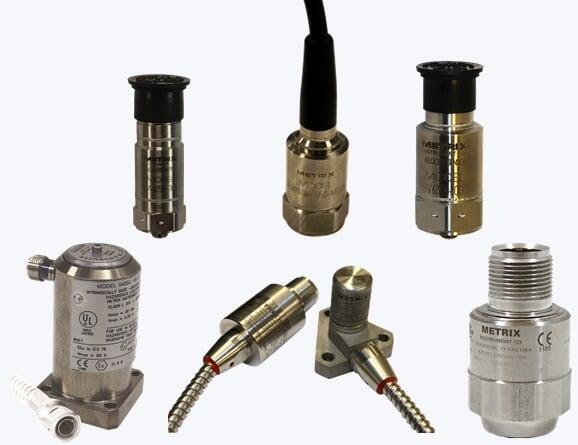
Portable Vibration Meters🔗
Application: Portable vibration meters are used for on-the-spot monitoring of machinery health, allowing maintenance personnel to quickly detect vibration anomalies that may indicate imbalance, misalignment, or bearing wear. They are ideal for route-based inspections and first-level diagnostics in predictive maintenance programs.
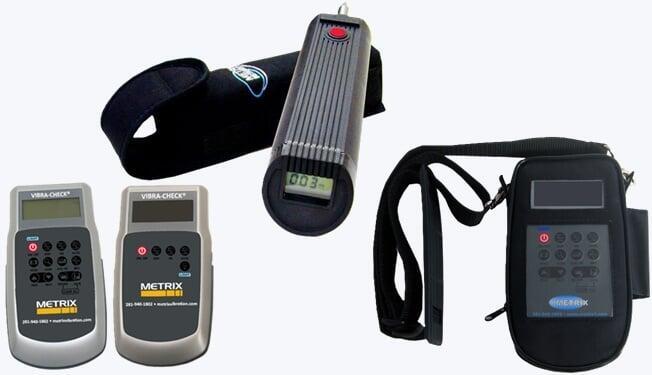
Vibration Switches
🔗
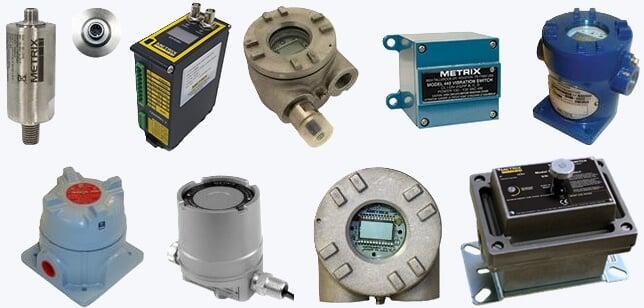
Vibration Transmitters🔗
Application: Vibration transmitters convert vibration measurements into standard output signals, enabling continuous monitoring and easy integration with control systems like PLCs, DCS, or SCADA platforms. Commonly installed on motors, pumps, and turbines, they provide real-time data for early detection of mechanical issues, supporting predictive maintenance strategies across industrial and utility applications.
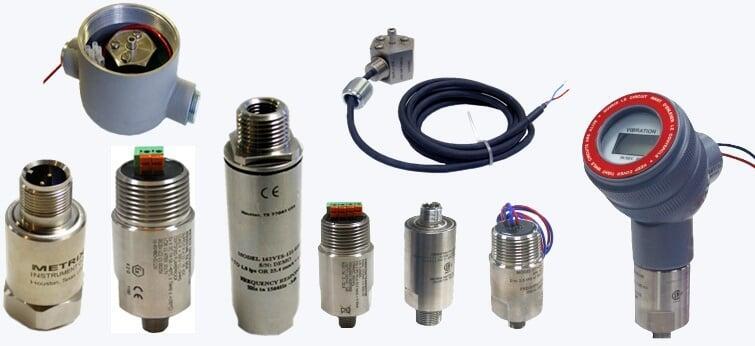
Vibration Signal Conditioners
🔗
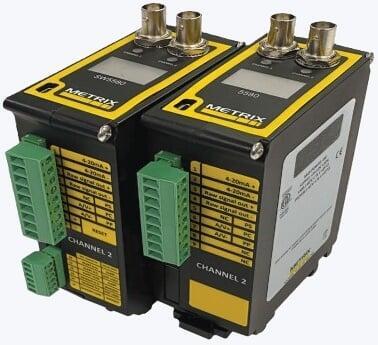
Vibration Monitors🔗
Application: Vibration monitors provide continuous surveillance of machinery health by tracking vibration levels over time and triggering alerts when predefined thresholds are exceeded. Commonly used on critical equipment like turbines, compressors, and pumps, they help prevent unexpected failures, optimize maintenance schedules, and enhance operational reliability across industrial and utility sectors.
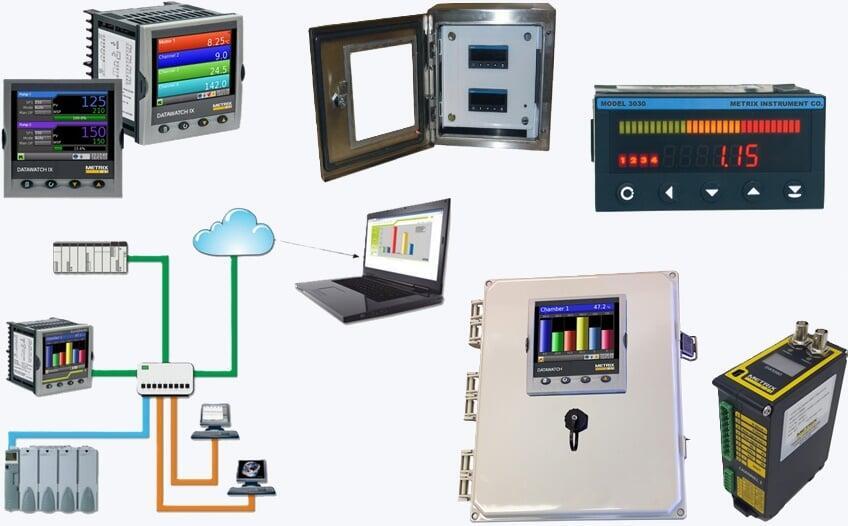
Vibration Data Loggers🔗
Application: Vibration data monitoring and recording devices capture and store vibration measurements over time, enabling detailed analysis of equipment performance and operating conditions. Ideal for diagnosing intermittent issues, validating maintenance actions, and supporting reliability studies, vibration recorders are used across industrial, utility, and research environments to enhance predictive maintenance and asset management strategies.
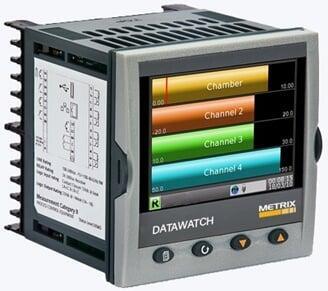
Talk to an Expert
Vibration Testing Equipment
At Clipper Controls, we offer a full range of vibration testers designed to validate the performance, durability, and reliability of critical components and assemblies. Our selection includes portable shaker systems engineered to deliver controlled, repeatable vibration profiles across a wide range of frequencies and amplitudes. Whether used for quality assurance, product development, or preventative maintenance programs, our equipment provides the precision and flexibility needed to simulate real-world operating conditions and verify design resilience.
We supply solutions suitable for both field and laboratory environments, allowing operators and engineers to perform vibration testing on motors, pumps, rotating machinery, structural components, and more. With capabilities for sine, random, and shock vibration testing, our systems support industries ranging from manufacturing and aerospace to power generation and industrial processing. Our team can assist in selecting and specifying the right vibration testing equipment to meet your operational and compliance requirements.
Shaker Tables for Vibration Testing
🔗
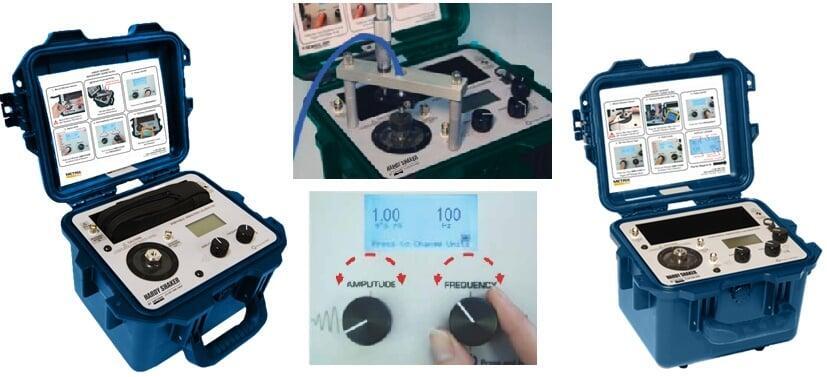
Talk to an Expert
Digital Proximity Instruments
Proximity Probes🔗
Application: Proximity probes measure shaft displacement and vibration in rotating machinery, making them essential for monitoring large turbines, compressors, and critical equipment with fluid-film bearings. They are typically applied in high-speed or high-value assets where precise shaft motion data is required for protection and diagnostics.
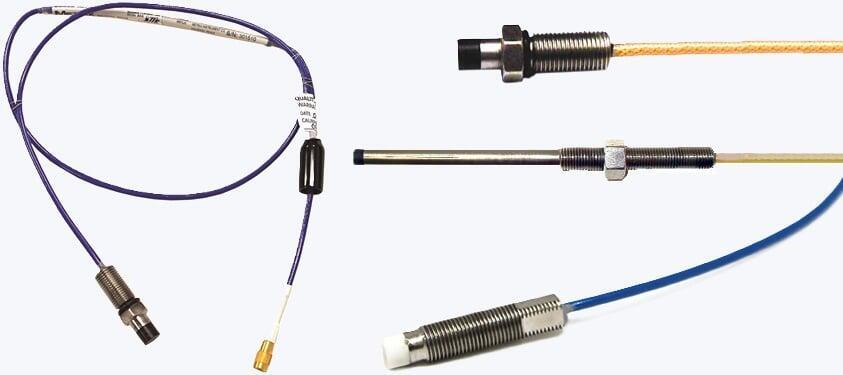
Proximity Probe Drivers🔗
Application: Proximity probe drivers are used in conjunction with proximity probes to process raw sensor signals and deliver usable outputs to monitoring systems. They are commonly applied in turbine and compressor protection systems where accurate interpretation of shaft vibration or position is critical for machine health diagnostics and trip logic.
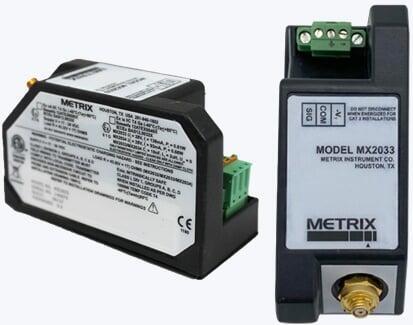
Proximity Probe Transmitters🔗
Application: Proximity probe transmitters convert probe signals into standardized outputs, such as 4–20 mA, for integration with control and monitoring systems. They are typically applied in critical rotating equipment to provide continuous shaft vibration or position data, supporting real-time condition monitoring and protective shutdown functions.
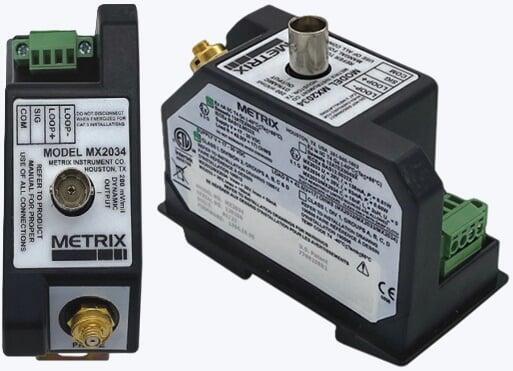
Proximity Probe Signal Conditioners🔗
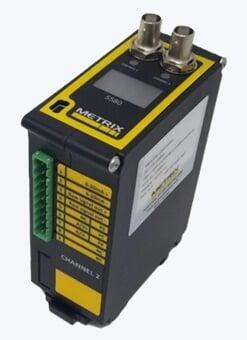
Talk to an Expert
Need Help?
Our Crew is Here To Serve You!
Vibration Monitoring Applications🔗
Power Generation Applications
In the power generation industry, vibration monitoring and machinery condition monitoring instrumentation play a critical role in ensuring the safe, efficient, and reliable operation of rotating equipment. These systems help detect early signs of mechanical issues, prevent unplanned outages, and support predictive maintenance strategies.
- Turbine Vibration Monitoring
Purpose: Turbines are central to power generation, and even minor vibration issues can lead to catastrophic failures. Proximity probes and proximity probe drivers are commonly used to measure shaft displacement and relative motion in steam, gas, and hydro turbines. Vibration transmitters and signal conditioners convert raw vibration data into standard outputs, enabling integration with control systems and condition monitoring platforms. - Generator Vibration Monitoring
Purpose: Generators are monitored using vibration sensors such as accelerometers or velocity sensors mounted on bearing housings. Vibration switches may also be installed to trigger alarms or automatic shutdowns when critical thresholds are exceeded. Vibration transmitters send continuous data to plant monitoring systems for real-time analysis. - Boiler Feed Pump and Circulating Pump Monitoring
Purpose: High-speed pumps critical to boiler operation are monitored using vibration sensors to detect imbalance, cavitation, or bearing wear. Portable vibration meters are used for routine route-based inspections, while vibration data loggers record long-term trends for detailed performance analysis. - Cooling Tower Fan Monitoring
Purpose: Large cooling tower fans rely on vibration switches and sensors to detect imbalance or misalignment. These devices help prevent blade damage and reduce the risk of catastrophic failures. - Condenser and Heat Exchanger Equipment Monitoring
Purpose: Vibration sensors are used to monitor pump motors and fans associated with condensers and heat exchangers, ensuring efficient heat transfer and system stability. - Auxiliary Equipment Monitoring
Purpose: Smaller machines such as lube oil pumps, combustion air fans, and gearboxes are monitored using vibration sensors, transmitters, and portable analyzers. Signal conditioners help filter and amplify sensor signals for reliable data collection. - Machinery Protection and Condition Monitoring Systems
Purpose: Across the entire plant, vibration monitors, transmitters, and proximity probe systems integrate with distributed control systems (DCS) and plant historians to provide continuous condition monitoring. These systems generate alarms, trigger shutdowns when necessary, and support predictive maintenance strategies by analyzing vibration trends and frequency spectra.
Oil & Gas Applications
- Pump Monitoring
Purpose: Pumps used for crude oil transport, water injection, and chemical dosing are monitored with vibration sensors such as accelerometers and velocity sensors to detect imbalance, cavitation, or bearing wear. Vibration transmitters and signal conditioners convert sensor signals for integration with control systems, while portable vibration meters are used during routine field inspections. - Compressor Monitoring
Purpose: Compressors used in gas gathering, processing, and pipeline transport are equipped with proximity probes and drivers to monitor shaft displacement and vibration. Vibration monitors and transmitters provide continuous data to control systems, while vibration switches help protect equipment by triggering alarms or emergency shutdowns when thresholds are exceeded. - Turbomachinery Monitoring
Purpose: Gas turbines, steam turbines, and expanders require precise monitoring to prevent catastrophic failures. Proximity probe systems track shaft motion and vibration, and signal conditioners prepare the data for reliable transmission to control systems. Continuous monitoring systems help identify developing faults before they escalate. - Pipeline Pump Station Monitoring
Purpose: Pumps and motors in pipeline stations are outfitted with vibration sensors and transmitters to monitor mechanical health and ensure continuous flow. Vibration data loggers are used to capture long-term trends, supporting predictive maintenance programs. - Offshore Platform Equipment Monitoring
Purpose: On offshore platforms, vibration sensors, switches, and monitors are installed on compressors, generators, drilling motors, and other rotating machinery to detect abnormal vibration in harsh marine conditions. This monitoring helps prevent equipment failure and ensures operational safety. - Refinery and Petrochemical Plant Monitoring
Purpose: Refineries rely on vibration monitoring across process pumps, compressors, fans, and agitators to maintain smooth operation. Sensors, transmitters, and proximity probe systems provide continuous condition monitoring, while portable analyzers assist with troubleshooting and field diagnostics. Signal conditioners help ensure clean and accurate signal delivery to control and monitoring systems. - Machinery Protection and Condition Monitoring Systems
Purpose: Across oil and gas operations, integrated condition monitoring systems combine vibration monitors, transmitters, proximity probes, and signal conditioners to deliver early warnings of mechanical issues. These systems help operators track trends, analyze frequency patterns, and support predictive maintenance strategies, reducing downtime and improving equipment reliability.
Mining & Mineral Processing Applications
- Crusher and Mill Monitoring
Purpose: Crushers and grinding mills are essential for material size reduction and are exposed to severe loads and impacts. Vibration sensors are mounted on bearings and casings to monitor imbalance, looseness, and bearing degradation. Vibration transmitters and signal conditioners convert signals for integration with plant control systems, while vibration switches provide immediate protection by triggering alarms or shutdowns when vibration exceeds safe limits. - Conveyor System Monitoring
Purpose: Conveyor belts and their drive motors are monitored using vibration sensors to detect misalignment, bearing faults, or gear defects. Portable vibration meters are often used for routine inspections, and data loggers can track long-term trends to anticipate failures before they disrupt material flow. - Pump and Fan Monitoring
Purpose: Pumps and ventilation fans in mineral processing plants are fitted with vibration sensors to monitor for cavitation, imbalance, and bearing wear. Vibration transmitters and monitors provide continuous feedback to the control room, and vibration switches help safeguard equipment against severe mechanical damage. - Screening and Separation Equipment Monitoring
Purpose: Vibrating screens, separators, and classifiers are critical for sorting and processing minerals. Vibration monitoring systems use sensors and signal conditioners to track equipment health, ensuring consistent performance and preventing unplanned downtime. - Heavy Mobile Equipment Monitoring
Purpose: Large haul trucks, excavators, and loaders are equipped with vibration monitoring systems to assess structural health and detect early signs of mechanical stress, extending equipment life and improving safety in mining operations. - Machinery Protection and Condition Monitoring Systems
Purpose: Across mining operations, centralized condition monitoring systems integrate vibration monitors, transmitters, proximity probes, and signal conditioners to deliver early warnings of mechanical issues. These systems support predictive maintenance strategies, helping reduce unplanned downtime and improve equipment availability in harsh mining environments.
Petrochemical & Chemical Processing Applications
- Pump Monitoring
Purpose: Process pumps used to move liquids, chemicals, and slurries are fitted with vibration sensors to monitor for imbalance, misalignment, cavitation, and bearing wear. Vibration transmitters and signal conditioners convert sensor signals into standard outputs for integration with plant control systems, while portable vibration meters assist maintenance teams with routine inspections. - Compressor Monitoring
Purpose: Centrifugal and reciprocating compressors used in gas compression and chemical processing are equipped with proximity probes and drivers to measure shaft displacement and vibration. Vibration monitors and transmitters provide continuous data to distributed control systems (DCS), and vibration switches offer critical protection by initiating alarms or automatic shutdowns when vibration exceeds safe limits. - Fan and Blower Monitoring
Purpose: Fans and blowers used for air movement, cooling, and process ventilation are monitored with vibration sensors to detect imbalance, bearing defects, and misalignment. Vibration switches are often installed to protect against catastrophic failures, and signal conditioners ensure clean, reliable signals for process control systems. - Agitator and Mixer Monitoring
Purpose: Agitators and mixers in reactors, tanks, and vessels require vibration monitoring to detect mechanical wear, misalignment, and bearing faults. Sensors and transmitters provide continuous condition data, helping maintain consistent mixing performance and prevent equipment failure. - Heat Exchanger and Cooling Tower Monitoring
Purpose: Pumps, motors, and fans associated with heat exchangers and cooling towers are fitted with vibration sensors and switches to monitor mechanical health and avoid unplanned outages that can disrupt thermal management processes. - Machinery Protection and Condition Monitoring Systems
Purpose: Across petrochemical and chemical plants, integrated condition monitoring systems use vibration monitors, transmitters, proximity probes, and signal conditioners to provide early warning of equipment issues. These systems enable operators to analyze vibration trends, diagnose faults, and implement predictive maintenance strategies that improve equipment uptime and reduce operational risk.
Cement & Aggregate Applications
- Crusher Monitoring
Purpose: Primary and secondary crushers experience heavy loads and severe impacts during material size reduction. Vibration sensors are mounted on bearings and housings to detect imbalance, bearing wear, and looseness. Vibration transmitters and signal conditioners process sensor signals for integration with plant control systems, while vibration switches provide immediate protection by triggering alarms or shutdowns when excessive vibration occurs. - Mill and Pulverizer Monitoring
Purpose: Ball mills, vertical roller mills, and pulverizers are critical for grinding raw materials and clinker. Vibration monitoring systems use sensors to detect gear mesh issues, bearing defects, and unbalance. Transmitters and signal conditioners convert vibration signals for real-time monitoring, helping maintenance teams address problems before they lead to costly failures. - Conveyor and Bucket Elevator Monitoring
Purpose: Conveyors and bucket elevators that transport raw materials and finished product are monitored using vibration sensors to detect misalignment, belt or chain issues, and bearing problems. Portable vibration meters are often used for routine inspections, and data loggers support long-term trend analysis for predictive maintenance. - Fan and Blower Monitoring
Purpose: Fans and blowers used for material handling, dust collection, and combustion air are equipped with vibration sensors and switches to monitor imbalance, blade defects, and bearing wear. Signal conditioners ensure clean data is delivered to monitoring systems for early detection of issues. - Kiln and Rotary Dryer Monitoring
Purpose: Rotary kilns and dryers rely on large support rollers and drive assemblies. Vibration sensors are used to monitor bearing condition, gear engagement, and drive alignment. Vibration transmitters and conditioners integrate these measurements into the plant’s control system to enable proactive maintenance. - Machinery Protection and Condition Monitoring Systems
Purpose: Across cement plants and aggregate operations, condition monitoring systems use vibration monitors, transmitters, proximity probes, and signal conditioners to deliver early warnings of mechanical issues. These systems help operators track vibration trends, diagnose developing faults, and implement predictive maintenance plans that minimize downtime and extend equipment life.
Food & Beverage Processing Applications
In the food and beverage processing industry, vibration monitoring and machinery condition monitoring instrumentation are essential for ensuring the reliability, efficiency, and safety of production equipment. These systems help detect early mechanical issues, reduce unplanned downtime, maintain product quality, and support regulatory compliance.
- Pump Monitoring
Purpose: Centrifugal and positive displacement pumps used for fluid transfer, CIP (clean-in-place) systems, and product handling are fitted with vibration sensors to monitor for imbalance, cavitation, and bearing wear. Vibration transmitters and signal conditioners convert sensor data for integration with plant control systems, while portable vibration meters assist maintenance teams during routine checks. - Mixer and Blender Monitoring
Purpose: Mixers, blenders, and agitators used for batching and blending ingredients are monitored with vibration sensors to detect misalignment, looseness, and bearing defects. Transmitters and monitors provide continuous feedback to control systems, helping ensure consistent mixing performance and avoid equipment failures. - Conveyor and Packaging Line Monitoring
Purpose: Conveyors, bottling lines, and packaging equipment are equipped with vibration sensors to monitor motor and bearing condition, detect misalignment, and identify belt or chain issues. Portable vibration meters are commonly used for route-based inspections, and vibration data loggers help track long-term trends for predictive maintenance. - Fan and Blower Monitoring
Purpose: Fans and blowers used in ventilation, drying, and cooling processes are monitored with vibration sensors and switches to detect imbalance, blade damage, and bearing faults. Signal conditioners ensure that clean, reliable signals reach monitoring and control systems. - Refrigeration and Compressor Monitoring
Purpose: Refrigeration systems and air compressors critical to food storage and processing are fitted with vibration sensors, transmitters, and switches to monitor for mechanical wear, misalignment, or component failure. Continuous monitoring ensures system reliability and helps maintain strict temperature control. - Machinery Protection and Condition Monitoring Systems
Purpose: Across food and beverage plants, integrated condition monitoring systems use vibration monitors, transmitters, proximity probes, and signal conditioners to provide early warnings of mechanical issues. These systems help improve equipment uptime, reduce maintenance costs, and support food safety and quality by minimizing unplanned disruptions.
Pharmaceutical Manufacturing Applications
In the pharmaceutical manufacturing industry, vibration monitoring and machinery condition monitoring instrumentation are essential for ensuring equipment reliability, product quality, and compliance with strict regulatory standards. These systems help detect early mechanical issues, reduce unplanned downtime, and maintain continuous, controlled production environments.
- Centrifuge Monitoring
Purpose: Centrifuges used for separation and purification processes are monitored with vibration sensors to detect imbalance, misalignment, and bearing wear. Vibration transmitters and signal conditioners convert sensor signals into standard outputs for integration with plant control systems, while vibration switches provide immediate protection by triggering alarms or shutdowns when vibration exceeds safe levels. - Mixer and Blender Monitoring
Purpose: Mixers and blenders used for blending powders, granules, or liquids are equipped with vibration sensors to monitor mechanical health and detect signs of looseness, misalignment, or bearing faults. Vibration monitors and transmitters provide continuous data to support consistent mixing performance and product uniformity. - Tablet Press and Packaging Equipment Monitoring
Purpose: Tablet presses, capsule fillers, and packaging lines are monitored using vibration sensors to identify abnormal vibration from wear, misalignment, or mechanical damage. Portable vibration meters are often used for routine inspections, and data loggers help capture long-term trends for predictive maintenance. - HVAC and Cleanroom Equipment Monitoring
Purpose: Fans, blowers, and air handling units that maintain cleanroom environments are monitored with vibration sensors and switches to ensure smooth operation and compliance with air quality standards. Signal conditioners help deliver accurate vibration data to building management and control systems. - Pump and Compressor Monitoring
Purpose: Pumps and compressors used in fluid handling, filtration, and utility systems are fitted with vibration sensors, transmitters, and signal conditioners to detect imbalance, cavitation, or bearing degradation. Continuous monitoring helps maintain equipment reliability and prevents process interruptions. - Machinery Protection and Condition Monitoring Systems
Purpose: Across pharmaceutical manufacturing facilities, integrated condition monitoring systems use vibration monitors, transmitters, proximity probes, and signal conditioners to deliver early warnings of equipment issues. These systems help reduce downtime, support compliance with Good Manufacturing Practice (GMP) standards, and protect product integrity throughout the manufacturing process.
Aerospace & Defense Applications
In the aerospace and defense industry, vibration monitoring and machinery condition monitoring instrumentation are essential for ensuring the reliability, safety, and performance of critical equipment and systems. These technologies help detect early signs of mechanical wear or failure, support predictive maintenance, and meet strict operational and regulatory standards.
- Engine and Turbine Monitoring
Purpose: Aircraft engines, gas turbines, and auxiliary power units (APUs) are equipped with vibration sensors and proximity probes to monitor shaft displacement, rotor imbalance, and bearing condition. Vibration transmitters and signal conditioners convert data for integration with onboard or ground-based monitoring systems, while vibration switches provide immediate protection by triggering alarms or automated responses when limits are exceeded. - Test Stand and Ground Support Equipment Monitoring
Purpose: Engine test stands, dynamometers, and ground support equipment use vibration monitoring to assess mechanical health during testing and operation. Sensors and transmitters provide real-time data on imbalance, misalignment, and component wear, while data loggers capture trends for post-test analysis and maintenance planning. - Flight Control and Actuation System Monitoring
Purpose: Electromechanical actuators, hydraulic pumps, and control surface drives are monitored with vibration sensors to detect abnormal vibration caused by wear, misalignment, or mechanical faults. Continuous monitoring helps maintain precise control system performance and ensure safe flight operation. - Radar, Antenna, and Satellite Equipment Monitoring
Purpose: Rotating radar systems, tracking antennas, and satellite ground station equipment rely on vibration sensors and condition monitoring systems to detect mechanical issues, prevent failures, and maintain uninterrupted operation in demanding environments. - Manufacturing and Maintenance Facility Equipment Monitoring
Purpose: CNC machines, composite material equipment, and precision assembly tools in aerospace manufacturing are monitored using vibration instrumentation to detect spindle imbalance, tool wear, or motor faults. Portable vibration analyzers are often used for troubleshooting, and integrated systems support predictive maintenance programs. - Machinery Protection and Condition Monitoring Systems
Purpose: Across aerospace and defense operations, condition monitoring systems integrate vibration monitors, transmitters, proximity probes, and signal conditioners to provide early warnings of mechanical issues. These systems improve equipment uptime, ensure mission readiness, reduce maintenance costs, and enhance operational safety.
Semiconductor & Electronics Manufacturing Applications
In the semiconductor and electronics manufacturing industry, vibration monitoring and machinery condition monitoring instrumentation are critical for maintaining the precision, stability, and cleanliness required in production environments. These systems help detect mechanical issues early, prevent costly downtime, protect sensitive equipment, and ensure consistent product quality.
- Wafer Fabrication Equipment Monitoring
Purpose: Semiconductor fabrication tools such as etchers, deposition systems, and lithography machines require extremely stable operating conditions. Vibration sensors and monitors are used to detect external and internal vibration sources that could affect alignment, precision, or process stability. Signal conditioners and transmitters ensure accurate data delivery to building management and process control systems. - Cleanroom HVAC and Fan Monitoring
Purpose: Cleanroom air handling units, filtration fans, and blowers are equipped with vibration sensors and switches to monitor for imbalance, bearing wear, or motor faults. Continuous monitoring helps maintain the precise environmental conditions required for particle-sensitive manufacturing and supports cleanroom certification compliance. - CMP, Dicing, and Back-End Process Equipment Monitoring
Purpose: Chemical mechanical planarization (CMP) systems, wafer dicing saws, and packaging equipment rely on vibration monitoring to detect mechanical wear, tool degradation, or spindle imbalance. Portable vibration analyzers are used for periodic diagnostics, while data loggers track long-term trends to inform predictive maintenance. - Chiller and Vacuum Pump Monitoring
Purpose: Chillers and vacuum pumps supporting process equipment are fitted with vibration sensors, transmitters, and signal conditioners to monitor for misalignment, cavitation, and bearing failures. Early detection of issues helps avoid equipment disruptions that could compromise sensitive production processes. - Precision Assembly and Test Equipment Monitoring
Purpose: Automated assembly lines, wire bonders, and testing equipment are monitored with vibration instrumentation to ensure mechanical stability and precision performance. Condition monitoring helps maintain product quality and prevents micro-defects that can arise from excessive vibration. - Machinery Protection and Condition Monitoring Systems
Purpose: Across semiconductor and electronics manufacturing facilities, integrated condition monitoring systems combine vibration monitors, transmitters, and signal conditioners to provide early warnings of mechanical issues. These systems support predictive maintenance programs, improve equipment uptime, and protect high-value assets critical to production throughput and quality.
Terms & Definitions🔗
Root Mean Square (RMS) Vibration
A calculated value that represents the overall energy of a vibration signal, commonly used as a baseline metric for assessing machinery health.
Vibration Analysis
The specialized process of reviewing vibration data—often by a trained analyst—to interpret frequency patterns, diagnose machine conditions, and recommend corrective actions.
Vibration Analyzer
A handheld or portable tool that measures and analyzes vibration signals to diagnose machine faults and recommend corrective actions.
Vibration Data Logger
A device that records vibration measurements over time, allowing for historical analysis, troubleshooting, or validation of maintenance activities.
Vibration Meter
A portable handheld instrument used to measure overall vibration levels in equipment, commonly applied during routine inspections or troubleshooting.
Vibration Monitor
An instrument or system that continuously tracks vibration levels, providing real-time data and alerts when readings exceed acceptable thresholds.
Vibration Sensor
A device that detects and measures vibration levels in machinery or structures, typically using piezoelectric, velocity, or displacement sensing technologies.
Vibration Shaker Table
A machine that simulates vibration conditions in a controlled environment to test the durability, performance, and reliability of components or products.
Vibration Signal Conditioner
A module that processes raw vibration signals—filtering, amplifying, or converting them into formats usable by monitoring or control systems.
Vibration Switch
A device that triggers alarms or automatic shutdowns when vibration levels exceed preset limits, helping protect machinery from damage.
Vibration Tester
A portable device used to assess the vibration condition of machinery during field inspections, supporting maintenance and troubleshooting efforts.
Vibration Transmitter
A device that converts vibration signals into standard outputs (such as 4–20 mA) for integration with control systems like PLCs, DCS, or SCADA.
Frequently Asked Questions🔗
Does Clipper Controls provide help with selecting the right vibration monitoring equipment?
Yes. Our technical team works closely with you to understand your application and recommend the most appropriate vibration sensor, switch, transmitter, signal conditioner, and monitoring displays for your environment.
What is vibration monitoring and why is it important?
Vibration monitoring is the process of measuring and analyzing machine vibration to detect early signs of mechanical problems such as imbalance, misalignment, or bearing failure. It helps prevent unplanned downtime, reduce maintenance costs, and extend equipment life.
What types of equipment can benefit from vibration monitoring?
What’s the difference between a vibration sensor and a vibration transmitter?
When should I use a vibration switch instead of a full monitoring system?
Vibration switches are ideal for simple protection applications where automatic alarms or shutdowns are needed when vibration exceeds a preset level. For continuous monitoring and diagnostics, full monitoring systems or transmitters with data analysis are recommended.
What is vibration analysis and who performs it?
Vibration analysis is the specialized process of interpreting vibration data to diagnose equipment health. It’s typically performed by trained vibration analysts or condition monitoring specialists using advanced tools like analyzers and software.
Can vibration monitoring help with predictive maintenance?
Yes. By continuously tracking equipment health, vibration monitoring enables predictive maintenance programs—allowing teams to address issues before they cause failures, improving reliability and reducing costs.
What is the role of proximity probes in vibration monitoring?
Proximity probes are used to measure shaft displacement and relative motion in critical rotating machinery, providing precise data on shaft vibration and position, which is essential for protecting high-speed and high-value assets.
Need Help?
Our Crew is Here To Serve You!
Services We Offer
Instrumentation Calibrations
Rental Equipment
Equipment Troubleshooting
Repairs & Maintenance
Instrumentation
Flow Studies
Startup & Training
Technologies
Resources
Brands We Recommend
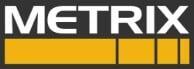